Titanium and aluminum TA7 powder
TA7 powder belongs to the family of titanium aluminides, which are intermetallic compounds composed of titanium and aluminum. This unique powder exhibits exceptional strength, lightweight characteristics, and high-temperature stability, making it an attractive choice for numerous engineering applications.
Low MOQ
Provide low minimum order quantity to meet different needs.
OEM & ODM
Provide customized products and design services to meet unique customer needs.
Adequate Stock
Ensure fast order processing and provide reliable and efficient service.
Customer Satisfaction
Provide high quality products with customer satisfaction at the core.
share this product
Table of Contents
Overview of Titanium and Aluminum TA7 Powder
TA7 belongs to the titanium-aluminide intermetallic alloy system combining the lightweight properties of aluminum with the strength and corrosion resistance of titanium. The near-equiatomic ratio of Ti and Al provides an excellent balance of properties for elevated temperature applications.
Key characteristics of TA7 powder include:
- Very high specific strength (strength-to-weight ratio)
- Excellent high temperature tensile and creep strength
- Low density compared to nickel or steel alloys
- Good corrosion resistance in various environments
- Available in range of particle sizes and morphologies
TA7 powder has emerged as an excellent choice for reducing weight and improving efficiency in aerospace engines and airframes operating at high temperatures.
Chemical Composition of TA7 Powder
TA7 powder has the following nominal composition:
Element | Weight % |
---|---|
Titanium (Ti) | Balance |
Aluminum (Al) | 7% |
Tin (Sn) | 2-5% |
Zirconium (Zr) | 1-4% |
Silicon (Si) | 0.5% max |
Carbon (C) | 0.1% max |
Oxygen (O) | 0.13% max |
The amount of tin and zirconium can be varied to optimize the high temperature mechanical properties. Impurity levels of Si, C, O are minimized.
Properties of TA7 Powder
Key properties of TA7 powder include:
Property | Value |
---|---|
Density | 3.7-4.0 g/cm3 |
Melting Point | 1460°C |
Thermal Conductivity | 6.7 W/mK |
Electrical Resistivity | 1.78 μΩ.cm |
Young’s Modulus | 110 GPa |
Poisson’s Ratio | 0.32 |
Tensile Strength | 800 MPa |
Yield Strength | 760 MPa |
Elongation | 1-2% |
Creep Resistance | 190 MPa at 700°C |
The properties like high strength, low density, oxidation resistance and thermal stability make TA7 suitable for the most demanding elevated temperature applications.
Production Method for TA7 Powder
TA7 powder can be produced via methods like:
- Gas Atomization – High pressure inert gas used to atomize molten TA7 alloy resulting in spherical powder ideal for AM.
- Plasma Rotating Electrode Process – Centrifugal disintegration of rapidly rotating molten metal stream produces spherical powder.
- Mechanical Alloying – High energy ball milling of blended elemental Ti and Al powders followed by annealing.
Gas atomization provides excellent control over powder characteristics like particle size distribution, morphology, microcleanliness and flowability.
Applications of TA7 Powder
TA7 powder is commonly used in:
- Additive Manufacturing – Selective laser melting to produce complex airfoil shapes, impellers, turbine blades.
- Metal Injection Molding – To manufacture small, complex net-shape parts like turbocharger components needing high strength and temperature resistance.
- Thermal Spray Coatings – Applied via plasma or HVOF spraying on valve surfaces, bearings, landing gear components needing wear/corrosion resistance at high temperatures.
- Powder Metallurgy – Pressing and sintering to create lightweight, high-strength structural parts for aerospace applications.
Specifications of TA7 Powder
TA7 powder is available under various size ranges, shapes and purity levels:
- Particle Size: From 15-45 μm for AM methods, up to 100 μm for thermal spray processes.
- Morphology: Near-spherical powder shape provides optimal flow and packing density.
- Purity: From commercial purity to ultra high purity levels based on impurity limits and process requirements.
- Oxygen Content: Levels maintained below 2000 ppm for most applications.
- Flow Rate: Powder customized for excellent flow rates above 25 s/50 g.
