개요
구형 분말 특수 분무 공정에 의해 생성된 둥근 형태의 금속 또는 세라믹 분말을 말합니다. 불규칙한 분말 입자와 비교하여 구형 분말은 우수한 유동성, 높은 충전 밀도 및 입자 내부 마찰 감소와 같은 이점을 제공합니다. 따라서 분말 야금, 열 분사, 금속 적층 제조 및 세라믹 가공을 사용하는 까다로운 산업 응용 분야에 이상적입니다.
이 포괄적인 가이드는 다양한 유형의 구형 분말, 그 특성, 제조 방법, 주요 용도, 사양, 공급업체, 취급 절차, 장비 유지 관리, 공급업체 선택 기준, 장단점, 자주 묻는 질문에 대한 답변을 다루고 있습니다.
종류 구형 분말
재료 및 생산 방법에 따른 구형 분말의 주요 유형은 다음과 같습니다.
재질
- 금속 분말 - 스테인리스강, 공구강, 초합금, 티타늄, 알루미늄 등
- 세라믹 분말 – 알루미나, 지르코니아, 실리카, 탄화물, 질화물 등
- 복합/합금 분말 – 니켈 기반, 코발트 기반, Fe 기반 등
생산 방법
- 가스 분무 분말
- 플라즈마 원자화 분말
- 전극 유도 용융 가스 원자화(EIGA)
- 회전전극공정(REP)
- 플라즈마 회전 전극 공정(PREP)
- 열 스프레이 파우더
가스 원자화는 가장 널리 사용되는 공정이지만 PREP과 같은 방법은 우수한 구형성과 매끄러운 표면 형태를 제공합니다. 생산 방법은 최종 분말 특성을 제어합니다.
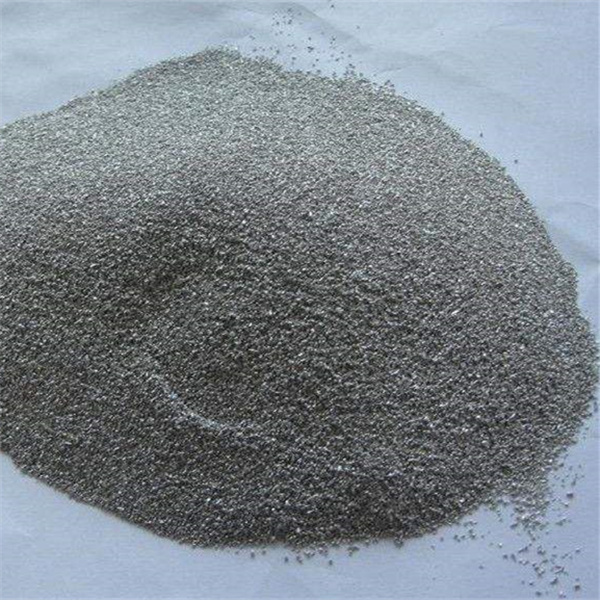
속성 및 응용
주요 구형 분말 유형의 특성 및 일반적인 용도:
스테인리스 스틸
- 높은 경도와 내식성
- 밸브, 펌프, 의료기기
공구강
- 우수한 내마모성
- 절삭 공구, 다이, 펀치
초합금
- 높은 온도와 스트레스를 견딜 수 있음
- 터빈 블레이드, 항공우주 부품
티타늄
- 높은 중량 대비 강도 비율
- 항공우주 패스너, 생체의학 임플란트
알루미늄
- 가볍고 열전도율이 우수함
- 자동차 부품, 방열판
도자기
- 높은 경도, 내마모성 및 내식성
- 베어링, 씰, 갑옷 코팅
구형 형태는 기본 재료의 고유 특성 외에도 분말 충전 밀도와 흐름을 향상시킵니다.
