雾化金属粉末概述
雾化金属粉末工业 是金属 3D 打印、热喷涂、金属注射成型、钎焊和焊接等工业应用的重要原材料。
雾化金属粉末的主要特性:
特征 | 说明 |
---|---|
生产方法 | 气体或水雾化产生细小液滴 |
材料 | 铝、钛、镍、钴、不锈钢合金 |
粒子形状 | 球形或不规则形态 |
颗粒大小 | 从 10 微米到 150+ 微米 |
尺寸分布 | 严格控制粒度范围 |
通过对粉末特性的精确控制,可以在成分、尺寸、形状和质量方面满足特定的应用要求。
雾化金属粉末的应用
雾化金属粉末的主要应用包括
应用 | 使用的典型材料 |
---|---|
快速成型制造 | 钛、铝、镍、不锈钢、钴合金 |
金属注射成型 | 不锈钢、钛钢、合金钢 |
热喷涂 | 铜、铝、镍、不锈钢 |
钎焊和软焊 | 铜、银、镍合金 |
焊接 | 铝合金、不锈钢、镍合金 |
雾化技术可实现球形形态和严格的尺寸控制,使粉末成为这些工艺的理想选择。
通过对雾化工艺参数和条件的精心控制,可定制流动性、表观密度和纯度等专用特性,以满足各种应用的要求。
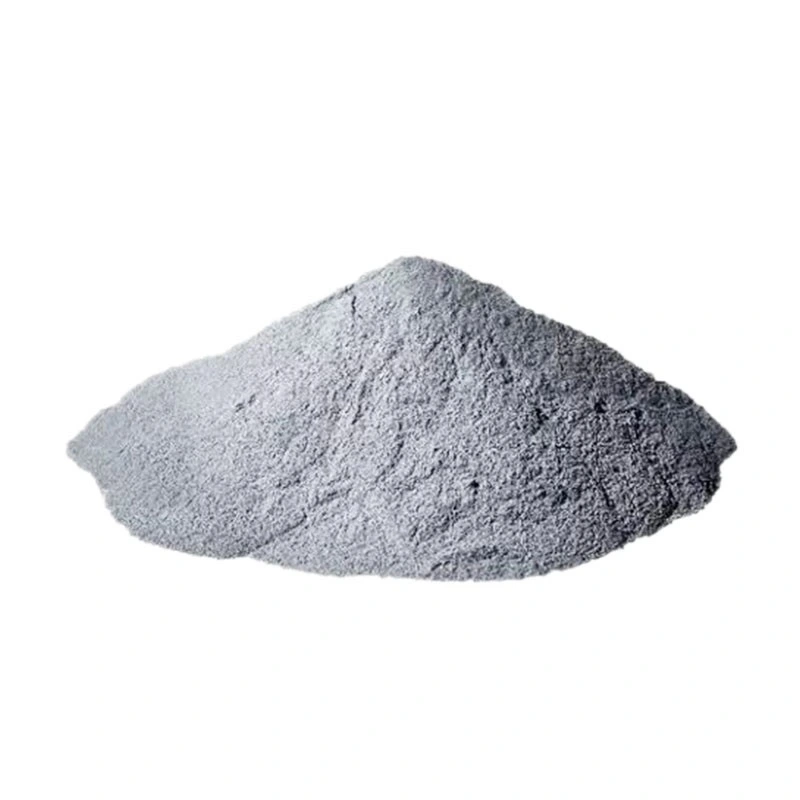
雾化金属粉末的生产方法
生产雾化金属粉末的主要方法有
方法 | 说明 |
---|---|
气体雾化 | 熔化的金属在高压气体喷射下分解成细小的液滴。 |
水雾化 | 熔融金属流被高速水流击碎成液滴。 |
旋转电极 | 离心力将熔融金属从旋转的电极上分散开来。 |
等离子雾化 | 等离子弧将金属丝原料熔化成超细粉末。 |
每种方法都能生产出具有独特特性的粉末,适合不同的应用。气体雾化是工业上应用最广泛的工艺。
雾化金属粉末工业 生产流程
典型的气体雾化金属粉末生产工艺包括
- 原材料制备 - 钢锭熔化和合金化
- 雾化 - 将金属分解成粉末
- 粉末收集 - 与雾化气体分离
- 筛分 - 将粉末按粒度分级
- 调节 - 流动添加剂、干燥、混合
- 质量控制 - 按照规格取样和测试
- 包装 - 用于装运的罐、瓶、桶
每个步骤都经过精心的过程控制,确保粉末质量和特性的可重复性。该工艺采用自动化的工业规模设备。
气体雾化器的设计和运行
气体雾化器采用以下关键设计元素:
组件 | 功能 |
---|---|
压力容器 | 在高压下保持惰性气体 |
喷嘴 | 将加压气体加速到超音速 |
熔体浇注系统 | 将熔融金属流送入雾化区 |
旋风分离器和过滤器 | 将粉末与气流分离 |
控制系统 | 监控和调节工艺参数 |
在运行过程中,金属熔体被倒入高速惰性气体喷嘴中,然后被分解成细小的粉末。粉末特性由气体压力、喷嘴设计、浇注速度和熔体过热度等参数控制。
雾化金属粉末的主要质量特性
