Significance of Additive Manufacturing Powder Suppliers
Additive manufacturing, particularly 3D printing using metal powders, is a rapidly evolving field. Suppliers like Metal3DP Technology Co., LTD play a crucial role in this industry. These suppliers specialize in providing 3D printing metal powders for various industrial applications. The significance of such suppliers can be understood through several key aspects:
Organizational Excellence and Certification
- Commitment to Quality: Companies like Metal3DP emphasize organization and certification as fundamental aspects of their operation. This commitment ensures high standards in additive manufacturing1.
- ISO 9001 Certification: Such certification is a testament to a supplier’s dedication to superior quality management, customer satisfaction, and continual improvement2.
Technical and Custom Solutions
- Advanced Technologies: Suppliers utilize advanced technologies like SLS (Selective Laser Sintering), SLM (Selective Laser Melting), and SEBM (Selective Electron Beam Melting) to provide cutting-edge solutions in 3D printing3.
- Customization: The ability to tailor metal powders to specific project needs is vital for addressing diverse industrial requirements4.
Support and Development
- Application Development: From prototyping to production, suppliers offer comprehensive support, ensuring that the products meet the specific needs of their clients5.
- Digital Manufacturing Partnership: Suppliers often act as partners in guiding organizations through digital transformation, enhancing their manufacturing processes6.
Cost of Additive Manufacturing Powders
Additive manufacturing (AM) powder suppliers play a critical role in the 3D printing industry, providing the raw materials necessary for producing high-quality, precision components. The cost of these powders is an important consideration for businesses and individuals involved in additive manufacturing. Here’s an overview of the costs involved, as exemplified by Metal3DP’s offerings:
Metal Powder Costs
Material | Price Range (per kg) | Notes |
---|---|---|
Stainless Steel | $45 – $105 | Most economical, widely used in various industries |
Titanium Ti64 | $350 – $500 | Used in aerospace and medical, higher cost |
Nickel Superalloys | $90 – $250 | Critical applications, moderate cost |
Cobalt Chrome | $110 – $350 | Medical and aerospace, higher end of price range |
TiAl2 Alloy | $350 – $450 | Price varies by purity, particle size, quantity |
Factors Influencing Costs
- Composition and Quality: The type of metal powder and its quality specifications significantly affect the price. High-quality powders meeting strict aerospace and medical standards command premium pricing.
- Volume of Purchase: Bulk orders can lead to negotiated lower prices. For example, TiAl2 alloy powder costs might be lower for orders above 100 kg1.
- Custom Alloys and Small Lots: Tailored materials and smaller quantities typically incur higher costs.
- Reusing Powders: Utilizing oversize and recovered powders can help in reducing expenses.
Market Trends
- Price Variability: The costs of metal powders can fluctuate based on market demands, technological advancements, and production scales.
- Economies of Scale: As production scales up, the overall costs of metal powders are gradually decreasing, although they still represent a significant portion of operating costs in metal AM2.
Impact on Buyers
- Budgeting for Small Buyers: Material costs remain a limiting factor for smaller buyers due to less leverage in price negotiations.
- Advantages for Larger Purchasers: Larger organizations can negotiate better deals, thus reducing their per-unit cost of metal powders.
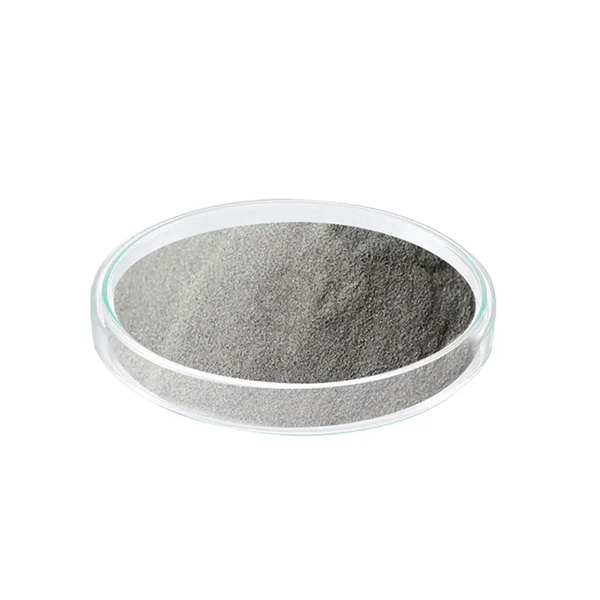
Different Types of Additive Manufacturing Powder Suppliers
Additive manufacturing (AM) involves a variety of metal powders, each catering to different industrial requirements. Metal3DP offers a diverse range of metal powders suitable for various additive manufacturing applications. Here’s an overview of their offerings:
Common Types of Metal Powders
Material | Key Properties | Common Applications |
---|---|---|
Stainless Steel | Corrosion resistance, high strength | General industry |
Tool Steel | Extreme hardness, wear resistance | Tooling, heavy-duty applications |
Titanium | High strength-to-weight ratio | Aerospace, medical |
Aluminum | Lightweight, high conductivity | Automotive, aerospace |
Nickel Alloys | Heat resistance, toughness | High-temperature applications |
Cobalt Chrome | Biocompatibility, hardness | Medical, aerospace |
Specific Metal Powder Examples
- 17-4PH Stainless Steel Powder for MIM: Ideal for metal injection molding (MIM) with high strength, good corrosion resistance, and enhanced mechanical properties after heat treatment1.
