Nickel aluminide powder is an intermetallic compound composed of nickel and aluminum. It is considered an advanced material that offers high strength, corrosion resistance, and oxidation resistance at elevated temperatures. Some key properties and uses of nickel aluminide powder include:
Types and Characteristics
Type | Characteristics |
---|---|
NiAl | Most common nickel aluminide compound. B2 crystal structure. Melting point 1638°C. Density 5.9 g/cm3. High strength and stiffness at elevated temperatures. |
Ni3Al | Ordered L12 crystal structure. Melting point 1390°C. Oxidation resistance up to 1200°C. |
NiAl3 | Simple cubic crystal structure. Brittle intermetallic. Oxidation resistance up to 1000°C. |
Applications and Uses
Application | Uses |
---|---|
Aerospace | High-temperature structural components like turbine blades, exhaust nozzles. |
Automotive | Turbocharger rotors, valves, fuel injector components. |
Industrial | Heat exchangers, reaction vessels, radiant burner tubes. |
Power Generation | Coal gasification plants, heat exchangers. |
Chemical Industry | Reactors, heaters, reformers. |
Specifications and Design Standards
Parameter | Typical Range |
---|---|
Particle size | 10-150 μm |
Purity | ≥99.5% |
Oxygen content | ≤2000 ppm |
Carbon content | ≤1000 ppm |
Morphology | Spherical, irregular |
True density | 5.5-6.2 g/cm3 |
Tap density | 3.5-5 g/cm3 |
Specific surface area | 0.5-10 m2/g |
Flowability | Good |
Nickel aluminide powder should meet specifications like ASTM B964, AMS 4754, GE P1TF68, etc. based on application. Important properties like particle size distribution, morphology, purity, oxide content, etc. are controlled during production.
Suppliers and Pricing
Supplier | Price Range |
---|---|
Atlantic Equipment Engineers | $55-75/kg |
Carpenter Technology | $60-85/kg |
Sandvik | $70-100/kg |
ATI Powder Metals | $80-120/kg |
Stanford Advanced Materials | $75-110/kg |
Pricing depends on order quantity, purity levels, particle characteristics, and morphology. Small lab quantities are more expensive than bulk orders. Spherical is generally costlier than irregular powder.
Installation, Operation, and Maintenance
Nickel aluminide powder requires controlled conditions during installation:
- Use inert gas glove boxes for handling powder
- Minimize exposure to air/moisture
- Control room temperature between 20-30°C
- Keep powder containers sealed when not in use
For operation, important factors are:
- Avoid contamination from tools/dies
- Calibrate dispensing equipment periodically
- Monitor density/flowability
For maintenance:
- Clean equipment regularly
- Inspect glove boxes, seals, tubing for leaks
- Follow material safety procedures
Choosing the Right Supplier
Key factors when selecting a nickel aluminide powder supplier:
- Technical expertise and testing capabilities
- Quality certifications like ISO 9001
- Consistent production process and quality control
- Reasonable minimum order quantity
- Customization services for particle size, shape, purity
- Responsiveness to inquiries and requests
- Competitive pricing for small to large volumes
- Location and logistics infrastructure
Pros and Cons of Nickel Aluminide Powder
Pros | Cons |
---|---|
High strength at elevated temperatures | Brittle below 700°C |
Excellent corrosion resistance | Significant oxidation above 1000°C |
Low density compared to superalloys | Less ductility than nickel alloys |
Good thermal conductivity | More expensive than steel/aluminum |
High stiffness and creep resistance | |
Improved fatigue life |
Advantages Over Other Materials
Compared to other high-temperature alloys, nickel aluminide offers:
- Higher strength than stainless steel at >700°C
- Better oxidation resistance than nickel alloys up to 1000°C
- Lower density versus superalloys like Inconel
- Cost savings over exotic alloys like Hastelloy
- Less prone to thermal fatigue versus tungsten alloys
However, limitations include lower tensile ductility, fracture toughness, and high temperature stability above 1000°C.
