概述 MIM 技术
金属注射成型(MIM),又称粉末注射成型(PIM),是一种先进的制造工艺,用于大批量生产小型、复杂的金属零件。
MIM 将注塑成型的设计灵活性和精度与机加工金属零件的强度和性能相结合。它可以利用先进的金属合金,经济高效地生产出具有良好机械性能的复杂部件。
金属射出成型工艺首先使用由细金属粉末与粘合剂材料混合而成的原料。然后使用注塑成型设备将原料注入模具。粘合剂将金属粉末固定在一起,并为成型提供流动性。
成型后,通过脱脂工艺将粘合剂从成型的绿色部件中去除。脱脂后的部件称为棕色部件,然后在高温下烧结,将金属颗粒熔结在一起,形成一个坚固的金属部件,其材料特性接近于锻造部件。
MIM 适合使用各种金属(如不锈钢、低合金钢、工具钢、磁性合金、超级合金、钛合金和钨重合金)制造小型复杂零件。它结合了注塑成型的多功能性和粉末冶金的材料灵活性。
MIM 技术的主要优点包括
- 可大批量生产复杂、精细的金属部件
- 近净成形制造减少了浪费并最大限度地降低了加工成本
- 接近锻造材料的良好机械性能
- 多种金属可供选择,包括不锈钢、工具钢和超级合金
- 可将部件整合为单一组件
- 产量高,单位成本低
- 自动化流程的一致性和可重复性
MIM 技术是小型复杂零件的理想选择,如医疗设备、枪械部件、手表部件和汽车零件等,这些零件要求精确、强度高、经济实用和大规模生产。
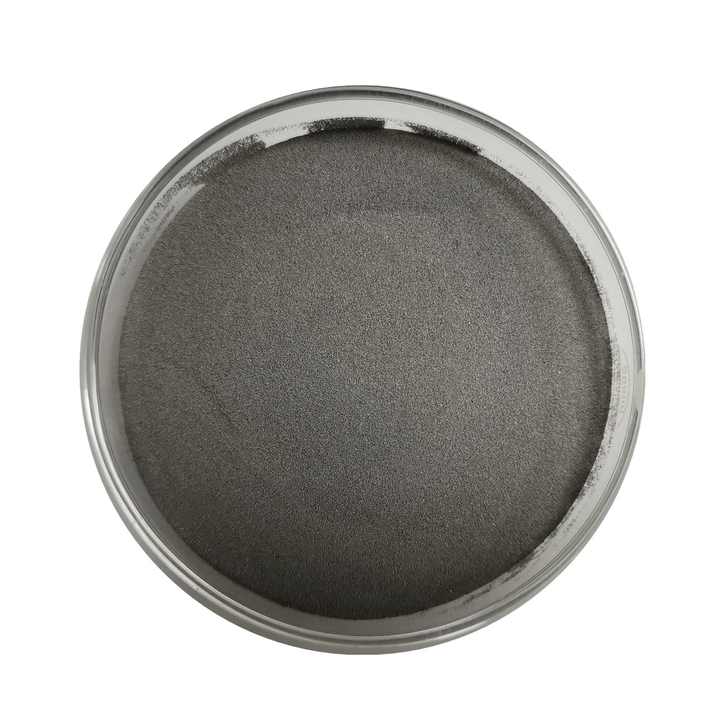
MIM 技术的应用和用途
MIM 技术广泛应用于各行各业,可高效地大批量制造小型、高精度金属零件。以下是 MIM 技术的一些主要应用领域和用途:
行业 | 应用和用途 |
---|---|
医疗和牙科 | 手术器械、牙科植入物、整形外科植入物、导管组件、针管、手术刀手柄、镊子、夹子、手术紧固件、可重复使用的手术器械 |
枪械与防卫 | 扳机、击锤、保险装置、弹射器、弹夹、弹壳、弹丸、弹头部件 |
汽车 | 燃油系统部件、油泵齿轮、叶轮、阀门、涡轮增压器部件、电子部件、转向/传动部件 |
航空航天 | 涡轮叶片、叶轮、齿轮齿、衬套、泵部件、发动机部件 |
消费品 | 手表部件、珠宝配件、餐具、剪刀、剃须刀、手工工具、拉链部件 |
工业硬件 | 旋钮、配件、紧固件、插座、连接器、喷头、喷嘴 |
电子产品 | 连接器、开关、微电机、微型齿轮、屏蔽罩、电感器、磁铁转子 |
** 针对特定应用的金属射出成型的优势**
- 精密:适用于微型零件,如具有复杂几何形状的医疗设备或手表部件。
- 强度:适用于需要高强度的部件,如汽车涡轮增压器和枪械扳机。
- 耐磨性:由工具钢合金制成的 MIM 零件具有出色的耐磨性,使用寿命长。
- 耐腐蚀:不锈钢 MIM 零件耐腐蚀,可用于可重复使用的手术工具、植入物等。
- 高硬度:金属射出成型可以生产硬度超过 40 HRC 的零件,如刀具、工具、模具等。
- 电气性能:MIM 用于制造电感器、电机转子等软磁元件。
- 成本效益高:与机加工相比,大批量生产可大幅降低零件成本。
MIM 设备和工具指南
MIM 工艺使用的主要设备包括注塑成型机、脱脂和烧结炉。以下是相关概述:
设备 | 目的 | 考虑因素 |
---|---|---|
注塑机 | 在加热和加压的情况下,将 MIM 原料注入模腔 | 锁模力、注塑速度和压力能力、精度和重复性、控制和自动化功能。 |
粘合剂去除炉 | 用热或化学方法去除模制件上的粘合剂 | 温度范围、气氛控制、装载量、排胶均匀性。 |
烧结炉 | 通过加热至接近熔点,使去骨的棕色部件致密化 | 温度范围、气氛控制、加热均匀性、批量能力,全自动为佳。 |
模具和工具 | 成型腔将 MIM 原料成型为所需的几何形状 | 可承受成型压力和温度,加工精密,表面光洁度好,可快速加热/冷却。 |
原料设备 | To mix the metal powder and binder into homogeneous MIM feedstock | Mixers, temperature controllers, pelletizers. |
二次加工 | Additional steps like machining, joining, surface treatment | As per part needs like CNC machining, welding, EDM, coating. |
质量控制 | To test feedstock, sintered parts properties | Powder morphology, density, flow rate, viscosity analyzers, mechanical testing equipment. |
Safety Equipment | To handle fine powders safely | Gloves, respirators, dust collection systems. |
Design and Performance Standards
- ISO 21227 – Powders for metal injection molding
- ASTM F2885 – Metal Injection Molding Process
- MPIF 35 – Standards for MIM feedstock
- ASTM E2781 – MIM Tensile Test Specimen Design
- ISO 2740 – Sintered Metal Injection Molding parts
Cost Breakdown
The typical cost distribution in MIM production is:
- Raw Materials (Powder + Binder): 50-60%
- Manufacturing (Molding + Debinding + Sintering): 25-35%
- Secondary Processing: 5-10%
- Quality Control: 2-5%
- Engineering (R&D, Design): 2-5%
供应商和定价
Here are some leading global suppliers of MIM equipment and their price ranges:
供应商 | 产品类别 | 价格范围 |
---|---|---|
阿尔堡 | Injection molding machines | $100,000 – $500,000 |
Indo-US MIM | MIM feedstock & services | $5 – $50 per Kg |
Elnik | Debinding and sintering furnaces | $50,000 – $1,000,000 |
FineMIM | End-to-end MIM production | $0.5 – $5 per part |
Parmatech | Metal powder Atomization | $250,000 – $1,000,000 |
Meridian Technologies | Tooling and mold design | $5,000 – $100,000 |
安装、运行和维护
MIM is an automated process but needs careful installation, operation and maintenance for optimum performance:
活动 | 详细信息 |
---|---|
安装 | Precision alignment of injection molding machine and molds. Calibrate temperature controllers. Test run with trial batches. |
运行 | Ensure feedstock quality control as per standards. Achieve process parameters like injection pressure, temperature and speed. |
维护 | Schedule preventive maintenance for molding machine barrels, screws, molds. Maintain debinding furnace atmosphere. Calibrate instruments. |
清洁 | Follow SOPs for machine barrel cleaning after runs. Ensure no powder accumulation in furnace or ducts. Mold cleaning with designed media. |
安全 | Wear personal protective equipment while handling fine powders. Proper disposal of chemical binders. Allow furnace cooling before maintenance. |
Training | Train machine and furnace operators on procedures. Conduct refresher sessions on safety and maintenance. |
优化 | Adjust process parameters until part quality stabilizes within specifications. Maintain detailed process records. |
Typical Maintenance Activities and Frequency
活动 | 频率 |
---|---|
Injection molding machine nozzle cleaning | After each batch |
Mold polishing | 每周 |
Machine barrel cleaning | 每月 |
Binder removal oven atmosphere check | 每月 |
Sintering furnace thermocouple calibration | 6 个月 |
Mold flow studies | 每年 |
How to Choose an MIM Supplier
Choosing a competent MIM supplier is critical to get good quality parts on time at reasonable cost. Here are important factors to consider:
系数 | 标准 |
---|---|
Technical Capability | Advanced equipment, years of experience, technical expertise |
Material Options | Range of materials like stainless steel, tool steel, tungsten alloys |
二次加工 | In-house machining, joining, coating facilities |
Quality Systems | ISO 9001 certification, quality control and inspection procedures |
生产能力 | High volume production ability for stability |
准备时间 | Fast turnaround time from design to delivery |
地点 | Geographic proximity for logistics efficiency |
费用 | Pricing model – per part pricing preferred |
客户服务 | Responsiveness to inquiries, technical support, project management |
Questions to Ask Prospective MIM Suppliers
- What materials and part sizes do you have experience with?