- 17-4PH Stainless Steel Powder: Widely used in aerospace, medical, automotive, and general engineering for its strength, corrosion resistance, and weldability2.
- 300M Stainless Steel Powder: A high-alloy austenitic stainless steel used in powder metallurgy and AM for its corrosion resistance and high strength3.
- 304L Stainless Steel Powder: An austenitic chromium-nickel stainless steel with low carbon content, offering excellent corrosion resistance and weldability, suitable for non-critical applications1.
Production Methods for Metal Powders
Metal3DP employs various production methods for creating these powders:
- Gas Atomization: Produces spherical droplets from molten alloy using inert gas, resulting in high purity and flowability.
- Plasma Atomization: Uses high heat plasma to melt alloy into fine spheres, ensuring a clean internal structure.
- Mechanical Alloying: Involves ball milling to synthesize alloys from elemental blends, producing nanostructured particles4.
These methods contribute to the diverse range of metal powders available, each suited for specific additive manufacturing processes and applications. The choice of powder depends on the required properties of the final product, such as strength, corrosion resistance, or biocompatibility.
Functions Served by Additive Manufacturing Powder Suppliers
Additive manufacturing powder suppliers, such as Metal3DP Technology Co., LTD, fulfill several critical functions in the industry. These functions are essential for various sectors, including aerospace, medical, automotive, and more. Below is an overview of the key functions served by these suppliers:
Table of Functions
Function | Description |
---|---|
Production of High-Quality Powders | Suppliers like Metal3DP produce a wide range of high-quality metal powders optimized for different additive manufacturing techniques like laser and electron beam powder bed fusion1. |
Equipment Manufacturing | Apart from powders, they also specialize in 3D printing equipment capable of delivering industry-leading print volume, accuracy, and reliability for mission-critical parts2. |
Advanced Manufacturing Techniques | Employing industry-leading gas atomization and PREP technologies, these suppliers create metallic powders with high sphericity and good flowability3. |
Customized Solution Development | They partner with customers to develop tailored solutions, addressing modern manufacturing challenges4. |
Industry Application Support | Offering comprehensive solutions and application development services to implement 3D printing and accelerate digital manufacturing transformations2. |
Overview of Services
- Quality Assurance: Suppliers like Metal3DP are committed to quality, ensuring that both their 3D printing systems and the precision-engineered metal powders meet the highest standards. This level of excellence is crucial for industries where reliability and precision are paramount4.
- Collaboration and Customer Focus: These suppliers engage closely with their clients, offering a customer-focused approach. This collaboration allows for the development of solutions tailored specifically to the needs and challenges faced by their clients in various sectors4.
- Pioneering Innovation: By constantly evolving and innovating, additive manufacturing powder suppliers redefine the possibilities in metal additive manufacturing. Their expertise and cutting-edge technologies enable next-generation manufacturing, crucial for organizations looking to stay ahead in a competitive market2.
