CoCr28Mo6 Powder
CoCr28Mo6 powder, also known as ASTM F75 alloy, is a cobalt-chromium-molybdenum alloy powder used for manufacturing of orthopedic implants due to its biocompatibility, high strength and corrosion resistance.
Low MOQ
Provide low minimum order quantity to meet different needs.
OEM & ODM
Provide customized products and design services to meet unique customer needs.
Adequate Stock
Ensure fast order processing and provide reliable and efficient service.
Customer Satisfaction
Provide high quality products with customer satisfaction at the core.
share this product
Table of Contents
Overview of CoCr28Mo6 Powder
CoCr28Mo6 powder, also known as ASTM F75 alloy, is a cobalt-chromium-molybdenum alloy powder used for manufacturing of orthopedic implants due to its biocompatibility, high strength and corrosion resistance.
It has excellent wear resistance and is commonly used for making hip, knee and dental implants. The “28Mo6” designation indicates it contains 28% chromium and 6% molybdenum.
Key properties and advantages:
CoCr28Mo6 Powder Properties and Characteristics
Properties | Details |
---|---|
Composition | Co-28Cr-6Mo alloy |
Density | 8.3 g/cc |
Particle shape | Irregular, angular |
Size range | 10-45 microns |
Apparent density | 4.0-4.5 g/cc |
Flowability | Moderate |
Corrosion resistance | Excellent due to passive oxide layer |
Biocompatibility | High, used for implants |
Wear resistance | Very good due to high Cr content |
Cost | Moderate to high |
CoCr28Mo6 powder can be used to manufacture implants using 3D printing or traditional techniques like metal injection molding. It provides an optimal combination of mechanical properties, corrosion resistance and biocompatibility.
CoCr28Mo6 Powder Composition
Typical composition of CoCr28Mo6 powder:
CoCr28Mo6 Powder Composition
Element | Weight % |
---|---|
Cobalt | Balance |
Chromium | 27-30% |
Molybdenum | 5-7% |
Nickel | <1% |
Manganese | <1% |
Carbon | <0.35% |
Iron | <0.75% |
Silicon | <1% |
- Cobalt provides strength, toughness, and biocompatibility
- Chromium improves corrosion and wear resistance
- Molybdenum contributes to high strength and hardness
- Other elements like C, Ni, Mn, Fe, and Si present as impurities
The high Cr and Mo content result in excellent mechanical properties required for load bearing implant applications.
CoCr28Mo6 Powder Physical Properties
CoCr28Mo6 Powder Physical Properties
Properties | Values |
---|---|
Density | 8.3 g/cc |
Melting point | 1350-1400°C |
Thermal conductivity | 18 W/mK |
Electrical resistivity | 94 μΩ-cm |
Curie temperature | 1329°C |
Coefficient of thermal expansion | 14.5 x 10^-6 /K |
- High density compared to titanium alloys
- Maintains strength at elevated temperatures
- Lower thermal conductivity than pure metals
- Becomes paramagnetic above Curie temperature
- CTE higher than other competing alloys
These properties make it suitable for high temperature load bearing implant applications requiring corrosion resistance.
CoCr28Mo6 Powder Mechanical Properties
CoCr28Mo6 Powder Mechanical Properties
Properties | Values |
---|---|
Hardness | 35-45 HRC |
Tensile strength | 170-220 ksi (1170-1510 MPa) |
Yield strength | 140-180 ksi (965-1240 MPa) |
Elongation | 8-16% |
Modulus of elasticity | 230-300 GPa |
Fatigue strength | 50 ksi (345 MPa) |
- Excellent combination of strength and ductility
- Strength levels exceed requirements for load bearing implants
- Hardness provides good wear and abrasion resistance
- High fatigue strength ensures durability under cyclic loading
The mechanical properties make CoCr28Mo6 suitable for orthopedic implants experiencing high static and dynamic loads.
CoCr28Mo6 Powder Applications
Primary applications of CoCr28Mo6 powder include:
CoCr28Mo6 Powder Applications
Application | Examples |
---|---|
Orthopedic implants | Hip, knee, dental implants |
Medical devices | Surgical tools, instruments |
Aerospace | Turbine engine components |
Automotive | Fuel injection parts |
Industrial | Valves, tooling, molds |
Some specific product uses:
- Articulating surfaces in joint replacement implants
- Dental crowns, bridges and root implants
- Orthopedic fixation devices like bone plates
- High temperature resistant aerospace engine components
- Automotive fuel injection nozzles
- Cutting tools, gaskets, valves requiring wear resistance
The biocompatibility, corrosion resistance and tribological properties make CoCr28Mo6 highly suitable for orthopedic and dental applications.
