Overview of Electron Beam Melting
Electron beam melting (EBM) is an additive manufacturing process that uses an electron beam power source to selectively melt and fuse metallic powder material layer-by-layer to build up components.
Some key details about electron beam melting include:
- Uses an electron beam gun under vacuum to melt the powder.
- Builds occur at high temperatures, enabling good interlayer bonding.
- Primarily used for Ti, Ni, Co alloys, and other high performance materials.
- Provides near-full density parts with properties equaling or exceeding traditionals means.
- Supports complex geometries not feasible by conventional fabrication.
- Commonly used in aerospace, medical, and automotive industries.
- Also referred to as electron beam additive manufacturing (EBAM) or electron beam freeform fabrication (EBF3).
Electron Beam Melting Equipment
Type | Description |
---|---|
Electron beam gun | Generates and focuses high energy beam to melt the material. Key component. |
Powder bed | Contains powder layers raked by blades or rollers. Built on a movable platform. |
Vacuum chamber | Entire system is under vacuum during builds. Critical for beam focus. |
Control system | Software slices and controls build parameters. Provides in-process monitoring and control. |
Handling system | For loading/unloading parts and recycling unused powder. |
Shielding | Lead shielding required around chamber due to x-ray generation. |
Materials Used in Electron Beam Melting
Material | Key Properties | Typical Applications |
---|---|---|
Titanium alloys | High strength-to-weight ratio, biocompatibility | Aerospace, medical implants |
Nickel alloys | Corrosion resistance, high strength | Turbines, rocket components |
Cobalt-chrome alloys | Hardness, wear/corrosion resistance | Medical implants, tooling |
Stainless steel | Good durability, easier processing | Industrial tooling, molds |
Aluminum alloys | Low weight | Aerospace, automotive |
Precious metals | Highly chemically inert | Jewelry, medical |
EBM can process high-performance alloys difficult with laser-based processes due to power intensity.
EBM Process Specifications
Parameter | Typical Range |
---|---|
Beam power | 1-3 kW |
Beam voltage | 30-150 kV |
Build size | 200 x 200 x 350 mm max |
Layer height | 50-200 μm |
Build speed | 5-100 cm3/hr |
Beam size | 0.1-1 mm diameter |
Vacuum level | 5 x 10-4 mbar |
Beam focus | 0.1-0.5 mm spot size |
EBM systems allow adjusting parameters like beam power, speed, focus etc. to tune for specific materials.
Suppliers of EBM Systems
Supplier | Key Details | Starting Price Range |
---|---|---|
Supplier 1 | Pioneer of EBM technology. Largest installed base. | $1.2-$1.5 million |
Supplier 2 | Systems for smaller parts. Faster scan speeds. | $0.8-$1.2 million |
Supplier 3 | Research systems. Open parameters control. | $0.5-$0.8 million |
System costs vary based on build volume, beam power, included accessories and software capabilities.
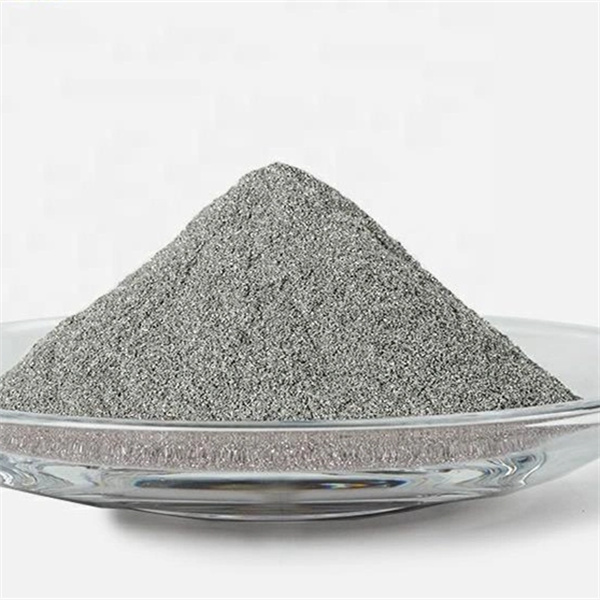
How to Choose an EBM System Supplier
When selecting an EBM system supplier, key factors to consider include:
- Technical expertise – Supplier should have in-depth knowledge of electron beam physics, metallurgy, and process experience.
- Proven technology – Look for well-established suppliers with a track record of successful system installations.
- Application experience – Supplier should understand client application needs and recommend appropriate system specifications.
- System reliability – Choose suppliers known for engineering robust EBM systems with reasonable uptimes and service intervals.