- Do you offer secondary processing like machining or coating?
- What quality certifications and inspection procedures are followed?
- How is handling of sensitive materials like titanium alloys or tungsten carbides done?
- What production volumes can you reliably deliver on a monthly basis?
- How is scrap minimized and yields maximized?
- What is the part-to-part variability in dimensions and properties?
- How will design optimization be done for MIM process?
- What quality reports and control charts will be provided?
Comparing MIM with Other Processes
Comparison between MIM and other metal manufacturing processes:
过程 | 优势 | 缺点 |
---|---|---|
MIM | Complex geometries, mass production, near net shape, wide material choices | Upfront tooling investment, size limitations |
数控加工 | Material flexibility, fast turnaround of prototypes | Limited complexity, lower volumes |
金属铸造 | Low part cost, high volumes | Shape limitations, lower strength |
Metal Stamping | High speed, high volumes, low costs | Only suits 2D geometries |
三维打印 | Design freedom, fast prototyping | Lower strength, higher cost, limited sizes and materials |
Benefits of MIM over Machining
- Higher material utilization with near net shape
- No expensive machining for complex shapes
- Superior mechanical properties
- Lower tooling costs compared to machining dies
- Automated process enables mass production
- Better surface finishes possible
Advantages of MIM over Metal Casting
- Better dimensional accuracy and surface finish
- Fewer defects like porosity compared to cast parts
- Isotropic properties unlike directional casting
- Low to no flash or opening unlike castings
- No melt-related reactions or compositional changes
- Cores and undercuts possible unlike casting
- Wide material options beyond castable alloys
- Consistency of properties with powder metallurgy
Limitations of MIM versus CNC Machining
- Size limited by injection molding machine capacity
- More upfront time and cost for tooling
- Tight tolerances +/- 0.5% vs. +/- 0.1% for CNC machining
- Geometry limitations vs. unrestricted machining
- Lower maximum hardness achievable compared to machining
- Secondary machining often still needed to achieve tolerances
When Not to Use MIM
- Very large parts beyond MIM equipment capacity
- Parts needing extremely tight tolerances below 0.5%
- Applications requiring surface hardness above 50 HRC
- Products with very low volume requirements
- Components with extreme aspect ratios unsuitable for molding
- When no time for design optimization for MIM process
- Cost-sensitive applications with cheaper manufacturing options
MIM Design and Modeling Considerations
Proper part and feedstock design is crucial for MIM to achieve required properties and performance. Here are key design considerations:
Part Design Stage
- Optimize wall thicknesses for uniform mold filling during injection
- Include generous internal radii and fillets to ease filling
- Avoid severe changes in cross-section along the flow path
- Design proper mold gates and runners for suitable flow patterns
- Add strengthening ribs and gussets to avoid sagging or warpage