雾化粉末的重要质量属性:
属性 | 说明 |
---|---|
粒度范围 | 以关键尺寸为重点的受控分配 |
形态学 | 球形/圆形优于不规则形状 |
化学成分 | 严格控制每批产品中的合金元素 |
表观密度 | 更高的密度可提高产品性能 |
杂质 | 尽量减少气体拾取(如氧气) |
流量特性 | 粉末流动顺畅,无结块 |
要满足应用规格要求,就必须严格控制和监控每个生产步骤的质量。
气体雾化工艺放大的注意事项
扩大气体雾化生产规模的关键因素:
- 大批量生产会增加熔体库存需求
- 在较高流量下保持稳定的熔流至关重要
- 必须考虑到天然气使用量的增加
- 更大的筛分系统可筛分更多粉末
- 扩大材料处理和存储区域
- 升级控制系统和数据采集
- 大型设备的人员培训
大规模生产的好处包括提高生产率、灵活性和规模经济。
AM 中金属粉末的规格
用于增材制造应用的典型粉末规格:
参数 | 要求 |
---|---|
颗粒大小 | 10-45 微米常见 |
形态学 | 球形,表面光滑 |
组成 | 严格控制合金元素 |
表观密度 | > 所需的 4 克/立方厘米 |
流动性 | 流动性极佳,无结块 |
杂质 | 尽量减少氧气 |
要满足 AM 粉末的性能要求,就必须在雾化过程中严格控制成分、尺寸和形态。
粉末表征方法
分析雾化金属粉末的重要方法:
方法 | 提供数据 |
---|---|
筛分 | 粒径分布 |
霍尔流量计 | 粉末流速 |
光学显微镜 | 形态和微观结构 |
扫描电子显微镜成像 | 高倍放大形态 |
表观密度 | 粉末的包装密度 |
化学分析 | 元素的构成 |
测试数据有助于将粉末特性与下游应用中的性能联系起来。
全球金属粉末市场规模
全球金属粉末市场规模:
- 2020 年估值为 $29 亿美元
- 预计到 2028 年将达到 $57 亿美元
- 年复合增长率约为 10%
主要增长动力:
系数 | 对增长的影响 |
---|---|
快速成型制造 | 金属 AM 粉末需求快速增长 |
轻量化趋势 | 更多使用轻合金粉末 |
高性能部件 | 粉末可制成高级合金部件 |
电动汽车 | 为电机/电池开发的新型粉末 |
随着粉末在各行各业实现先进制造技术,预计市场将持续强劲增长。
金属粉末生产的经济效益
金属粉末生产的经济影响:
- 利用金属原料生产高价值的先进材料
- 创造专业、高薪的制造业工作岗位
- 金属粉末从生产地区出口到全球各地
- 支持下游制造技术和产品
- 生产设施需要大量资本投资
- 需求增长增加了经济活动和投资
该行业对整个供应链和制造业产生上游和下游影响。
金属粉末生产的主要地区
全球主要金属粉末生产地区:
地区 | 关键细节 |
---|---|
