3D printing, also known as additive manufacturing, allows creating physical objects by depositing materials layer by layer based on a digital 3D model. There are many different 3D printing technologies and materials to choose from depending on the application requirements. This comprehensive guide examines the most common 3D printing types, their key characteristics, suitable applications, and pros and cons to help select the right 3D printing method.
Overview of Key 3D Printing Methods
Here is a comparison of the most popular 3D printing technologies and materials available:
3D Printing Type | Materials | Key Characteristics | Typical Applications |
---|---|---|---|
Fused Deposition Modeling (FDM) | Thermoplastics like PLA, ABS, PETG | Low cost, good strength | Prototyping, hobbyist printing |
Stereolithography (SLA) | Photopolymers, resins | Excellent accuracy and surface finish | Jewelry, dental models |
Selective Laser Sintering (SLS) | Nylon, metal powders | Good mechanical properties | Functional prototyping, tooling |
Multi Jet Fusion (MJF) | Nylon plastic | High productivity, strength | Mass production |
Binder Jetting | Metal, sand, gypsum powders | Large build size, fast print speeds | Casting patterns, molds |
Material Jetting | Photopolymers | Multi-material printing capability | Medical models, arts |
This table summarizes the key 3D printing technologies, materials used, their characteristics, and typical applications. Read on for a more detailed examination of each 3D printing type.
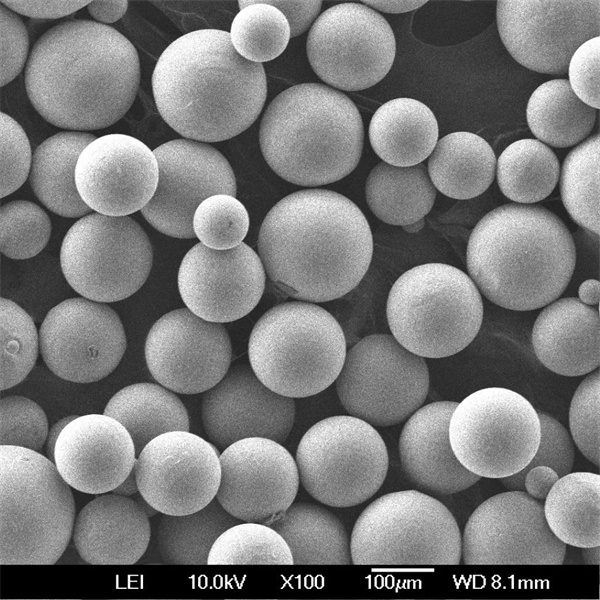
Fused Deposition Modeling (FDM)
Fused deposition modeling (FDM) is the most common and affordable 3D printing technology used by hobbyists and professionals alike.
How FDM 3D Printing Works
FDM printing works by heating a thermoplastic filament to a semi-liquid state and depositing it layer by layer on the print bed. As the layers are deposited, they fuse together and solidify to produce the final 3D object.
Key Components of an FDM 3D Printer:
- Print head – extrudes the melted plastic
- Print bed – provides a static base to print objects on
- Filament – the raw material, supplied as a spool of plastic wire
- Control system – guides the print head to deposit plastic precisely
The most commonly used filament materials are:
- PLA (Polylactic Acid) – Easy to print with, strongest material for FDM
- ABS (Acrylonitrile Butadiene Styrene) – Slightly flexible, durable plastic
- PETG (Polyethylene Terephthalate Glycol) – Combines strength of ABS with clarity of PLA
Advantages of FDM Printing
Low Cost: Both the printers and materials are very affordable compared to other 3D printing technologies. Hobbyist printers start at just a few hundred dollars.
Simple Operation: FDM printers are easy to set up and use. No complex post-processing required for the finished prints.
Choice of Materials: There are many types of filaments available – plastics, composites, flexibles and even dissolvable supports.
Limitations of FDM Printing
Lower Resolution: Layer heights are around 0.1 – 0.3mm resulting in a stair-stepping effect on slopes and curves.
Weak Inter-layer Bonding: Layers can delaminate under stress as there is no chemical fusion between layers.
Limited Geometries: FDM cannot make enclosed voids or undercuts as support material is required.
Warping: Thermoplastics like PLA and ABS shrink when cooling causing warping at corners.
