Aluminum AlSi10Mg powder is an aluminum alloy containing silicon and magnesium as its major alloying elements. This metal powder has emerged as a popular choice for additive manufacturing applications like selective laser sintering (SLS) and direct metal laser sintering (DMLS) thanks to its excellent mechanical properties, lightweight nature, corrosion resistance and high strength-to-weight ratio.
This article provides a comprehensive technical overview of Aluminum AlSi10Mg powder covering its composition, properties, production methods, applications, advantages and limitations. Quantitative data is presented in tabular formats along with insights and subjective commentary to help readers thoroughly understand this advanced engineering material.
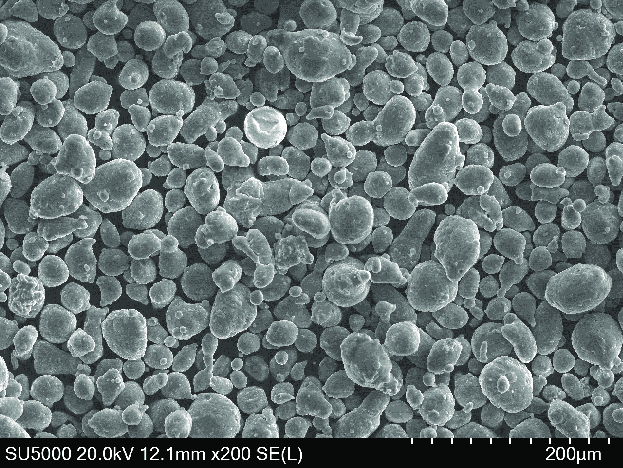
Aluminum AlSi10Mg Powder Composition
The composition of Aluminum AlSi10Mg powder is as follows:
要素 | 重量 % |
---|---|
铝 (Al) | 剩余 |
硅 (Si) | 9-11% |
镁(Mg) | 0.2-0.45% |
铁(Fe) | < 0.55% |
锰 (Mn) | < 0.45% |
钛 (Ti) | < 0.15% |
The high silicon content results in good fluidity and castability as well as improved strength and hardness. The addition of magnesium enhances strength through solid solution strengthening and precipitation hardening.
Small amounts of iron, manganese and titanium are also present as impurity elements. Tighter control over composition allows this alloy powder to achieve better consistency in final part properties.
Aluminum AlSi10Mg Powder Properties
AlSi10Mg is valued for its excellent strength-to-weight ratio and good corrosion resistance. Here are some of the key properties of this aluminum alloy powder:
机械性能
物业 | 价值 |
---|---|
密度 | 2.68 克/立方厘米 |
极限拉伸强度 | 430 MPa |
屈服强度 | 270 MPa |
杨氏模量 | 73 GPa |
Elongation at Break | 8% |
硬度 | 120 HB |
The low density compared to steels along with high strength and stiffness make AlSi10Mg an attractive lightweight substitute in many applications. The elongation indicates moderate ductility for an aluminum alloy while the Brinell hardness value is high enough for good wear resistance.
物理特性
物业 | 价值 |
---|---|
熔点 | ~600°C |
导热性 | 150 W/m-K |
电阻率 | 3.5 x 10^-6 Ω-cm |
热膨胀系数 | 21 x 10^-6 K^-1 |
The moderately high melting point coupled with good thermal conductivity suits AlSi10Mg for thermal processing methods involved in additive manufacturing. The electrical and thermal expansion properties are typical of aluminum alloys.
Corrosion Properties
- Excellent corrosion resistance in neutral aqueous environments
- Resistant to attack by most acids and alkalis
- Susceptible to pitting and crevice corrosion by chlorides
Overall, AlSi10Mg powder displays very good corrosion resistance due to the protective oxide layer on its surface. This makes it suitable for use in humid environments and applications involving contact with water.
Aluminum AlSi10Mg Powder Production
AlSi10Mg powder for AM processes is commonly produced by:
- 雾化 – Alloy molten metal stream is disintegrated by gas or water jets into fine droplets that solidify into powder. This produces spherical powder ideal for powder bed fusion.
- 等离子旋转电极工艺(PREP) – Alloy is melted by plasma arc and centrifugally atomized by rotating electrode disks. Gives spherical powder with good flowability.
- 气体雾化 – An inert gas like argon or nitrogen is used to atomize the molten alloy resulting in fine spherical powder. Most widely used process.
Key powder attributes:
- Particle size range – 15 to 45 microns
- Morphology – Spherical shape with some satellites
- Flowability – Excellent, with Hall flow rates > 30 s/50 g
- Apparent density – ~2.7 g/cc
- Tap density – Up to 80% of alloy density
These properties make AlSi10Mg readily compatible with common AM processes like selective laser melting and electron beam melting that involve powder spreading and levelling.
Applications of Aluminum AlSi10Mg Powder
Some major applications of AlSi10Mg alloy powder include:
航空航天 Brackets, airframe components, engine parts
汽车 Chassis parts, linkage components, transmission gears
工业 Robotics parts, tooling, machine components
医疗 Orthopedic implants, prosthetic devices, surgical instruments
Consumer: Electronics housings, sporting goods, automotive accessories
The lightweight nature along with strength makes this alloy suitable for weight-sensitive mobility applications in aerospace, automotive and medical sectors. AlSi10Mg enables high strength customized metal parts to be produced using AM for diverse industry applications.
