A100 steel alloy powder
A100 steel alloy powder is a specialized form of steel that consists of a precise blend of iron and other alloying elements. It is manufactured by atomization, a process that involves rapidly solidifying molten metal into fine powder particles. This fine powder exhibits excellent flowability and can be easily consolidated into various shapes using powder metallurgy techniques.
Low MOQ
Provide low minimum order quantity to meet different needs.
OEM & ODM
Provide customized products and design services to meet unique customer needs.
Adequate Stock
Ensure fast order processing and provide reliable and efficient service.
Customer Satisfaction
Provide high quality products with customer satisfaction at the core.
share this product
Table of Contents
Overview of A100 Steel Alloy Powder
A100 stainless steel contains high levels of nickel and manganese along with chromium, nitrogen and carbon to achieve outstanding low temperature toughness and ductility. It retains excellent impact strength and resistance to cryogenic embrittlement down to the temperature of liquid helium.
Key characteristics of A100 powder include:
- Excellent low temperature toughness and ductility
- High impact strength at cryogenic temperatures
- Good strength and hardness at room temperature
- Very good weldability and fabricability
- Resistant to cryogenic embrittlement
- Available in various particle size distributions
A100 powder is designed for applications requiring thermal stability and toughness at extremely low temperatures such as liquid natural gas storage and transportation. This article provides a detailed overview of this alloy powder.
Chemical Composition of A100 Powder
The typical composition of A100 powder is:
Element | Weight % |
---|---|
Nickel (Ni) | 9-11% |
Manganese (Mn) | 12-14% |
Chromium (Cr) | 14-16% |
Nitrogen (N) | 0.15-0.30% |
Carbon (C) | 0.08% max |
Silicon (Si) | 1% max |
Iron (Fe) | Balance |
The key alloying elements like nickel, manganese, chromium along with nitrogen enable exceptional cryogenic temperature toughness and ductility in A100 steel.
Properties of A100 Powder
A100 powder possesses the following properties:
Property | Value |
---|---|
Density | 7.9-8.1 g/cm3 |
Melting Point | 1400-1450°C |
Thermal Conductivity | 12 W/mK |
Electrical Resistivity | 0.80 μΩ.cm |
Young’s Modulus | 190-210 GPa |
Poisson’s Ratio | 0.29-0.30 |
Tensile Strength | 620 MPa |
Yield Strength | 275 MPa |
Elongation | 35-40% |
Impact Strength | 50-120 J at -196°C |
A100 maintains excellent ductility and impact strength even at the temperature of liquid helium making it suitable for the most demanding cryogenic applications.
Production Method for A100 Powder
A100 powder can be produced via:
- Gas Atomization – High pressure inert gas used to atomize the molten alloy resulting in fine spherical powder ideal for AM.
- Water Atomization – High velocity water jet breaks up the molten stream into irregular powder particles. Lower cost but higher oxygen pickup.
- Mechanical Alloying – Ball milling of blended elemental powders followed by sintering and secondary atomization.
Gas atomization allows excellent control over particle size distribution, shape, oxygen pickup and microcleanliness.
Applications of A100 Powder
Typical applications for A100 powder include:
- Additive Manufacturing – Used in laser powder bed fusion and binder jetting for cryogenic parts like valve bodies, pump components, storage tanks etc.
- Metal Injection Molding – To manufacture small, complex cryogenic parts needing high ductility and impact strength.
- Thermal Spray Coatings – Wire arc spray deposition to produce coatings providing cryogenic resistance.
- Cryogenic Vessels – Liners, fittings, fasteners, forged and cast parts for storage, transportation of liquefied natural gas.
- Cryocoolers – Powder forged compressor parts, regenerator housings requiring high cryogenic toughness.
Specifications of A100 Powder
A100 powder is available under various size ranges, shapes and grades:
- Particle Size: From 10-45 μm for AM methods, up to 150 μm for thermal spray processes.
- Morphology: Spherical, irregular and blended shapes. Smooth spherical powder provides optimal flow and packing density.
- Purity: From commercial to high purity grades based on application requirements.
- Oxygen Content: Levels maintained below 2000 ppm for most applications.