FDM Printer Manufacturers
Some of the leading manufacturers of FDM 3D printers include:
- MakerBot
- Ultimaker
- Prusa Research
- FlashForge
- Raise3D
- CraftBot
There are also many hobbyist 3D printer kits like Creality and Artillery that offer great value.
FDM Printing Applications
Prototyping – Great for quickly iterating design prototypes and proof of concepts.
Education – FDM 3D printers are popular in schools and colleges for education.
Tooling – Can be used to print jigs, fixtures, guides and other manufacturing tools.
Hobbyist Printing – Enthusiasts use FDM to create models, cosplay props, miniatures, gadgets and more.
End-Use Parts – Can be used for production of final parts, best suited for components that don’t require high accuracy or surface finish.
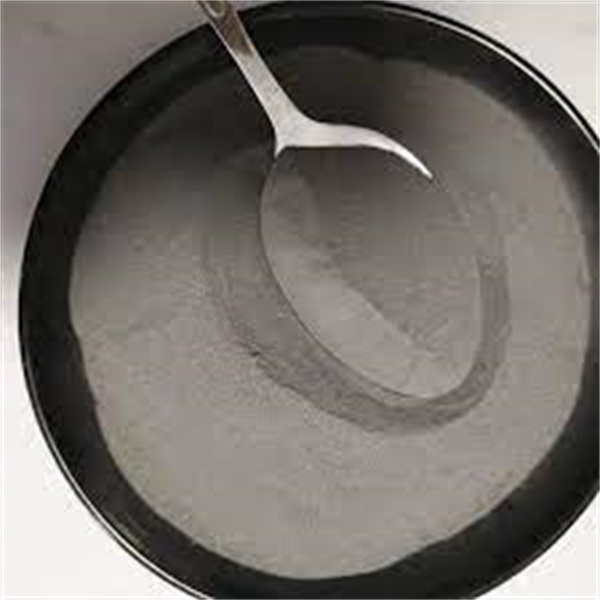
Stereolithography (SLA) Printing
Stereolithography (SLA) is a form of 3D printing that uses photopolymers that solidify when exposed to ultraviolet light. SLA can create highly accurate and smooth parts making it ideal for detailed models, jewelry, dental aligners and medical devices.
How SLA Printing Works
SLA printing starts with a vat of liquid photopolymer resin. A laser beam traces each layer pattern on the resin surface which solidifies the exposed areas. The build platform lifts to separate the printed layer from the vat and allow fresh resin to flow under for the next layer.
Key Components of an SLA Printer:
- UV laser – selectively cures resin layer by layer
- Resin vat – contains the liquid polymer resin
- Build platform – rises after each layer is printed
- Resin tank – stores and supplies the resin
Commonly used SLA resins include:
- Standard photopolymers – Accurate, moderately strong parts
- Durable and flexible resins – For more robust parts
- Castable resins – Burn out cleanly for metal casting
Benefits of SLA 3D Printing
Excellent Accuracy – Can produce highly detailed parts with smooth surfaces down to ~0.025 mm layer resolution.
Great Mechanical Properties – Objects printed are isotropic with strength comparable to injection molded parts.
Variety of Resins – Can choose resin properties from rigid to flexible and even bio-compatible.
No Supports Needed – The resin vat provides constant support during printing enabling complex geometries.
Limitations of SLA Printing
Smaller Build Volumes – SLA printers generally have smaller maximum print sizes (< 1 cubic foot).
Post-Processing Required – Printed parts must be cleaned and cured under UV light.
Resin Toxicity – Some photopolymers contain hazardous ingredients and irritants.
Resin Cost – Materials are considerably more expensive than FDM filament.
Popular SLA Printer Brands
Leading SLA 3D printer manufacturers include:
- Formlabs
- Peopoly
- Anycubic
- Phrozen
- Creality
- Elegoo
Many offer both hobbyist and professional SLA 3D printers.
Applications of SLA Printing
Jewelry – Excellent for making highly detailed jewelry pieces and master patterns.
Dental – Used to manufacture surgical guides, orthodontic models, and aligners.
Model Making – Highly accurate architectural models, miniatures and action figures.
Medical Devices – Suitable for customized prosthetics, implants and life-like anatomical models for surgeons.
