MIM 快速成型制造 是指一种大批量生产小型复杂金属零件的工业流程。使用注塑成型设备将复合金属粉末原料成型为绿色状态的形状,然后进行去骨,最后烧结以达到完全的密度。
MIM 充分利用了聚合物注塑成型和绿色成型的几何灵活性以及金属合金的性能。随着增材制造工艺的不断扩展,本指南涵盖了 MIM 的成分、特性、应用、规格、工艺流程、供应商、权衡和常见问题。
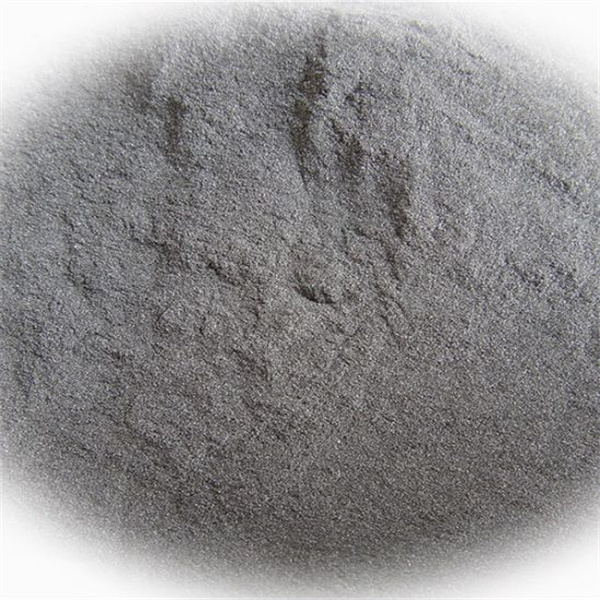
MIM 合金的成分
许多成分都可用作 MIM 原料:
材料 | 普通合金 | 概述 |
---|---|---|
不锈钢 | 316L、17-4PH、420 | 耐腐蚀、硬度高,用于医疗用途 |
工具钢 | H13, P20 | 高强度、耐热性,用于模制模具 |
铝合金 | 2024, 6061, 7075 | 重量轻,强度重量比高 |
钛合金 | 钛-6Al-4V | 重量轻、耐腐蚀、强度高,适用于航空航天领域 |
镍合金 | 铬镍铁合金 625 和 718 | 耐热/耐腐蚀,适用于涡轮机械 |
钨 | WHA, WC | 密度极高,非常适合平衡应用 |
可根据需要提供标准配方和定制配方。
的特性 MIM 快速成型制造
除了根据性能要求量身定制的成分外,所产生的主要特性还包括
物业 | 说明 |
---|---|
密度 | 范围从接近纯金属密度到大于 95% 理论密度 |
拉伸强度 | 250 兆帕至 1300 多兆帕,取决于加固策略 |
硬度 | 根据合金选择,硬度可达 70 HRC |
耐腐蚀性 | 根据所选成分,阻力水平可能不同 |
表面粗糙度 | 成型时 <6 μm Ra,电镀/抛光后降至 <0.2 μm Ra |
复杂几何 | 模塑可实现其他工艺无法实现的复杂形状 |
功能分辨率 | 可实现小至 ~100 μm 的小槽、小孔、小螺纹 |
壁厚 | 根据几何形状成型的壁厚可低至 ~0.25 毫米 |
公差 | 公差比金属 AM 更小,尺寸公差一般为 ±0.3% |
这些功能使 MIM 适用于最终使用的精密部件。
MIM 快速成型技术的应用
金属射出成型的几何灵活性和量身定制的构成适合各行各业:
行业 | 组件示例 |
---|---|
汽车 | 齿轮、摇臂、涡轮增压器部件 |
航空航天 | 涡轮叶片、叶轮、喷嘴导叶 |
枪支 | 扳机、保险、滑轨、弹射器、枪口 |
医疗/牙科 | 手术刀手柄、镊子、头骨板、头冠 |
石油和天然气 | 阀体、阀杆、执行器等阀门部件 |
微电子 | 屏蔽、连接器、引脚、垫片、致动器 |
MIM 还有助于制造能够进行大规模生产成型/成形操作的模具镶件。
MIM 原料规格
原料特性要求对公差和特征能力进行严格控制:
参数 | 典型规格 | 测试方法 |
---|---|---|
粉末粒度 | 3 - 20 μm | 激光衍射 |
粉末装载 | >55 vol% | 热重分析 |