Applications for Additive Manufacturing Powder Suppliers
Additive manufacturing powder suppliers, like Metal3DP, provide essential materials for a wide range of industrial applications. These applications leverage the unique capabilities of metal powders in 3D printing, offering strength, durability, and design flexibility. Below is a detailed overview of the various applications:
Table of Applications
Industry Sector | Application Description |
---|---|
Aerospace | Producing lightweight components and advanced materials to enhance flight performance and fuel efficiency1. |
Healthcare | Creating personalized implants and surgical tools, improving surgical success rates and patient recovery times2. |
Automotive | Manufacturing lightweight components for improved fuel efficiency, vehicle performance, and innovative design3. |
Jewelry | Assisting in jewelry design, enabling the creation of unique and highly personalized jewelry pieces4. |
Energy | Rapid manufacturing of critical components for efficient performance and reliability of energy equipment5. |
Industrial Manufacturing | Employed for rapid prototyping, efficient production, and manufacturing complex components to enhance business efficiency and reduce production costs6. |
Overview of 3D Printing Techniques and Materials
- 3D Printing Techniques: The common techniques used in these sectors are Selective Laser Melting (SLM), Direct Metal Laser Sintering (DMLS), and Electron Beam Melting (EBM).
- Materials Used: These methods utilize fine metal powders, typically 10-45 microns in size with spherical morphology, made from materials like stainless steel, titanium, nickel alloys, aluminum, and cobalt-chromium7.
- End-Product Characteristics: 3D printed metal parts are known for their strength, durability, design freedom, and lightweight. They are used for rapid prototyping, tooling, and low-volume production of complex parts.
- Post-Processing Requirements: After printing, some post-processing such as support removal, stress relieving, and surface finishing may be required7.
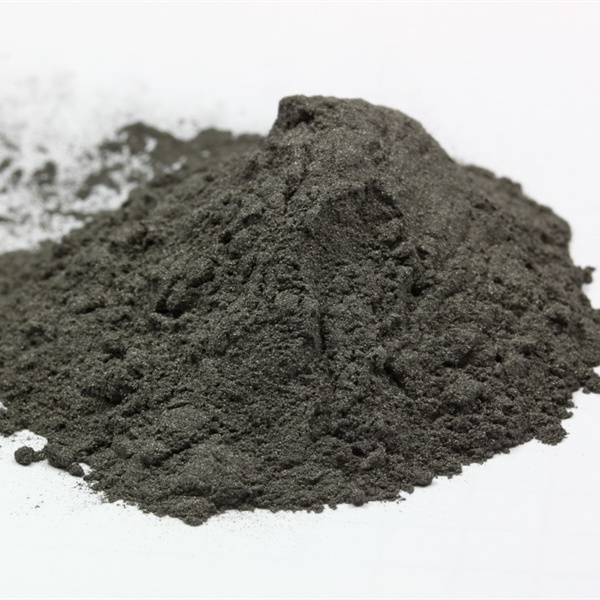
Benefits of Additive Manufacturing Powder Suppliers
Additive manufacturing (AM) powder suppliers like Metal3DP Technology Co., LTD offer a range of benefits to industries and companies incorporating 3D printing into their manufacturing processes. These benefits are realized through the provision of high-quality metal powders, advanced production technologies, and customer-focused solutions.
Table of Benefits
Benefit Category | Description and Impact |
---|---|
Advanced Production | Utilization of industry-leading gas atomization and PREP technologies to produce high-quality metallic powders with high sphericity and good flowability1. |
High-Quality Powders | Offering a wide range of optimized metal powders for laser and electron beam powder bed fusion, including innovative alloys like TiNi, TiTa, TiAl, TiNbZr, CoCrMo, stainless steels, and superalloys2. |
Industry Applications | Enabling the 3D printing of dense, high-quality metal parts with superior mechanical properties for critical applications in aerospace, medical, automotive, and other fields3. |
Collaborative Solutions | Development of tailored solutions through partnerships with customers and partners, addressing modern manufacturing challenges4. |
Comprehensive Services | Providing a combination of SEBM printers, advanced metal powders, and application development services to implement 3D printing and accelerate digital manufacturing transformations3. |
Overview of Impact
- Quality and Reliability: Suppliers like Metal3DP focus on delivering industry-leading print volume, accuracy, and reliability, which is essential for manufacturing mission-critical parts3.
- Innovation in Manufacturing: By constantly evolving and offering pioneering metal additive manufacturing solutions, these suppliers redefine manufacturing possibilities4.
- Customer-Centric Approach: They place a strong emphasis on customer focus, listening to needs, exceeding expectations, and providing seamless solutions and support4.
- Expanding Capabilities: These suppliers enable next-generation manufacturing by delivering cutting-edge systems and powders, facilitating organizations in their additive manufacturing journey3.
In summary, additive manufacturing powder suppliers contribute significantly to various industries by providing high-quality, precision-engineered metal powders and advanced manufacturing solutions. Their collaborative approach, focus on quality, and commitment to innovation help companies navigate modern manufacturing challenges and embrace the potential of 3D printing.