IN738LC 是一种重要的镍基超级合金,广泛用于制造燃气涡轮发动机的热段部件。它具有优异的高温机械性能和良好的加工性能。
本指南详细介绍了 IN738LC,包括其成分、特性、加工、应用、优势、局限性、供应商以及与其他超级合金的比较。
介绍 IN738LC 超级合金
IN738LC 是一种可沉淀硬化的镍基超级合金,具有以下主要特性:
- 出色的高温强度和抗蠕变性
- 良好的抗热疲劳和抗氧化性
- 可在 ~1100°C 温度下保持特性
- 成分经过优化,易于加工
- 在燃气轮机中的广泛应用
- 可提供板材、中厚板、棒材和锻件
- 可采用适当的技术进行焊接
其均衡的特性使 IN738LC 适用于在苛刻条件下工作的各种燃气轮机部件。
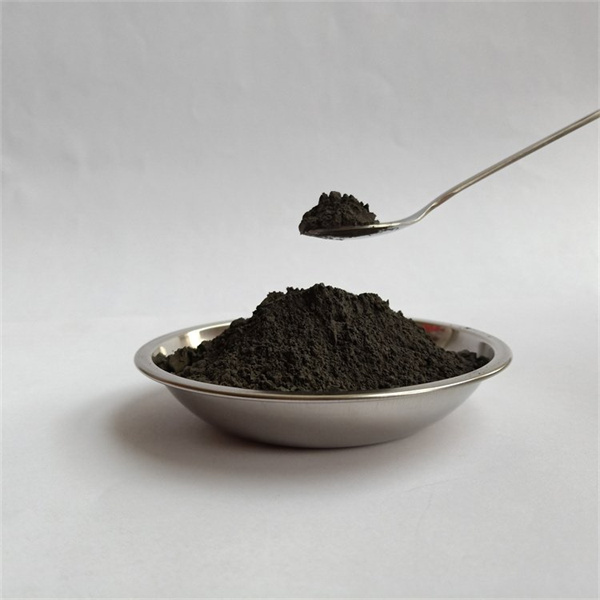
IN738LC 的化学成分
IN738LC 的标称化学成分为
IN738LC 化学成分
要素 | 重量 % |
---|---|
镍 | 巴尔 |
铬 | 16.0 |
钴 | 8.5 |
铝质 | 3.4 |
钛 | 3.4 |
钽 | 1.7 |
碳 | 0.11 |
硼 | 0.001 |
- 镍提供基体并提高延展性
- 抗热腐蚀和氧化的铬
- 用于强化的难熔元素,如 Ta、Ti、W
- 用于晶界强化的碳/硼
- 优化成分,提高焊接性
平衡合金设计兼具高温强度、延展性和可制造性。
IN738LC 的物理和机械特性
物理特性
- 密度:8.19 克/立方厘米
- 熔化范围1315-1370°C
- 导热系数:11 W/m-K
- 弹性模量:205 GPa
- 电阻率: 125 μΩ-cm
室温下的机械性能
- 拉伸强度: 1035 兆帕
- 0.2% 屈服强度:965 兆帕
- 伸长率:22%
- 疲劳强度:590 兆帕
高温机械性能
- 拉伸强度
- 704°C 时 750 兆帕
- 982°C 时为 255 兆帕
- 断裂强度:
- 760°C 时 240 兆帕(100 小时)
- 982°C 时 170 兆帕(100 小时)
这些特性使其适用于温度高达 ~9500C 的长期使用,并具有适当的设计余量。
IN738LC 超级合金的主要应用
IN738LC 适用于
- 燃气轮机热段部件:
- 燃烧器内衬
- 过渡管道
- 涡轮喷嘴
- 1 级和 2 级涡轮叶片和叶片
- 火箭发动机燃烧室
- 热处理装置
- 核燃料棒
- 化学加工工业部件
其多功能性使其适用于严苛环境中的多种关键高温应用。
制造和加工 IN738LC
IN738LC 的重要制造环节包括
融化
- 真空感应熔炼和真空电弧重熔
- 确保化学均匀性
成型
- 高于 1150°C 的热加工
- 板材和箔材的冷加工
热处理
- 溶液处理 - 1120°C,快速冷却
- 沉淀硬化 - 845°C,24 小时,空气冷却
加入
- 电子束和真空钎焊
- 使用匹配的填充合金进行熔焊
涂料
- 扩散铝涂层和覆盖涂层
- 隔热涂料
要获得最佳性能,对熔化、热加工、热处理、连接和涂层的控制至关重要。
为什么选择 IN738LC 超级合金?
IN738LC 的一些主要优势
- 优异的高温机械性能
- 在 ~1100°C 温度范围内保持强度和抗蠕变性
- 良好的抗热疲劳和抗氧化性
- 与其他镍超合金相比,加工灵活性更高
- 可熔焊以制造复杂部件
- 可提供板材、中厚板、棒材和锻件
- 与同类合金相比具有成本效益
- 已有的处理方法和数据
- 获准用于发动机关键部件
IN738LC 具有均衡的性能和加工性,是许多燃气轮机热段部件的理想选择。
使用 IN738LC 超耐热合金的局限性
使用 IN738LC 时需要考虑的一些限制有
- 高温强度低于最新的单晶合金
- 不适用于温度极高的涡轮机部件
- 在成型过程中容易产生应变时效裂纹
- 需要仔细控制热处理
- 抗氧化性低于含铌合金
- 焊接性不如 IN718
- 成型会产生残余应力
IN738LC 可能不适合非常苛刻的环境。适当的设计和加工是减少限制的关键。
IN738LC 超耐热合金供应商
一些主要的 IN738LC 合金供应商包括
- 特种金属公司
- 阿勒格尼技术公司
- 海恩斯国际公司
- 木匠技术
- 山特维克材料技术
- Precision Castparts Corp.
