Additive manufacturing (AM), also known as 3D printing, relies on metallic and non-metallic powders to build components layer-by-layer. Choosing a reputable AM powder supplier is crucial for achieving optimal material properties, performance, and end-use part quality.
This comprehensive guide provides everything you need to know about selecting the right additive manufacturing powder and supplier, including:
Overview of Additive Manufacturing Powder
Additive manufacturing powders refer to the raw materials used in powder bed fusion, directed energy deposition, binder jetting and other powder-based AM processes.
Key types of AM powders:
- Metals – Titanium, aluminum, steel, nickel, cobalt-chrome
- Polymers – Nylon, PEEK, TPU, ABS, polyamide
- Ceramics – Alumina, zirconia, silicon carbide
- Composites – Particle reinforced, short fiber
Powder characteristics:
- Chemistry – Purity, composition, alloying
- Particle size and distribution
- Particle shape – spherical, irregular
- Density and porosity
- Flowability
- Moisture content
Key powder suppliers:
- OEMs like EOS, 3D Systems, GE Additive
- Metal powder specialists such as AP&C, Sandvik, Praxair
- Large metal producers including Carpenter, Höganäs, Rio Tinto
Choosing the optimal powder type and parameters tailored to your AM process and applications is vital for high quality parts.
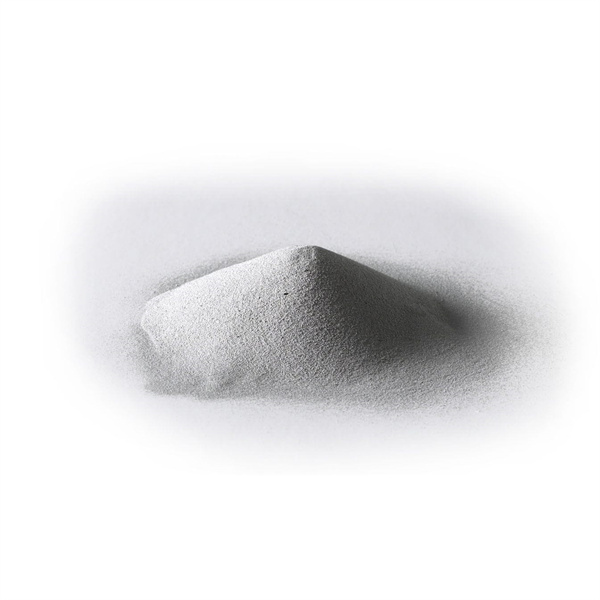
Types of Additive Manufacturing Powder
There are four major categories of AM powders for metals, polymers, ceramics and composites:
Metal Powders
Most widely used metals include:
- Titanium and titanium alloys
- Aluminum alloys
- Stainless steels
- Tool steels
- Cobalt-chrome alloys
- Nickel superalloys
- Precious metals like gold, silver
Benefits: High strength, durability, thermal resistance
Applications: Aerospace, medical, automotive, industrial
Polymer Powders
Common polymers used:
- Nylon (PA12, PA11)
- ABS
- PEEK
- TPU
- Polyamide
Benefits: Toughness, chemical resistance, flexibility
Applications: Consumer products, industrial parts
Ceramic Powders
Examples include:
- Alumina
- Zirconia
- Silicon carbide
- Silicon nitride
- Tricalcium phosphate
Benefits: High hardness, heat/corrosion resistance
Applications: Cutting tools, dental, aerospace
Composite Powders
- Particle reinforced metals and polymers
- Short fiber reinforced plastics
Benefits: Enhanced mechanical properties
Applications: Automotive, sporting goods, infrastructure
The right powder type influences part properties like strength, function, aesthetics and more.
Additive Manufacturing Powder Properties
AM powders must meet strict specifications for:
Property | Details | Significance |
---|---|---|
Chemistry | Alloy composition, purity levels | Affects microstructure, defects, mechanical properties |
Particle Size | Average size and distribution | Influences resolution, surface finish, density |
Particle Shape | Spherical, irregular, satellite particles | Impacts packing density, flowability, spreadability |
Density | Bulk and tap density | Higher density enables greater part density |
Flow Characteristics | Flow rate, angle of repose | Ensure smooth powder spreading during printing |
Moisture Content | Low moisture content | Prevents powder agglomeration and degradation |
Surface Oxides | Thin, uniform oxide layer | Low oxidation gives superior powder flow and properties |
Strict control over these powder characteristics is essential for high quality AM components.
