Peleburan laser selektif (SLM) adalah proses manufaktur aditif logam yang menggunakan laser untuk melebur bubuk logam menjadi komponen yang sepenuhnya padat. Panduan ini membahas teknologi SLM, sistem, bahan, aplikasi, manfaat, dan pertimbangan ketika mengimplementasikan manufaktur aditif dengan SLM.
Pengantar SLM Manufaktur Aditif
Selective laser melting (SLM) adalah teknik manufaktur aditif fusi unggun serbuk yang menggunakan laser berdaya tinggi untuk secara selektif melelehkan dan memadukan partikel serbuk logam lapis demi lapis untuk membangun komponen 3D yang sangat padat secara langsung dari data CAD.
Atribut utama dari teknologi SLM:
- Menggunakan sinar laser terfokus untuk melelehkan logam bubuk
- Menambahkan materi hanya jika diperlukan di setiap lapisan
- Memungkinkan geometri kompleks yang tidak dapat dicapai dengan pengecoran atau pemesinan
- Menciptakan komponen logam berbentuk hampir bersih dengan kepadatan tinggi
- Bahannya meliputi aluminium, titanium, baja tahan karat, paduan
- Volume pembuatan bagian kecil hingga sedang
- Ideal untuk komponen yang kompleks dan bervolume rendah
- Menghilangkan kebutuhan akan perkakas keras seperti cetakan atau cetakan
- Mengurangi limbah secara signifikan dibandingkan dengan metode subtraktif
- Memungkinkan desain yang ringan dan konsolidasi bagian
- Memungkinkan peningkatan fungsional dengan struktur yang direkayasa
Dengan kemampuannya, SLM memberikan manfaat yang mengubah permainan untuk desain produk yang inovatif dan manufaktur yang ramping. Namun, dibutuhkan keahlian untuk menguasai prosesnya.
Cara Kerja Manufaktur Aditif SLM
Proses produksi SLM terdiri dari:
- Menyebarkan dan meratakan lapisan tipis serbuk logam pada pelat rakitan
- Memindai sinar laser terfokus secara selektif untuk melelehkan bubuk
- Menurunkan platform bangunan dan mengulangi pelapisan dan peleburan
- Melepaskan komponen yang sudah selesai dari alas bedak
- Bagian pasca-pemrosesan sesuai kebutuhan - pembersihan, perlakuan panas, dll.
Mengontrol laser, pola pemindaian, atmosfer ruang dan parameter lainnya secara tepat, sangat penting untuk menghasilkan komponen logam yang padat dan berkualitas tinggi dengan SLM.
Sistem SLM memiliki generator laser, optik pengiriman sinar, sistem pengiriman bubuk, ruang pembuatan, penanganan gas inert, dan kontrol pusat. Performa sangat bergantung pada rekayasa sistem dan penyetelan parameter build.
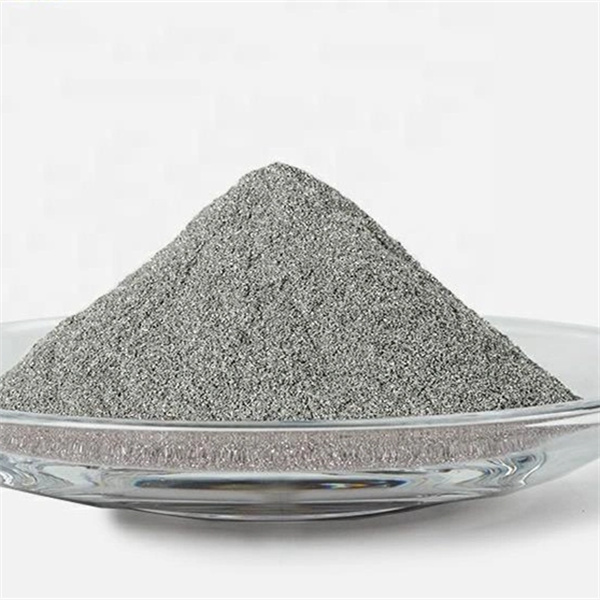
Produsen Peralatan SLM
Pemasok global terkemuka untuk sistem manufaktur aditif SLM meliputi:
Perusahaan | Model | Kisaran Ukuran Bangun | Bahan | Kisaran Harga |
---|---|---|---|---|
Solusi SLM | NextGen, NXG XII | 250 x 250 x 300 mm <br>500 x 280 x 365 mm | Ti, Al, Ni, Baja | $400k - $1.5M |
EOS | M 300, M 400 | 250 x 250 x 325 mm <br> 340 x 340 x 600 mm | Ti, Al, Ni, Cu, Baja, CoCr | $500k - $1.5M |
Trumpf | TruPrint 3000 | 250 x 250 x 300 mm <br> 500 x 280 x 365 mm | Ti, Al, Ni, Cu, Baja | $400k - $1M |
Konsep Laser | Garis X 2000R | 800 x 400 x 500 mm | Ti, Al, Ni, Baja, CoCr | $1M+ |
Renishaw | AM400, AM500 | 250 x 250 x 350 mm <br>395 x 195 x 375 mm | Ti, Al, Baja, CoCr, Cu | $500k - $800k |
Pemilihan sistem tergantung pada kebutuhan ukuran bangunan, bahan, kualitas, biaya, dan dukungan layanan. Bermitra dengan penyedia solusi SLM yang berpengalaman disarankan untuk mengevaluasi opsi dengan benar.
