Cu 99.95 Powder
Cu 99.95 powder, also referred to as electrolytic tough pitch (ETP) copper powder, is a high purity copper powder containing a minimum of 99.95% copper. It has excellent electrical and thermal conductivity combined with good mechanical properties. Key applications include electrical contacts, brushes, welding products, brazing, friction materials and diamond tools.
Low MOQ
Provide low minimum order quantity to meet different needs.
OEM & ODM
Provide customized products and design services to meet unique customer needs.
Adequate Stock
Ensure fast order processing and provide reliable and efficient service.
Customer Satisfaction
Provide high quality products with customer satisfaction at the core.
share this product
Table of Contents
Overview of Cu 99.95 Powder
Cu 99.95 powder, also referred to as electrolytic tough pitch (ETP) copper powder, is a high purity copper powder containing a minimum of 99.95% copper.
It has excellent electrical and thermal conductivity combined with good mechanical properties. Key applications include electrical contacts, brushes, welding products, brazing, friction materials and diamond tools.
Some key properties and advantages of Cu 99.95 powder include:
Cu 99.95 Powder Properties and Characteristics
Properties | Details |
---|---|
Composition | 99.95% minimum copper |
Density | 8.94 g/cc |
Particle shape | Irregular, angular |
Size range | 2-150 microns |
Apparent density | Up to 50% of true density |
Flowability | Low to moderate |
Conductivity | Excellent electrical and thermal conductivity |
Sinterability | Good sinterability in H2 atmosphere |
Purity | High purity copper |
Cu 99.95 provides an optimal balance of conductivity, mechanical properties, sintering characteristics and cost for fabrication of parts via pressing and sintering.
Cu 99.95 Powder Composition
Typical composition of Cu 99.95 powder:
Cu 99.95 Powder Composition
Element | Weight % |
---|---|
Copper (Cu) | 99.95% min |
Oxygen (O) | 0.05% max |
Lead (Pb) | 0.005% max |
Other impurities | 0.005% max |
- Copper provides excellent conductivity and ductility
- Oxygen present as impurity affects conductivity and sintering
- Lead and other impurities carefully controlled
High copper content gives excellent electrical and thermal conductivity combined with good mechanical properties after sintering.
Cu 99.95 Powder Physical Properties
Cu 99.95 Powder Physical Properties
Properties | Values |
---|---|
Density | 8.94 g/cc |
Melting point | 1083°C |
Thermal conductivity | 400 W/mK |
Electrical resistivity | 1.72 μΩ-cm |
Recrystallization temperature | 200-300°C |
Curie temperature | -269°C |
- High density compared to iron and aluminum
- Excellent thermal conductivity for heat removal
- Low electrical resistivity provides high conductivity
- Resistivity increases above Curie temperature
- Recrystallization enables sintering and improves ductility
The physical properties make Cu 99.95 suitable for applications like electrical contacts and brushes requiring high conductivity.
Cu 99.95 Powder Mechanical Properties
Cu 99.95 Powder Mechanical Properties
Properties | Values |
---|---|
Tensile strength | 220-340 MPa |
Yield strength | 70-190 MPa |
Elongation | 35-60% |
Hardness | 45-90 HB |
Modulus of elasticity | 110-130 GPa |
Compressive strength | 500-700 MPa |
- Good combination of strength and high ductility
- Relatively low hardness and high malleability
- Moderate strength levels compared to high strength alloys
- Properties depend on factors like porosity and grain size
The mechanical properties make Cu 99.95 suitable for softer conductive components that require deformation and compressive strength.
Cu 99.95 Powder Applications
Typical applications of Cu 99.95 powder include:
Cu 99.95 Powder Applications
Industry | Application Examples |
---|---|
Electrical and electronics | Contacts, connectors, brushes, RF shielding |
Automotive | Brushes, bushings, bearings |
Industrial | Welding electrodes, casting molds, metal matrix composites |
Manufacturing | Brazing and soldering, tooling components |
Friction products | Brake pads, clutch discs |
Some specific uses:
- Sliding electrical contacts and brushes
- Structural components requiring conductivity
- Jewelry crafting and artisanal products
- Diamond tools with copper metal matrix
- Welding rods and brazing paste formulations
- Mold liners for casting reactive alloys
The excellent balance of conductivity, mechanical properties, formability and cost make Cu 99.95 suitable for this broad range of applications.
