superalloys metal powder enable additive manufacturing of high strength, heat resistant alloy components unmatched by conventional metals. This guide covers superalloy compositions, powder specifications, properties data, pricing insights and comparisons to inform powder metallurgy procurement decisions.
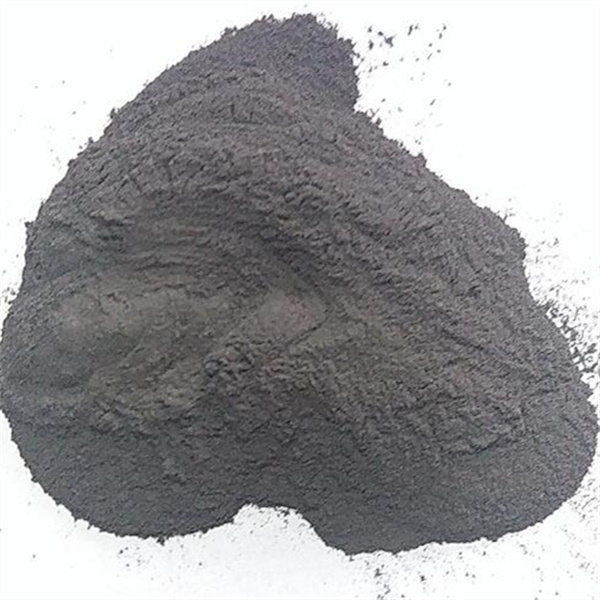
Introduction to superalloys metal powder
Key capabilities of superalloy powders:
- Withstand extreme temperatures up to 85% of melting points
- Retain strength, corrosion resistance and stability in harsh environments
- Facilitate innovative complex part geometries through AM
Common classification groups:
- Nickel-based – Inconel, Waspaloy, Rene alloys
- Cobalt-based – Haynes, HS alloys
- Iron-based – A286, 901, 304 variants
This guide provides considerations when selecting superalloy powder:
- Alloy Compositions and Powder Production Methods
- Mechanical Properties, Test Methods and Data Sheets
- Particle Size Distribution Specifications
- Powder Morphology Characteristics and Consistency
- Pricing Models Based on Order Volumes
- Oxidation and Corrosion Resistance
- Pros vs Cons: Powder vs Solid Bar
- FAQs on Quality Control and Applications
Let us explore superalloy powders specifically…
superalloys metal powder Compositions
Table 1 shows nominal compositions of common nickel and cobalt-based superalloys with some variation between powder manufacturers.
Alloy | Key Alloying Elements |
---|---|
Inconel 718 | Ni, Fe, Nb, Mo, Al |
Inconel 625 | Ni, Cr, Mo, Nb |
Rene 41 | Ni, Co, Cr, Mo, Ti, Al |
Waspaloy | Ni, Co, Cr, Mo, Ti, Al |
Haynes 282 | Co, Cr, W, Mo, Ti, Al |
Small additions of boron, carbon, zirconium and silicon also tailor grain structure, strengthen boundaries and enhance high temperature behavior through precipitate formation.
Mechanical Properties and Test Methods
Table 2 shows typical minimum mechanical properties met by common superalloy powders, with actual values varying based on build geometry, post-processing, and heat treatment.
Alloy | Yield Strength | Tensile Strength | Test Method |
---|---|---|---|
Inconel 718 | 1035 MPa | 1275 MPa | ASTM E8 |
Rene 41 | 760 MPa | 1035 MPa | ASTM E8 |
Haynes 282 | 830 MPa | 1035 MPa | ASTM E8 |
Review test reports carefully to ensure powder lots procured meet certification requirements and application needs.
superalloys metal powder Particle Size Specs
Table 3 shows particle size distribution categories generally used to classify superalloy powders:
Size Range | Typical Mesh |
---|---|
Submicron | -100 +325 mesh |
Fine | -140 +325 mesh |
Extra Fine | -200 +325 mesh |
Other key particle characteristics:
- Spherical morphology
- Satellite free smooth surfaces
- Controlled size distribution
- Flow rates >30s in Hall funnel
For printing, 25-45 micron mean sizes give a good balance of resolution and flowability. Adjust based on specific machine capabilities and minimum feature sizes needed.