AlSi10Mg Powder for Additive Manufacturing
AlSi10Mg is one of the most popular aluminum alloy powders used in powder bed fusion AM processes like:
- 选择性激光熔化(SLM)
- Selective laser sintering (SLS)
- 直接金属激光烧结(DMLS)
- 电子束熔化(EBM)
Benefits of Using AlSi10Mg Powder in AM:
- Parts with strength exceeding cast alloy components
- Near full density up to 99.8%
- Excellent surface finish and geometric accuracy
- Complex geometries possible through AM
- Reduced waste compared to subtractive methods
- Lightweighting compared to titanium or steel parts
- Consistent and repeatable mechanical properties
AlSi10Mg enables substantial weight savings over traditional materials while matching or exceeding their performance. This drives its widespread usage across aviation, space, automotive and medical sectors.
However, factors like porosity control, anisotropy, residual stresses, and heat treatment requirements need special consideration when printing with this alloy.
AlSi10Mg 粉末供应商
Some of the major global suppliers of Aluminum AlSi10Mg alloy powder include:
公司名称 | 产品名称 |
---|---|
AP&C | ALC-42 |
Arcam AB | AlSi10Mg |
木匠 | AlSi10Mg |
EOS | AlSi10Mg |
GE Additives | AlSi10Mg |
LPW 技术 | AlSi10Mg |
普莱克斯 | Al-43 |
山特维克 | 鹗 AlSi10Mg |
These powder suppliers have extensive experience producing AlSi10Mg to the exacting standards demanded by AM. They also provide technical data, material characterization and parameter guidelines to aid AM processing.
硅铝镁合金粉定价
The price of AlSi10Mg powder suitable for AM can range from $50/kg to $120/kg based on:
- 纯度水平
- Consistency in chemical composition
- Particle size range and distribution
- Powder morphology (sphericity and surface texture)
- Supply quantity
- Geographic region
High quality gas atomized AlSi10Mg powder intended for critical applications costs over $100/kg while cheaper powder with less stringent specifications can cost ~$60/kg in bulk volumes.
Inquiry to get best price from Met3DP!
AlSi10Mg versus Alternatives for AM
AlSi10Mg competes against several alternative lightweight alloys and materials when selecting powder for AM. Here is how it compares:
合金 | 优点 | 缺点 |
---|---|---|
AlSi10Mg | Strength, corrosion resistance, weldability | Lower maximum temperature |
Ti6Al4V | High strength, biocompatibility | Expensive, high density |
AlSi7Mg | Higher ductility | Lower strength than AlSi10Mg |
斯卡莫洛伊 | High strength with heat treatment | 有限的耐腐蚀性 |
Aluminum 6061 | Widespread availability | Lower strength than AlSi10Mg |
Carbon fiber | Very low mass | Challenging to print, anisotropic |
For the majority of applications, AlSi10Mg provides the best combination of mechanical performance, corrosion resistance, weldability and cost-effectiveness. Its strength surpasses 6061 aluminum while it avoids the high expense of titanium alloys.
Advantages and Limitations of AlSi10Mg for AM
优势
- High specific strength exceeding some titanium alloys
- Nearly 30% lower density compared to steel
- Cost advantage over exotic alloys like titanium and inconel
- Better corrosion resistance than magnesium or carbon fiber composites
- Improved ductility over very high strength aluminum alloys
- Capability to integrate stiffening elements and lattices to enhance stiffness
- Faster build rates than reactive metals like titanium
- Powder recyclability over multiple builds
局限性
- Lower maximum operating temperature than steels or titanium alloys
- Susceptibility to thermal warping and cracking compared to steels
- Extra support structures required during builds
- Higher porosity levels than with steels
- Heat treatments needed for optimal properties
- More anisotropic mechanical properties than isotropic materials like steels
- Surface roughness often requires finishing operations
- Limited biocompatibility compared to titanium
Understanding these tradeoffs allows appropriate selection for specific applications and operating conditions.
AlSi10Mg Powder – Frequently Asked Questions
Here are answers to some common questions about AlSi10Mg powder for AM:
Q: What particle size is best for AM with AlSi10Mg powder?
A: A particle size range of 15-45 microns works well across most AM processes. Finer powder below 10 microns can cause dust issues while larger particles above 60 microns hurts density and surface finish.
Q: What is the effect of silicon content on AlSi10Mg properties?
A: Increasing silicon from ~9% to ~11% enhances powder flowability. It also improves hardness and thermal stability at the expense of some loss in ductility and fracture toughness.
Q: Why is gas atomization the preferred method for making AM AlSi10Mg powder?
A: Gas atomization allows precise control over the spherical morphology and narrow particle distribution needed for AM processes. It avoids contamination issues seen with water atomization.
Q: How should AlSi10Mg parts be heat treated after AM processing?
A: A typical heat treatment is solutionizing at 530-550°C for 1-3 hours followed by hot isostatic pressing (HIP) and then aging at 160-180°C for 6-8 hours to achieve optimal strength.
Q: Is AlSi10Mg easily weldable for post-processing AM parts?
A: Yes, AlSi10Mg can be welded using 5XXX filler alloys. Good weldability allows additional joining and modification of AlSi10Mg AM parts.
Q: Does AlSi10Mg powder require drying before AM processing?
A: Pre-drying at 80-100°C for 2-4 hours is recommended to remove surface moisture that can cause issues like balling and porosity during AM builds.
结论
AlSi10Mg aluminum alloy powder has emerged as one of the foremost materials for additive manufacturing of metal parts across diverse industries. Its properties like high strength-to-weight ratio, good corrosion resistance, excellent flowability and ease of post-processing make AlSi10Mg a versatile choice for AM.
As AM processes continue maturing, AlSi10Mg is poised to deliver lighter and stronger components with optimized geometries to drive the next generation of design innovation. With ongoing alloy development and parameter optimization, the capabilities of this material will expand even further.