Applications of Additive Manufacturing Powders
AM powders are used across the following key industries and applications:
Industry | Applications |
---|---|
Aerospace | Turbine blades, airframe and engine structures, brackets, heat sinks |
Medical | Orthopedic and dental implants, surgical tools, patient-matched devices |
Automotive | Lightweighted components, custom parts, tooling |
Industrial | Heavy equipment parts, robotics, tooling, jigs and fixtures |
Consumer | Jewelry, collectibles, gaming miniatures |
Oil & Gas | Downhole tools, valves, wellhead parts, pump components |
Other applications include architectural models, rapid tooling, nuclear and chemical equipment.
AM enables faster and more flexible production of complex, optimized parts across sectors.
AM Powder Specifications
AM powder properties and quality can be customized as per requirements:
Parameter | Options |
---|---|
Materials | Metals, polymers, ceramics, composites |
Chemistry | Different alloys, polymers, reinforcements |
Particle size | Nano, micro, 10-45 μm, 15-150 μm etc. |
Size distribution | Tight distributions available |
Particle shape | Predominantly spherical |
Density | Up to ~98% theoretical density |
Flow rate | Optimal flow rates achieved |
Surface oxides | Low oxidation levels |
Contamination | Minimized impurity levels |
Moisture content | Low moisture content |
Work with suppliers to tailor powder specifications to your AM process, material needs and end-use requirements.
Design Considerations for AM Powders
Certain design practices enhance AM powder performance:
- Alloy modification – Adjusting compositions to optimize mechanical properties, avoid hot cracking etc.
- Blending – Mixing different powders to achieve custom material properties
- Coatings – Applying specialized coatings to protect alloy powders from oxidation
- Sieving – Classifying powder into narrow particle size fractions
- Degasification – Removing gaseous contaminants that cause porosity
- Flow additives – Adding nanoscale flow agents to improve powder flowability
- Rejuvenation – Recycling used powder by removing moisture and impurities
Work closely with your AM powder supplier to leverage these design options for superior part properties.
Standards for Additive Manufacturing Powders
Key standards help ensure AM powder quality and consistency:
- ASTM F3049 – Standard guide for characterizing AM metals
- ASTM F3055 – Standard specification for additive metals
- ASTM F3213 – Standard for metal powders used in powder bed fusion
- ISO/ASTM 52915 – Standard specification for Ti-6Al-4V alloy
- ASTM F3184 – Standard for stainless steel powders
- ASTM F3301 – Standard for nickel alloy powders
- ISO/ASTM 52904 – Process characteristics and performance QC of AM metals
Powder suppliers and users should adhere to these standards to benchmark quality.
AM Powder Suppliers
Leading global AM powder manufacturers include:
Supplier | Materials | Description | Pricing |
---|---|---|---|
AP&C | Ti, Al, CoCr, Steels | Specialist producer of spherical powders | $xx-$xxx/kg |
Sandvik | Ti, Ni, Al, Steels | Wide alloy offerings for AM | $xx-$xxx/kg |
Praxair | Ti, Ni, CoCr, Al | High quality atomized & alloy powders | $xx-$xxx/kg |
Carpenter | Ti, CoCr, SS, Al | Broad range of alloys and particle sizes | $xx-$xxx/kg |
GE Additive | Ti, Al, CoCr, Cu | OEM providing integrated AM solutions | $xx-$xxx/kg |
Höganäs | Steels, SS | Major global powder metal supplier | $xx-$xxx/kg |
There are numerous reputable global suppliers offering quality AM powders across metals, polymers, ceramics, and composites.
How to Select an Additive Manufacturing Powder Supplier
Here are key factors to consider when choosing an AM powder supplier:
- Technical expertise in AM powder manufacturing
- Range of materials offered – metals, polymers, ceramics etc.
- Quality management – Powder characterization, sampling, testing, analysis, documentation, certifications
- Spherical powder capabilities – For density and flowability
- Customization abilities – Tailored size distribution, composition, coatings etc.
- AM process understanding – Powder optimized for your specific AM technology
- R&D expertise – Ongoing powder developments
- Customer support – Application advice, troubleshooting, training
- Lead times – Inventory availability for quick delivery
- Pricing – Competitive for your volume and quality needs
Partner with a powder manufacturer committed to consistent quality and technical support.
How to Store Additive Manufacturing Powder
Proper AM powder storage preserves material quality and prevents degradation:
- Store powder in original sealed containers away from humidity and contamination
- Maintain cool, dry facility conditions
- Limit temperature variations which can induce moisture absorption
- Use a first-in-first-out (FIFO) inventory system
- Only open container at time of use
- Discard used powder in a timely manner
- Conduct periodic quality checks on stored powder
- Check chemistry, size distribution, flow rate, surface oxides
- Follow all safety precautions – PPE, inert gas handling, ignition source control
Proper storage is essential for powder stability and maximizing part quality over time.
