Spherical powders feature rounded particle morphology versus irregular shapes. This guide provides a comprehensive look at types of spherical powders, production methods, characteristics, applications, suppliers, and pros/cons.
Overview of Spherical Powders
Key attributes of spherical powders:
- Particles feature rounded morphology
- Produced by gas or water atomization
- More free-flowing than irregular powders
- Allows higher packing density and sintered density
- Used in additive manufacturing and powder metallurgy
- Available in various metals, alloys, and ceramics
The spherical shape provides advantages in handling, consolidation, and performance.
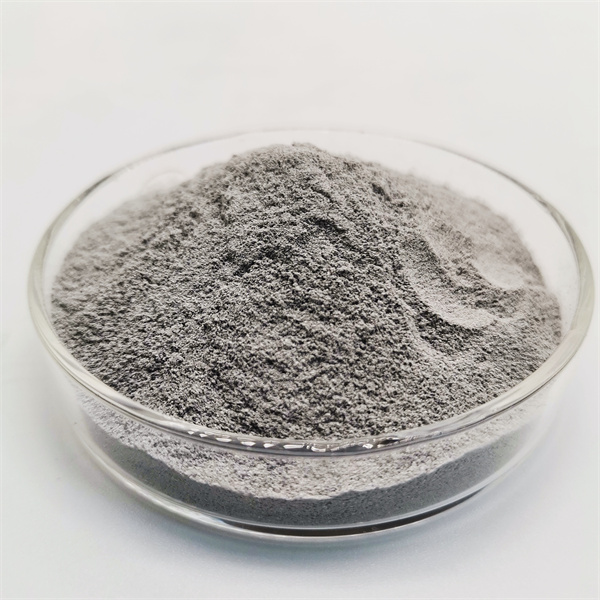
Types of Spherical Powder
Common spherical powder types include:
- Metal powders – stainless steel, titanium, aluminum, nickel alloys
- Alloy powders – tool steels, superalloys, iron alloys
- Ceramic powders – alumina, zirconia, silica
- Carbide powders – tungsten carbide, silicon carbide
- Precious metals – gold, platinum, silver
Both pure metals and alloys are produced in spherical form.
生产方法
Two primary methods produce 球形粉末:
气体雾化
- Metal stream melted by induction, plasma or electron beam
- High pressure inert gas (N2, Ar) disintegrates stream into droplets
- Droplets solidify into spherical particles
- Produces tight particle size distribution
水雾化
- Molten metal stream impinges water jet
- Metal disintegrates into spherical droplets
- More irregular shapes than gas atomization
- Wider particle distribution
- Lower cost than gas atomization
Gas atomization is preferred for critical applications needing uniformity.
特点
Spherical powders provide:
- Improved flowability due to roundness and surface smoothness
- Higher packing density compared to irregular powders
- More uniform particle melting leading to better densification
- Isotropic shrinkage during sintering
- Reduced entrapped porosity after compaction
- Allows thinner powder layers in additive manufacturing
The spherical shape brings handling and performance benefits.
应用 Spherical Powders
Common uses taking advantage of spherical powder properties:
- Metal additive manufacturing – better powder spreading, dense prints
- Metal injection molding – improves powder loading and flow
- Thermal spraying – more consistent particle melting
- Powder metallurgy – higher density with less pressing pressure
- Powder coating – improved fluidization and surface finish
- Electronics – spherical conductive powders for contacts, circuits
Spherical powders enhance manufacturing processes involving powder flow and melting.
规格
Key spherical powder specifications:
- Chemistry – composition tolerance
- Particle size – distribution statistics
- Morphology – circularity, smoothness
- 表观密度和敲击密度
- Flow rate through standard orifice
- Specific surface area – BET method
- Impurities – limits on gaseous/metallic impurities
Standards include ISO, ASTM, ASME, and industryspecific standards.