Casting Patterns – Investment casting can produce metal end-use parts from SLA resin patterns.
Selective Laser Sintering (SLS)
Selective laser sintering (SLS) uses a laser to fuse powdered material and produce 3D objects. A wide choice of plastic, metal, ceramic and composite powders can be used in SLS printers to create functional prototypes and end-use parts.
How SLS 3D Printing Works
SLS printing takes place in a chamber filled with powder material. A laser selectively melts and fuses the powder grains together where required based on the 3D model. The print platform then lowers, allowing a fresh layer of powder to be rolled over the top. This cycle repeats until the full object is built in the powder bed.
Key Components of SLS Printers:
- CO2 laser – selectively fuses powder material
- Powder bed – stores and supplies the raw material powder
- Roller – spreads fresh powder for each layer
- Heat lamp – preheats powder just below melting point
Common SLS materials include:
- Nylon (PA 12) – Most used plastic for strong, durable parts
- Alumide – Nylon-aluminum composite filament, mimics metal
- TPU, PEBA – Flexible materials for rubber-like components
- PEEK, PEKK – High performance thermoplastics, heat/chem resistant
- Stainless steel – For high strength end-use metal parts
Benefits of SLS Printing
Functional Strength Parts – Near isotropic properties allow functional prototypes and end-use parts.
Complex Geometries – Self supporting shapes and lattice structures are possible by printing in powder bed.
Choice of Materials – SLS can process various metals, plastics, polymers, composites and ceramics.
No Supports Needed – The surrounding powder itself acts as support during printing.
Drawbacks of SLS Printing
Rough Surfaces – Powder-based printing results in a grainy surface finish requiring secondary finishing.
Large Equipment – SLS printers are considerably bulkier and heavier than other technologies.
Material Costs – Powder materials are more expensive compared to filament.
Post-Processing – Unfused powder must be cleaned off printed parts before use.
SLS Printer Manufacturers
Prominent SLS 3D printer companies include:
- 3D Systems
- EOS
- Farsoon
- Prodways
- Ricoh
- Sharebot
- Sintratec
Both industrial and desktop SLS printers are now available.
Applications of SLS Printing
Functional Prototyping – Used to create working models for fit, assembly and performance testing.
Manufacturing Tools – Print production line jigs, fixtures, inspection gauges, etc.
End-Use Parts – Aerospace and automotive industries use SLS to make finished components.
Biomedical – SLS can make customized implants, scaffolds and medical tools.
Architecture – Detailed scale models of buildings, topography and terrain made via SLS printing.
Multi Jet Fusion (MJF) Technology
Multi jet fusion (MJF) is a powder bed 3D printing process developed by HP. It uses an array of inkjet printheads to selectively deposit fusing and detailing agents on the powder layers. MJF enables productive and scalable manufacturing applications with excellent part quality.
How MJF 3D Printing Works
The MJF printing process takes place inside a powder bed chamber very similar to SLS. Inkjet printheads selectively deposit fusing agent where the part should solidify. This is immediately followed by a detailing agent that improves edge definition and surface smoothness. The powder is then recoated and the cycle repeats until the full object is printed.
Key Components of MJF Printers:
- Array of HP thermal inkjet printheads
- Powder bed to hold nylon plastic powder
- IR lamps to preheat powder bed
- Roller to spread fresh powder layers
MJF printers exclusively use PA12 nylon powder material available in different grades with properties such as enhanced elasticity, strength-to-weight ratio, and more.
Benefits of MJF 3D Printing
High Productivity – Very fast print speeds allow mass production of end-use parts.
Excellent Mechanical Properties – Parts equal or exceed injection molded nylon with isotropic properties.
High Detail – Prints have good feature definition and surface finish right out of the printer.
Economies of Scale – MJF production costs reduce significantly with higher volumes.
Limitations of MJF Technology
Single Material – Currently limited to nylon plastic though composites are being developed.
Large Equipment – MJF printers have a substantial footprint and are heavy.
Post-Processing – Unfused powder must be cleaned off printed parts before use.
High Initial Cost – Industrial grade MJF 3D printers have considerable cost.