Global Suppliers of TA7 Powder
Some of the major global suppliers of TA7 powder include:
- AP&C (Canada)
- TLS Technik (Germany)
- Sandvik Osprey (UK)
- Tekna (Canada)
- ECKA Granules (Germany)
- Metal Technology (UK)
These companies produce various grades of TA7 powder tailored for additive manufacturing, thermal spray, powder metallurgy and other high temperature applications.
Pricing of TA7 Powder
TA7 powder is priced higher than steels and nickel alloys:
- Quantity – $100-150 per kg for bulk orders above 500 kg. Smaller quantities are priced significantly higher.
- Quality – High purity, spherical powder manufactured under tightly controlled conditions using advanced processes demands premium pricing.
- Supplier – Major global suppliers offer cost advantages compared to smaller manufacturers due to higher production volumes.
- Geography – Prices vary across regions with Europe and North America being higher priced markets compared to Asia.
For critical applications, buyers should focus on powder quality rather than lowest cost while sourcing TA7 powder.
Storage and Handling of TA7 Powder
TA7 powder requires careful storage and handling:
- Should be stored in sealed containers under inert gas like argon to prevent oxidation.
- Avoid accumulation of fine powder to minimize risk of dust explosions.
- Use proper PPE, ventilation, grounding and safety practices during powder handling.
- Prevent contact between powder and ignition sources due to flammability hazard.
- Follow applicable safety guidelines from supplier SDS.
Care should be taken when handling this highly reactive alloy powder.
Inspection and Testing of TA7 Powder
Key quality control tests performed on TA7 powder:
- Chemical analysis using ICP-OES or XRF to ensure composition meets specifications.
- Particle size distribution using laser diffraction as per ASTM B822 standard.
- Morphology analysis through SEM imaging.
- Powder flow rate measurement using Hall flowmeter as per ASTM B213 standard.
- Density measurement by helium pycnometry.
- Impurity analysis through inert gas fusion or ICP-MS.
- Microstructure characterization by X-ray diffraction.
Thorough testing ensures batch consistency and powder quality for the intended application.
Comparison Between TA7 and Inconel 718 Powders
TA7 and Inconel 718 powders compared:
Parameter | TA7 | Inconel 718 |
---|---|---|
Density | 3.7-4.0 g/cm3 | 8.2 g/cm3 |
High temperature strength | Comparable | Comparable |
Oxidation resistance | Better | Good |
Cost | Higher | Lower |
Workability | Poor | Excellent |
Applications | Aerospace components | Aerospace, automotive |
Availability | Low | Readily available |
TA7 offers weight savings over Inconel 718. But workability is poor and availability is lower for titanium aluminide powder.
TA7 Powder FAQs
Q: How is TA7 powder produced?
A: TA7 powder is commercially produced using gas atomization, plasma rotating electrode process, and mechanical alloying followed by annealing. Gas atomization offers the best control of powder characteristics.
Q: What are the main applications of TA7 powder?
A: The major applications of TA7 powder include additive manufacturing, thermal spray coatings, metal injection molding, and powder metallurgy to manufacture lightweight structural parts needing high temperature capability.
Q: What is the typical TA7 powder size used for selective laser melting?
A: For SLM process, the ideal TA7 powder size range is 15-45 microns with spherical morphology and good powder flow and packing density.
Q: Does TA7 powder require special handling precautions?
A: Yes, it is highly reactive and requires careful handling under inert atmosphere using proper ventilation, grounding, PPE to prevent fire or explosion hazards.
Q: Where can I purchase TA7 powder suitable for aerospace parts?
A: For aerospace applications needing lightweight and high strength, TA7 powder can be purchased from leading manufacturers including AP&C, TLS Technik, Sandvik Osprey, and Tekna.
About Met3DP
Product Category
HOT SALE
CONTACT US
Any questions? Send us message now! We’ll serve your request with a whole team after receiving your message.
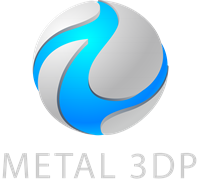
Leading provider of additive manufacturing solutions headquartered in Qingdao, China.
COMPANY
PRODUCT
cONTACT INFO
- Qingdao City, Shandong, China
- info@metal3dp.com
- amy@metal3dp.com
- +86 19116340731