金属注射成型 (MIM) 是一种用于生产具有严格公差的小型复杂金属零件的制造工艺。MIM 结合了注塑成型的多功能性和机加工金属的强度和完整性。本文详细介绍了 MIM 技术、应用、设备、工艺、设计注意事项等。
金属注射成型概述
金属注射成型是一种粉末冶金工艺,可利用注射成型技术大批量生产小型精密金属部件。
MIM 如何工作
MIM 工艺是将精细金属粉末与粘合剂材料混合,制成可注入模具的原料。成型后的零件被称为 "绿色零件",然后进行烧结以去除粘合剂,并将金属粉末固结成固体结构。基本步骤如下
- 混合 - 细金属粉末与粘合剂混合,形成均匀的原料
- 注塑成型 - 原料熔化后注入模具,形成绿色部件
- 除胶 - 粘合剂通过溶剂、热力或催化脱胶去除
- 烧结 - 对去毛刺的部件进行烧结,使金属结构致密并得到强化
- 辅助业务 - 其他精加工步骤,如机加工、钻孔、攻丝等。
金属射出成型的优势
与其他制造技术相比,金属射出成型具有多种优势:
- 大批量生产,单件成本低
- 公差要求严格的复杂几何形状
- 各种材料,如不锈钢、钛、钨、钴铬等。
- 减少废料损失和材料浪费
- 近净成形加工减少机加工
- 小零件尺寸从 0.005 磅到 0.5 磅不等
- 通过组合组件实现部件整合
- 表面光滑,光洁度高
计量信息模型的局限性
金属注射成型的一些局限性包括
- 启动和工具成本高
- 零件尺寸范围有限
- 需要专用设备
- 多道工序,生产速度较慢
- 基于粉末特性的尺寸限制
- 根据粉末流动限制零件几何形状
金属射出成型的应用
金属射出成型技术被广泛用于制造公差要求严格的小型复杂零件,涉及的行业包括
- 医疗 - 整形外科植入物、牙科植入物、手术器械
- 汽车 - 发动机部件、阀门、齿轮
- 航空航天 - 涡轮叶片、叶轮、喷嘴
- 电子 - 连接器、微型齿轮、屏蔽
- 枪支 - 触发器、击锤、保险装置
- 手表 - 表壳、表链、表冠
- 工业 - 旋钮、紧固件、切割工具
在金属零件生产中,金属射出成型与熔模铸造、机械加工和冲压等其他工艺竞争。
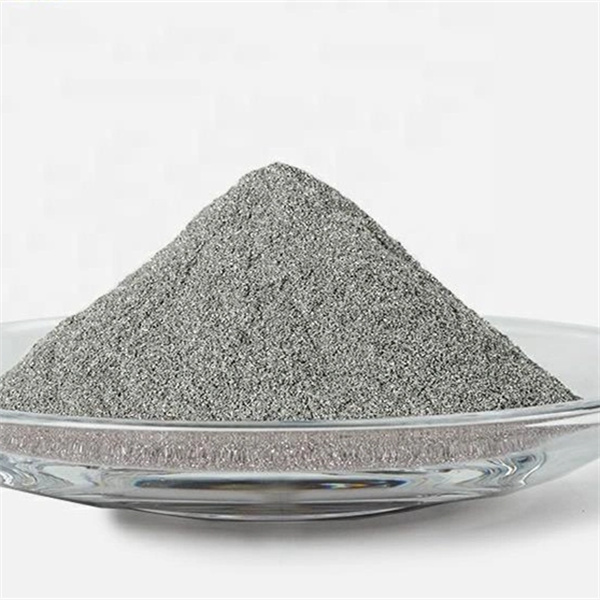
金属注射成型 设备指南
MIM 工艺的每个阶段都需要专用设备。以下是主要的 MIM 设备类型:
设备 | 功能 |
---|---|
粉末喂料机 | 精确测量细粉 |
搅拌机 | 均匀混合粉末和粘合剂 |
制粒机 | 将原料制成用于成型的颗粒 |
注塑机 | 将原料模塑成所需形状 |
脱脂炉 | 从模制件上去除粘合剂 |
烧结炉 | 致密和强化金属结构 |
磨床 | 拆除闸门、滑道和光滑表面 |
加工中心 | 钻孔、车削、铣削烧结部件的特征 |
先进的自动化、处理系统和控制装置用于整合流程,最大限度地提高生产率。必须根据材料、零件尺寸、产量和质量要求等因素精心选择设备。
金属注射成型工艺步骤
MIM 加工涉及多个步骤,将精细金属粉末转化为完全致密的最终使用部件。
步骤 1 - 混合
- 金属粉末和粘合剂在混合器中充分混合,形成均匀的原料
- 粉末粒度、形状和分布对成型性和烧结有影响
- 粘合剂可在注塑成型过程中提供流动性和粘附性
- 蜡、热塑性塑料(如 PP、PE、PVC)和用作粘合剂的聚合物
- 使用西格玛刀片、Z 型刀片、双行星搅拌器进行搅拌
步骤 2 - 制粒
- 将原料混合物粒化成小颗粒,用于注塑成型
- 改善物料流动性,防止料筒内物料偏析
- 制粒机使用旋转刀片将原料切割成均匀的颗粒
- 颗粒形状和大小会影响包装密度和成型性
步骤 3 - 注塑成型
- 原料颗粒被模压成所需的部件形状和尺寸
