Metal powders are a critical raw material for additive manufacturing using powder bed fusion technology. This guide provides an overview of various metal powders used in 3D printing processes like selective laser melting (SLM) and electron beam melting (EBM).
Introduction to Metal Powders for AM
Metal powders enable printing of complex, high-performance metal parts using additive manufacturing.
Materials used:
- Stainless steels
- Tool steels
- Cobalt-chrome alloys
- Titanium and titanium alloys
- Aluminum alloys
- Nickel superalloys
- Copper alloys
Key powder properties:
- Chemistry – Purity and composition
- Particle shape and morphology
- Particle size distribution
- Apparent density and tap density
- Flowability
- Powder reuse
Powder production methods:
- Gas atomization
- Water atomization
- Plasma atomization
- Electrode induction melting
- Carbonyl process
- Mechanical alloying
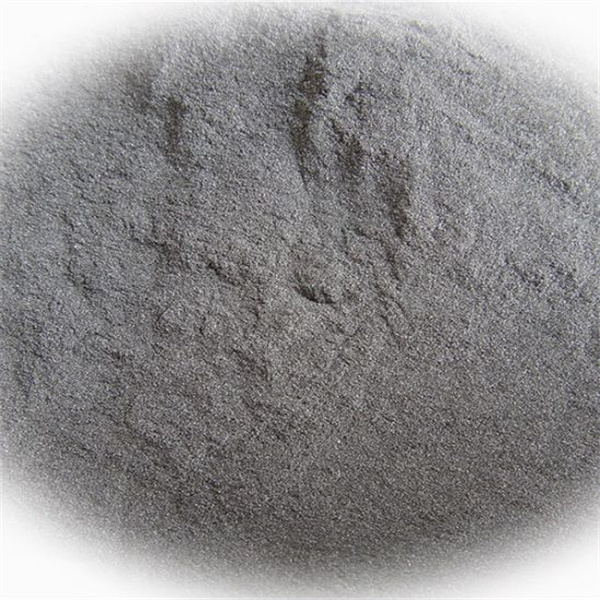
Stainless Steel Powders
Stainless steel powders are commonly used for printing corrosion resistant parts:
Alloy types:
- Austenitic steels like 316L, 304L
- Martensitic steels like 17-4PH
- Duplex steels like 2205
- Precipitation hardening like 17-4PH, 15-5PH
Characteristics:
- High corrosion and oxidation resistance
- Good strength and ductility
- Less prone to cracking than high-alloy steels
- Parameters like build atmosphere critical
Applications:
- Chemical and process industry parts
- Marine components
- Medical implants and devices
- Food/pharma industry parts requiring hygiene
Suppliers: Carpenter, Sandvik, Praxair, Höganäs, LPW Technology
Tool Steel Powders
Tool steels like H13 are ideal for printing wear and high-hardness parts:
Alloy types:
- Shock-resistant steels like S7
- Cold work steels like D2
- Hot work steels like H13, H11
- High speed steels like M2
Characteristics:
- Excellent hardness up to 60 HRC
- High wear resistance
- Good toughness and thermal fatigue resistance
- Require high-temperature solution annealing
Applications:
- Metal forming dies and molds
- Cutting tools and drill bits
- Wear parts and bearings
- High-temperature tooling
Suppliers: Sandvik, Erasteel, LPW Technology, Tekna Plasma Systems
Cobalt-Chrome Alloys
Cobalt-chrome powders print biocompatible implants and dental restorations:
Alloy types:
- CoCrMo like Co-28Cr-6Mo
- CoNiCrMo like Co-35Ni-20Cr-10Mo
- CoCr like Co-67Cr-28Fe
Characteristics:
- Excellent biocompatibility and corrosion resistance
- High strength and hardness
- Wear resistance for articulating joints
- Challenging printability and cracking tendency
Applications:
- Dental copings, bridges and crowns
- Orthopedic knee and hip implants
- Fixation devices like cranial plates
- Spinal fusion hardware
Suppliers: SLM Solutions, Carpenter, Arcam EBM
Titanium Powders
Titanium powders create strong, lightweight printed parts:
Alloy types:
- Unalloyed titanium like Ti Grade 1-4
- Ti-6Al-4V alloy
- Ti-6Al-7Nb alloy
- Other alpha + beta alloys
Characteristics:
- High strength-to-weight ratio
- Excellent corrosion resistance
- Good high-temperature properties
- Low density – 4.5 g/cc
- Reactive and requires inert atmosphere
Applications:
- Aerospace and motorsports components