CoCr28Mo6 Powder Specifications
Key standards for CoCr28Mo6 powder:
CoCr28Mo6 Powder Standards
Standard | Description |
---|---|
ASTM F75 | Wrought Co-Cr-Mo alloy for surgical implants |
ASTM F1537 | Specification for wrought Co-Cr-Mo alloy for dental appliances |
ISO 5832-4 | Implant grade wrought Co-Cr-Mo-Ni alloy |
ASTM F3056 | Specification for additive manufacturing CoCr alloy for orthopedic implants |
These standards specify:
- Chemical composition limits
- Mechanical property requirements
- Production method (gas atomization)
- Acceptable impurity levels
- Quality assurance processes
- Test methods to verify powder properties
Meeting these requirements ensures suitability for orthopedic implant applications.
CoCr28Mo6 Powder Particle Size
CoCr28Mo6 Powder Particle Size Distribution
Particle size | Characteristics |
---|---|
10-25 microns | Used for laser powder bed fusion (LPBF) |
25-45 microns | Used for binder jetting and DMLS |
15-45 microns | Used for metal injection molding |
- Finer powder provides better resolution and surface finish in AM
- Coarser powder improves flowability for powder processing
- Size range selection depends on production technique used
- Tight control over particle size distribution is maintained
Controlling particle size and morphology is critical for high powder packing density and optimized sintering.
CoCr28Mo6 Powder Apparent Density
Typical apparent density:
CoCr28Mo6 Powder Apparent Density
Apparent density | Characteristics |
---|---|
4.0 – 4.5 g/cc | Irregular powder morphology |
35-45% of true density | Due to voids between particles |
- Higher apparent density improves powder flow and compressibility
- Irregular shape and wide size distribution reduces packed density
- Values up to 60% are possible with optimized spherical powder
Higher apparent density allows efficient powder pressing and sintering to full density. It improves manufacturing productivity.
CoCr28Mo6 Powder Production Method
CoCr28Mo6 Powder Production
Method | Details |
---|---|
Gas atomization | High pressure inert gas breaks up molten alloy stream into fine droplets |
Vacuum induction melting | High purity starting materials melted under vacuum |
Multiple remelting | Improves chemical homogeneity |
Sieving | Classifies powder into different size fractions |
Blending | Different powder sizes blended to customize particle size distribution |
- Gas atomization produces fine spherical powder morphology
- Vacuum melting and multiple remelting minimize impurities
- Post-processing provides fine control over particle size distribution
Automated production and strict process control ensures reliable and consistent properties of CoCr28Mo6 powder.
CoCr28Mo6 Powder Pricing
CoCr28Mo6 Powder Pricing
Factor | Impact on Price |
---|---|
Powder grade | Higher purity grades cost more |
Particle size | Ultrafine powder more expensive |
Order quantity | Price reduces for bulk orders |
Packaging | Argon filled containers increase cost |
Testing requirements | More rigorous testing increases cost |
Lead time | Faster delivery times increase price |
Indicative Pricing
- CoCr28Mo6 for medical: $80-120 per kg
- CoCr28Mo6 for industrial: $50-90 per kg
Reduced prices applicable for bulk orders exceeding several hundred kilograms.
CoCr28Mo6 Powder Suppliers
CoCr28Mo6 Powder Suppliers
Company | Location |
---|---|
Carpenter Powder Products | USA |
Praxair | USA |
Sandvik Osprey | UK |
Hoganas | Sweden |
Erasteel | France |
Aubert & Duval | France |
Factors for selecting supplier:
- Powder grades available
- Production capacity
- Powder quality and consistency
- Compliance to medical standards
- Pricing and minimum order quantity
- Lead time and delivery reliability
Medical grades require more rigorous quality control and testing.
CoCr28Mo6 Powder Handling and Safety
CoCr28Mo6 Powder Handling
Recommendation | Reason |
---|---|
Avoid inhalation | Due to risk of lung tissue damage from fine particles |
Use protective masks | Prevent accidental ingestion |
Handle in ventilated areas | Reduce airborne particle circulation |
Use hazmat suits | Minimize skin contact |
Ensure no ignition sources | Powder can combust in oxygen |
Follow anti-static protocols | Prevent fire from static discharge |
Use non-sparking tools | Avoid possibility of ignition during handling |
Store in sealed containers | Prevent contamination and oxidation |
CoCr28Mo6 powder is relatively inert but general precautions are recommended for safe handling and processing.
