Niobium is a refractory metal with unique properties like high temperature strength, corrosion resistance, and superconductivity. Niobium powder enables manufacturing advanced components from this metal using techniques like additive manufacturing and powder metallurgy.
This guide provides a detailed overview of niobium powder including its properties, production methods, particle characteristics, applications, advantages, limitations, pricing, and comparisons with alternative metals.
Introduction to Niobium Powder
Niobium powder has the following key characteristics:
- Made from refractory element niobium (Nb)
- High melting point of 2477°C
- Density of 8.57 g/cm3
- Available in various particle size distributions
- Mainly used in cemented carbides and superalloys
- Also used in electronics, optics, and superconductors
- Suitable for additive manufacturing, thermal spray, and MIM
Niobium’s refractory properties lend themselves for manufacturing specialized high performance components via powder metallurgy routes.
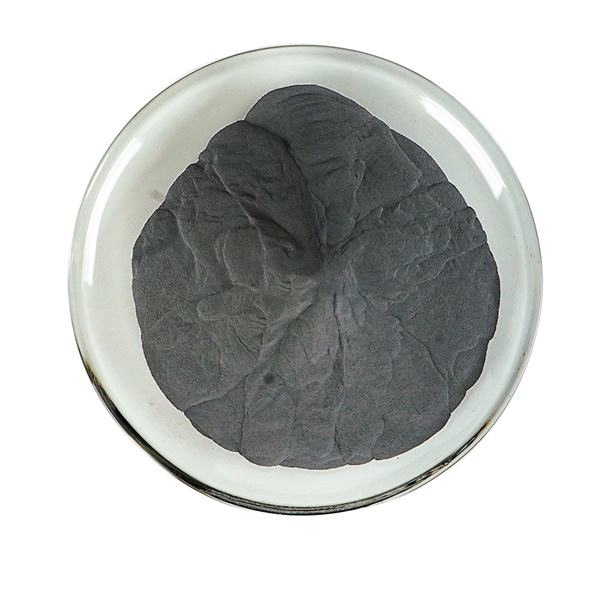
Properties and Characteristics of Niobium Powder
Physical Properties
- Density: 8.57 g/cm3
- Melting point: 2477°C
- Electrical resistivity: 15 μΩ-cm
- Thermal conductivity: 53 W/m-K
- Thermal expansion: 7.3 μm/m-K
Mechanical Properties
- Tensile strength: 550 MPa
- Yield strength: 240 MPa
- Elongation: 30%
- Elastic modulus: 105 GPa
High Temperature Properties
- Retains strength above 1000°C in vacuum
- Superconducting transition at 9.2K
- Low vapor pressure even near melting point
Chemical Properties
- Excellent corrosion resistance
- Forms stable protective oxide layer
- Low solubility in Fe, Ni, Cu alloys
Production Methods for Niobium Powder
Key techniques used for producing niobium powder include:
- Hydriding-Dehydriding – Most common method to make fine niobium powders
- Calcium Reduction – Reduction of Nb2O5 for high purity niobium
- Electron Beam Melting – Melting and atomization into fine powder
- Carbon Reduction – Uses carbon to reduce niobium pentoxide
Powder Processing
- Degassing in vacuum to reduce impurities
- Milling and conditioning to improve powder characteristics
- Alloying with other elements like titanium
Controlling oxygen levels and achieving high purity are critical during niobium powder production.