- Flow Rate: Powder customized for flow rates above 25 s/50 g.
Global Suppliers of A100 Powder
Some of the major global suppliers of A100 powder include:
- Sandvik Osprey (UK)
- Hoganas (Sweden)
- Praxair (USA)
- Oerlikon Metco (Switzerland)
- Erasteel (France)
- CNPC Powder (China)
These companies produce various grades of A100 powder tailored for additive manufacturing, thermal spray, powder metallurgy and other cryogenic applications.
Pricing of A100 Powder
A100 powder is priced higher than austenitic grades due to complex chemistry:
- Quantity – $50-100 per kg for bulk orders above 500 kg. Smaller quantities are priced higher.
- Quality – High purity, spherical powder with controlled characteristics demands premium pricing.
- Supplier – Large global suppliers offer competitive pricing owing to higher volumes.
- Geography – Prices vary between regions with Europe and North America being higher priced markets.
For critical cryogenic applications, buyers should focus on quality rather than lowest cost while procuring A100 powder.
Storage and Handling of A100 Powder
A100 powder requires controlled storage and handling:
- Store in sealed containers under inert gas to prevent oxidation
- Avoid accumulation of fine powder to minimize dust explosion risks
- Use proper grounding, ventilation, PPE when handling powder
- Prevent contact with moisture, acids, strong oxidizers
- Follow recommended safety practices from supplier SDS
Inert gas glove box techniques are preferred when handling reactive alloy powders like A100.
Inspection and Testing of A100 Powder
Key quality control tests performed on A100 powder:
- Chemical analysis using OES or XRF to ensure composition is within specified limits
- Particle size distribution as per ASTM B822 standard
- Morphology analysis through SEM imaging
- Powder flow rate measured as per ASTM B213 standard
- Density determination by helium pycnometry
- Impurity testing by ICP-MS
- Microstructure characterization by X-ray diffraction
Thorough testing ensures the powder meets the required chemical, physical and microstructural characteristics for cryogenic applications.
Comparison Between A100 and 304L Stainless Steel Powders
A100 and 304L stainless steel powders compared:
Parameter | A100 | 304L |
---|---|---|
Type | Austenitic | Austenitic |
Ni content | 9-11% | 8-12% |
Low temperature toughness | Excellent | Poor |
Corrosion resistance | Moderate | Excellent |
Cost | Higher | Lower |
Weldability | Very good | Excellent |
Applications | Cryogenic parts | Automotive, appliances |
A100 offers exceptional low temperature toughness whereas 304L provides better overall corrosion resistance at lower cost.
A100 Powder FAQs
Q: How is A100 steel alloy powder produced?
A: A100 powder is commercially produced using gas atomization, water atomization and mechanical alloying followed by sintering. Gas atomization provides the best control of characteristics.
Q: What are the main applications of A100 powder?
A: The major applications include additive manufacturing, thermal spray coatings, metal injection molding, and powder metallurgy of cryogenic parts needing high ductility and impact strength at extremely low temperatures.
Q: What is the typical A100 powder size used for binder jetting AM?
A: For binder jetting process, the common A100 powder size range is 20-45 microns with spherical morphology to enable good powder packing and binder infiltration.
Q: Does A100 powder require any special handling precautions?
A: Yes, it is recommended to handle A100 powder carefully under controlled humidity and inert atmosphere using proper grounding, ventilation and PPE.
Q: Where can I purchase A100 powder suitable for cryogenic storage vessels?
A: For cryogenic applications needing high toughness, A100 powder can be purchased from leading manufacturers including Sandvik Osprey, Hoganas, Praxair, Oerlikon Metco, and Erasteel.
About Met3DP
Product Category
HOT SALE
CONTACT US
Any questions? Send us message now! We’ll serve your request with a whole team after receiving your message.
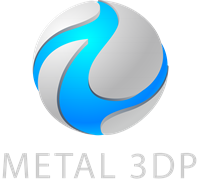
Leading provider of additive manufacturing solutions headquartered in Qingdao, China.
COMPANY
PRODUCT
cONTACT INFO
- Qingdao City, Shandong, China
- info@metal3dp.com
- amy@metal3dp.com
- +86 19116340731