Significance of Iron Alloys Powder
Iron alloy powders are crucial materials used in manufacturing a wide range of products. These powders are made up of various iron particles, ranging in size from 20-200 μm, and their properties can vary significantly based on the production method used. There are three main types of iron powder: reduced iron powder, atomized powder, and electrolytic iron powder, each with specific applications based on their properties.
Applications in Automotive Parts:
Engine Parts | Steering & Suspension Parts | Transmission Parts | Other Applications |
---|---|---|---|
Cam shaft pulley | Power steering rotor cam ring | M/T Synchronizer hub | Bearings and filter parts |
Crank shaft pulley | Pressure plate | A/T Hub clutch | Hand Warmers |
Valve guide | Rack guide | Synchronizer ring | Magnetic materials |
Oil pump inner rotor | Shock absorber | Shift fork | Oxygen scavengers |
Additional Uses:
Iron powders also find use in seats and door parts for vehicles, as well as in machine parts, high strength/wear-resistant parts, and as a fuel due to their combustible nature. They are also employed as oxygen scavengers in packaging.
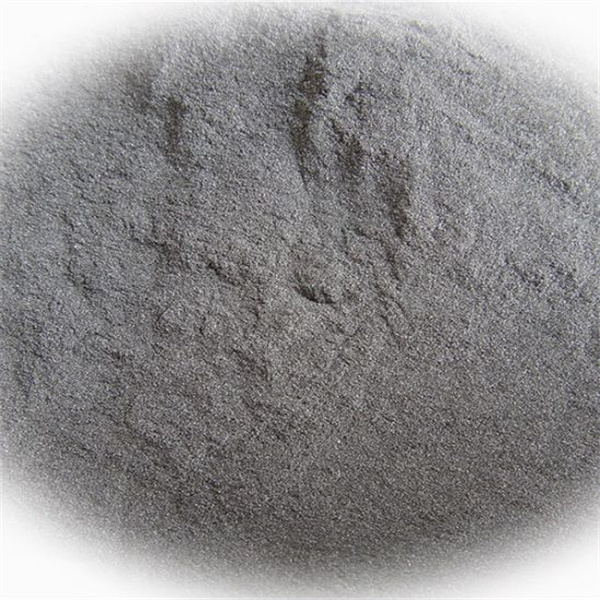
Cost Analysis of Iron Alloys Powder
The cost of iron alloys powder is influenced by the demand from various industries, particularly automotive, which is a significant consumer of iron powders. As of 2020, the global iron powder market size was valued at USD 5,587.3 million and is expected to grow to USD 8,308.2 million by 2028, exhibiting a CAGR of 5.2% during the forecast period. This growth is driven by rising disposable incomes and the increasing production of automobiles, especially in countries like China, Japan, and India.
Projected Market Growth Influences:
Factor | Influence on Cost |
---|---|
Increased automotive production | Drives up demand and potentially increases costs |
Adoption as a sustainable fuel option | Increases demand and may lead to higher costs |
Additive manufacturing advancements | Could reduce costs through efficient production |
The cost is also affected by its use as a sustainable fuel option, which is gaining popularity. Powdered iron is being adopted in industries as a low-carbon emission fuel with the potential to replace fossil fuels. This emerging application could influence the price due to the new demand in energy sectors.
Different Types of Iron Alloys Powder
Iron alloys powder is a key material in powder metallurgy, which refers to various forms of iron mixed with alloying elements to achieve different properties for specific applications. The types of iron alloy powders and their common alloying elements, characteristics, and applications are outlined below.
Types and Applications:
Powder Type | Alloying Elements | Characteristics | Applications |
---|---|---|---|
Pure Iron | Carbon, Oxygen | High green strength, low cost | Automotive, machinery |
Low Alloy Steels | C, Mn, Si, Cr, Mo | Enhanced strength, hardenability | Automotive, oil/gas |
Tool Steels | C, W, Mo, V, Co | High hardness, wear resistance | Cutting tools, dies |
Stainless Steels | Cr, Ni, Mo | Corrosion resistance, strength | Valves, marine applications |
Soft Magnetic Alloys | Ni, Mo, Cu, Nb | High permeability, low loss | Electromagnets, motors |
Tailoring Properties:
The properties of iron alloy powders can be tailored through the selection of specific alloying elements and processing conditions. Parameters that can be controlled include composition, particle size and shape, purity, apparent and sintered density, porosity, and surface area. These factors are manipulated using different production methods such as gas or water atomization, milling, compaction pressure, and sintering techniques.
