金属粉末雾化 是一种用于生产具有精确粒度和分布的精细金属粉末的工艺。本指南全面介绍了金属粉末雾化设备,包括类型、特点、应用、规格、供应商、安装、操作、维护等。
金属粉末雾化设备概述
金属粉末雾化是将熔融金属流分解成细小的液滴,然后凝固成粉末颗粒。专用雾化设备用于雾化金属并控制粉末特性。
雾化器的主要类型包括
雾化器类型 | 说明 |
---|---|
气体雾化器 | 使用高速惰性气体喷射器打散金属流 |
喷雾器 | 使用喷水装置雾化熔融金属 |
离心雾化器 | 使用旋转盘/转轮甩出金属水滴 |
超声波雾化器 | 使用超声波振动干扰金属流 |
雾化可对粉末的粒度、形状、化学性质、微观结构和粒度分布进行广泛控制。可对工艺参数进行定制,以生产出最适合特定应用的粉末。
金属粉末雾化的主要应用包括
金属粉末雾化的应用 |
---|
快速成型制造粉末 |
金属注塑粉末 |
热喷涂涂层 |
粉末冶金 |
钎焊合金 |
表面涂层 |
催化剂 |
化工/石油工业 |
电子材料 |
磁性材料 |
金属粉末雾化器设备规格
金属粉末雾化器是为连续低成本生产粉末而设计的复杂工程系统。主要设计规格包括
雾化器设备规格 | 详细信息 |
---|---|
雾化法 | 气体、水、离心、超声波 |
处理的金属类型 | 黑色金属和有色金属;合金 |
金属进给速度 | 高达 2000 公斤/小时 |
气体流速 | 在 10-15 巴压力下,最高可达 100,000 立方米/小时 |
喷嘴设计 | 多喷嘴;流量/压力优化 |
圆盘直径 | 离心雾化器最大 500 毫米 |
频率 | 超声波雾化器的频率范围为 20-60 千赫 |
控制装置 | 带数据监控的 PLC/计算机控制 |
冷却 | 水冷/风冷组件 |
环境系统 | 排烟;气体净化 |
自动化水平 | 手动到全自动选项 |
合规性 | ATEX 和 CE 指令;质量标准 |
雾化器腔体由高级钢材制成,可承受高温和金属飞溅。气体喷嘴和旋转盘等关键部件由特殊合金制成,具有很高的耐用性。集成冷却、安全联锁和排烟装置最大程度地减少了对环境的影响。
先进的控制装置可优化工艺参数,如气体流量、金属流速、圆盘速度、喷嘴配置等,以实现所需的粉末特性。系统可与金属熔化、粉末分离和收集装置集成,实现自动化粉末生产。
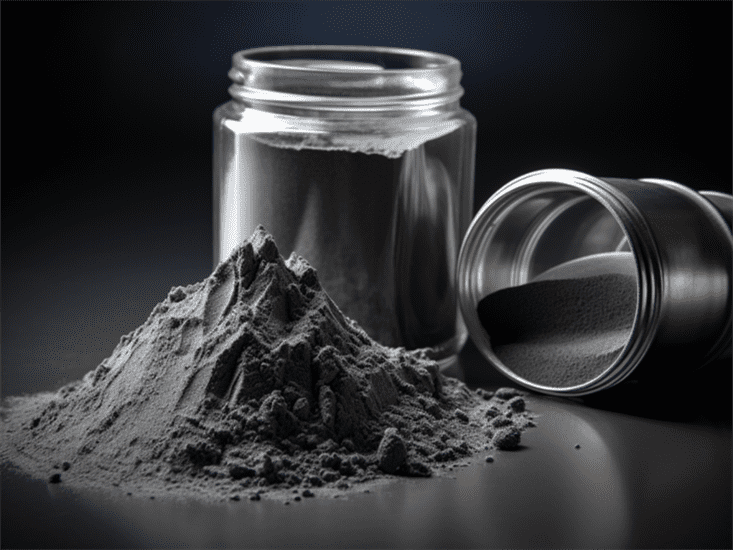
金属粉末雾化系统供应商
有许多全球领先的供应商生产气体、水、离心和超声波雾化系统:
雾化器供应商 | 地点 |
---|---|
AP&C | 加拿大 |
ALD 真空技术 | 德国 |
PSI 有限公司 | 英国 |
COPROD | 法国 |
制作金属粉末 | 英国 |
必和必拓 | 澳大利亚 |