MJF Printer Models
HP currently has three MJF printer models:
- HP Jet Fusion 3200/4200 – For prototyping and short run manufacturing
- HP Jet Fusion 5200 series – Optimized for full scale manufacturing
- HP Metal Jet S100 – For volume production of metal parts
Applications of MJF 3D Printing
Mass Customization – Ideal for efficient lot sizes ranging from 10s to 1000s of identical parts.
Automotive – Used to manufacture jigs, fixtures, fluid system components, headlamps and more.
Consumer Goods – Mass produce end-use parts for electronics, footwear, housewares, sporting goods, etc.
Industrial Manufacturing – Print production line tooling like conveyor guards, assembly fixtures, jigs and factory floor equipment.
Binder Jetting Technology
Binder jet 3D printing uses liquid bonding agent selectively deposited to join powder particles. It enables fast, affordable printing of large metal or sand mold components for industrial use.
How Binder Jet Printing Works
The binder jetting process spreads a thin layer of powder on the build platform. An inkjet print head dispenses droplets of binder fluid in the areas that should solidify. The binder bonds the powder grains together forming the solid object layer by layer.
Key Components of a Binder Jet Printer:
- Print head – deposits binding fluid
- Powder bed – holds the raw material powder
- Roller – spreads fresh powder for each layer
- Curing oven – cures green parts after printing
Binder jetting can use any powder material including:
- Stainless steel powder – Most common for final metal parts
- Sand – For printing molds and cores
- Ceramics – To produce art sculptures and decor items
- Gypsum – For architectural ornamentation
Advantages of Binder Jet Printing
High Speed – Very fast print times independent of part complexity or quantity.
Low Waste – Unbound powder can be reused resulting in material savings.
Large Parts – Massive print volumes possible up to 1 cubic meter.
Material Flexibility – Wide range of metals, sand, ceramics and composites can be printed.
Limitations of Binder Jetting
Lower Resolution – Prints have a grainy surface finish due to liquid saturation limits.
Post-Processing – Sintering required to achieve full density and properties for metal parts.
Anisotropic – Mechanical properties vary depending on build orientation.
Dimensional Accuracy – Shrinkage of printed parts during sintering can affect precision.
Major Binder Jetting Printer Manufacturers
Companies making binder jet 3D printing systems include:
- ExOne
- Digital Metal
- DESCAM
- Voxeljet
- Desktop Metal
- GE Additive
Both industrial and office-friendly binder jetting printers are available.
Uses of Binder Jet 3D Printing
Metal Casting – Sand molds and cores printed for investment casting of complex metal objects.
Tooling – Lightweight, low-cost binder jet tooling for plastic injection molding.
Series Production – Stainless steel binder jetting for small batch manufacturing.
Architecture – Artists use to create intricate decorative stonework, ornaments and statues.
Education – Affordable way for schools to introduce metal 3D printing.
Material Jetting Technology
Material jetting is a 3D printing method that deposits tiny droplets of photopolymer material to build the object layer-by-layer. It facilitates multi-material printing and complex geometries unmatched by other technologies.
How Material Jetting Works
Material jetting print heads selectively deposit photopolymer material in droplets as small as one picoliter in volume. UV lamps instantly cure each layer as it is printed. The build platform lowers, allowing the next layer to be printed. Support structures are also printed using a removable gel.
Key Components of a Material Jet Printer:
- Print heads – piezoelectric injectors that jet material droplets
- UV lamps – instantly cure deposited material
- Material trays – hold the liquid photopolymers
- Software – controls material blending
Some common jetting materials include:
- Rigid plastic resins – For durable and detailed models
- Rubber-like resins – Flexible parts with elastic properties
- Transparent material – Clear models and optical components
- Wax, gel supports – Dissolve away after printing
Benefits of Material Jetting
Multi-Material – Ability to print different resins and gradients in a single part.
High Detail – Extremely smooth surface finish with thin 16-30 micron layers.
Diverse Material Properties – From rigid plastic to simulated polypropylene.
Complex Shapes – Can make enclosed voids and undercuts by printing support gel.
Drawbacks of Material Jetting
Small Build Size – Constrained to smaller models and parts, usually under 1 foot size.
Material Costs – Printing materials are very expensive compared to other 3D printing processes.
Moisture Sensitivity – Printed parts can degrade or warp when exposed to humidity.
Post-Processing – Support gels must be removed and parts require UV curing.
