Inconel 600 is a standard engineering material for high temperature applications up to 1100°C. This guide covers Inconel 600 powder compositions, properties, manufacturing methods, applications, specifications, pricing, comparisons, and frequently asked questions when considering this nickel-chromium-iron alloy.
Typical Composition of Inconel 600 Powder
Element | Weight % |
---|---|
Nickel | 72% min |
Chromium | 14-17% |
Iron | 6-10% |
Carbon | 0.15% max |
Manganese | 1% max |
Sulfur | 0.015% max |
Silicon | 0.5% max |
Copper | 0.5% max |
The nickel-chromium balances high temperature strength with fabricability. Low carbon content minimizes harmful carbide precipitation during exposures above 550°C.
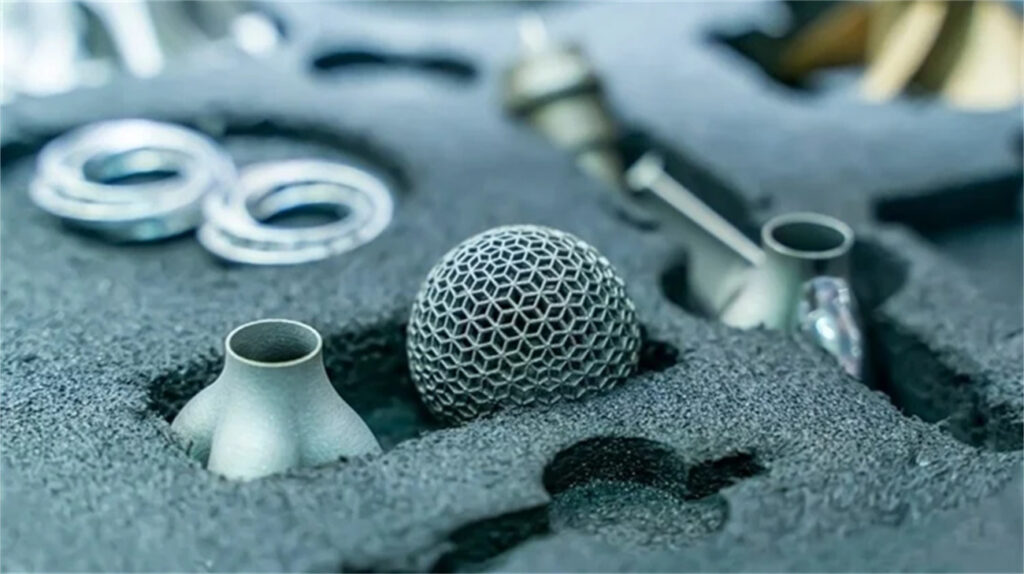
Key Properties and Characteristics
- Excellent high temperature strength up to 1150°C
- Resists chloride stress corrosion cracking
- More ductile than higher alloyed Inconels
- 100% weldable for similar or dissimilar material joints
- Hot workable using standard fabrication techniques
- Available in argon gas atomized spherical powder
Applications of Inconel 600 Powder
Industry | Common Components |
---|---|
Aerospace | Exhaust components, fasteners |
Chemical | Heat treating fixtures, reaction vessels |
Oil & Gas | Wellhead control lines, downhole tools |
Pollution Control | Coal gasification, exhaust recuperators |
Food processing | High pressure steam lines |
Good blend of fabricability and heat resistance suits Inconel 600 for demanding thermal environments needing occasional alloy welding, brazing or soldering steps during manufacturing or service.
Inconel 600 Powder Specifications
Standard | Grades Coverd |
---|---|
ASTM B163 | Seamless nickel and nickel alloy pipes |
ASTM B564 | Welded nickel and nickel alloy conduits |
ISO 14577 | Metallic materials for laser powder bed fusion |
No specifications explicitly for powder; application determines acceptance criteria. Standards for wrought product used as baseline.
Global Suppliers and Price Range
Company | Lead Time | Price/kg |
---|---|---|
Sandvik Osprey | 10-14 weeks | $50-$150 |
TLS Technik | 16 weeks | $60-$180 |
Atlantic Equipment | 12 weeks | $45-$130 |
Prices for 100+ kg quantity. Significant cost reduction above 500 kg volumes possible through negotiations.
Comparative Analysis
Attribute | Inconel 600 | Inconel 625 | Hastelloy B-2 |
---|---|---|---|
Max temperature | 1150°C | 1050°C | 1260°C |
Corrosion resistance | Moderate | Very good | Excellent |
Cost | Low | High | Very high |
Formability | Excellent | Moderate | Poor |
Among Ni alloys, Inconel 600 strikes best balance of temperature rating, fabricability and alloy cost. Prefer others if extreme corrosion or heat needed.
FAQ
Why is Inconel 600 preferred for high temperature fasteners?
Easy forming and joining characteristics facilitate nut and bolt manufacturing unlike highly alloyed grades needing specialty processing. Good creep strength above 550°C suits turbocharger applications.
What particle size range works best for laser powder bed fusion?
Around 25 to 45 microns optimal for balancing surface finish, resolution, and build speed. Too coarse powders hurt density and accuracy. Verify size distribution for adequate flowability.
What process parameters matter most when printing Inconel 600 parts?
Energy density, preheat control, powder spread parameters that ensure dense melting without excess oxidation or residual stresses leading to cracking during build and heat treatment steps.
What heat treatments apply for additively manufactured Inconel 600?
Stress relief aging similar to wrought processing helps attain consistent properties – 1050-1120°F for 1-3 hours typically specified. Precipitation treatments less common.
How is used Inconel 600 powder recycled?
retrieval systems filter, sieve, blend about 20-30% reused powder with fresh material continuously. Monitor oxygen levels and re-use fraction limits to avoid contamination issues.
Conclusion
To summarize, Inconel 600 powder provides an optimal combination of formability, weldability and heat resistance essential for component fabrication across demanding industries via additive manufacturing or other powder metallurgy techniques.