AlSi10 Powder
AlSi10 is an aluminum alloy powder containing 10% silicon and remainder aluminum. It offers an excellent combination of strength, low density, thermal properties, corrosion resistance and weldability.
Low MOQ
Provide low minimum order quantity to meet different needs.
OEM & ODM
Provide customized products and design services to meet unique customer needs.
Adequate Stock
Ensure fast order processing and provide reliable and efficient service.
Customer Satisfaction
Provide high quality products with customer satisfaction at the core.
share this product
Table of Contents
AlSi10 is an aluminum alloy powder containing 10% silicon and remainder aluminum. It offers an excellent combination of strength, low density, thermal properties, corrosion resistance and weldability.
AlSi10 Powder Composition
The typical composition of AlSi10 alloy powder is:
Element | Composition |
---|---|
Aluminum (Al) | Balance |
Silicon (Si) | 9-11% |
- Aluminum forms the matrix providing low density, ductility and corrosion resistance.
- Silicon provides solid solution strengthening and improves castability.
Strict control of the aluminum to silicon ratio is critical to achieve optimal strength and physical properties. Other minor alloying elements like magnesium, iron, copper or zinc may also be present in certain grades.
Properties of AlSi10 Powder
AlSi10 powder possesses an excellent combination of properties making it suitable for various demanding applications:
Property | Value |
---|---|
Density | 2.7 g/cm3 |
Melting Point | ~600°C |
Thermal Conductivity | 150-180 W/m-K |
Electrical Conductivity | 35-40% IACS |
Coefficient of Thermal Expansion | 21-23 x 10<sup>-6</sup> /°C |
Modulus of Elasticity | 80-85 GPa |
Tensile Strength | 240-300 MPa |
Elongation | 1-5% |
Hardness | 80-90 Brinell |
Corrosion Resistance | Excellent |
- Low density – Up to 65% lighter than copper alloys and steels.
- High thermal conductivity – Enables rapid dissipation of heat in electronics.
- High strength-to-weight ratio – Strength comparable to titanium alloys with lower density.
- Excellent weldability and castability – High fluidity when molten allowing easy casting and welding.
- Resistant to corrosion and oxidation – Protective oxide layer prevents corrosion in many environments.
This exceptional property profile makes AlSi10 suitable for lightweight structural applications across aviation, space, automotive and other sectors.
Applications of AlSi10 Powder
Owing to its lightweight, strength and thermal properties, AlSi10 powder is ideal for:
Applications | Benefits |
---|---|
Aerospace components | Low density combined with high strength. |
Automotive parts | Weight reduction without compromising mechanical performance. |
Electronic housings | Thermal management for heat dissipation combined with low weight. |
Medical implants | Biocompatible, non-toxic, corrosion resistant. |
Thermal management | High thermal conductivity to dissipate heat. |
- Used extensively in aircraft and rocket components like engine mounts to reduce weight.
- Automotive industry uses AlSi10 for pistons, transmission casings, suspension parts to improve fuel efficiency through lightweighting.
- Electronic enclosures and heat sinks leverage high thermal conductivity for efficient cooling.
- Rewards excellent strength-to-weight ratio with lower density compared to titanium alloys.
- Provides excellent biocompatibility, corrosion resistance for medical implants like orthopedic devices.
AlSi10 delivers maximum performance in demanding applications where low mass and high strength are critical.
AlSi10 Powder Specifications
AlSi10 powder is available in various size fractions, shapes and purity levels:
Parameter | Options |
---|---|
Particle size | 5-150 microns |
Particle shape | Spherical, irregular |
Apparent density | Up to 2.7 g/cm3 |
Flow rate | Up to 25 s/50g |
Purity | Up to 99.7% |
Alloy variants | AlSi12, AlSi5 |
- Smaller particles promote better sintering while larger sizes provide higher flowability.
- Spherical morphology improves flow and packaging density. Irregular particles offer cost benefits.
- Higher apparent density increases effective loading in composites manufacturing.
- Higher flow rates enhance ease of powder handling and processing.
- High purity reduces contamination issues during processing and improves final properties.
- Range of silicon levels between 5-12% available to balance fluidity and strength.
Powder attributes are customized based on specific application requirements and processing methods.
Consolidation Methods for AlSi10 Powder
AlSi10 powder can be transformed into full density components using techniques like:
Method | Benefits |
---|---|
Additive manufacturing | Excellent geometric freedom for complex shapes. |
Metal injection molding | High precision net shape capability. |
Pressing and sintering | Economical for high volume simpler geometries. |
Extrusion | Continuous production of rods and tubes. |
Isostatic pressing | Achieves full density and improves properties. |
- Powder bed fusion additive manufacturing methods like selective laser melting are popular for prototypes or low volume production.
- Metal injection molding offers closest tolerances and excellent surface finish.
- Pressing followed by liquid phase sintering is commonly used but secondary processing like extrusion is needed.
- Extrusion leverages excellent castability to produce rods, tubes and profiles.
- Cold and hot isostatic pressing reduce porosity and increase density.
The consolidation technique influences the microstructure, final properties, geometrical capabilities and productivity.
Heat Treatment of AlSi10 Parts
Solution heat treatment and artificial aging are used to tailor the strength of AlSi10 components:
Heat Treatment | Details | Purpose |
---|---|---|
Solutionizing | 530-550°C, quench | Dissolve soluble phases |
Artificial Aging | 150-180°C, 5-10 hrs | Precipitation hardening |
Annealing | 350°C, slow cooling | Restores ductility |
- Solution heat treatment dissolves alloying elements like silicon in the aluminum matrix followed by rapid cooling or quenching.