Leading Material Jetting System Manufacturers
Prominent companies that develop material jetting 3D printers include:
- Stratasys
- 3D Systems
- Xaar
- voxeljet
- EnvisionTEC
- DowDupont
The printers are designed for commercial and industrial use.
Applications of Material Jetting
Prototyping – Excellent for concept models requiring multi-material properties and fine details.
Manufacturing – Used to produce small batch runs of end-use parts, suits low-volume complex geometries.
Medical – Surgical guides, anatomical models with realistic textures are printed.
Dental – Multi-material jetting creates realistic prosthetics and orthodontic aligners.
Consumer – Personalized fashion accessories, phone cases, footwear are 3D printed.
Automotive – Makes detailed small plastic and rubber components like gaskets.
Aerospace – Lightweight non-structural parts with complex geometries printed.
How to Choose the Right 3D Printing Technology
With so many 3D printing types available, it can be confusing to determine the best method for an application. Here are some key criteria to guide the selection process:
Printing Objective – Prototype, visual concept model, functional testing part, end-use production? Different technologies suit different goals.
Part Size – Desktop printers have small build volumes. Consider industrial systems for larger components.
Part Geometry – Assess requirements for enclosed voids, undercuts, surface finish, dimensional precision.
Material Needs – Match material properties like strength, heat resistance, flexibility to the application.
Budget – Industrial 3D printers have higher equipment costs. Factor in operating costs like material expenses.
Speed and Throughput – Some technologies like MJF and binder jetting are much faster than others.
Post-Processing – Compare secondary labor and costs like support removal, surface finishing, powder recovery.
Technical Expertise – Simpler methods like FDM need less training than SLS or material jetting.
By evaluating the criteria above for a particular application, the list of suitable 3D printing technologies can be narrowed down significantly to choose the optimal method. Prototyping and mass production will require very different printers. Seeking expert guidance can further help make the right 3D printing technology selection.
Comparison of 3D Printing Methods
Here is a summary of the key differences between popular 3D printing technologies:
Parameter | FDM | SLA | SLS | MJF | Binder Jetting | Material Jetting |
---|---|---|---|---|---|---|
Raw material | Filament | Liquid resin | Powder | Powder | Powder | Liquid resin |
Accuracy | Medium | High | Medium | High | Medium | High |
Surface finish | Medium | High | Low | Medium | Low | High |
Max build size | Medium | Small | Large | Medium | Very large | Small |
Supported geometries | No | Yes | Yes | Yes | Yes | Yes |
Speed | Slow | Medium | Medium | Very fast | Very fast | Medium |
Part strength | Medium | Medium | High | High | Medium | Medium |
Materials available | Good | Fair | Excellent | Limited | Excellent | Good |
Post-processing | Minimal | Required | Required | Required | Required | Required |
Software complexity | Simple | Medium | Complex | Complex | Medium | Complex |
Equipment cost | $500-$100k | $3k-$250k | $100k-$1M | >$100k | >$100k | >$100k |
Material cost | Low | High | Medium | Medium | Medium | Very high |
This comparison chart summarizes the typical features, capabilities, and costs associated with the most common 3D printing technologies. It provides a quick guide to the trade-offs between different methods to inform the selection process for a particular application.
Pros and Cons of Key 3D Printing Methods
3D Printing Type | Advantages | Disadvantages |
---|---|---|
FDM | Inexpensive, good strength, variety of materials | Lower accuracy, weak inter-layer bonding, warping |
SLA | High accuracy, great surface finish, clear resins available | Small build volume, materials expensive, post-processing |
SLS | Functional strength parts, complex geometries supported | Grainy surface finish, large equipment, material costs |
MJF | Very high speed, excellent mechanical properties | Limited to nylons currently, high printer cost |
Binder Jetting | Fast printing, large build sizes, various materials | Lower resolution, post-processing, anisotropic properties |
Material Jetting | Multi-material ability, great details, diverse properties | Small build size, support removal required, high material costs |
Understanding the inherent advantages and limitations of each 3D printing process enables selection of the optimal technology based on application requirements. The pros and cons must be weighed carefully based on key criteria like part properties, accuracy, cost and speed.