Karakteristik Proses SLM
SLM melibatkan interaksi yang kompleks antara berbagai parameter proses. Berikut adalah karakteristik utamanya:
Laser - Daya, panjang gelombang, mode, kecepatan pemindaian, jarak penetasan, strategi
Bedak - Bahan, ukuran partikel, bentuk, laju pengumpanan, kepadatan, kemampuan mengalir, penggunaan ulang
Suhu - Pemanasan awal, peleburan, pendinginan, tekanan termal
Suasana - Jenis gas inert, kandungan oksigen, laju aliran
Bangun Piring - Bahan, suhu, lapisan
Strategi Pemindaian - Pola penetasan, rotasi, garis tepi
Dukungan - Meminimalkan, antarmuka, penghapusan
Pengolahan pasca - Perlakuan panas, HIP, permesinan, finishing
Memahami hubungan antara parameter ini sangat penting untuk mencapai suku cadang bebas cacat dengan sifat mekanis yang dioptimalkan.
Pedoman Desain Bagian SLM
Desain komponen yang tepat sangat penting untuk keberhasilan manufaktur aditif SLM:
- Desain dengan mempertimbangkan prinsip-prinsip AM vs metode konvensional
- Mengoptimalkan geometri untuk mengurangi berat, penggunaan material, meningkatkan kinerja
- Meminimalkan kebutuhan akan penyangga dengan menggunakan sudut mandiri
- Memungkinkan untuk mendukung wilayah antarmuka dalam desain
- Arahkan komponen untuk mengurangi tekanan dan menghindari cacat
- Mempertimbangkan efek penyusutan termal dalam fitur
- Desain saluran interior untuk menghilangkan bubuk yang tidak meleleh
- Mengatasi potensi lengkungan pada bagian yang menggantung atau bagian yang tipis
- Desain permukaan akhir yang memperhitungkan kekasaran as-built
- Mempertimbangkan efek garis lapisan pada kinerja kelelahan
- Desain antarmuka fiksasi untuk melepaskan komponen dari bedengan serbuk
- Meminimalkan volume bubuk yang tidak disinter yang terperangkap
Perangkat lunak simulasi membantu menilai tekanan dan deformasi pada komponen SLM yang kompleks sebelum mencetak.
Opsi Bahan SLM
Berbagai paduan dapat diproses dengan teknologi SLM, dengan sifat material akhir yang bergantung pada parameter:
Kategori | Paduan Umum |
---|---|
Titanium | Ti-6Al-4V, Ti 6242, TiAl, Ti-5553 |
Aluminium | AlSi10Mg, AlSi12, Scalmalloy |
Baja tahan karat | 316L, 17-4PH, 304L, 4140 |
Baja Perkakas | H13, Baja Perkakas, Baja Perkakas Tembaga |
Paduan Nikel | Inconel 625, 718, Haynes 282 |
Kobalt Chrome | CoCrMo, MP1, CoCrW |
Logam Mulia | Emas, Perak |
Memilih paduan yang kompatibel dan melakukan pemanggilan dalam parameter build yang memenuhi syarat sangat penting untuk mencapai performa material yang dibutuhkan.
Aplikasi SLM Utama
SLM memungkinkan kemampuan transformatif di seluruh industri:
Industri | Aplikasi SLM yang umum |
---|---|
Dirgantara | Bilah turbin, impeler, komponen UAV |
Medis | Implan ortopedi, alat bedah, perangkat khusus pasien |
Otomotif | Komponen yang lebih ringan, perkakas khusus |
Energi | Katup minyak/gas yang kompleks, penukar panas |
Industri | Sisipan pendingin, jig, perlengkapan, pemandu yang sesuai |
Pertahanan | Drone, senjata api, kendaraan & komponen pelindung tubuh |
Manfaat dibandingkan dengan manufaktur konvensional meliputi:
- Kemampuan kustomisasi massal
- Waktu pengembangan yang lebih singkat
- Kebebasan mendesain untuk peningkatan performa
- Konsolidasi bagian dan pengurangan bobot
- Menghilangkan penggunaan material yang berlebihan
- Konsolidasi rantai pasokan
Validasi kinerja mekanis yang cermat diperlukan saat menerapkan komponen SLM dalam aplikasi penting.