- Account for part shrinkage during sintering in initial dimensions
- Develop prototype molds for design validation before full production
Feedstock Development
- Match feedstock viscosity to mold complexity at molding temperatures
- Ensure sufficient powder loading for required sintered density
- Select suitable binder components and powder ratio for mixability
- Optimize powder particle size distribution for powder packing density
- Adjust feedstock formulations for defect-free binder removal
- Validate feedstock properties through mold flow simulations
- Test multiple feedstock iterations to achieve full mold-ability
Simulation and Modeling
- Mold flow modeling to optimize gate locations and runners
- Structural FEA to predict warpage and optimize part geometry
- CFD simulations for uniform binder removal and sintering
- Thermal modeling to minimize residual stresses
- Mechanical modeling to maximize strength and performance
- Process modeling software to study interactions between parameters
- Experimental validation of software predictions through prototype molds
Key Modeling Outputs
- Mold filling time, feedstock viscosity, flow front temperature
- Weld line, air trap and other molding defect predictions
- Spatial binder content, temperature and dissolution gradients
- Sintering rate, density gradients, shrinkage, warpage trends
- Residual stress distribution, hot tear and crack estimates
- Mechanical strength, fatigue life, damage tolerance analysis
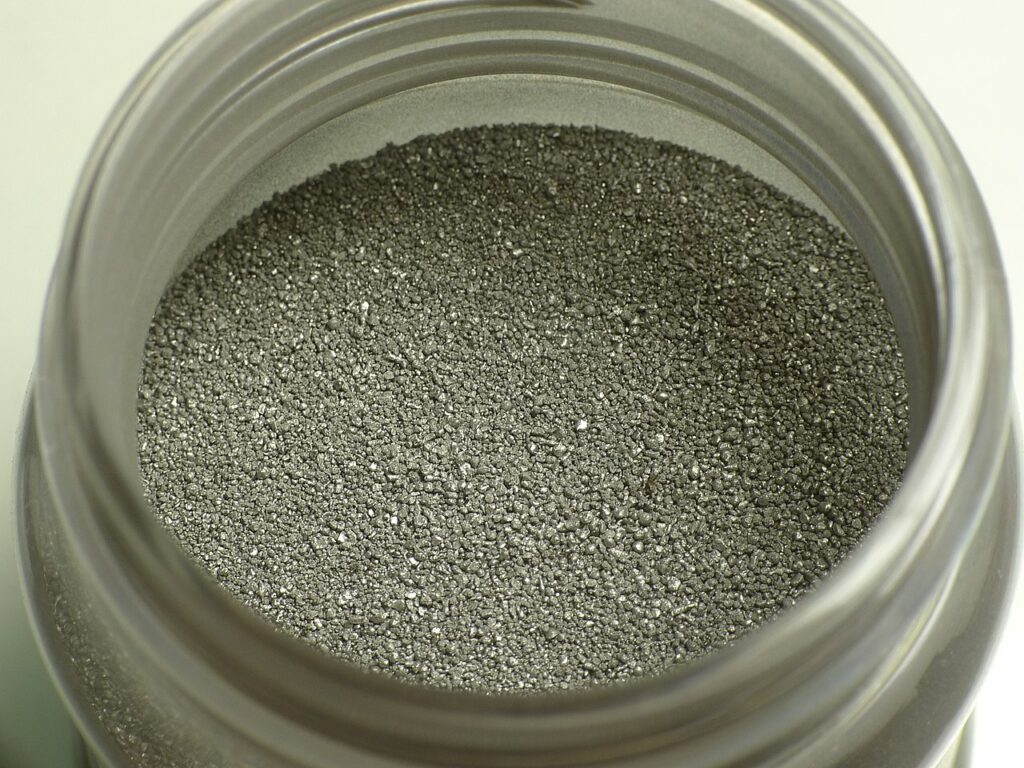
MIM Defects and Mitigation Methods
Defects can arise in MIM parts due to non-optimized feedstock, molding parameters or furnace conditions. Here are common MIM defects and mitigation methods:
缺陷 | Root Causes | Mitigation Methods |
---|---|---|
表面缺陷 | Low mold temperature, high friction, binder components | Optimize mold polishing, use mold release agents, lower mold temp gradually |
Weld lines | Undesirable feedstock flow fronts | Optimize gate and runner design through modeling to prevent weld lines |
Warpage | Non-uniform heating in furnace, residual stresses | Structural optimization, pre-sintering stress relief, optimized furnace settings |
Cracks | Rapid sintering, high binder content, steep thermal gradients | Lower heating rate, optimize binder system, structural redesign |
孔隙率 | Low powder loading in feedstock, poor mixing | Increase powder content in feedstock, improve mixing process |
Dimensional variation | Inconsistent shrinkage, mold wear, density gradients | Statistical process control, mold maintenance, optimize debinding and sintering |
污染 | Poor handling, furnace atmosphere control | Proper PPE, improve air filters, prevent cross-contamination in furnace batches |
Incomplete filling | High mold temperature, high viscosity | Increase mold and feedstock temperature, use lower viscosity binder |
MIM Industry Data and Trends
MIM Global Market Size
The global MIM market was valued at USD 1.5 billion in 2022 and is projected to reach USD 3.1 billion by 2030, growing at 8.7% CAGR, driven by demand from healthcare, automotive and aerospace sectors.