3D Printing Material Options
3D printers employ a range of materials from plastics to metals to customized photopolymers. Here are some of the most common material options used across the different 3D printing processes:
Plastics
- ABS – Strong, durable, slightly flexible
- PLA – Tough, low warp, bio-derived polymer
- Nylon – Excellent strength, versatility, cost
- PETG – Clear, low odor, easier to print than ABS
- TPU – Flexible filament for rubber-like parts
Photopolymers
- Standard resins – Accurate with good mechanical properties
- Castable resins – Burn out cleanly for metal casting
- Durable resins – Withstand high temperature, toughness
- Dental SG resin – Biocompatible class 1 material
- Flexible resin – Elastic properties similar to polypropylene
Metals
- Stainless steel – Most common metal powder for high strength applications
- Aluminum – Lightweight but strong parts
- Titanium – Biocompatible with high corrosion resistance
- Nickel alloy – Hardness and heat resistance for tooling
- Precious metals – Silver, gold, suitable for jewelry
Ceramics
- Alumina – High hardness, heat and corrosion resistance
- Zirconia – Very high strength and fracture toughness
- Hydroxyapatite – Bioceramic used for bone implants
- Porcelain – For highly artistic sculptures and decorative artifacts
Composites
- Carbon fiber – Reinforced with carbon for very high strength
- Glow in the dark – PLA with phosphorescent additives
- Wood & metal filled – Hybrid materials like bronzefill, copperfill etc.
- Magnetic – Iron powder infused filament for magnetic components
With various materials available for different 3D printing technologies, the options can be matched precisely to the mechanical, thermal, electrical and aesthetic requirements of an application.
3D Printing Surface Finishes
The surface finish, texture and accuracy of a 3D printed part depends on several factors:
- 3D Printing Process – FDM, SLA, SLS etc. have varying resolutions
- Layer Height – Thinner layers provide a smoother surface
- Orientation – Parts can be printed vertically or diagonally
- Raster Angles – Alternating raster orientation between layers reduces visible stepping
- Post-Processing – Methods like sanding, grinding, coating improve finish
Here is a comparison of surface finishes attained with different 3D printing technologies:
3D Printing Method | Raw Material | Typical Layer Height | Surface Finish |
---|---|---|---|
FDM | Filament | 50 – 200 microns | Fair to medium |
SLA | Liquid resin | 25 – 100 microns | Excellent |
SLS | Powder | 50 – 150 microns | Medium to poor |
Binder jetting | Powder | 80 – 140 microns | Medium to poor |
Material jetting | Liquid resin | 16 – 30 microns | Excellent |
SLA and material jetting can attain the smoothest surfaces. FDM printing requires optimizing layer height, raster angles and finishing to improve surface quality.
Design Guidelines for 3D Printing
Consider these design principles when modeling parts for 3D printing:
- Optimize wall thickness to 1.2-2mm for adequate strength
- Include fillets and rounds to relieve stress concentrations
- Design snap fits, living hinges and flexible components with optimal clearances
- Minimize overhangs requiring support material as much as possible
- Orient part optimally on the build platform to reduce supports
- Allow for clearance in moving assemblies for post-processing steps
- Design tolerances according to printer and material capabilities
- Ensure enclosed voids have escape holes for powder removal in some processes
- Account for property changes due to layer orientation and build direction
Following DfAM (Design for Additive Manufacturing) principles enables creating 3D printable models tailored to the capabilities of the selected technology and materials.
Suppliers of 3D Printing Equipment
There are a vast number of vendors supplying professional 3D printing equipment including:
Desktop 3D Printers
- MakerBot, Ultimaker, Prusa Research, FlashForge, LulzBot, Formlabs
Industrial Plastic Printers
- Stratasys, 3D Systems, EOS, EnvisionTEC, Carbon
Metal 3D Printers
- EOS, Renishaw, Desktop Metal, Markforged, Xact Metal
Volume Production Systems
- HP, Carbon, Desktop Metal, Bound Metal
Specialized Printers
- Organovo (bioprinting), Nanoscribe (microscale), wholmen (large scale)
Printer Kits
- Creality, Artillery, Tronxy, Anycubic
Print Services
- Materialise, Sculpteo, Protolabs, Shapeways
When sourcing a suitable 3D printer, consider printer technology, build volume, materials, accuracy, software capabilities, manufacturer reputability, service plans, and operating costs.