IN738LC 有两种型号:
- 板材
- 酒吧
- 锻造原料
- 电线
- 焊接耗材
产品形式多样,可满足不同的制造要求。
IN738LC 超级合金成本
IN738LC 成本指标
- 板材$90-110/kg
- 条形码:$100-120/千克
- 锻造库存:$110-130/公斤
- 成本取决于尺寸、数量、供应商和原材料成本
- 10-15% 一般比当代镍合金经济
- 需要高纯度原材料,增加了成本
IN738LC 可为许多燃气轮机应用提供经济高效的性能。长期协议可确保价格稳定。
比较 IN738LC 替代超级合金
与 IN718 比较
- IN738LC 具有更高的耐温能力
- 更好的蠕变和热疲劳性能
- 与 IN718 相比,成型问题减少
- IN718 具有更好的焊接性
与 IN713C 的比较
- IN738LC 具有更高的拉伸强度和蠕变强度
- 提高相位稳定性
- 膨胀系数低于 IN713C
- IN713C 具有更好的可制造性
与当代镍合金的比较
- 昱合金 N5、CMSX-4 等先进合金具有更高的温度强度
- 不过,它们的可制造性也较差,成本较高
- IN738LC 提供经济高效的性能组合
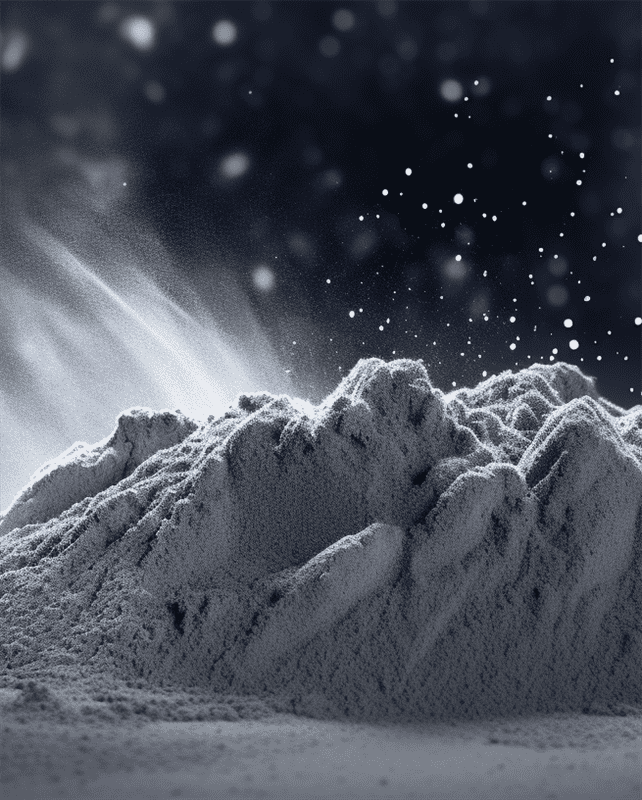
常见问题
问:IN738LC 合金的主要用途是什么?
答:主要应用于燃气轮机热段部件,如燃烧器、过渡管道、喷嘴、涡轮叶片和叶片。它还用于火箭发动机和核燃料棒。
问:IN738LC 的主要特性是什么?
答:与其他镍超合金相比,它具有优异的高温机械性能(最高可达 1100°C)、良好的抗疲劳性和抗氧化性、高强度和更好的可加工性。
问:IN738LC 采用什么热处理方式?
答:在 1120°C 下进行固溶处理,然后在 845°C/24 小时下进行沉淀硬化。受控热处理对达到所需性能至关重要。
问:IN738LC 如何焊接?
答:通常采用电子束和真空钎焊。也可以使用匹配的填充合金和严格控制的工艺进行熔焊。
问:IN738LC 有哪些替代品?
答:替代品包括 IN718、IN713C 和先进的镍合金,如 Renes N5、CMSX。与 IN738LC 相比,它们各有利弊。
问:IN738LC 是否需要涂层?
答:可使用扩散铝涂层或覆盖涂层。热障涂层有利于涡轮机部件。涂层可增强抗氧化性和抗腐蚀性。
问:加工 IN738LC 时有哪些注意事项?
答:它需要高速切削和锋利的刀具,以避免加工硬化效应。大量的冷却液是必不可少的。机加工会产生残余应力,需要进行去应力热处理。
问:IN738LC 在燃气涡轮发动机中的应用?
答:广泛用于燃烧衬里、过渡管道、喷嘴、第 1 和第 2 级涡轮叶片以及热段叶片。
问:IN738LC 有哪些形式?
答:常见的产品形式包括薄板、中厚板、棒材、锻件和线材。根据要求,可使用各种形式制造热截面部件。