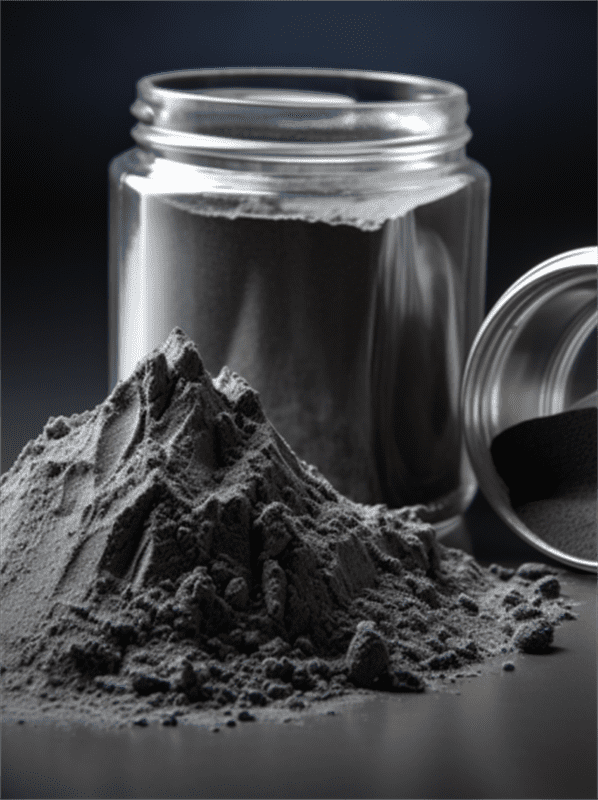
Applications and Use Cases
Nickel aluminide powder has found applications in diverse industries that demand materials capable of withstanding high temperatures:
Aerospace Applications
The aerospace industry utilizes nickel aluminide powder for:
Aircraft Engines
- Turbine blades, vanes, combustors
- Afterburner components, tails cones
- Engine exhaust nozzles
- Thermal management systems
Rocket/Spacecraft
- Rocket engine nozzles, thrusters
- Thermal protection systems
- Structural panels, thrust chambers
Key properties like high-temperature strength, creep resistance, oxidation resistance, and lower density make nickel aluminide suitable for aerospace systems operating at extreme conditions for prolonged durations.
By replacing superalloys with nickel aluminides, weight reductions up to 30% can be achieved in some applications. This improves fuel efficiency.
Automotive Applications
In automobiles, nickel aluminide finds usage in:
Powertrain
- Turbocharger rotors
- Pistons, cylinder heads
- Valve components
- Fuel injection systems
Exhaust System
- Catalytic converters
- Particulate filters
- Mufflers, tailpipes
The high-temperature capability along with castability allows nickel aluminide to withstand stresses in powertrain parts and corrosive exhaust gases for improved durability and emissions control.
Industrial Applications
Nickel aluminide powder is utilized in high-temperature industrial processes like:
Petrochemical
- Reactors, heaters, reformers
- Syngas coolers, heat exchangers
- Burner nozzles, flares
Power Generation
- Heat recovery steam generators
- Waste heat exchangers
- Coal gasification, IGCC plants
Glass Manufacturing
- Melting pots, stirrers
- Thermocouples, regulators
- Fiber drawing equipment
The excellent corrosion/oxidation resistance coupled with high-temperature strength makes nickel aluminide suitable for equipment handling hot corrosive media in chemical, petrochemical and power plants.
Production Methods
Nickel aluminide powder can be produced through various methods that control the powder morphology, particle size distribution, oxide content and other parameters:
Gas Atomization
- Molten alloy stream atomized by inert gas into fine droplets
- Rapid solidification yields spherical powder
- Tight control of particle size distribution
- Oxide content <1000 ppm
Plasma Rotating Electrode Process (PREP)
- Graphite electrode rotated in argon plasma
- Material melted and thrown off by centrifugal force
- Irregularly shaped particles formed
- Medium control of size distribution
- Oxide content ~2000 ppm
Mechanical Alloying
- Elemental metal powders milled together
- Repeated cold welding and fracturing
- Tight particle size distribution
- Oxide content dependent on initial powders
Electrode Induction Melting Gas Atomization (EIGA)
- Consumable electrode induction melted in inert gas
- Improved process control and cleanliness
- Very low oxide content <500 ppm
- Applicable for reactive alloys like aluminides
Gas atomization provides the best combination of particle sphericity, size distribution control and low oxide content. Mechanical alloying has challenges with oxygen pickup. EIGA allows lower oxide levels but higher cost.
nickel aluminide powder Specifications
Nickel aluminide powder is available in various size ranges, purity levels, morphologies and forms based on the production process and intended application:
Particle Size Distribution
Size Range | Typical Usage |
---|---|
10-38 μm | Thermal spray coatings, PM sintering |
45-105 μm | Metal injection molding, CIP |
150-250 μm | Laser cladding, welding |
Smaller particle sizes allow better densification while larger sizes provide faster feeding and deposition rates. Custom sizes can be produced based on need.
Chemical Composition
Component | Content Range |
---|---|
Nickel | 30-65% |
Aluminum | Balance |
Oxygen | 500-2500 ppm |
Nitrogen | 50-500 ppm |
Carbon | 50-1000 ppm |
Higher aluminum content improves oxidation resistance. Tighter control of oxygen and carbon is needed for critical applications. Other elements like Cr, Co, Ta, Mo can be alloyed for customized properties.