- Medical implants and prosthetics
- Food/chemical industry parts
- Automotive parts
Suppliers: AP&C, Tekna, Carpenter Additive
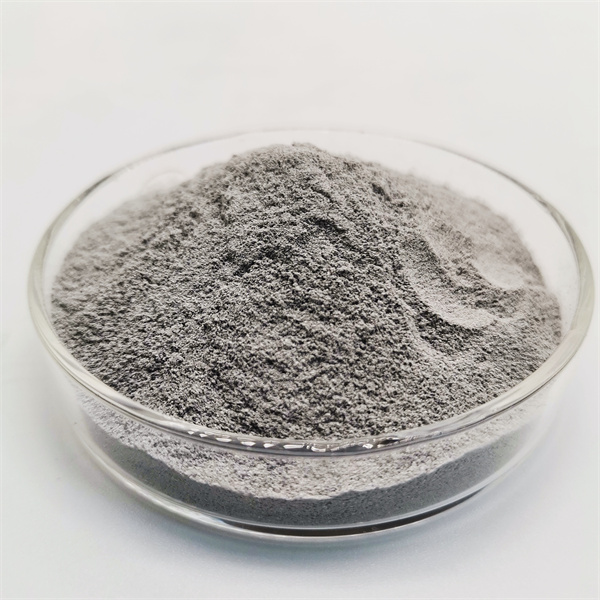
Aluminum Alloys
Aluminum powders print lightweight structural or functional parts:
Alloy types:
- AlSi10Mg
- AlSi7Mg
- AlSi12
- Scalmalloy® and other Al alloys
Characteristics:
- Low density – 2.7 g/cc
- Good strength and stiffness
- Excellent thermal conductivity
- Prone to cracking and residual stresses
Applications:
- Automotive and motorsports components
- Aerospace and space applications
- Heat exchangers
- Medical equipment like casts
Suppliers: AP&C, Sandvik, LPW Technology, ECKA Granules
Nickel Superalloys
Nickel superalloys like Inconel 718 print high-temperature parts:
Alloy types:
- Inconel 718
- Inconel 625
- Waspaloy
- Hastelloy X
Characteristics:
- Excellent high-temperature strength
- Good corrosion and creep resistance
- Ability to work under stress at high temps
- Challenging to process and prone to cracking
Applications:
- Turbine blades
- Combustion chamber parts
- Spacecraft components
- Nuclear/chemical industry parts
Suppliers: Praxair, Carpenter Additive, GE Additive
Copper Alloys
Copper alloys like CuCrZr print highly conductive parts:
Alloy types:
- Copper-chromium like CuCr1Zr
- Copper-nickel like CuNi2SiCr
- Bronzes like CuSn10
Characteristics:
- Excellent thermal and electrical conductivity
- Good corrosion resistance
- Antibacterial property
- Lower strengths than steels and Ni alloys
Applications:
- Electrical components like busbars
- Heat exchangers and heat sinks
- Waveguides and RF components
- Medical instruments and fixations
Suppliers: Sandvik, LPW Technology, Metalysis
Technical Specifications
Typical metal powder specifications used in AM:
Parameter | Typical Values | Test Standards |
---|---|---|
Particle size | 10 – 45 μm | ASTM B214 |
Particle shape | Spherical | ISO 13322-2 |
Flow rate | 25 – 35 s/50g | ASTM B213 |
Apparent density | 2 – 5 g/cc | ASTM B212 |
Tap density | 4 – 8 g/cc | ASTM B527 |
Residual oxygen | < 300 ppm | In-house method |
Residual nitrogen | < 50 ppm | In-house method |
Residual carbon | < 30 ppm | ASTM E1019 |
Powder Production Methods
1. Gas Atomization
- Highly spherical powder
- Small particle sizes of 5-100 μm
- Used for reactive alloys like titanium
2. Water Atomization
- Irregular powder shape
- Larger particles up to 300 μm
- Lower cost process
3. Plasma Atomization
- Controlled particle shapes
- Submicron to 150 μm sizes
- High purity powder
4. Mechanical Alloying
- Elemental blending and milling
- Cost-effective for custom alloys
- Large particle sizes
Suppliers and Pricing
Supplier | Materials | Price Range |
---|---|---|
LPW Technology | Tool steels, stainless steels | $50 – $120/kg |
AP&C | Titanium alloys, Al alloys | $70 – $450/kg |
Sandvik | Stainless steels, Ni alloys | $45 – $250/kg |
Praxair | Superalloys, titanium | $150 – $600/kg |
Carpenter Additive | Tool steels, CoCr, stainless | $80 – $300/kg |
- Stainless steel powders cost $45-$120 per kg
- Titanium alloy powders cost $150-$450 per kg
- Superalloys and tool steels cost $250-$600 per kg
Prices depend on alloy, quality, lot size, and purchase agreements.