Cost Considerations for 3D Printing
The costs of getting started with 3D printing depend on many factors:
Printer Cost
- Desktop FDM machines start under $300
- Professional industrial printers range from $5,000 to over $1,000,000
Materials
- 1 kg of PLA filament: $20-50
- 1 liter resin for SLA: $50-200
- Metal powders: $100-500 per kg
Software
- Free 3D modeling tools like Tinkercad or Fusion360
- Licensed CAD software costs $1000 – $7000
Post-Processing Equipment
- Printer consumables like filament, resin, nozzles
- Finishing tools for smoothing, painting, coating
- Industrial sintering ovens for metal powders
Technical Expertise
- Operator training and learning curve
- Professional engineering support
Thoroughly consider both initial equipment costs and ongoing operating expenses while adopting 3D printing for production applications. Leverage 3D printing service bureaus to avoid capital expenditure.
Choosing a 3D Printing Service Bureau
Here are some tips for selecting a 3D printing service provider:
- Review range of printing technologies supported that match application needs
- Look for materials expertise relevant to your projects
- Evaluate build volume capacities and production scalability
- Assess workforce skills and engineering support offered
- Consider speed, delivery times, and location
- Review quality certifications and sample parts for surface finish
- Compare pricing models: per part, volume discounts, subscription
- Check customer reviews and testimonials online
- Evaluate post-processing, finishing and coating capabilities
- Discuss ownership, data protection and confidentiality
- Understand order process, upload options, and lead times
- Consider high-touch services like design for AM, engineering expertise
Partnering with the right service bureau provides access to a variety of 3D printing capabilities without major capital investment.
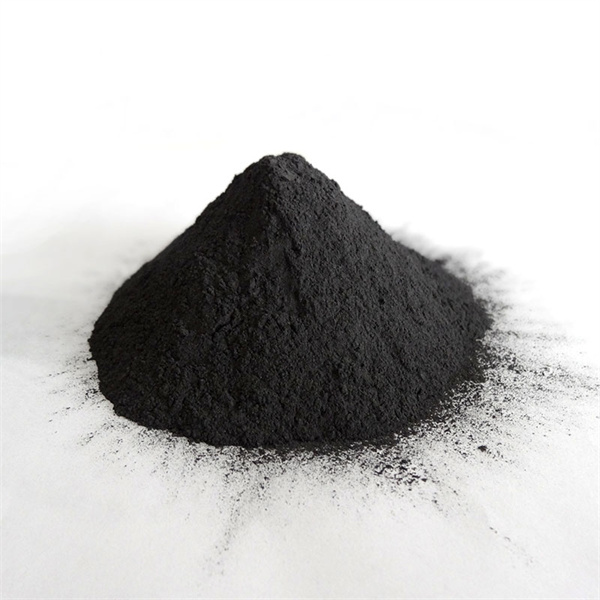
Future Outlook for 3D Printing
3D printing technology is projected to continue advancing rapidly:
- Declining costs and increased affordability of industrial 3D printers
- New material development widening applications – composites, bio-materials
- Improved surface finishes rivaling traditional manufacturing
- Hybrid manufacturing combining 3D printing with machining and other processes
- Automated post-processing and finishing solutions
- Software enhancements for design, process simulation and optimization
- Leveraging metal binder jetting and multi-laser metal PBF for mass production
- Increased part quality, precision, repeatability for end-use manufacturing
- Streamlined workflows and digital inventory for on-demand part production
- Growth of high-value specialty applications in medical, aerospace, defense
These innovations will expand 3D printing capabilities beyond rapid prototyping towards digital manufacturing across industrial sectors.
Conclusion
3D printing has evolved into a disruptive technology with far-reaching applications from prototyping to production. Understanding the working principles, capabilities, use-cases and economics of different 3D printing processes is crucial for effective adoption. With various technologies and material options now available combined with declining costs, 3D printing utilization will accelerate across diverse industries in the coming decade. Companies must actively evaluate how 3D printing can improve their product development cycles, supply chains and manufacturing operations to remain competitive. With advancements in speed, accuracy, repeatability, and part properties, 3D printing promises to be a strategic component of the future digital manufacturing landscape.