Powder Morphology
Type | Characteristics |
---|---|
Spherical | Improved flowability, packing density |
Irregular | More cost-effective production |
Blended | Mixture of particle shapes |
Encapsulated | Core-shell structure for reactivity control |
Spherical powder provides better handling while irregular powder can achieve higher density parts after compaction. Core-shell morphologies allow reactive alloy formation.
Forms and Blends
- Single component powders
- Pre-alloyed blends
- Elemental or master alloy blends
- Composite blends with oxides, carbides
Different starting powder compositions can be customized to achieve target properties in the final part.
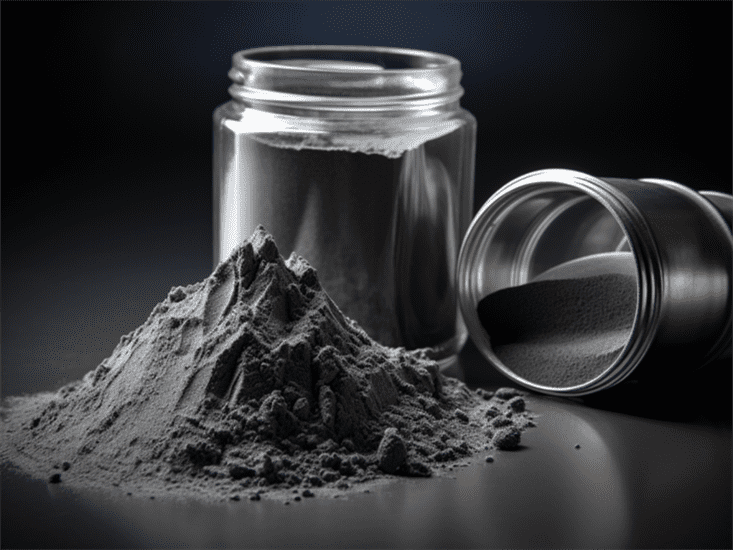
How to Choose Nickel Aluminide Powder
Selecting the right nickel aluminide powder requires evaluating key parameters based on production method, application requirements and specifications:
Particle Size
- Finer for thermal spray, metal injection molding
- Coarser for laser cladding, welding
- Multimodal distribution for optimal packing density
Purity Levels
- High purity for aerospace applications
- Lower purity acceptable for industrial uses
- Control of O2, N2 and C critical
Morphology
- Spherical for powder bed fusion AM
- Irregularacceptable for press and sinter
- Blended shapes to improve density
Oxide Content
- <1000 ppm preferred for fatigue resistance
- 2000-3000 ppm typical for sintered parts
- Core-shell structure to limit oxidation
Alloy Composition
- NiAl for balance of properties
- Ni3Al for maximum strength
- NiAl3 for oxidation resistance
- Tailor Al and Ni levels based on need
Price vs Performance
- Evaluate pricing from multiple suppliers
- Assess price breaks for larger quantities
- Compare quality certification and support
Work closely with powder producers to select the nickel aluminide powder composition and characteristics optimized for your production process and target application.
How to Use Nickel Aluminide Powder
Using nickel aluminide powder requires proper storage, handling procedures and processing to achieve desired properties:
Storage and Handling
- Store sealed containers in a dry, inert atmosphere
- Use argon-filled glove boxes for powder handling
- Limit exposure to air and moisture during transfer
- Avoid sparks, flames, ignition sources
Mixing and Blending
- Gentle dry mixing in closed containers
- Consider pre-alloyed versus elemental blends
- Optimize blending time cycle for homogeneity
Compaction
- Cold isostatic pressing up to 200 MPa
- Warm isostatic pressing up to 300 MPa
- Hot pressing in vacuum or inert gas
- Minimize air exposure during compaction
Sintering
- Vacuum or reducing atmosphere preferred
- Sinter between 1000-1300°C
- Slow cooling to prevent cracking
Post Processing
- Hot isostatic pressing to eliminate porosity
- Heat treatment to modify microstructure
- Machining/grinding for final dimensions
Controlled processing and minimizing oxygen contamination throughout the conversion process is key to achieving high quality nickel aluminide parts.