Pro dan Kontra dari Manufaktur Aditif SLM
Keuntungan:
- Kebebasan desain dimungkinkan melalui proses aditif
- Kompleksitas dicapai tanpa peningkatan biaya
- Menghilangkan kebutuhan akan perkakas keras seperti cetakan atau cetakan
- Menggabungkan sub-rakitan menjadi komponen tunggal
- Ringan dari struktur organik yang dioptimalkan untuk topologi
- Kustomisasi dan produksi volume rendah
- Mengurangi waktu pengembangan dibandingkan dengan pengecoran/pemesinan
- Rasio kekuatan-terhadap-berat yang tinggi dari struktur mikro yang halus
- Sangat meminimalkan limbah material dibandingkan proses subtraktif
- Produksi tepat waktu dan terdesentralisasi
- Mengurangi waktu tunggu dan inventaris suku cadang
Keterbatasan:
- Volume pembuatan yang lebih kecil daripada proses AM logam lainnya
- Akurasi dan hasil akhir permukaan yang lebih rendah daripada pemesinan CNC
- Pilihan paduan yang memenuhi syarat terbatas dibandingkan dengan pengecoran
- Uji coba yang signifikan untuk mengoptimalkan parameter build
- Sifat material anisotropik dari penumpukan lapisan demi lapisan
- Potensi tegangan sisa dan cacat retak
- Kesulitan penghilangan serbuk dari geometri internal yang kompleks
- Sering kali memerlukan pasca-pemrosesan untuk mendapatkan properti akhir
- Biaya peralatan lebih tinggi daripada pencetakan 3D polimer
- Diperlukan fasilitas khusus dan penanganan gas inert
Ketika diterapkan secara tepat, SLM memungkinkan terobosan kinerja yang tidak mungkin dilakukan dengan cara lain.
Menerapkan Manufaktur Aditif SLM
Langkah-langkah utama saat mengadopsi teknologi SLM meliputi:
- Mengidentifikasi aplikasi yang sesuai berdasarkan kebutuhan
- Mengonfirmasi kelayakan SLM untuk desain yang dipilih
- Mengembangkan protokol kualifikasi proses yang ketat
- Berinvestasi dalam peralatan SLM yang sesuai
- Mengamankan keahlian dalam proses bedengan serbuk logam
- Menetapkan prosedur kualitas bahan yang ketat
- Menguasai pengembangan dan pengoptimalan parameter
- Menerapkan metode pasca-pemrosesan yang kuat
- Sifat mekanis yang memenuhi syarat dari komponen jadi
Rencana pengenalan metodis yang difokuskan pada aplikasi berisiko rendah meminimalkan jebakan saat menambahkan kemampuan aditif SLM. Bermitra dengan biro layanan SLM yang berpengalaman atau OEM sistem memberikan akses ke keahlian.
Analisis Biaya Produksi SLM
Ekonomi produksi SLM melibatkan:
- Biaya peralatan mesin yang tinggi
- Tenaga kerja untuk penyiapan pembuatan, pasca-pemrosesan, kontrol kualitas
- Biaya material dari bahan baku bubuk logam yang sesuai
- Penyelesaian bagian - pemesinan, pengeboran, deburring, dll.
- Overhead - fasilitas, gas inert, pemeliharaan
- Pengembangan proses trial-and-error awal
- Biaya menurun dengan pengalaman dan volume produksi
- Menjadi ekonomis pada volume sekitar 1-500 unit
- Memberikan keuntungan biaya tertinggi untuk geometri yang kompleks
Memilih paduan yang memenuhi syarat dari pemasok yang memiliki reputasi baik disarankan untuk mencegah cacat. Bermitra dengan penyedia layanan menawarkan jalur adopsi yang lebih cepat dan berisiko lebih rendah.
SLM Dibandingkan dengan Proses Lainnya
Proses | Perbandingan dengan SLM |
---|---|
Mesin CNC | SLM memungkinkan bentuk-bentuk kompleks yang tidak dapat dibuat melalui proses subtraktif. Tidak memerlukan perkakas yang keras. |
Cetakan Injeksi Logam | SLM tidak memiliki biaya perkakas yang tinggi. Sifat material yang lebih baik daripada MIM. |
Die Casting | SLM memiliki biaya perkakas yang lebih rendah. Tidak ada batasan ukuran. Geometri yang sangat kompleks dapat dicapai. |
Laminasi Lembar | SLM menciptakan material yang sepenuhnya padat dan isotropik dibandingkan komposit laminasi. |
Pengaliran Pengikat | SLM menciptakan bagian hijau yang sepenuhnya padat dibandingkan bagian yang disemprotkan pengikat berpori yang membutuhkan sintering. |
DMLS | SLM memberikan akurasi yang lebih tinggi dan sifat material yang lebih baik daripada DMLS polimer. |
EBM | Peleburan berkas elektron memiliki tingkat pembuatan yang lebih tinggi tetapi resolusi yang lebih rendah daripada SLM. |
Setiap proses menawarkan keunggulan spesifik berdasarkan persyaratan aplikasi, ukuran batch, bahan, dan kebutuhan kinerja.