Powder Handling and Storage
To prevent contamination, proper powder handling is critical:
- Use dedicated powder sieving areas
- Ensure inert atmosphere gloveboxes and hoppers
- Use conductive containers to dissipate static charges
- Ground all equipment and transport containers
- Avoid contact with oil, water, or oxygen
- Store powder in sealed containers under inert gas
- Control temperature and humidity during storage
- Follow safety precautions like PPE when handling
Proper storage extends powder reuse life.
Powder Sieving
Sieving ensures consistent particle sizes:
Benefits:
- Removes satellite particles that cause defects
- Breaks up agglomerates
- Improves flow and packing density
- Reduces recyclability issues
- Removes foreign contaminants
Procedure:
- Sieve powder using mesh sizes around 20-63 μm
- Sieve using rotational or vibratory sieving
- Perform sieving under inert atmosphere
- Document remaining powder weight percentage
Sieving improves part quality by ensuring ideal powder spreadability.
Installation and Commissioning
Installing a metal AM printer with powder system involves:
- Cleaning equipment surfaces to avoid contamination
- Leak testing inert gas connections
- Checking laser or electron beam power
- Loading and testing powder recoating system
- Integrating chiller, exhaust, and service connections
- Installing monitoring and safety sensors
- Verifying powder sieving and handling systems
- Calibrating build plate levelling
- Test printing sample parts and validating quality
Vendors provide installation and commissioning support.
Operation and Best Practices
Printer operation guidelines:
- Perform regular leak checks and inert gas purity tests
- Precondition powder to ensure consistent texture
- Adjust layer thickness and laser parameters for new materials
- Closely monitor the melt pool and control part temperature
- Validate critical dimensions using test prints
- Monitor powder condition and reuse only within recommendations
- Perform regular maintenance on optics, beam delivery system and powder recoating mechanism
Personnel safety:
- Use appropriate PPE such as respirators and gloves
- Avoid contact with reactive fine metal powders
- Handle waste powder properly under inert atmosphere
Part post-processing:
- Use appropriate solution heat-treatment and ageing temperatures tailored to alloy and application
- Control ramp rates during thermal processing to relieve stresses
- Use hot isostatic pressing for complex parts if needed to improve densities
- Apply finishing steps like CNC machining and polishing
Maintenance and Inspection
Regular maintenance activities:
Daily:
- Inspect optics like mirrors, lenses, windows for damage
- Clean the build chamber and powder handling system
- Check inert gas levels and recharge if needed
- Test the sieve mechanism and powder recoater
Weekly:
- Calibrate sensors and instrumentation
- Check fasteners, electrical terminals and grounding
- Lubricate and inspect moving parts like motors and drives
- Monitor filters for replacement
Monthly:
- Leak test inert gas system using helium
- Inspect safety devices like fire detectors
- Check the CHP system health
Yearly:
- Schedule preventive maintenance with equipment vendor
- Calibrate laser power meter
- Replace filters and consumable items
Maintenance as per vendor guidelines is required to sustain part quality and equipment health.
Choosing the Right Metal Printing System
Factors to consider when selecting a metal AM machine:
1. Production Requirements
- Type of components to be produced
- Material needed based on part properties
- Production volume requirements
- Required accuracy and surface finish
2. Printer Specifications
- Supported materials and parameters
- Build size and speed
- Precision and repeatability
- Inert atmosphere management
- Automation features and controls
3. Powder Handling System
- Integrated or standalone system
- Sieving, feeding, storage and reuse capabilities
- Containment for reactive materials like titanium
- Monitoring features to avoid contamination
4. Standards Compliance
- Industry standards like ASTM F3301
- Manufacturer quality certifications
- Safety standards compliance
5. Supplier Credentials
- Proven track record in AM industry
- Local sales and technical support capabilities
- Maintenance contracts and services offered
- Operator training plans
- Overall cost of ownership
Thorough requirements analysis and comparisons of machine offerings using these criteria results in the selection of the ideal 3D metal printing system tailored to the production needs.
