Overview of electron beam melting equipment Technology
electron beam melting equipment is an additive manufacturing technology used to fuse metal powders together layer by layer utilizing a high-power electron beam in a vacuum environment. EBM equipment offers capabilities unmatched by other metal 3D printing methods in terms of build rate, part density, residual stress, and mechanical properties.
Key attributes of electron beam melting technology include:
Table 1: Overview of Electron Beam Melting Characteristics
Attribute | Details |
---|---|
Heat Source | High power electron beam |
Environment | High vacuum |
Feedstock | Metal powder bed |
Beam Control | Electromagnetic lenses/deflection coils |
Build Mode | Layer by layer metal fusion |
Applications | Aerospace, Medical, Automotive, Tooling |
EBM machines provide rapid melting of conductive materials into fully dense components with material properties equivalent or superior to traditional manufacturing methods.
The controlled vacuum environment and intelligent energy delivery minimize issues with oxidation or contamination during processing. This facilitates very high densities and excellent structural integrity perfect for critical applications.
By leveraging high beam power for rapid scanning rates across each layer, EBM enables extremely fast build speeds unattainable using laser-based systems. This advantage in productivity is a key driver for technology adoption.
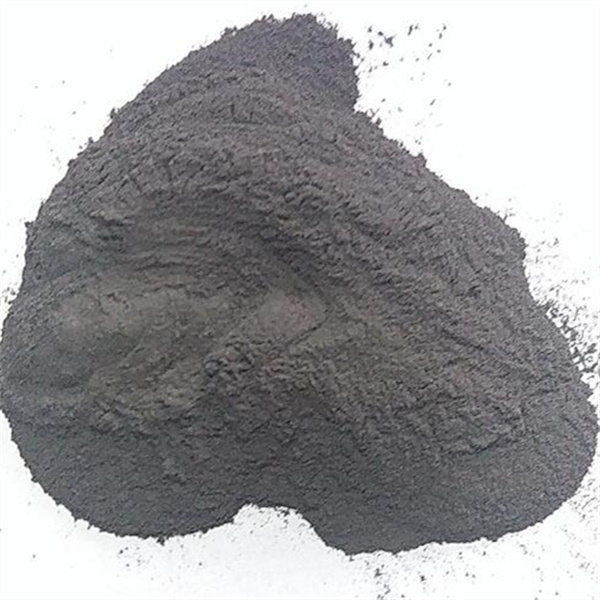
Types of electron beam melting equipment Systems
There are several categories of EBM equipment on the market offering various build envelope sizes, beam power levels, and production capacities tailored towards different applications.
Table 2: Types of Electron Beam Melting Equipment
Machine Class | Build Size | Beam Power | Typical Uses |
---|---|---|---|
Small envelopes | 150 x 150 x 150 mm | 3-4 kW | Dental, medical devices |
Standard platforms | 200 x 200 x 350 mm | 6-8 kW | Aerospace components, tooling |
Mid-range platforms | 400 x 400 x 400 mm | 14-16 kW | Automotive, larger aircraft parts |
Large envelopes | 800 x 800 x 500 mm | 30-60 kW | Structural brackets, turbine blades |
Larger equipment sizes facilitate bigger components for industries like aerospace and automotive to reduce assembly part counts. Smaller, lower power machines target high-value applications in medical and dental sectors.
Most EBM system builders offer modular machine architectures to scale capacity, beam power, and build volume as customer adoption and application requirements advance over time.
Fundamentals of Electron Beam Melting Technology
The core subsystems and processing steps involved in electron beam additive manufacturing include:
Table 3: Overview of Electron Beam Melting Fundamentals
Stage | Function | Key Components |
---|---|---|
1. Powder handling | Feed new layers of material | Powder hoppers and rakes |
2. Beam generation | Create/accelerate electron beam | Tungsten filament cathode, anode voltage |
3. Beam focusing | Electromagnetics converge beam | Magnetic coil lenses |
4. Deflection | Direct focused beam location | Deflection coils |
5. Vacuum system | Ensure contaminant-free environment | Diffusion pumps, valves, sensors |
6. Control system | Coordinate and monitor all functions | Computer, software, sensors |
An EBM machine requires the integrated operation of these subsystems to efficiently manufacture parts layer-by-layer from metal powder:
- High-speed beam deflection steers the molten regions precisely across each powder bed layer
- Vacuum removes gaseous contamination preventing material oxidation/nitridation
- Powder rakes efficiently spread fresh material ensuring density
- Closed loop sensors provide feedback ensuring dimensional accuracy
- Robust computer controls coordinate every aspect of the build process
The unique combination of a pure metal powder consumable with a high intensity energy source inside a vacuum chamber enables very rapid melting and solidification for exceptional metallurgical properties.
Understanding these fundamental principles helps buyers select equipment optimized for their goals whether maximizing productivity, part quality, operational costs, or application requirements.