- Control software – Supplier should offer user-friendly software for programming, monitoring, and optimizing builds.
- Technical support – Look for responsive support engineers to troubleshoot issues and help improve process outcomes.
- Training – Supplier should provide comprehensive training on equipment operation, maintenance, and safety.
- Future roadmap – Select a supplier investing in ongoing EBM innovations for your long-term needs.
How to Optimize the EBM Process
To achieve high quality EBM printed parts, follow these process optimization best practices:
- Start with high purity spherical powder feedstock tailored for EBM. Handling, storage, and reuse of powder also crucial.
- Take time to calibrate the electron beam profile and focus. Beam shaping can further improve density.
- Dial in optimal beam current and scanning speed for stable, homogeneous melting.
- Adjust beam focus dynamically during builds to account for geometry changes.
- Set hot bed temperature over 700°C to reduce residual stresses and avoid cracking.
- Tune parameters separately for contours vs. hatch regions to improve surface finish and resolution.
- Optimize support structures to minimize while still providing enough anchoring and heat dissipation.
- Account for parameter differences between various materials – titanium alloy settings differ from nickel superalloys, for example.
- Take an iterative, empirical approach – run test builds while varying parameters to find the sweet spots.
How to Design Parts for EBM
To successfully design components suited to the EBM process:
- Design walls thicker than 0.4 mm to ensure full melting and prevent cracking.
- Include a 5-15° draft angle on surfaces angled in the build direction to aid powder removal.
- Minimize unsupported overhangs to reduce sagging and defects on downward facing surfaces.
- Incorporate lattices and conformal cooling channels enabled by EBM’s design freedom.
- Consolidate sub-assemblies into single parts to improve quality and reduce processing steps.
- Position parts in build chamber to minimize support requirements and avoid collisions during raking.
- Account for 20-50% lower mechanical strength horizontally vs vertically due to layer-based construction.
- Allow an additional stock of 0.5-1mm for post-processing like surface machining or grinding.
Work closely with EBM machine operators during part design iterations to leverage their process knowledge.
How to Post-Process EBM Parts
Typical post-processing steps for EBM printed components include:
- Support removal – Carefully remove support structures, if any, by hand or using cutting tools.
- Stress relieving – Heat treat at 600-800°C for 1-3 hours to relieve residual stresses.
- Machining – CNC milling, turning, drilling to improve dimensional accuracy and surface finish.
- Grinding – Automated or manual grinding brings precision tolerances and finer finishes.
- Polishing – Yields excellent surface finish free of any adhered powder particles.
- Coatings – Apply functional coatings for hardness, wear resistance, electrical insulation etc.
- Hot isostatic pressing (HIP) – Closes internal voids and further improves fatigue performance.
- Joining – Integrate features like threaded holes, fasteners etc. using suitable techniques.
Post-process EBM parts using qualified operators with experience handling the specific alloy composition.
How to Install and Integrate EBM Parts
When preparing EBM printed parts for integration into final products:
- Thoroughly clean surfaces to remove loose powder and oxidation. Proper cleaning improves bonding.
- Apply protective coatings as needed – hard anodizing, plating, painting etc. enhance corrosion and wear protection.
- Account for thermal expansion differences when joining EBM parts to other metal components to avoid stresses.
- Select joining techniques suitable for the material – welding, mechanical fastening, adhesives etc.
- Use thermal management – preheating and controlled cooling rates – when welding or brazing.
- Validate assembly functionality under operating loads and environments using prototyping and testing.
- Inspect for defects using techniques like x-ray, UT, penetrant testing – critical for high liability applications.
Work side-by-side with designers and engineers when integrating EBM parts to ensure robust, optimized performance in the end assembly.
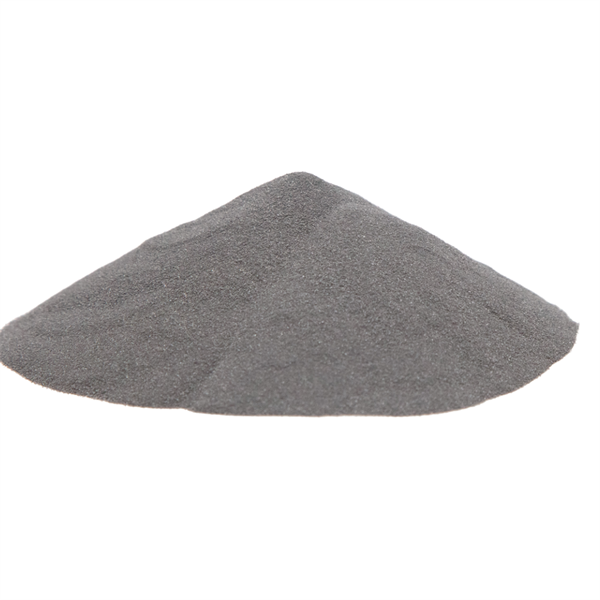
Operating and Maintaining EBM Printers
To sustain optimal EBM printer operation and prevent downtime:
- Perform scheduled preventative maintenance per supplier guidelines – replace worn components like shields.