Choosing a Supplier:
When selecting a supplier for iron alloy powders, factors such as powder quality, composition range, manufacturing capabilities, testing facilities, quality certifications, technical expertise, customer support, delivery records, location proximity, and pricing should be considered.
Functions of Iron Alloys Powder
Iron alloys powder serves a variety of functions in numerous industries, mainly due to its versatility and the different properties that can be achieved through various alloying elements. Below is a table highlighting the primary functions of iron alloys powder and their applications in different sectors.
Functions and Industrial Applications:
Function | Industrial Applications |
---|---|
Structural component fabrication | Automotive, aerospace, machinery |
Wear-resistant parts production | Tooling, industrial equipment |
Magnetic applications | Electronics, motors, inductors |
Additive manufacturing | 3D printing for complex part creation |
Metallurgy and sintering | Creating high-density materials |
Catalysis | Chemical industry for reactions |
Energy storage and generation | Used as a fuel in some industrial processes |
Iron alloys powder is particularly prominent in the automotive sector, where it is used to manufacture various engine, steering, suspension, and transmission parts due to its high dimensional accuracy and controlled porosity. Additionally, the powder plays a role in the production of high-strength and wear-resistant parts, and it is also a key component in magnetic materials.
The powder is not only used in traditional manufacturing methods but also plays a significant role in modern production techniques such as additive manufacturing, where it allows for the creation of complex designs that would be difficult to achieve with other materials.
Applications for Iron Alloys Powder
Iron alloys powder is used across various industries due to its ability to be tailored for different applications through alloying and processing. The following table summarizes the primary applications for iron alloys powder in different sectors.
Primary Applications Across Industries:
Industry | Applications |
---|---|
Automotive | Engine parts, gear components, brakes, suspension systems |
Aerospace | Structural components, landing gear, engine components |
Machinery | Gears, bearings, tool parts |
Electronics | Electromagnets, inductors, magnetic cores |
Additive Manufacturing | Prototyping, functional parts, complex geometries |
Healthcare | Surgical instruments, orthopedic implants |
Construction | Reinforcement materials, modular components |
Energy | Fuel for industrial heating processes, energy storage systems |
Iron alloys powder is integral in manufacturing parts with high precision and controlled properties. It is also pivotal in emerging technologies like 3D printing, where its properties enable the production of complex parts with reduced waste. In healthcare, it is used for producing surgical tools and implants due to its biocompatibility.
Benefits of Iron Alloys Powder
Iron alloys powder offers a range of benefits that can be leveraged across various manufacturing processes and applications. Below is a table that outlines the key benefits of using iron alloys powder and how it can be advantageous in different contexts.
Advantages and Benefits:
Benefit | Advantages in Context |
---|---|
High Precision | Enables near net-shape manufacturing, reducing post-processing |
Customizable Material Properties | Tailored alloy compositions for specific application requirements |
Cost-Effectiveness | Minimizes material waste and machining costs |
Versatility | Suitable for a wide range of industrial applications |
Enhanced Performance | Improved wear resistance and strength for durable components |
Innovation in Production | Facilitates complex designs with additive manufacturing |
Using iron alloys powder can significantly impact production efficiency and product performance. For instance, in the automotive industry, the precision of components made from iron powder alloys results in better engine performance and longevity. In the field of additive manufacturing, it allows for the creation of intricate designs that would be otherwise impossible or cost-prohibitive with traditional materials.
Choosing the Right Iron Alloys Powder
Selecting the appropriate iron alloys powder is critical for achieving the desired outcome in manufacturing processes. The table below provides guidance on factors to consider when choosing the right iron alloys powder for your needs.
Factors for Selection:
Selection Criteria | Considerations |
---|---|
Alloy Composition | Determine the alloying elements needed for the intended use |
Particle Size and Shape | Match the powder characteristics with the manufacturing process |
Purity and Quality | Ensure the powder meets the required standards and certifications |
Application Requirements | Consider the mechanical and physical properties needed |
Supplier Capabilities | Verify supplier’s production, testing, and support services |
Cost | Balance between quality needs and budget constraints |
The selection process involves understanding the specific requirements of the end product, such as strength, magnetic properties, or corrosion resistance, and then matching those needs with the properties provided by different iron powder alloys. Additionally, supplier reliability and technical support are crucial for ensuring consistent quality and performance.