Specifications of Electron Beam Melting Machines
There are numerous performance-driving specifications purchasers must consider when selecting EBM equipment best matching their production needs and operating conditions.
Table 4: Key Electron Beam Melting Equipment Specifications
Parameter | Typical Range | Importance |
---|---|---|
Beam power | 3-60 kW | Build rates, max part size |
Beam speed | Up to 8 m/s | Layer times, productivity |
Spot size | 50-200 μm | Resolution, fine feature definition |
Current | 1-50 mA | Material compatibility, beam optimization |
Accelerating voltage | 30-150 kV | Penetration depth, unmolten powder |
Vacuum level | 5 x 10-5 mbar | Purity, material integrity |
Powder layer thickness | 50-200 μm | Vertical resolution, density |
Understanding specifications like beam power, scanning speed, spot size, and minimum layer thickness enables appropriate machine selection for the intended application and throughput targets.
Other vital factors influencing system selection encompass:
- Control software: Capabilities for efficient build setup, optimization tools for parameter development, monitoring/analytics features, and compatibility with downstream CAD/CAM digital workflows.
- Materials palette: Number of qualified materials available from the OEM determines range of applications accessible to the equipment. Priority metal choices include titanium, nickel superalloys, tool steels, stainless steel, cobalt chrome, and aluminum.
- Ancillary equipment: Requirements for supplementary powder handling tools, post-processing stations, sieving tools, external heat treatment, HIP furnaces, and powder recycling systems.
- Services: Value of maintenance contracts, application optimization assistance, operator training services, and equipment relocation provisions.
Careful assessment of machine specifications against current and future production demands facilitates appropriate investment decisions in EBM capacity.
Overview of Electron Beam Melting Process Economics
Aside from pure equipment acquisition costs, manufacturing organizations need realistic projections of the complete production economics associated with bringing EBM technology online.
Table 5: Summary of EBM Processing Economics
Cost Element | Typical Range |
---|---|
Machine acquisition | $800,000 to $2,500,000 |
Installation | $50,000 to $250,000 |
Facility infrastructure | $100,000 to $500,000 |
Auxiliary powder equipment | $50,000 to $150,000 |
Annual materials | $100,000 to $800,000 |
Consumable parts | $20,000 to $100,000 |
Operating labor | 1 to 3 operators per system |
Energy consumption | $15,000 to $50,000 |
Maintenance contracts | $50,000 to $150,000 |
With machine prices ranging from around $800,000 for starter systems up to $2,500,000 for large industrial solutions, equipment represents just one portion of the overall investment equation.
Other key variables influencing operating profitability and return on investment calculations encompass:
- Materials usage: Powder is up to 30% of total part cost stack, optimize buy:make strategies and reuse ratios.
- Labor: Manual versus automated powder/part handling impacts staffingrequirements. Pursue build optimization to maximize unattended run times.
- Facility: Installation, energy, environmental control, and ancillary equipment expenses add up. Factor in safety, utilities, and compliance costs.
- Maintenance: Preventative upkeep is crucial for uptime, production quality, and equipment longevity. Weigh OEM vs in-house service options.
Analyzing these cost factors before acquiring EBM capacity facilitatesrealistic business planning. Modeling part production scenarios using actual performance data improves visibilityinto financial risks and profitability outlooks.
Popular Materials for Electron Beam Melting
The high beam intensity and vacuum environment make EBM suitable for processing reactive and refractory alloys difficult to melt with other additive methods or casting processes.
Table 6: Common Materials Used in Electron Beam Melting
Material Class | Alloy Examples | Applications |
---|---|---|
Titanium alloys | Ti-6Al-4V, Ti-6Al-4V ELI | Aerospace structures |
Nickel superalloys | Inconel 718, Inconel 625 | Turbine blades, exhaust systems |
Tool steels | H13, Maraging 300 | Injection molds, tooling |
Cobalt chrome | CoCrMo | Medical/dental implants |
Stainless steels | 17-4PH, 316L | Corrosion resistance needed |
Exotic & custom alloys | Cu, Al, Ta, W, Mo | Electronics, research |
The most popular materials for EBM remain titanium alloys for lightweight aerospace components, nickel superalloys for extreme temperature resistance, and medical grade cobalt chrome for biocompatible implants.
However, the flexibility of powder bed fusion accommodates practically any alloy system, including reactive elements like aluminum or refractory metals that pose melt challenges using traditional methods. This facilitates innovation in areas such as electronics thermal management, spectroscopy components, and high temperature applications above 1000°C.
Thanks to the vacuum processing environment mitigating contamination issues, material quality and integrity comparing very favorably over competing AM or casting processes.
Benefits of Electron Beam Melting Technology
Aside from facilitation very high build rates unmatched by other powder bed technologies, EBM offers additional advantages making it the process of choice for critical applications in aerospace, medical, and industrial sectors.