superalloys metal powder Pricing
Table 4 provides rough superalloy powder price estimates under typical market conditions:
Order Quantity | Price Estimate |
---|---|
10 kg | $450+/kg |
100 kg | $275+/kg |
500 kg | $225+/kg |
1000+ kg | Subkey discounts |
- Special alloys command premium baseline pricing
- Large orders in 500-1000+ kg range enable >50% discounts from list price points through bulk buying leverage
- Actual market prices tied to raw material input price fluctuations
Oxidation and Corrosion Resistance
Superalloys maintain exceptional stability even when exposed to extreme environments:
Table 5
Alloy | Typical Service Temp. | Corrosion Resistance |
---|---|---|
Inconel 718 | 700°C | Excellent |
Rene 41 | 760°C | Excellent |
Haynes 282 | 1095°C | Excellent |
Carefully engineered compositions with nickel, chromium and aluminum form tenacious passivating oxide barriers protecting surfaces against attack up to very high proportions of melting points.
Elements like molybdenum further boost pitting and crevice corrosion resistance.
Pros vs Cons: Powder vs Solid Bar
Table 6
Advantages | Disadvantages | |
---|---|---|
Superalloy Metal Powder | Complex shapes | Higher cost |
Superior properties | Post-processing | |
Weight reduction | Parameter optimization | |
Superalloy Solid Bar | Lower cost | Shape limits |
Availability | Much heavier | |
Machinability | Material waste |
In general, superalloy powder justifies premiums for low volume complex components where advanced properties are vital. Standard mill forms offer affordability for simple shapes in high production use cases.
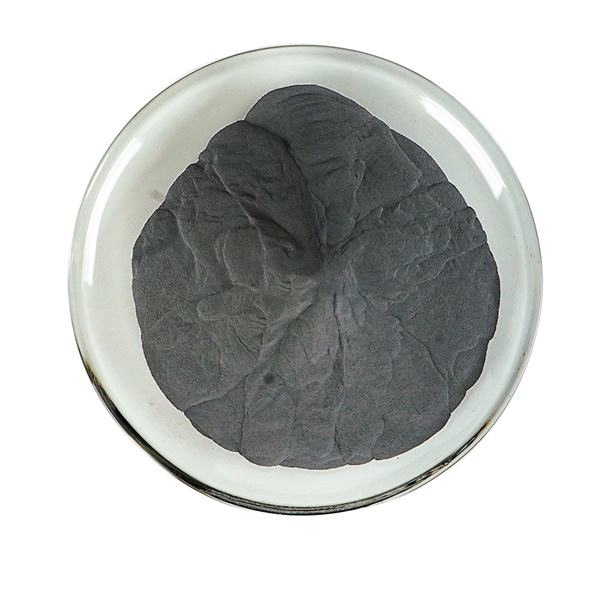
FAQs
Table 7 – Common questions:
FAQ | Answer |
---|---|
Should I review test reports? | Yes, scrutinize all certs thoroughly to ensure powder quality |
What size powder particles should I start with? | 25-45u provides a robust starting point |
What factors affect consistency? | Raw powder production method impacts variability |
How much powder should I buy initially? | Start small scale to validate print process control |
Table 8 – Application-specific advice:
FAQ | Answer |
---|---|
What post processing should I use for hot section turbine blades? | Hot Isostatic Pressing to remove pores and enhance fatigue performance |
What alloy maximizes high temperature yield strength? | Consider Rene 41 or Haynes 282 alloys |
How can I minimize part anisotropy effects? | Utilize elevated temperature heat treatments to relieve stresses |
What’s better for cryogenic parts – powder or cast? | Powder enables complex conformal channels unlike castings |