供应商提供标准型号以及根据特定金属类型和粉末要求定制的雾化器。二手和翻新雾化器的价格也比新设备低 30-50%。
雾化器的价格因容量、自动化程度和附加处理单元的不同而有很大差异。新系统的指示性成本如下
雾化器类型 | 容量 | 价格范围 |
---|---|---|
气体雾化器 | 50 - 1000 公斤/小时 | $500,000 – $5,000,000 |
喷雾器 | 50 - 500 公斤/小时 | $200,000 – $2,000,000 |
离心雾化器 | 10 - 200 公斤/小时 | $100,000 – $1,000,000 |
超声波雾化器 | 1 - 50 公斤/小时 | $50,000 – $500,000 |
金属粉末雾化器的安装和操作
必须遵循正确的安装和操作程序,以实现金属雾化器的设计生产率和粉末质量:
- 雾化器需要专用的地基和服务,包括压缩空气、冷却水和通风管道。该区域必须受气候控制,并且没有气流。
- 根据容量确认公用设施要求--电力、惰性气体、排气系统。对安全联锁进行测试。
- 进行试运行并微调工艺参数,以优化粉末生产和特性。
- 运行期间,所有工艺指标和数据都通过控制系统进行监控。进料速度、气体参数和温度均按照配方进行控制。
- 如果任何参数偏离范围,系统将安全关闭。关闭电源和公用设施。
- 使用旋风分离器、袋式过滤器、洗涤器等设备从气流中分离后,收集产品粉末。定期抽样检测验证粉末质量。
- 按照计划进行的预防性维护包括检查、更换磨损部件和大修。这样可以最大限度地减少计划外停机时间。
维护和安全方面
日常维护对于最大限度地延长正常运行时间和提高安全性至关重要:
- 目视检查是否有泄漏、损坏和磨损
- 更换过滤器、垫圈等消耗品
- 测试联锁和安全装置
- 润滑运动部件
- 检查转子、喷嘴和圆盘的状况
- 检查冷却、通风等公用设施
- 校准仪器
- 审查数据日志和趋势
金属粉末雾化器的安全考虑因素:
- 高压电子设备需要隔离和屏障
- 惰性气体保护,防止氧化或火灾
- 避免水接触熔融金属(蒸汽爆炸风险)
- 排烟装置可最大限度地减少接触
- 人员需要防护装备和培训
- 屏蔽运动部件;门上的联锁装置
- 紧急停止按钮和电源隔离
如何选择金属粉末雾化器
选择金属粉末雾化系统时需要考虑的关键因素有
雾化器选择标准 | 详细信息 |
---|---|
生产能力 | 所需金属粉末产量(公斤/小时 |
目标粉末规格 | 粒度范围、形态、纯度等。 |
金属类型 | 与黑色金属和有色金属等的兼容性 |
费用 | 设备成本、每公斤运行成本 |
空间要求 | 系统占地面积;高度限制 |
支持 | 安装支持、培训、维护 |
选项 | 额外的处理、分离和收集装置 |
控制功能 | 监测、数据跟踪和自动化水平 |
认证 | 安全、电气、压力容器规范 |