- 使用温度和压力可控的改良注塑机
- 优化成型参数以尽量减少缺陷非常重要
- 被称为 "绿色部件 "的模塑部件具有形状,但没有强度
步骤 4 - 脱胶
- 通过溶剂、热或催化方法从绿色部件中提取粘合剂
- 溶剂脱胶利用毛细作用溶解粘合剂
- 热力脱胶在熔炉中分解粘合剂
- 催化脱胶利用催化剂加速粘合剂的去除
- 脱脂后的棕色部件具有多孔的金属颗粒结构
步骤 5 - 烧结
- 棕色部件在受控气氛炉中烧结
- 金属颗粒之间的结合是通过扩散和质量传输形成的
- 烧结过程中可达到接近全密度的 96-99%
- 优化气氛、温度和时间,避免出现缺陷
- 在成型过程中考虑烧结收缩率
步骤 6 - 二级操作
- 退火、机加工、钻孔、电镀等其他金属加工步骤
- 退火可消除烧结产生的内应力
- 数控加工去除浇口,平滑表面,增加功能
- 电镀和喷漆用于增强或防腐蚀保护
MIM 工艺结合了注塑成型和粉末冶金的优点,可制造复杂、高精度的金属零件。
MIM 零件的设计考虑因素
MIM 可实现机械加工无法实现的几何自由度,但需要考虑某些设计因素:
- 壁厚 - 典型范围为 0.3 - 4.0 毫米,某些粉末的壁厚可达 6 毫米
- 表面处理 - 光洁度比铸造更光滑,但不如机加工精细;对于 MIM 而言,Ra 值一般为 1 - 4 μm
- 尺寸公差 - 根据零件几何形状,可达到 ±0.1% 至 ±0.5% 的微米级精度
- 密度 - 通过优化烧结工艺,可实现高达 99% 的全密度
- 几何学 - 避免粉末滞留并允许粘结剂逸出至关重要
- 草稿角度 - 具有 1-3° 拔模角的锥形壁,便于工件排出
- 半径和圆角 - 渐进式过渡优于急转弯
- 孔和洞 - 通孔的最小直径为 0.25 - 0.5 毫米
- 线程 - 可以成型,但通常在烧结后进行机加工,以提高精度
- 表面细节 - 限制精细细节,以减少模具磨损;成型后工艺可增强
MIM 设计应注重几何形状,以最大限度地提高性能,而不是简化制造。该工艺可将多部件组装成一个部件,大大降低成本和重量。
金属注射成型中使用的材料
金属射出成型可以用各种金属、合金和陶瓷生产零件,适用于各种行业。
材料 | 应用 | 属性 |
---|---|---|
不锈钢 | 医疗、枪械、海事 | 耐腐蚀性、强度 |
低合金钢 | 汽车、工业 | 磁响应、机加工性能 |
软磁合金 | 传感器、执行器 | 高渗透性 |
硬金属合金 | 切割工具 | 耐磨性、硬度 |
铜合金 | 电子、热敏 | 导电性 |
铝合金 | 电、热 | 轻便、导电 |
钛合金 | 航空航天、汽车 | 强度、生物相容性 |
钨合金 | 辐射屏蔽 | 高密度 |
金属陶瓷 | 电子、光学 | 抗氧化性 |
零件功能、成本、后处理步骤和合金兼容性等因素决定了理想的 MIM 材料选择。
MIM 供应商和设备制造商
全球有许多公司提供 MIM 材料、服务、生产和设备。以下是整个价值链中的一些主要 MIM 供应商:
公司名称 | 产品/服务 |
---|---|
巴斯夫 | 原料、粘合剂 |
山特维克鹗 | 金属粉末 |
赫加纳斯 | 金属粉末 |
中石油粉末 | 金属粉末 |
印度米姆 | MIM 产品和服务 |
MPP | MIM 产品和服务 |
ARC 集团 | MIM 产品和服务 |
阿特拉斯冲压金属公司 | MIM 零件生产 |
爱普生 Atmix | MIM 设备 |
Milacron | 注塑机 |
Elnik | 烧结炉 |
TCN | 脱脂、烧结炉 |