Cu 99.95 Powder Specifications
Key specifications for Cu 99.95 powder include:
Cu 99.95 Powder Specifications
Standard | Description |
---|---|
ASTM B602 | Standard specification for undeformed, wrought, electrolytic tough pitch copper |
JIS H3125 | Electrolytic copper and copper alloy powders |
ISO 3497 | Copper powders for general purposes |
ASTM B Guidance | Apparent density, flow rate, particle size distribution |
These standards define:
- Minimum 99.95% copper content
- Limits on impurities like O, Pb
- Required powder characteristics
- Production method – electrolytic process
- Acceptable particle size distribution
- Testing methods for powder properties
Compliance ensures the powder meets the required purity and properties for the intended application.
Cu 99.95 Powder Particle Sizes
Cu 99.95 Powder Particle Size Distribution
Particle Size | Characteristics |
---|---|
2-20 microns | Very fine powder used in microelectronics |
5-30 microns | Fine powder for sintering and injection molding |
15-150 microns | Coarse powder suitable for pressing |
- Finer powder sizes provide greater sintered density
- Coarse powder has better flowability for automated filling
- Size range tailored based on part requirements
- Both irregular and spherical powder shapes are available
Controlling particle size distribution allows optimizing pressing characteristics, sintered density and properties.
Cu 99.95 Powder Apparent Density
Cu 99.95 Powder Apparent Density
Apparent Density | Details |
---|---|
Up to 50% of true density | For irregular powder morphology |
3.5-5.0 g/cc typical | Compacts to nearly full density after pressing and sintering |
- Higher apparent density improves powder flow and compactibility
- Irregular morphology limits maximum packing density
- Values up to 60% are possible with optimized spherical powder
- High green density after compaction enables good sintering
Higher apparent density improves manufacturing productivity and part quality.
Cu 99.95 Powder Production Method
Cu 99.95 Powder Production
Method | Details |
---|---|
Electrolysis | Copper cathodes dissolved anodically into Cu+ ions which are deposited onto stainless steel cathodes |
Grinding | Coarse powder broken down and classified into specific size ranges |
Annealing | Softens the powder particles and improves compressibility |
Reducing atmosphere | Prevents oxidation of particles during production |
- Automated electrolytic process allows high purity powder production
- Grinding and sieving provides controlled particle size distribution
- Annealing enables easy compaction into high density parts
- Strict process control ensures reliable and consistent powder quality
Cu 99.95 Powder Pricing
Cu 99.95 Powder Pricing
Factor | Impact on Price |
---|---|
Purity grade | Higher purity grades cost more |
Particle size | Ultrafine is more expensive |
Order quantity | Price decreases with bulk orders |
Production method | Additional processing increases cost |
Packaging | Special packaging like vacuum sealing adds cost |
Indicative Pricing
- Cu 99.95 fine powder: $8-12 per kg
- Cu 99.95 coarse powder: $7-10 per kg
- Reduced pricing applicable for bulk orders >500 kg
Pricing depends on order volume, particle size, production method, purity level and packaging.
Cu 99.95 Powder Suppliers
Cu 99.95 Powder Suppliers
Company | Location |
---|---|
Kymera International | USA |
GGP Metalpowder | Germany |
American Chemet Corporation | USA |
Shanghai CNPC Powder Material | China |
Nuclead | France |
Libo Metals | China |
Selection factors for suppliers:
- Powder purity levels and grades offered
- Production capacity and lead times
- Average particle size ranges
- Customization of size distribution
- Packaging and minimum order quantity
- Pricing levels based on order volume
- Compliance with international specifications
Cu 99.95 Powder Handling and Storage
Cu 99.95 Powder Handling
Recommendation | Reason |
---|---|
Avoid inhalation | Potential respiratory irritation |
Use masks, gloves | Prevent ingestion |
Ensure adequate ventilation | Reduce airborne particles |
Avoid ignition sources | Flammable dust hazard |
Follow anti-static procedures | Prevent fire from static discharge |
Use non-sparking tools | Avoid ignition during handling |
Store in cool, dry location | Prevent oxidation and moisture absorption |
Storage Recommendations
- Store in sealed containers away from acids or chlorides
- Maintain temperatures below 27°C
- Limit exposure to:
- Oxidizing acids like nitric acid
- Hot sulfuric acid
- Hydrogen sulfide
- Ammonia solutions
- Chlorinated hydrocarbons
Proper handling and storage helps preserve purity and prevent reactivity or fire hazards.