Pros and Cons of Metal AM
Advantages:
- High geometric complexity printed easily
- Shorter time to functional parts
- Reduced waste compared to subtractive processes
- Single setup production directly from CAD
- Lightweighting and part consolidation potential
- Performance improvements with engineered alloys
- Customization and mass customization capabilities
Disadvantages:
- High machine and material costs
- Additional post-processing steps required
- Limited size based on build chamber
- Control of internal defects can be challenging
- Material properties can vary versus wrought
- Surface finish limitations may require finishing
- Training and expertise requirements
Troubleshooting Common Metal AM Issues
Defect | Possible Causes | Corrective Actions |
---|---|---|
Porosity | Improper process parameters | Optimize laser power, speed, hatch spacing |
Powder contamination | Use fresh sieved powder, improve powder handling | |
Insufficient overlap between scan tracks | Adjust beam focus size and overlap | |
Cracking | Excessive thermal stresses | Optimize preheating, control cooling rate with heaters |
Material prone to cracking | Change orientation to reduce stresses | |
Contamination from build atmosphere | Ensure high purity inert atmosphere | |
Warping | Uneven heating or cooling | Optimize scan patterns and restrain part on build plate |
Poor Surface Finish | Part temperature too low | Increase preheat temperature |
Improper melt pool fluidity | Adjust power and other parameters | |
Contaminated powder | Use fresh powder and improve handling |
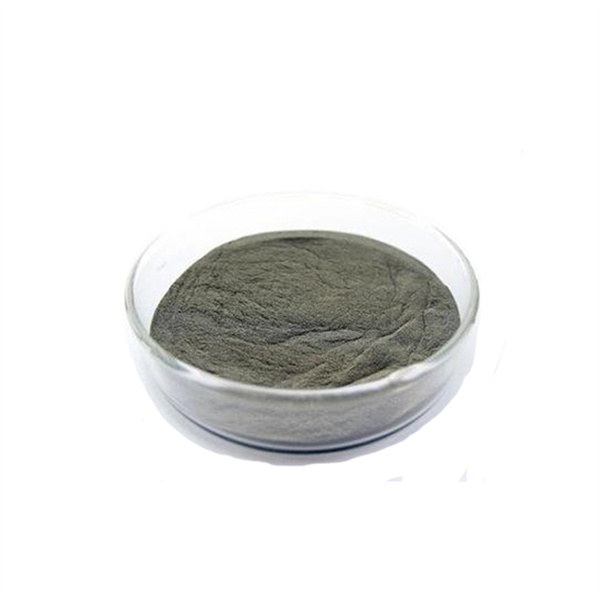
FAQs
Q: What metal alloy powders can be used for AM?
A: Stainless steels, tool steels, titanium alloys, nickel superalloys, aluminum alloys, cobalt-chrome, and copper alloys are common.
Q: What is the typical range of powder particle sizes used?
A: For PBF-LB/M processes, 10-45 microns is common, with tighter distribution around 20-45 μm.
Q: How long can metal powders last?
A: With ideal argon storage, many alloys last 1-2 years. Reuse life is shorter – 20-100 prints based on alloy.
Q: What post-processing steps are required on metal AM parts?
A: Support removal, heat treatment, surface finishing like CNC machining, polishing and coating are often required.
Q: How are reactive metal powders like titanium and aluminum handled?
A: Specialized powder handling under inert argon atmosphere is needed to prevent oxygen pickup.
Q: What are common powder contamination risks?
A: Exposure to atmosphere leading to oxygen or nitrogen pickup. Metallic particles from machining or wear. Oil and moisture.
Q: What standards are used for qualifying metal powders?
A: ASTM B214, ASTM B812, ASTM F3049, ASTM F3301, and MPIF standards.
Q: Why is powder sieving important?
A: It breaks up agglomerates, removes satellites, and provides optimum and consistent powder size for high density and surface finish.
Conclusion
Metal powders enable additive manufacturing of advanced, high-performance components with properties better than wrought materials in some cases. A wide range of alloys from stainless steels to superalloys and titanium are available in powder form, tailored to demanding applications across aerospace, medical, automotive, and general industries. With continual improvements in alloys, quality standards, production processes, machinery, and part properties – metal AM is maturing into a core production technology globally. However, process and material expertise and rigorous quality control are essential to realize the full benefits. As more experience is gained, metal AM provides unprecedented capabilities to manufacture complex and customized parts with greater design freedom and shorter lead times.