Table 7: Primary Benefits of Electron Beam Melting
Benefit | Description |
---|---|
High density | Approaches 100% thanks to high beam energy and vacuum |
Exceptional material properties | Improved beyond cast or wrought |
High deposition rates | Build speeds up 10x faster than laser based systems |
Low residual stress | 70-90% less distortion or cracking |
Design freedom | Complex geometry facilitation |
Buy:make customization | Combine multiple parts into one complex assembly |
Specific examples where EBM delivers value over conventional fabrication encompass:
Productivity
- Producing Inconel 718 turbine blades at 10 times the rate of precision casting techniques.
- Manufacturing upwards of 10 hip implants simultaneously due to larger build volumes.
- Leveraging automated powder handling and job queuing for 24/7 lights out production.
Performance
- Creating Ti-6Al-4V satellite brackets with superior strength-to-weight ratio.
- Offering cobalt chrome dental bridges with superior aesthetic finish and accuracy.
- Fabricating H13 tooling with conformal cooling delivering longer injection mold life.
Quality
- Achieving cleaner material microstructures completely free of microporosity defects common in casting.
- Ensuring zero internal stresses and distortion thanks high pre-heat temperatures.
- Preventing contamination in reactive materials leveraging the high vacuum environment.
The unique melting conditions facilitated by electron beam technology repeatedly proves itself the foremost AM solution for high value applications requiring exceptional material performance.
Popular EBM Equipment Suppliers
A variety of established industrial organizations and specialized startups offer electron beam melting solutions catering to different customer adoption hurdles across market segments.
Table 8: Leading Electron Beam Melting Equipment Providers
Supplier | Details | Target Segments |
---|---|---|
Arcam EBM (GE Additive) | Pioneered first EBM machine | Aerospace, medical, automotive |
Sciaky | Largest build envelopes | Aerospace structures |
JEOL | Research grade platforms | Universities |
Wayland Additive | Budget systems | Job shops |
6K | Low cost metal powders | Process development |
Other equipment makers targeting electron beam applications outside traditional additive manufacturing include:
- Canon – Electron beam welding solutions
- PTR Group – Electron beam furnaces and welders
- IBE Services – Small electron beam welders
- Teta – High power industrial EB welding
Industry leader Arcam EBM (now part of GE Additive) established the dominant patent and market share position after introducing the first commercial EBM machine in 2002. They remain the foremost equipment supplier across aerospace, medical device, automotive, and industrial categories.
Most providers leverage partnerships with material producers, research groups, and end-user organizations to continually improve EBM process capabilities matching real production demands. These collaborative technology improvement efforts will ultimately expand adoption across even more critical industry applications going forward.
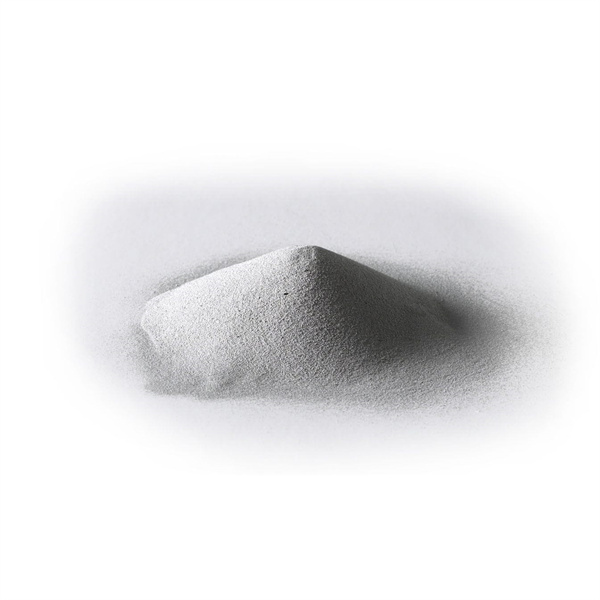
FAQ
Q: How large of a facility is needed to house EBM equipment?
A: Minimum floor space measures around 100 sq. ft for smaller machines, but larger platforms occupying 500+ sq. ft are common. Another 500+ sq. ft is typical for supplementary powder handling and post-processing stations. Facilities require at least 8 foot ceilings and reinforcing for heavy equipment loads exceeding 12,000 lbs.
Q: What materials are incompatible with EBM processing?
A: Aluminum alloys pose oxidation risks without proper inert environments. Refractory metals with very high melt temperatures exceeding 3600°C like tungsten or rhenium remain unsuitable. Otherwise EBM accommodates most alloy systems.
Q: How many trained operators are required per EBM machine?
A: One machine operator can typically oversee several EBM machines depending on automation level and production volumes. Additional personnel are needed for powder operations, post-processing, quality activities, maintenance, and engineering support.
Q: What safety risks are associated with EBM technology?
A: High voltage electron beams pose arc flash hazards requiring proper enclosures and safety controls. Reactive metal powder exposure risks also require protective equipment and handling protocols for fire and health dangers. Proper training is critical.