Recycling Additive Manufacturing Powder
Used AM powder can be recycled:
Method | Overview |
---|---|
Thermal | Heat treatment burns off coatings and impurities |
Mechanical | Physical processes remove contamination and refresh particles |
Chemical | Chemical processes strip surface oxides and coatings |
Plasma | Plasma energy dissociates unwanted elements from powder |
Benefits of recycling:
- Reduces powder costs significantly
- More sustainable manufacturing
- Achieves high reuse rates in certain alloys
Work with your AM powder supplier to implement cost-effective powder recycling practices.
Cost Analysis of Additive Manufacturing Powders
AM powder costs vary significantly by material:
Material | Cost Per Kg |
---|---|
Aluminum Alloys | $50 – $120 |
Titanium Alloys | $170 – $450 |
Stainless Steels | $50 – $120 |
Tool Steels | $50 – $200 |
Nickel Superalloys | $150 – $500 |
Cobalt Chrome | $150 – $300 |
Polymers | $80 – $200 |
Powder cost depends on:
- Base material cost
- Alloy composition
- Production method – gas vs water atomization
- Quality – impurities, particle size distribution
- Purchase volume – higher volumes give lower prices
Balancing powder quality with affordability is key for maximizing value.
Pros and Cons of Metal vs. Polymer AM Powders
Metal Powder Pros
- High strength and thermal resistance
- Excellent durability and crack growth resistance
- Wide range of advanced alloy options
- Can replicate final part material properties
Metal Powder Cons
- Higher material costs
- Limited sizes and suppliers currently
- Safety precautions required in handling
- More infrastructure needed for processing
Polymer Powder Pros
- Lower material costs
- More suppliers and choice in materials
- Generally safer handling
- Requires less complex infrastructure
Polymer Powder Cons
- Lower strength, heat resistance, and durability
- Limited high performance polymers currently
- Often used for prototyping vs final parts
- Unpredictable and anisotropic material properties
The right option depends on application requirements, operating conditions, and economics.
Future Outlook for AM Powder
The AM powder market is projected to reach over $5 billion by 2028, led by growth in:
- Aerospace and medical sectors
- Adoption of AM for production applications
- New alloys and materials for AM
- Adoption of AM by auto manufacturers
- Supply chain development as demand scales up
Key future opportunities and developments include:
- New AM powder producers entering the market
- Competitive pricing with increased volumes
- Higher purity and improved flowability
- Custom alloy compositions and particle optimization
- Improved recycling processes and economics
- Automated powder handling and inventory management
AM powders will play an integral role in the AM industry’s continued expansion and adoption across critical manufacturing industries.
FAQ
Q: What materials are available for additive manufacturing?
A: The most common materials are metals, polymers, ceramics and composites. Metals include titanium, aluminum, stainless steel, tool steel, nickel alloys, and precious metals. Polymers include nylon, PEEK, ABS, polyamide.
Q: What is the most widely used AM metal powder?
A: Titanium alloys, particularly Ti-6Al-4V, are the most common metal powders used in key industries like aerospace and medical.
Q: What is the optimal AM powder particle size?
A: Standard powder sizes range from 10-45 microns for most AM processes. However, optimal size depends on the specific machine and process parameters.
Q: How much does metal AM powder cost?
A: Powder costs range widely from $50-$500/kg depending on the alloy, quality, and purchase volume. Titanium is on the higher end while aluminum and steel are lower cost.
Q: Does using recycled powder degrade material properties?
A: Properties can degrade after repeated recycling. Utilization rates depend on the alloy and recycling process. Work with your supplier to maximize reuse while maintaining consistency.
Q: What are key powder characteristics for AM?
A: Key characteristics include chemistry, particle size distribution, shape, density, flowability, low moisture content and surface oxides.
Q: How is AM powder produced?
A: Metal powder is mainly produced using gas or water atomization. Polymers use various pulverization methods. Ceramics use advanced processes like plasma spheroidization.
Q: How can you determine AM powder quality?
A: Conduct testing and characterization per industry standards for parameters like chemistry, cleanliness, particle size distribution, flow rate, density, and moisture content.
Q: What precautions are needed when handling metal AM powder?
A: Use appropriate PPE, minimize dust, avoid ignition sources, implement proper storage and housekeeping practices, follow all recommended safety procedures.
Q: How is AM powder different than powder for other processes like MIM?
A: AM powders require more stringent specifications for particle size distribution, spherical morphology, flow characteristics, and cleanliness to maximize part quality.