MIM Technology
Revolutionizing Precision Components
Discovering the Potential of MIM Technology
Metal3DP’s groundbreaking Hot Isostatic Pressing (HIP) Technology. As pioneers in this domain, we harness the formidable capabilities of HIP to catapult metal components to unprecedented echelons of performance, strength, and reliability. Our commitment to excellence drives us to redefine the boundaries of what’s achievable, and HIP serves as our vehicle to elevate the very essence of metal components.
Metal Injection Molding (MIM) Technology merges the advantages of plastic injection molding and powder metallurgy to produce intricate metal components with unparalleled precision and complexity.
Principle and Process
MIM leverages a mixture of fine metal powders and binders, creating a feedstock that is injection molded into precise shapes. The formed components undergo debinding and sintering, resulting in solid metal parts.
Limitations and Considerations
MIM’s limitations include design complexity, size restrictions, and material limitations. Designers must balance geometrical intricacies with manufacturability.
Advantages of MIM Technology
Advantages 01
Intricate Geometry
MIM excels in crafting complex shapes and features, overcoming traditional manufacturing constraints.
Advantages 02
High Precision
The injection molding process delivers tight tolerances, ensuring consistent and accurate components.
Advantages 03
Material Versatility
MIM accommodates a wide range of metals and alloys, tailoring material properties to application needs.
Advantages 04
Cost-Efficiency
MIM reduces production costs compared to traditional methods for intricate components, making it ideal for mass production.
Advantages 05
Near Net Shape
MIM often produces components close to the final shape, minimizing machining and waste.
Application of MIM Technology
Metal Injection Molding (MIM) Technology is a versatile force driving innovation across various industries, revolutionizing component fabrication with precision and complexity.
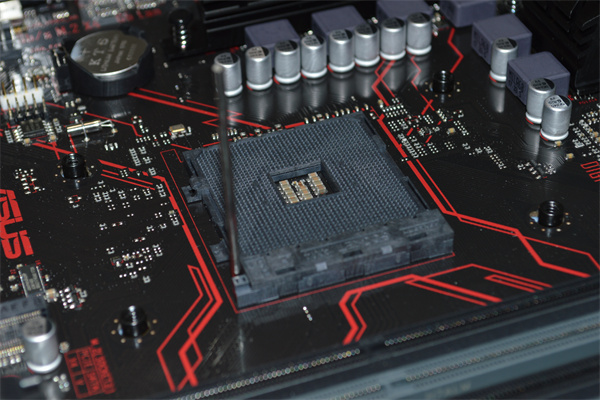
Electronics
From micro-connectors to intricate parts, MIM empowers the electronics sector with high-precision components.
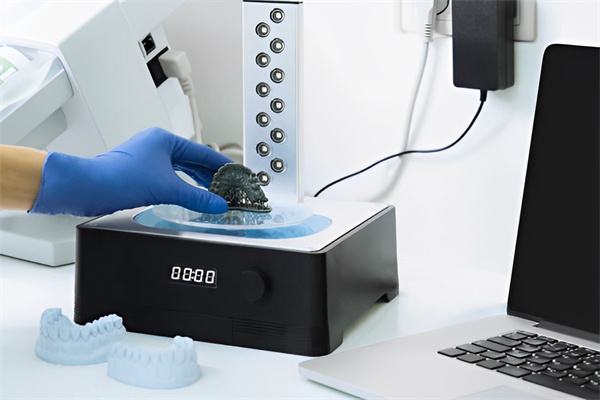
Medical
MIM advances medical devices, creating biocompatible implants and surgical instruments with unmatched precision.
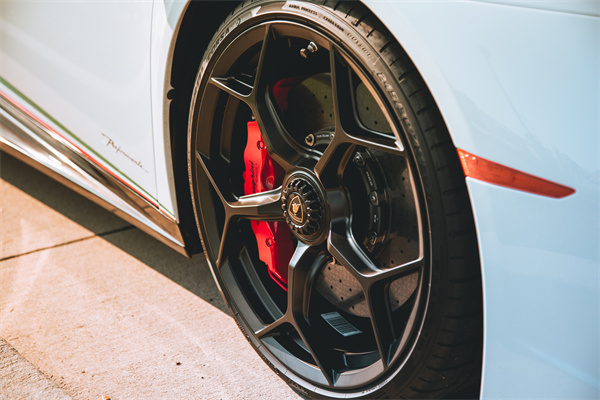
Automotive
Automotive components, including engine parts and transmission elements, benefit from MIM’s intricate design capabilities.
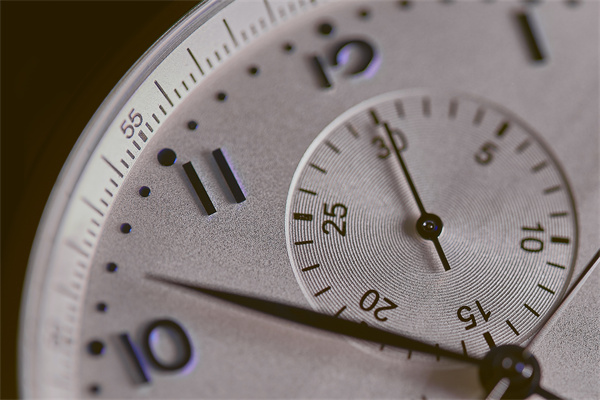
Consumer Goods
MIM transforms consumer products, producing watch components, locks, and hinges with precision.