CoCr28Mo6 Powder Inspection and Testing
CoCr28Mo6 Powder Testing
Test | Details |
---|---|
Chemical analysis | Verifies composition using ICP spectroscopy |
Particle size distribution | Determines distribution using sieve analysis |
Apparent density | Measured as per ASTM B212 standard |
Powder morphology | SEM image analysis |
Flow rate analysis | Time taken for fixed powder quantity to flow through funnel |
Tap density test | Density measured after mechanical tapping |
Rigorous testing ensures consistent powder quality and compliance with specifications like ASTM F75 for medical grade powder.
CoCr28Mo6 Powder Storage and Handling
CoCr28Mo6 Powder Storage
Factor | Effect |
---|---|
Air, oxygen | Risk of oxidation at high temperatures |
Moisture | Low corrosion rate at room temperature |
Hydrocarbons | Fire hazard if allowed to contaminate powder |
Acids, alkalis | Resistant to dilute acids and bases |
Organic solvents | Some absorption and staining if immersed |
Temperatures above 400°C | Increased oxidation rate in air |
Recommendations:
- Store sealed in inert gas filled containers
- Keep below 30°C temperature
- Avoid contact with oxidizing acids and chlorinated solvents
- Open containers only in controlled environments
With proper precautions, CoCr28Mo6 powder exhibits good stability during storage and handling.
Comparison With Stainless Steel Powder
CoCr28Mo6 vs. Stainless Steel Powder
Parameter | CoCr28Mo6 | Stainless Steel |
---|---|---|
Density | 8.3 g/cc | 7.9 g/cc |
Tensile strength | 1170-1510 MPa | 600-1100 MPa |
Ductility | 8-16% | 15-40% |
Corrosion resistance | Excellent | Good |
Wear resistance | Excellent | Moderate |
Biocompatibility | High | Moderate |
Cost | High | Low |
Uses | Medical implants, aerospace | Industrial applications |
- CoCr28Mo6 has higher strength and hardness
- Stainless steel provides better ductility and toughness
- CoCr28Mo6 is more corrosion resistant
- CoCr28Mo6 is preferred for biomedical applications
- Stainless steel is more cost-effective
CoCr28Mo6 outperforms stainless steel for applications requiring high strength, hardness and corrosion resistance.
CoCr28Mo6 Powder Pros and Cons
Advantages of CoCr28Mo6 Powder
- Excellent biocompatibility and corrosion resistance
- High strength and hardness
- Good wear resistance
- High temperature capability
- Can be processed using AM or MIM techniques
- Suitable for load-bearing implant applications
- Provides good aesthetic appearance
Limitations of CoCr28Mo6 Powder
- More expensive than stainless steel or titanium alloys
- Lower ductility and fracture toughness
- Requires protective atmosphere during processing
- Difficult to machine compared to other alloys
- Limitations in joining and welding the material
- Release of Co ions in body raises health concerns
CoCr28Mo6 Powder FAQs
Q: What are the main applications of CoCr28Mo6 powder?
A: The main applications are orthopedic joint replacement implants like hips and knees, dental implants and crowns, surgical instruments, and high performance aerospace components.
Q: What gives CoCr28Mo6 excellent corrosion resistance?
A: The high chromium content enables formation of a stable, continuous and self-healing protective oxide layer on the surface preventing corrosion.
Q: What are the key differences between medical and industrial grades of CoCr28Mo6 powder?
A: Medical grade powder has higher purity, lower impurities, finer particle size, better size distribution control, and goes through more rigorous testing to meet standards like ASTM F75.
Q: What precautions are required during storage and handling of CoCr28Mo6 powder?
A: Recommended precautions include avoiding inhalation, using protective gear, ensuring proper ventilation, controlling static discharge, using non-sparking tools, and storing in sealed inert gas purged containers.
About Met3DP
Product Category
HOT SALE
CONTACT US
Any questions? Send us message now! We’ll serve your request with a whole team after receiving your message.
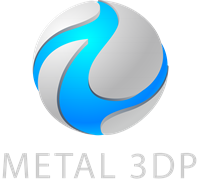
Leading provider of additive manufacturing solutions headquartered in Qingdao, China.
COMPANY
PRODUCT
cONTACT INFO
- Qingdao City, Shandong, China
- info@metal3dp.com
- amy@metal3dp.com
- +86 19116340731