Industry Growth Drivers
- Lightweighting trends across automotive, aerospace, electronics sectors
- Demand for small, complex metal components in medical devices
- More viable with a wider range of MIM-able materials
- Automation bringing down production costs
- Growth in manufacture of precision components
- Increased adoption in emerging applications like watchmaking
Projected CAGR by Region
- Asia Pacific: 9.3% CAGR
- Europe: 10.2% CAGR
- North America: 7.6% CAGR
- Rest of the World: 7.9% CAGR
Share of MIM Parts by Industry
- Consumer products: 22%
- Automotive: 21%
- Firearms: 15%
- Medical: 14%
- Industrial: 13%
- Aerospace: 8%
- Others: 7%
MIM Technology Development Trends
- New binder systems to reduce defects and enable complex geometries
- Novel feedstock formulations for better powder loading and sintering
- Multi-material MIM combining different powders into one component
- Automation of post-processing like machining, joining, threading etc.
- Hybrid MIM + Additive Manufacturing techniques
- New heating methods like microwave sintering for faster processing
- Integrated simulations combining multiple physics and manufacturing steps
- Increased adoption of quality management systems
摘要
Key takeaways:
- MIM enables high volume production of intricate metal components through combining injection molding and powder metallurgy.
- Suitable for small, complex, high precision parts in medical, firearms, automotive, aerospace, and consumer industries.
- Benefits include near-net shape, wide material choice, good mechanical properties close to wrought materials.
- Involves molding of feedstock, debinding, and sintering steps using specialized equipment.
- Requires expertise in part design, feedstock development, process modeling, defect control, and quality management.
- Projected to grow at 8.7% CAGR globally driven by demand across industries.
- Ongoing technology developments for faster processing, more materials, increased automation and improved part quality.
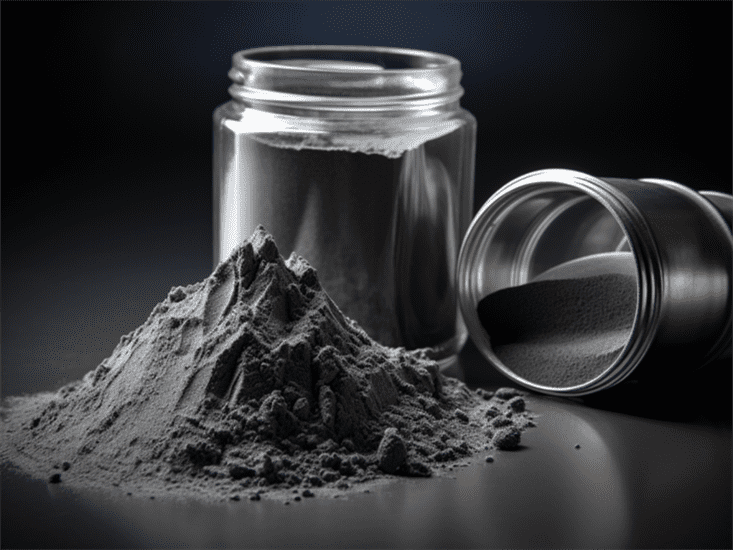
常见问题
Q: What are the key advantages of MIM technology?
A: The main advantages of MIM are:
- Ability to produce small, complex geometries not possible through machining or casting
- Near-net shape manufacturing resulting in
Q: What is the typical tolerance capability of MIM?
A: MIM can generally achieve tolerances of +/- 0.5% although +/- 0.3% is possible for some geometries and machining may be needed for tighter tolerances.
Q: What size of parts can be produced using MIM?
A: MIM can produce parts from 0.1 grams up to around 250 grams in mass. Larger parts are possible but challenging due to limitations in molding machine size.
Q: How does MIM compare to plastic injection molding?
A: While both use injection molding equipment, MIM can produce metal parts whereas plastics have much lower strength. But MIM has lower production rates and higher costs than plastic injection molding.
Q: What heat treatment is used in MIM?
A: The sintering process in MIM involves heating to almost melting point of the metal powder so no further heat treatment is typically needed. Additional heat treatments can be done as required to modify properties.
Q: What materials can be used in MIM?
A: A wide range of materials are MIM-able including stainless steels, tool steels, superalloys, titanium, tungsten heavy alloys, and magnetic alloys among others. New material development is a key research area in MIM.
Q: How does MIM compare to metal 3D printing?
A: MIM can produce higher volumes with better surface finish and mechanical properties. But 3D printing offers greater design freedom and faster time to market for prototypes or custom parts.