在整个 MIM 供应链中,还有许多较小的地区性参与者。希望采用 MIM 的最终用户可以根据所需的能力,与材料供应商和合同制造商合作。
MIM 零件与替代品的成本分析
以下是使用不同制造工艺生产 1000 个零件的估计成本比较:
过程 | 设置成本 | 机器成本 | 模具成本 | 部分费用 | 总计(1000 份) |
---|---|---|---|---|---|
数控加工 | 低 | $100,000 | $2,000 | $50 | $52,000 |
熔模铸造 | 高 | $500,000 | $40,000 | $20 | $60,000 |
金属注射成型 | 高 | $750,000 | $100,000 | $15 | $115,000 |
冲压 | 高 | $1,000,000 | $150,000 | $10 | $160,000 |
- 数控加工产量低、零件成本高、复杂性有限
- 熔模铸造更适合 10,000 件以下的产量
- MIM 对于具有复杂几何形状的中大批量产品具有优势
- 冲压的模具成本非常高,但在超过 10 万个零件的大批量生产中,零件价格最低
MIM 比其他工艺更经济的交叉点取决于产量、复杂性和尺寸。
选择 MIM 供应商或合作伙伴
选择有能力的 MIM 供应商或生产合作伙伴对于经济高效地生产零件至关重要。以下是主要考虑因素:
- 技术专长 - 具有类似 MIM 零件、材料和行业的经验
- 质量体系 - ISO 9001 认证、质量控制实践
- 生产能力 - 满足当前和未来产量需求的能力
- 二次加工 - 加工、冲压、电镀、喷漆能力
- 部分优化 - 设计支持 MIM,实现效益最大化
- 原型设计 - 验证设计的快速原型服务
- 工具能力 - 优先考虑内部模具设计和制造
- 原材料的获取 - 建立原料供应渠道
- 研发能力 - 不断研发先进材料和制造技术
- 以客户为中心 - 响应需求与合作方法
- 成本结构 - 定价模式和预测产量的竞争力
- 物流 - 能够可靠地交付零件,同时满足交货时间要求
优先考虑这些因素将有助于为特定应用确定合适的战略 MIM 合作伙伴。
安装 MIM 设备
对于在内部安装 MIM 功能的公司来说,正确的设备安装至关重要。以下是主要考虑因素:
- MIM 生产线需要约 2000 - 5000 平方英尺的占地面积
- 需要 200-600 千伏安容量的稳定电源
- 额定压力为 100 psi 的压缩空气管路
- 热量、废气和粉尘的排气通风
- 氮气、工艺用水和气体供应等公用设施
- 温度和湿度控制在 20±3 °C、50±20% 左右
- 夹层、安装辅助设备的平台
- 物料搬运系统,如升降机、叉车、料仓
- 控制室,用于监控的计算机系统
- 对员工进行工艺安全和设备操作培训
- 流程模拟、试运行以验证安装
- 校准和预防性维护计划
充足的空间、公用设施和受控条件对 MIM 设备的顺利运行至关重要。彻底的测试和培训可为实际生产做好准备。
MIM 设备维护
坚持不懈的维护可改善 MIM 生产设备的正常运行时间和性能。关键方面:
- 记录每台机器的预防性维护计划
- 每天清理材料溢出、泄漏、灰尘和碎屑
- 检查油液水平、泄漏、异常噪音和振动
- 监测压力、温度和功耗
- 测试加热、冷却和控制系统
- 更换筛网、螺钉、机筒等易损件
- 检查部件疲劳、损坏和对齐情况
- 根据运行时间进行定期更换和大修
- 跟踪分析维护日志
- 储存关键部件的备件库存
- 设备正确操作和安全培训
- 设备供应商提供及时的服务和支持
训练有素的员工和与设备供应商的合作有助于最大限度地提高 MIM 设备的生产率,同时最大限度地减少停机时间。