交货时间 | 交货、安装和调试所需时间 |
雾化器技术--气体、水、离心或超声--是根据材料、容量、粉末规格和预算来选择的。全球领先的供应商拥有专业的工程技术知识,可针对应用推荐最佳的雾化器配置。
金属粉末雾化器的优势和局限性
雾化器系统的一些主要优点和局限性如下:
优势
- 连续大规模生产精细金属粉末
- 控制粒度分布
- 雾化活性/高熔点合金的能力
- 自动化粉末生产降低成本
- 综合粉末处理和收集
- 参数监测和数据跟踪
局限性
- 设备和运营成本高
- 需要专门操作和维护的复杂系统
- 大型单元的尺寸和占地面积限制
- 对原料形状和质量的限制
- 高压气体、水和活动部件的安全注意事项
- 需要额外的下游加工,以达到最终粉末规格
虽然雾化器可实现卓越的粉末生产,但其工艺和设备的复杂性需要专家设计和工程支持。
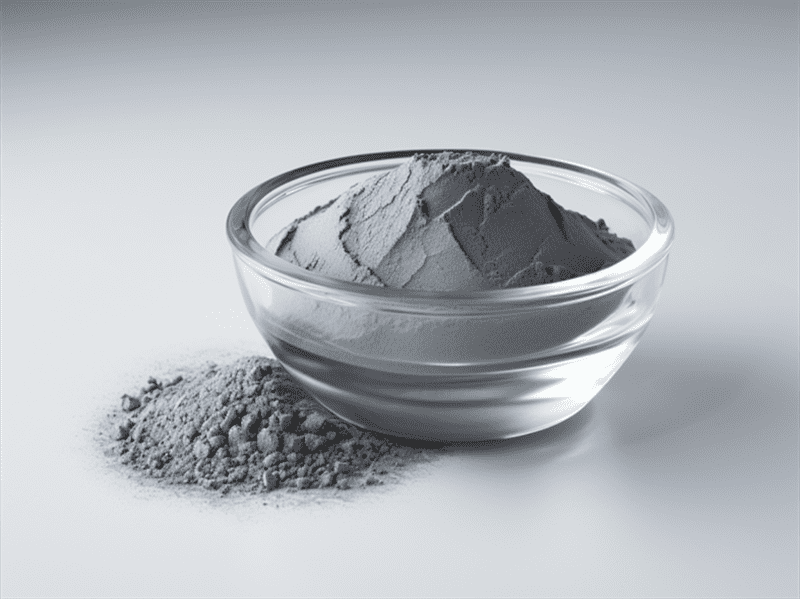
常见问题
下面是一些有关金属粉末雾化器的常见问题:
问:雾化技术可实现的粒度范围有多大?
答:雾化器可生产 1 微米至 250 微米的粉末,具体取决于所使用的技术和工艺参数。气体雾化器和离心雾化器可以生产 20 微米以下的细粉。
问:雾化后如何收集粉末?
答:气体中夹带的雾化粉末使用旋风分离器、袋式除尘器、湿式洗涤器等进行分离。铁粉可使用磁力分离。如有必要,还可对粉末进行筛分,以缩小粒度分布。
问:金属粉末雾化器需要采取哪些安全措施?
答:主要的安全措施包括联锁、紧急停止、通风、防爆电气、惰性气体保护、操作人员的防护装备等。水雾化器也需要采取措施防止蒸汽爆炸。
问:金属粉末雾化器需要多久维护一次?
答:预防性维护根据运行时间每周、每月、每季度进行安排。这包括更换过滤器等消耗品、测试联锁装置、检查部件磨损情况、检修旋转部件等。
问:任何金属合金都可以雾化成粉末吗?
答:大多数钢、铝、铜、镍钛等商用合金都可以雾化。难熔金属可能需要特殊的雾化器配置。为防止粉末偏析,可进行有限的合金化处理。
问:可以使用哪些类型的原材料--铸锭、液态金属?
答:不同的雾化器接受不同的进料--从液态金属浇注、连续铸造到固体线材/棒材进料。进料必须符合雾化所需的化学、纯度和质量标准。
问:金属粉末雾化器的运行成本是多少?
答:主要成本是公用事业费--电、惰性气体、冷却水。消耗品和维护也很重要。根据产能、复杂程度和人工情况,指示性运营成本为 $15-50/公斤粉末。
结论
金属粉末雾化技术可大批量生产各种金属和合金的细粉和稳定的粉末。随着粉末冶金技术的发展,雾化器已成为经济高效地生产粉末不可或缺的设备。
然而,该工艺涉及在高强度下运行的复杂工程系统。本指南总结了雾化器类型、选择标准、规格、安装和操作程序等关键因素,用户必须考虑这些因素,才能安全可靠地进行金属粉末雾化。