Prospek Masa Depan untuk Manufaktur Aditif SLM
SLM siap untuk pertumbuhan yang signifikan di tahun-tahun mendatang yang didorong oleh:
- Perluasan material yang sedang berlangsung dengan lebih banyak ketersediaan paduan
- Volume pembangunan yang lebih besar memungkinkan produksi skala industri
- Hasil akhir permukaan yang lebih baik dan toleransi yang lebih ketat
- Peningkatan keandalan dan produktivitas sistem
- Sistem hibrida baru yang mengintegrasikan pemesinan CNC
- Menurunnya biaya meningkatkan kelayakan bisnis
- Algoritme dan simulasi pengoptimalan lebih lanjut
- Penghapusan dukungan otomatis dan pasca-pemrosesan
- Pertumbuhan suku cadang yang memenuhi syarat untuk industri yang diatur
- Kemajuan berkelanjutan dari desain dengan kompleksitas tinggi
SLM akan menjadi arus utama untuk berbagai aplikasi yang semakin meluas di mana kemampuannya memberikan keunggulan kompetitif yang berbeda.
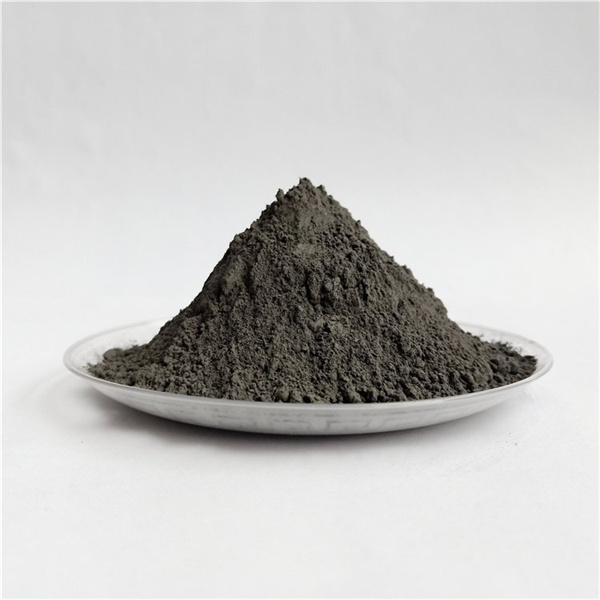
Pertanyaan Umum
Bahan apa saja yang dapat Anda proses dengan teknologi SLM?
Titanium, aluminium, baja tahan karat, baja perkakas, paduan nikel, dan krom kobalt biasanya diproses.
Seberapa akuratkah SLM?
Akurasi sekitar ± 0,1-0,2% adalah tipikal, dengan resolusi fitur minimum ~100 mikron.
Berapa biaya sistem SLM?
Peralatan SLM berkisar dari $300.000 hingga $1.000.000+, tergantung pada ukuran, kemampuan, dan opsi.
Jenis pasca-pemrosesan apa yang diperlukan?
Perlakuan panas, HIP, finishing permukaan, dan/atau pemesinan dapat digunakan. Penghapusan dukungan juga diperlukan.
Industri apa saja yang menggunakan manufaktur aditif SLM?
Sektor kedirgantaraan, medis, otomotif, industri, dan pertahanan merupakan pengguna awal SLM.
Bahan apa yang tidak cocok untuk SLM?
Logam yang sangat reflektif seperti tembaga atau emas masih menjadi tantangan. Sifat material untuk beberapa paduan masih terus berkembang.
Permukaan akhir apa yang dapat dicapai?
Kekasaran permukaan SLM as-built berkisar antara 5-15 mikron Ra. Penyelesaian akhir bisa lebih jauh memperbaiki hal ini.
Seberapa besar bagian yang dapat Anda buat dengan SLM?
Volume rakitan standar berkisar hingga 500mm x 500mm x 500mm. Mesin yang lebih besar dapat mengakomodasi komponen yang lebih besar.
Apakah SLM cocok untuk suku cadang produksi penggunaan akhir?
Ya, SLM semakin banyak digunakan untuk komponen produksi akhir, dengan contoh di industri kedirgantaraan dan medis.