金属注射成型模拟软件
模拟软件用于在实际生产前对 MIM 工艺进行数字化建模。其优点包括
- 预测充模模式和优化浇口位置
- 识别焊缝和空气疏水阀,防止出现缺陷
- 研究复杂几何形状中的热梯度和凝固现象
- 模拟排胶和烧结曲线对最终形状的影响
- 在制造前验证模具设计
- 通过虚拟原型减少试验成本
- 通过视觉演示培训人员
一些商用 MIM 仿真软件包包括
- MIMSIM - 通过烧结成型的集成模拟
- Sigma Soft - 模具填充和变形的 3D FEM 分析
- Netzsch MIMPre - 模拟 MIM 原料的流变特性
- Simufact 添加剂 - AM 工艺的多物理场模拟
- EOS PSW - 以烧结和热处理为重点的模拟
使用 MIM 软件可提高工艺一致性、优化零件质量并降低物理原型成本。从模拟到生产的集成工作流程是首选。
常见 MIM 缺陷的故障排除
MIM 零件中的一些典型缺陷和潜在的根本原因是
缺陷 | 原因 |
---|---|
短枪 | 注塑压力低,过早凝固 |
闪光灯 | 过度包装的模具、模具损坏 |
翘曲 | 冷却不均匀、粘合剂问题 |
裂缝 | 烧结速度快,粘合剂含量高 |
孔隙率 | 均质化不良,气体滞留 |
污染 | 交叉污染、炉内气氛 |
尺寸变化 | 原料问题、模具磨损、收缩 |
表面缺陷 | 气体孔隙率、液态金属脆化 |
内含物 | 原材料污染、喷嘴堵塞 |
应采用系统的缺陷分析方法来隔离造成缺陷的工艺参数,并采取纠正措施,如调整原料配方、成型参数、脱模和烧结曲线。
金属射出成型技术的优势
与其他金属零件生产方法相比,金属射出成型具有明显的优势:
- 复杂性 - 可实现复杂的三维几何形状,合并组件
- 一致性 - 工艺重复性高,部件差异小
- 效率 - 接近净形制造,减少原材料浪费
- 自动化 - 高度自动化的流程减少了劳动力
- 灵活性 - 金属、陶瓷、复合材料等多种材料
- 质量 - 良好的表面光洁度和机械性能
- 生产率 - 产量高,单件成本低
- 微型化 - 微型元件的细节可达 10 μm
- 可持续性 - 与机械加工相比更节能
- 费用 - 降低中高产能的总成本
MIM 的独特功能推动了汽车、航空航天、医疗和电子等不同行业的应用。
金属注射成型的局限性
尽管 MIM 有很多优点,但也有一定的局限性:
- 初始模具投资高
- 尺寸范围有限,通常在 65 克以下
- 精度低于 CNC 加工
- 需要工艺控制的多孔性风险
- 根据粉末特性限制材料选择
- 细粉的安全隐患
- 与成型性相关的零件几何形状限制
- 地块与地块之间的潜在差异
- 机械性能低于锻造材料
- 少量生产原型
- 在许多应用中需要进行二次加工
- 需要专业设备和训练有素的操作人员
对于高精度或小批量生产的大型金属零件,其他工艺可能比 MIM 更合适。
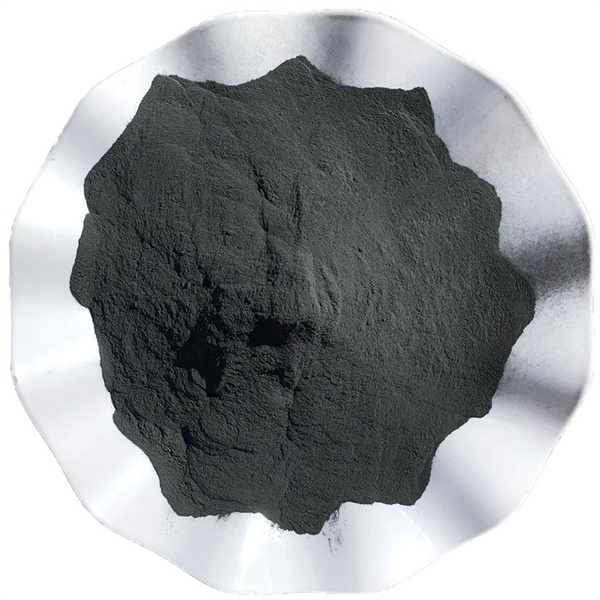
金属注射成型的未来
随着技术和材料的不断改进,预计金属射出成型技术将持续强劲增长:
- 新型粘合剂系统可提高成型性和绿色强度
- 使用纳米复合材料的新型原料配方
- 超过电流限制的大型部件
- 更多采用陶瓷和钨合金
- 医疗和电子领域需求增长强劲
- 利用增材制造技术制造 MIM 模具
- 利用机器人技术和工业 4.0 整合实现自动化
- 在极端环境中的更多应用
- 利用绑定金属沉积技术实现与金属 3D 打印的融合
随着研发的增加和应用的普及,未来几年 MIM 在各种应用领域的使用将迅速增长。