北美 | 美国是全球最大的生产国,大量出口海外 |
欧洲 | 德国、瑞典和英国的主要生产商为欧洲工业提供服务 |
亚太地区 | 中国、印度和韩国是以国内使用为主的主要生产国 |
中东 | 航空航天和石油/天然气行业带动产量增长 |
靠近最终用途行业和高内需推动了本地化增长。出口也服务于全球地区。
金属粉末行业增长的驱动因素
刺激金属粉末行业增长的主要驱动力:
司机 | 增长效应 |
---|---|
快速成型制造 | 专用 AM 金属粉末需求激增 |
轻量化 | 用粉末替代固体金属 |
高强度合金 | 用于制造坚固轻质部件的新型粉末合金 |
电动汽车 | 粉末马达、电池 |
航空航天 | 用于发动机和机身的粉末部件 |
这些技术趋势正在刺激金属粉末生产能力的投资和扩张。
金属粉末行业面临的挑战
金属粉末行业面临的主要挑战:
挑战 | 效果 |
---|---|
资本成本高 | 限制新进入者和投资 |
原材料价格 | 原料价格波动影响成本 |
质量要求 | 测试和过程控制费用 |
安全规定 | 爆炸风险导致合规成本增加 |
合并 | 收购减少竞争 |
尽管市场需求旺盛,但这些因素使增长和可持续发展面临挑战。企业必须创新才能保持竞争力。
金属粉末生产的技术趋势
金属粉末制造的新兴技术趋势:
- 雾化设备组件的快速成型制造实现设计灵活性
- 利用功率超声波辅助雾化技术制造更细的粉末
- 流体动力学和粉末形成的高级建模
- 通过传感器提高自动化和流程监控水平
- 预测性质量控制的机器学习
- 在闭环增材制造中直接重复使用粉末
- 用于微纳粉末生产的新型气体雾化方法
- 为新兴应用开发专用合金
技术创新将提高粉末质量和一致性,以更高的产量满足不断加速的市场增长。
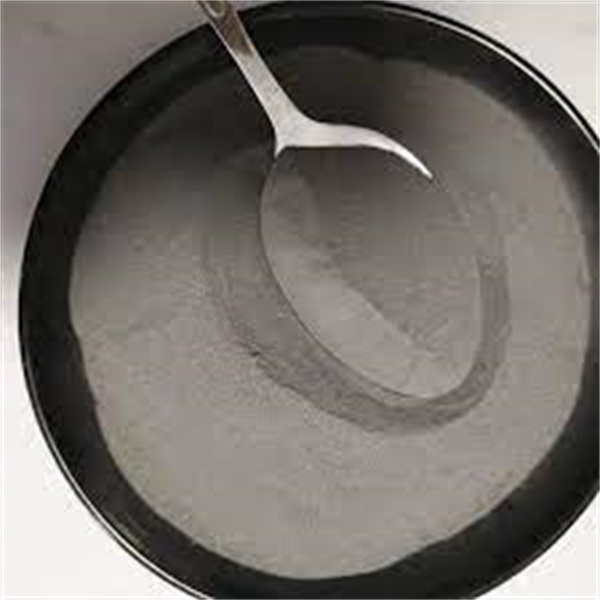
金属粉末行业概况
- 主要制造行业的重要粉末供应商
- 气体雾化是主要的生产技术
- 高性能合金推动需求快速增长
- 进入门槛高,但未来前景广阔
- 质量控制和先进加工的关键能力
- 与金属增材制造同时发展
- 拥有地区生产中心的高薪制造业
- 为继续扩张和技术开发做好准备
雾化金属粉末作为关键行业先进金属部件生产的战略材料,其经济重要性将与日俱增。
常见问题
问题 | 回答 |
---|---|
全球最大的金属粉末市场是哪里? | 北美洲,其次是欧洲和亚太地区。 |
金属粉末的主要工业应用是什么? | 增材制造、热喷涂、金属注射成型是最大的应用领域。 |
哪些合金通常被雾化成粉末? | 铝、钛、不锈钢、镍和钴合金最为常见。 |
气体雾化有什么用途? | 气体雾化是商业化生产金属粉末的主要方法。 |
如何按尺寸分离金属粉末? | 筛分/筛选用于将粉末分为特定的粒度范围。 |