供应商
Leading global suppliers of spherical powders include:
- Sandvik Osprey – Widest range of spherical powders
- Carpenter Additive – Broad selection of gas atomized alloys
- AP&C – Specializes in producing spherical titanium and nickel alloys
- Erasteel – Spherical powders for thermal spray and MIM
- Linde Gas – Atomization technology and metal powder producer
- Ampal Inc. – Spherical titanium, aluminum and other alloy powders
Reputable suppliers ensure reliable quality and consistency.
成本分析
Spherical powders incur higher costs than irregular powders:
- Gas atomization equipment has high capital costs
- Additional processing steps required
- Raw material yield losses from oversize/undersize powder
- Tighter sieving generates more recycle streams
- Higher purity raw materials needed
- Price premium around 30-50% over irregular powder
The benefits often justify the higher price point.
Pros and Cons of Spherical Powder
优势 | 缺点 |
---|---|
Excellent flowability | More expensive than irregular powder |
Higher packing density | 尺寸范围有限 |
More uniform melting | More controlled production |
Reduced porosity | Lower apparent density |
Better spreadability | Higher impurity levels than wrought forms |
Spherical powders provide significant benefits despite some drawbacks.
Spherical vs Irregular Powder
参数 | Spherical Powder | Irregular Powder |
---|---|---|
形状 | Rounded | Jagged, uneven |
流动性 | 优秀 | 公平 |
Packing density | 更高 | 较低 |
Printing resolution | Sharper | Poorer |
费用 | 更高 | 较低 |
可用性 | 有限合金 | Most common alloys |
The optimal choice depends on application requirements.
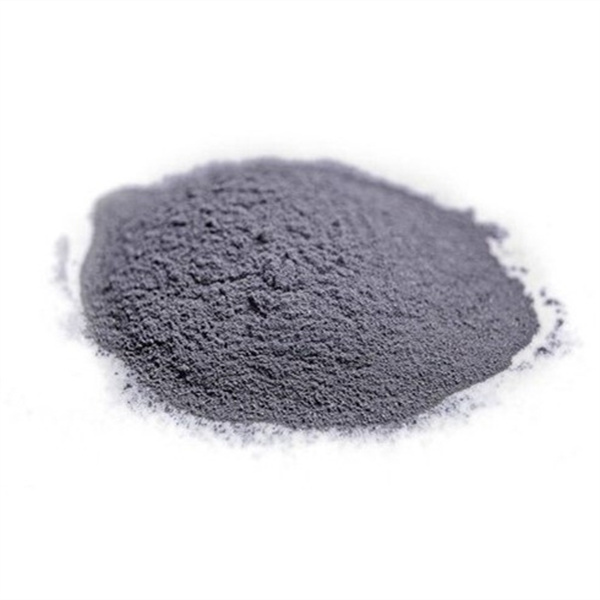
常见问题
What is spherical powder used for?
Spherical powders are ideal for additive manufacturing, metal injection molding, thermal spraying, and powder metallurgy applications where flow and dense consolidation are critical.
Why is spherical powder more expensive?
The specialized gas atomization production and tighter specifications required result in higher costs for spherical powder compared to irregular powder.
What is the main advantage of spherical powders?
The main benefit is improved powder flow during handling and processing, allowing higher packing densities and material deposition uniformity.
What metals are available as spherical powder?
Common choices include stainless steel, tool steel, titanium, aluminum, nickel, cobalt alloys. Specialized alloys are possible but may require custom production.
What is the difference between gas and water atomization?
Gas atomization produces more spherical particles and tighter distribution, while water atomization has lower costs but less uniform powder shapes.
Spherical powders provide significant advantages justifying their use where affordability permits.
结论
Spherical powders produced by gas or water atomization provide enhanced powder flow and densification crucial for additive manufacturing, thermal spraying, powder metallurgy, and powder injection molding. Their rounded morphology allows higher packing densities and uniform melting behavior. While more costly than irregular powders, spherical particles optimize processing and performance for critical components across aerospace, medical, automotive and industrial applications. Continued improvements in atomization technology combined with the growth of powder-based manufacturing will drive increasing development and adoption of high quality spherical powders.