Top Manufacturers of Iron Alloys Powder
Leading Iron Alloys Powder Manufacturers:
Manufacturer | Establishment | Headquarters |
---|---|---|
Advanced Technology & Materials Co. Ltd. | 1998 | Beijing, China |
Allegheny Technologies Incorporated (ATI) | 1996 | Texas, United States |
Carpenter Technology Corporation | 1889 | Pennsylvania, USA |
GKN Powder Metallurgy Engineering GMBH | 1934 | Michigan, USA |
Höganäs AB | 1797 | Höganäs, Sweden |
LIBERTY Steel Group | 1992 | London, UK |
Molyworks Materials Corporation | 2015 | California, USA |
POLEMA JSC | 1961 | Tula, Russia |
United Company Rusal Plc | 2007 | Moscow, Russia |
Sandvik AB | 1862 | Stockholm, Sweden |
These manufacturers are renowned for their extensive range of products and innovative solutions in the metal powder industry. They serve various sectors including automotive, aerospace, medical, and additive manufacturing, providing tailored iron alloys powders for specific applications and needs.
For more information on iron alloys powder and manufacturers, Metal3DP offers insights and access to a network of suppliers with diverse capabilities and products1.
Purchasing Iron Alloys Powder
When looking to purchase iron alloys powder, it’s important to consider suppliers who can provide the right quality and specifications for your application. Below is a guide to help identify where to make your purchase.
Iron Alloys Powder Suppliers:
Supplier | Specialty | Contact Information |
---|---|---|
Local Distributors | Accessible stock, quick delivery | Varies by location |
Direct from Manufacturers | Custom alloys, bulk orders | Refer to manufacturer’s website |
Online Marketplaces | Wide range, competitive pricing | Websites like Alibaba, ThomasNet |
Specialized Metal Powder Companies | High-quality, tailored solutions | Metal3DP |
Purchasing from a local distributor can be advantageous for small orders or when quick delivery is required. For more specific or large-scale needs, buying directly from manufacturers can be more cost-effective and provide more customization options. Online marketplaces offer a wide range and competitive pricing, while specialized metal powder companies can provide high-quality, tailored solutions for specialized applications.
For expert advice and a selection of high-quality iron alloys powder tailored to your needs, consider Metal3DP, which specializes in metal powders for additive manufacturing and other applications.
Product Advantages of Chinese Iron Alloys Powder
Chinese iron alloys powder offers several product advantages that make it an attractive option for various industries worldwide. The table below outlines the key benefits.
Advantages of Chinese Iron Alloys Powder:
Advantage | Description |
---|---|
Cost-Effectiveness | Competitive pricing due to large-scale production and market reach |
Innovation | Rapid advancement in material sciences and manufacturing technology |
Quality | Strict quality control standards and ISO certifications |
Diversity of Alloys | Wide range of alloy compositions tailored to industry needs |
Supply Chain Robustness | Strong supply chain and logistics capabilities |
Scalability | Capacity to scale production up or down according to demand |
Chinese manufacturers have invested significantly in research and development, leading to innovative products that often exceed international standards. Additionally, the robustness of the supply chain in China ensures reliable delivery and scalability of orders, from small batches to large-scale industrial requirements.
For those seeking to source high-quality iron alloys powder, Metal3DP is a resource that can provide access to a network of reputable Chinese suppliers, ensuring a combination of product quality and cost-effectiveness.
Best Supplier for Chinese Iron Alloys Powder
Identifying the best supplier for Chinese iron alloys powder depends on various factors including quality, reliability, and service. Below is a guideline to help determine the most suitable supplier.
Selecting the Top Chinese Iron Alloys Powder Supplier:
Criteria | Supplier Attributes |
---|---|
Quality Assurance | ISO certifications, product testing, and customer feedback |
Production Capabilities | Ability to deliver various alloy compositions and quantities |
Innovation | Investment in R&D and new product development |
Supply Chain Efficiency | Reliability in order fulfillment and logistics |
Customer Service | Technical support, responsiveness, and after-sales service |
Competitive Pricing | Offering the best value for the price point |
The “best” supplier is one that aligns closely with the specific needs of the purchaser, whether it’s for general manufacturing, specialized industrial applications, or cutting-edge additive manufacturing techniques.
To explore options and find a supplier that meets these criteria, consider visiting Metal3DP, which specializes in metal powders and can provide detailed information on reputable Chinese suppliers of iron alloys powder.