- Subsequent aging treatment causes fine precipitation resulting in considerable hardening.
- Annealing helps recover ductility after extensive prior cold working.
Careful control of time and temperature of solutionizing and aging allows customizing mechanical properties as per specific requirements.
Comparison of AlSi10 Powder with Alternatives
Here is how AlSi10 compares to other aluminum alloy powders:
Alloy | AlSi10 | AlSi12 | Al6061 | Al7075 |
---|---|---|---|---|
Strength | High | Highest | Medium | Very High |
Weldability | Excellent | Poor | Good | Poor |
Corrosion Resistance | Excellent | Excellent | Excellent | Good |
Thermal Conductivity | High | Medium | Medium | Low |
Density | Low | Low | Low | Low |
Cost | Low | High | Medium | High |
- AlSi12 has the highest strength but poorer weldability and thermal conductivity.
- 6061 is a popular general purpose alloy with medium strength and good corrosion resistance.
- 7075 excels in very high strength but has poor weldability and only moderate corrosion resistance.
- AlSi10 provides the best all-round properties with added cost benefits.
For most applications, AlSi10 offers the optimum balance of performance, weldability and cost.
AlSi10 Powder Manufacturers
As a widely used alloy, AlSi10 powder is produced by major global suppliers:
Manufacturer | Country |
---|---|
Hoeganaes Corporation | USA |
Sandvik Osprey | UK |
CNPC Powder | China |
Rio Tinto Metal Powders | Canada |
Toyal America | USA |
ECKA Granules | Germany |
Reputable manufacturers have stringent quality control and conform to specifications of international standards organizations. They also customize powder characteristics based on application requirements.
AlSi10 Powder Pricing
As a high performance alloy powder, AlSi10 commands a premium over plain aluminum powders. Indicative pricing is:
Powder Type | Particle Size | Price ($/kg) |
---|---|---|
For pressing | Under 150 μm | $12-18 |
For sintering | 45-150 μm | $15-22 |
For AM | 15-45 μm | $22-35 |
High purity | Up to 10 μm | $30-50 |
- Finer fractions for AM and sintering cost more than coarser pressing grades.
- Smaller order quantities under 100 kg attract higher prices.
- High purity grades with lower oxygen, nitrogen are over 50% more expensive.
- Reducing silicon content to AlSi5 lowers cost by around 15%.
Volume discounts, longer term contracts and simpler particle specifications can help lower cost.
Health and Safety Considerations for AlSi10 Powder
Like any metal powder, AlSi10 powder requires safe handling:
Hazard | Precautions | PPE |
---|---|---|
Skin/eye contact | Avoid direct contact. Rinse if exposed. | Gloves, goggles |
Inhalation | Avoid breathing dust. Ensure ventilation. | Respirator |
Ingestion | Avoid hand-mouth transfer. Wash hands. | – |
Fire | Use sand. Do not use water. | Protective gear |
- Wear gloves, goggles, mask when handling powder.
- Avoid skin contact. Wash after exposure.
- Store in cool, dry place away from sparks, flames.
- Ensure proper ventilation and dust collection.
- Refer SDS and local regulations for complete guidelines.
With proper precautions and PPE, AlSi10 powder can be safely handled during storage, processing and operation.
Inspection and Testing of AlSi10 Powder
To ensure quality requirements are met, AlSi10 powder should be tested for:
Parameter | Method | Specification |
---|---|---|
Chemical composition | OES, XRF, wet chemistry | Conformance to Al, Si, Mg content |
Particle size distribution | Laser diffraction, sieving | D10, D50, D90 within range |
Powder morphology | SEM imaging | Spherical shape and flowability |
Apparent density | Hall flowmeter test | Minimum specified density |
Flow rate | Hall flow meter test | Maximum flow seconds |
Impurity levels | ICP or LECO analysis | Low oxygen, moisture content |
Routine testing as per ASTM standards ensures consistency and high quality powder suitable for critical applications.
FAQs
Q. What is AlSi10 alloy used for?
A. AlSi10 is widely used in aerospace, automotive, and electronics applications where low weight and high strength are critical such as engine mounts, pistons, housings, heat sinks.
Q. Does AlSi10 require heat treatment?
A. Yes, solution heat treatment followed by aging can significantly enhance the tensile strength by precipitating alloying elements like silicon.
Q. What methods can consolidate AlSi10 powder?
A. AlSi10 powder can be consolidated to full density using additive manufacturing, metal injection molding, extrusion, and powder compact forging.
Q. Is AlSi10 weldable?
A. Yes, AlSi10 has excellent weldability owing to the silicon alloying addition which improves fluidity in the molten state. This allows easy fusion welding.
Q. Is AlSi10 powder safe to handle?
A. Like any fine metal powder, standard safety precautions should be taken during storage, handling and processing of AlSi10 powder to minimize health and safety risks.
About Met3DP
Product Category
HOT SALE
CONTACT US
Any questions? Send us message now! We’ll serve your request with a whole team after receiving your message.
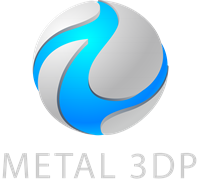
Leading provider of additive manufacturing solutions headquartered in Qingdao, China.
COMPANY
PRODUCT
cONTACT INFO
- Qingdao City, Shandong, China
- info@metal3dp.com
- amy@metal3dp.com
- +86 19116340731