Particle Size and Morphology
Size Distribution
- Ranges from 1 to 150 microns
- Smaller sizes preferred for additive manufacturing
- Larger sizes used for thermal spray coatings
Particle Morphology
- Irregular morphology with satellite particles
- Near spherical shaping achieved with plasma processing
- Flow rates measured by Hall flowmeter
Chemical Composition
- Niobium content above 99.8% purity
- Low oxygen, nitrogen and carbon levels
- Meets ASTM standard specifications
Applications of Niobium Powder
Key application areas of niobium powder include:
Additive Manufacturing
- Aerospace and aircraft components
- High temperature tooling
- Vacuum applications
- Customized or complex geometries
Cemented Carbides
- Cutting tools and wear parts
- Improves strength and fracture resistance
Nickel Superalloys
- Strengthening alloy addition
- Inconel 625, 718 type alloys
Electronics
- Capacitors, superconductors
- Optical coatings
- Beam shaping
Coatings
- Corrosion resistant coatings
- Thermal spray applications
Benefits and Advantages of Niobium Powder
Some major benefits of using niobium powder:
- High strength maintained at elevated temperatures
- Excellent oxidation and corrosion resistance
- Low coefficient of thermal expansion
- Good thermal and electrical conductivity
- Improves strength of superalloys and cemented carbides
- Relatively stable metal prices
- Enables additive manufacturing of complex parts
- High chemical purity available
- Custom alloys can be produced
- Lower density than tungsten or tantalum
The unique properties of niobium lend themselves useful for specialized applications where high temperature stability and/or low thermal expansion is needed.
Limitations and Disadvantages
Some limitations of using niobium powder include:
- High costs compared to nickel and iron powders
- Poorer weldability than stainless steels
- Susceptible to hydrogen embrittlement
- Pyrophoric nature requires careful handling
- Limited supplier base compared to common alloys
- Special melting equipment needed due to refractory nature
- Parameter development required for new additive applications
- Oxide inclusions possible requiring extensive degassing
Proper care must be taken to control powder production processes and handling procedures for niobium.
Niobium Powder Pricing
Niobium Powder Price Ranges:
- <10 microns: $70-$100 per kg
- 10-45 microns: $50-$70 per kg
- 45-106 microns: $40-$60 per kg
- Pricing depends on particle size, purity, and order volumes
- Requires high purity raw materials, increasing costs
- Limited suppliers pushes costs higher
- Still economical for certain high value applications
Long term agreements can secure stable niobium powder pricing from suppliers.
Comparison with Alternative Metal Powders
Versus Tungsten Powder
- Niobium has a lower density than tungsten
- Lower melting point than tungsten
- Similar high temperature strength capabilities
- Less chemically reactive than tungsten
Versus Tantalum Powder
- Lower density than tantalum
- Melts at much lower temperature than tantalum
- Less radioactive than natural tantalum
- Lower cost alternative to tantalum
Versus Titanium Powder
- Higher temperature capability than titanium
- Higher density and lower ductility
- Much higher costs than titanium powders
- Titanium has better corrosion resistance in some conditions
FAQs
Q: How is niobium powder produced?
A: The main production method is hydriding-dehydriding, where niobium pentoxide is chemically reduced and crushed into fine powder. High purity is maintained via controlled processes.
Q: What are the major applications of niobium powder?
A: Main applications include cemented carbides, nickel superalloys, electronics, and coatings. There is increasing use in additive manufacturing of aerospace and tooling components needing high temperature stability.
Q: What alloys is niobium powder added to?
A: Niobium is alloyed to improve high temperature strength of nickel and cobalt superalloys. It also enhances cemented carbides made from tungsten, titanium and tantalum carbides.
Q: Does niobium react with atmospheric oxygen?
A: At room temperature, niobium forms a protective oxide layer that prevents further reaction. At higher temperatures above 400°C, it reacts readily with atmospheric oxygen and burns.
Q: What particle sizes of niobium powder are available?
A: Typical size ranges are 1-10 microns for AM, 10-45 microns for pressing, and 45-150 microns for thermal spray. Finer powders provide better resolution but are more expensive.
Q: Is niobium powder pyrophoric?
A: Yes, niobium powder can ignite spontaneously in air, especially at finer sizes below 45 microns. Proper handling precautions are essential to prevent fires.
Q: How is niobium powder stored safely?
A: Niobium powder must be stored in sealed containers under inert gases like argon to prevent oxidation and pyrophoric ignition. Tightly controlled processing and storage conditions are critical.
Q: Is niobium powder reusable?
A: Unused niobium powder can be reused after screening to remove contaminants. However, fresh powder is generally recommended for critical applications to prevent defects from reuse.