粉末表观密度 | 2.5 - 4 克/立方厘米 | 霍尔流量计 |
水龙头密度 | >4 克/立方厘米 | 攻丝容积计 |
粘度曲线 | 取决于剪切速率 | 毛细管流变仪 |
颗粒大小分布 | 2 - 4 g 对形状敏感 | 筛分 |
这些规格在确保生坯和烧结强度的同时,还能促进模具流动。
金属射出成型制造工艺概述
- 开发具有所需粉末+粘合剂系统的复合原料
- 对原料进行造粒,实现精确的容积喷射控制
- 具有严格公差和表面光洁度的注塑模具零件
- 通过化学方法剥离并去除聚合物成分
- 理论密度大于 92% 的烧结球团
- 在几何尺寸允许的情况下,根据需要加工特征
- 必要时进行辅助电镀、热处理、涂层等处理
- 生产质量保证测试和验证
该系统将继续进行优化,以确保大批量生产时的可靠性。
MIM 设备和原料供应商
公司名称 | 材料 | 能力 |
---|---|---|
巴斯夫 | 多种 MIM 合金 | 优质原料 |
山特维克鹗 | 316L, 17-4PH, 更多 | 将雾化专业技术转移到 MIM |
MPP | 工具钢、不锈钢、定制钢 | 领先的 MIM 设备 |
CN 创新 | 定制合金 | 新颖作品专家 |
帕马泰克公司 | 钛合金、工具钢、铁合金、特殊材料 | 设备和原料 |
供应商提供成型机和熔炉等配套设备,实现交钥匙生产。
考虑 MIM AM 时的权衡取舍
优点
- 巩固高度复杂的几何形状和组件
- 均匀细粒带来卓越的机械性能
- 表面光洁度高,与模制的一样
- 经证明,一旦获得认证,即可进行大规模生产
- 与金属印刷相比,原材料浪费少
- 利用现有的注塑成型技术
缺点
- 原料配方和工具的前期成本较高
- 新部件和新应用的强化鉴定
- 尺寸范围有限,在几磅以下
- 仅限于粉末状合金
- 极限强度一般低于锻件
- 每个部件的成本高于其他工艺,直到 >10k 数量为止
金属射出成型技术具有良好的性能,可满足小型复杂金属部件的需求。
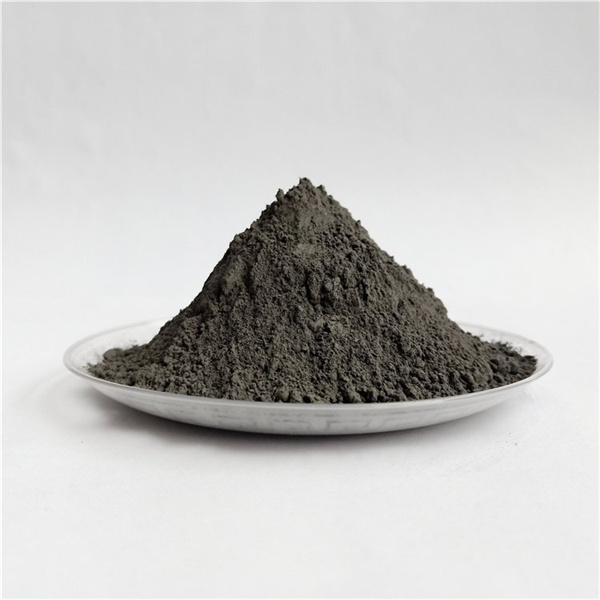
常见问题
MIM 能实际成型多小的特征?
典型的下限范围为:孔直径约 100-150 微米,模具壁厚约 0.3 毫米(约 12 英寸),某些几何形状的模具壁厚更薄。
是什么决定了 MIM 零件的尺寸范围限制?
一般难以处理超过约 5 英寸流线长度的薄壁形状,而不会出现下垂或变形。最大厚度通常在 0.5 英寸以下,重量在 5 磅范围内。
金属射入成型是否允许使用功能分级 (FGM) 复合材料?
是的,先进的模塑工艺现在支持在制造过程中在单个模塑部件中定制孔隙率或空间分级的多粉末原料。
市场上有多少种合金可用作 MIM 原料?
市场上有 60 多种基本配方--300 系列不锈钢占整个市场的 50% 以上,其次是工具钢、钛合金和镍超合金。
MIM 之后通常会经过哪些精加工工艺?
常见的二次加工包括滚筒精加工/振动去毛刺、表面研磨、喷丸强化、激光打标、钝化、电镀、热处理、连接和检查。