Cu 99.95 Powder Inspection and Testing
Cu 99.95 Powder Testing
Test Type | Details |
---|---|
Chemical analysis | ICP analysis to verify composition |
Particle size distribution | Laser diffraction analysis |
Apparent density | Hall flowmeter test per ASTM B212 |
Powder morphology | SEM imaging |
Tap density | Measured after mechanical tapping |
Flow rate analysis | Gravity flow rate through specified nozzle |
Stringent testing ensures the powder meets chemical, physical and morphological specifications required for the application.
Cu 99.95 Powder Pros and Cons
Advantages of Cu 99.95 Powder
- Excellent electrical and thermal conductivity
- Good ductility and malleability
- Cost-effective compared to pure silver or gold
- Good corrosion resistance and bio-compatibility
- Easy to sinter and compress into high density parts
- Recyclable and environmentally friendly
Limitations of Cu 99.95 Powder
- Lower strength than high strength alloys
- Moderate high temperature oxidation resistance
- Heavy compared to magnesium and aluminum
- Not suitable for highly stressed load-bearing components
- Surface tarnishing over time if uncoated
- Restricted food contact applications
Comparison With CuCrZr Powder
Cu 99.95 vs CuCrZr Powder
Parameter | Cu 99.95 | CuCrZr |
---|---|---|
Density | 8.94 g/cc | 8.8 g/cc |
Strength | 220-340 MPa | 450-650 MPa |
Conductivity | Excellent | Moderate |
Thermal stability | Fair | Excellent |
Cost | Low | High |
Uses | Electrical, thermal,moderate load | High strength structural parts |
- Cu 99.95 has better conductivity and lower cost
- CuCrZr provides higher strength and thermal stability
- Cu 99.95 suitable for softer conductive components
- CuCrZr preferred for high load structural parts
Cu 99.95 Powder FAQs
Q: What are the main applications of Cu 99.95 powder?
A: The main applications include electrical contacts, brushes, welding products, diamond tools, brazing alloys, friction materials, and metal matrix composites. It is widely used in electronics, automotive and industrial products.
Q: What affects the properties of Cu 99.95 powder parts?
A: Key factors affecting properties are apparent density, amount of lubricant, compacting pressure, sintering time/temperature, powder composition, particle size distribution, and presence of impurities.
Q: What precautions should be taken when handling Cu 99.95 powder?
A: Recommended precautions include avoiding inhalation, ensuring proper ventilation, wearing protective gear, controlling static discharge, using non-sparking tools, avoiding ignition sources, and storing in a cool, dry location in sealed containers.
Q: How does Cu 99.95 powder differ from bronze and brass powders?
A: Bronze and brass are copper alloys with tin and zinc while Cu 99.95 is pure copper. It has higher conductivity but lower strength than bronze or brass. Cu 99.95 is more cost-effective.
About Met3DP
Product Category
HOT SALE
CONTACT US
Any questions? Send us message now! We’ll serve your request with a whole team after receiving your message.
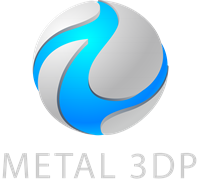
Leading provider of additive manufacturing solutions headquartered in Qingdao, China.
COMPANY
PRODUCT
cONTACT INFO
- Qingdao City, Shandong, China
- info@metal3dp.com
- amy@metal3dp.com
- +86 19116340731