- Check x-y-z accuracy of the beam regularly using calibration methods. Realign if needed.
- Inspect key vacuum system components – leak check seals, monitor pumps, replace filters periodically.
- Calibrate integrated process monitoring sensors at prescribed intervals.
- Monitor vacuum quality continuously – identify and correct any leaks immediately.
- Follow recommended cleaning procedures – keep build chamber, powder handling system clean.
- Only allow qualified technicians to service the high voltage beam supply and gun.
- Keep spare/wear parts like shields, pumps, filters stocked to minimize downtime.
Schedule maintenance shutdowns during low volume periods. Monitor EBM system health proactively between builds.
Pros and Cons of Electron Beam Melting
Electron beam melting has both advantages and limitations compared to conventional manufacturing methods:
Advantages
- Fabricates complex geometries not possible by other means.
- Consolidates sub-assemblies into single parts.
- Reduces waste – uses only required material.
- Shortens development time for new designs.
- Properties equal or exceed traditionals means like casting.
- Does not require binders or extra supports – results in purer material.
Disadvantages
- Higher per-part cost at low production volumes.
- Size limitations based on build chamber.
- Material selection limited compared to other AM processes.
- Post-processing often required to achieve final parts.
- Anisotropic properties due to layer-based construction.
- Requires significant power input for the electron beam.
When weighing EBM versus conventional methods, consider quantities, size, properties, lead time, and costs. EBM excels for complex, high-performance metal parts but with higher setup costs.
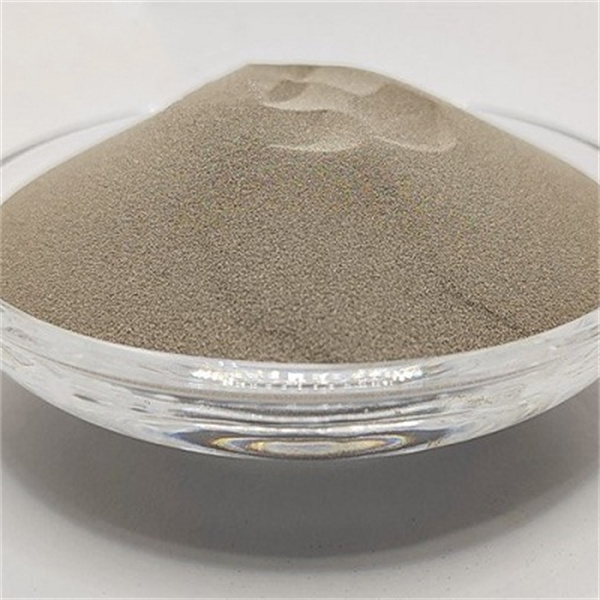
FAQ
Q: What materials can you process with EBM?
A: Primarily titanium, nickel, cobalt, and stainless steel alloys to date. Research is expanding material options including aluminum, tool steels, gold, tantalum, and more.
Q: What is the main difference between EBM and selective laser melting (SLM)?
A: EBM uses an electron beam energy source whereas SLM uses a laser. The higher beam power densities achievable with EBM allow processing of more refractory metals.
Q: What industries use EBM printing?
A: Aerospace is the largest adopter to date for components like turbine blades. But medical, automotive, and industrial sectors are also growing users of EBM.
Q: Does EBM produce porous or fully dense parts?
A: EBM can attain over 99% density with optimal parameters. The high temperature builds improve diffusion bonding between layers.
Q: What size parts can you create with EBM?
A: The maximum size is restricted by the build envelope, typically around 250 x 250 x 300 mm. Larger systems are in development targeting 500 mm cubes.
Q: How accurate is EBM compared to CNC machining?
A: EBM can achieve tolerances down to 0.1-0.3 mm when well calibrated. But machining is needed to reach tighter tolerances below 0.05 mm.
Q: What are some key benefits of EBM?
A: Design freedom, part consolidation, rapid prototyping, high strength alloys, reduced waste, and short lead times versus traditional fabrication.
Q: What safety precautions are required for EBM?
A: EBM systems generate x-ray radiation so adequate lead shielding of the build chamber is critical. Only trained personnel should operate.