Installation and Maintenance of Nickel Aluminide Parts
Proper installation and maintenance procedures need to be followed for nickel aluminide components used in high-temperature applications:
Installation Guidelines
- Thoroughly clean surfaces and interfaces
- Use anti-seize compounds on threads
- Apply torque gradually to avoid galling
- Account for thermal expansion gaps
In-Service Care
- Monitor operating temperatures and pressures
- Avoid thermal shock during start-up/shutdown
- Adjust cycle times to minimize damage
- Periodically inspect for cracks, wear
Maintenance Best Practices
Issue | Solution |
---|---|
Oxidation | Apply protective coatings, limit overheating |
Creep deformation | Adjust operating stresses and alloy composition |
Fatigue cracking | Optimize part design to minimize stress risers |
Corrosion pitting | Use inhibitors, coatings, cathodic protection |
Fouling, coking | Improve filtration, scheduled cleaning cycles |
Proper installation alignment, avoiding thermal shock, and monitoring creep/fatigue damage mechanisms during service can extend the reliable operating life of nickel aluminide components.
Nickel Aluminide Powder vs Alternatives
Nickel aluminide has some advantages and disadvantages compared to other high-temperature structural materials:
Versus Superalloys
- Higher strength-to-weight ratio
- Better oxidation resistance
- Lower material costs
- Less formability and weldability
Versus Refractory Metals
- Lower density for weight savings
- More ductile and tougher
- Less susceptibility to embrittlement
- Lower strength above 1000°C
Versus Ceramics
- Greater fracture toughness
- More thermally and electrically conductive
- Easier to fabricate complex shapes
- Lower hardness and abrasion resistance
Versus Composites
- Simpler alloy production and processing
- More isotropic properties
- Higher environmental stability
- Lower maximum use temperature
The optimum balance of properties and cost make nickel aluminides suitable for applications where superalloys may be too expensive but lower cost alloys lack sufficient performance.
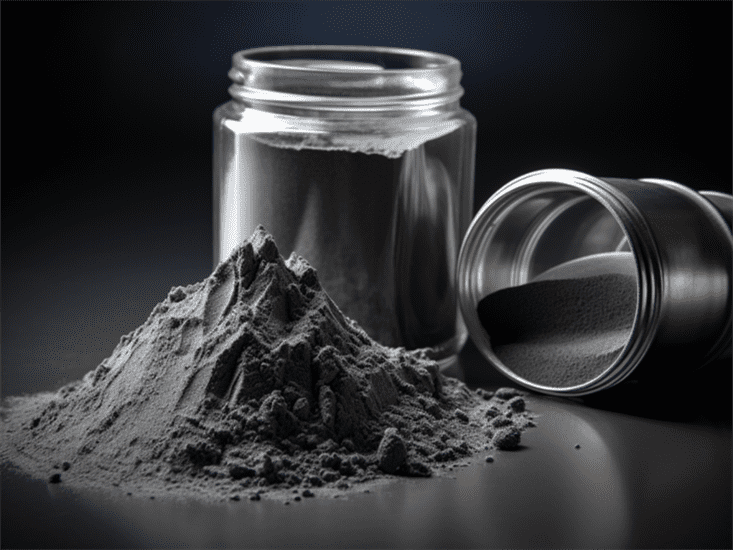
FAQ
Here are answers to some common questions about nickel aluminide powder:
What are the main advantages of nickel aluminide?
Nickel aluminide offers an excellent combination of high strength, creep resistance, corrosion resistance, and oxidation resistance at temperatures above 700°C along with lower density compared to superalloys.
What are the limitations of nickel aluminide?
Limitations include lower tensile ductility and fracture toughness compared to other alloys. Oxidation resistance deteriorates above 1000°C. Ambient temperature properties are also inferior.
What industries use nickel aluminide?
Major applications are in aerospace, automotive, chemical processing, power generation, and glass manufacturing where high temperature capability is needed.
How is nickel aluminide powder produced?
Main production methods include gas atomization, plasma rotating electrode process (PREP), mechanical alloying, and electrode induction gas atomization (EIGA).
What particle sizes are available?
Nickel aluminide powder can be supplied in particle size distributions ranging from 10-250 microns. Finer sizes are used for thermal spray while coarser sizes are preferred for laser cladding.
What affects the pricing of nickel aluminide powder?
Pricing depends on purity levels, production method, particle characteristics, order quantity, customization, and supplier margins. High purity spherical powder commands premium pricing.
How is nickel aluminide powder used?
Key steps involve controlled storage, mixing, compaction, sintering, heat treatment, and machining to make finished components. Minimizing oxygen exposure is critical throughout powder handling and processing.
How does nickel aluminide compare to superalloys?
Nickel aluminide has higher strength-to-weight ratio but inferior ambient temperature properties and formability compared to typical superalloys like Inconel 718, Hastelloy X.
What are hazards associated with nickel aluminide?
Like other nickel alloys, nickel aluminide powder is flammable and a health hazard. Proper protective equipment and handling procedures should be used to minimize risks.