제조방법
구형 분말을 생산하는 일반적인 방법:
가스 분무
- 불활성 가스 제트에 의해 용해 및 원자화되는 금속 합금
- 투자 비용 절감
- 10~150μm 크기 범위
플라즈마 원자화
- 플라즈마 에너지를 이용하여 용융 및 원자화
- 5μm까지 더 미세한 분말
- 더 높은 순도, 더 구형
에이가
- 원자화 챔버에서 유도 용융된 전극
- 미세한 액적의 급속한 응고
- 크기, 형태에 대한 제어
예습
- 플라즈마 토치로 녹인 회전 전극
- 미세한 분말로 원심분쇄
- 부드러운 구형
열 스프레이
- 고온 가스로 원자화된 공급원료 와이어/로드
- 산화물 분산 강화 합금
- 다른 방법보다 표면이 거칠다
사양
구형 분말의 일반적인 사양은 다음과 같습니다.
매개변수 | 사양 |
---|---|
입자 크기 | 10 - 150 μm |
파티클 모양 | 구형 |
유량 | 25 - 35 초/50g |
겉보기 밀도 | 40 – 60% |
탭 밀도 | 이론상 최대 90% |
표면 산화물 | 무게 기준 < 1% |
잔류가스 | 최소화 |
크기 분포, 높은 구형성, 매끄러운 표면 및 구성 요구 사항을 충족하는 것이 중요합니다. 크기가 작을수록 밀도가 향상되고 크기가 클수록 비용이 절감됩니다.
디자인 고려 사항
다음을 사용하는 부품의 주요 설계 요소 구형 분말:
- 치수 공차 – 소결 수축 계산
- 표면 마감 요구 사항 – 최소한의 후처리
- 기계적 특성 – 필요한 특성에 맞게 재료와 프로세스를 일치시킵니다.
- 생산 단가 – 성능과 비용의 균형을 맞추기 위한 부품 설계 최적화
- 보조 작업 – 큰 가공 여유 방지
- 조립 요구 사항 – 접합면, 연동 기능 설계
- 표준 준수 – 항공우주, 생물의학 등 응용분야
적층 제조와 같은 고급 제조 프로세스를 통해 구현되는 설계의 자유 덕분에 단조 금속으로는 불가능했던 더욱 최적화된 설계가 가능해졌습니다.
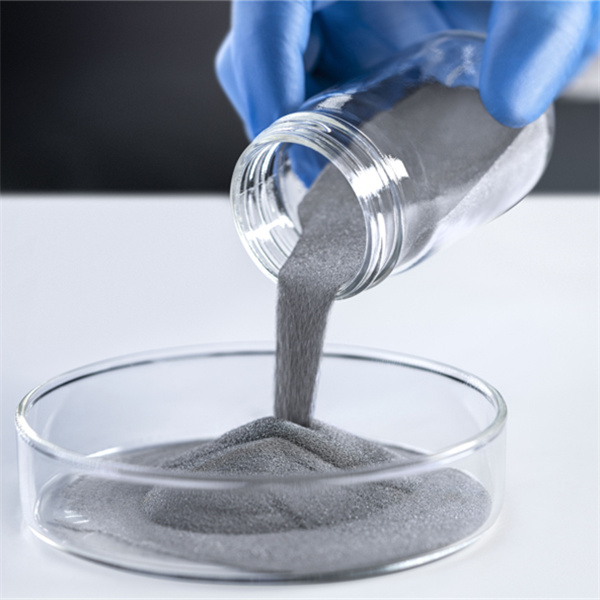
통합 프로세스
구형 분말에 적합한 일반적인 분말 통합 공정:
- 적층 제조 – 선택적 레이저 용융, 전자빔 용융 등은 최대의 유연성을 제공합니다.
- 금속 사출 성형 – 작고 복잡한 부품의 대량 생산
- 냉/열간 등압성형 – 순 모양 또는 거의 순 모양 부품을 생산합니다.
- 누르고 소결 – 성형과 소결을 결합한 기존 분말 야금 공정
- 열 스프레이 – 준비된 기판에 용융된 분말을 증착합니다.
- 슬러리 기반 방법 – 세라믹용 슬립캐스팅, 테이프캐스팅, 전기영동증착 등
구형 형태는 가공 중 분말 패킹 및 흐름을 개선하여 고밀도 및 균일한 미세 구조를 가능하게 합니다.
공급업체 및 가격
구형 분말의 주요 글로벌 공급업체는 다음과 같습니다.
공급업체 | 재료 | 가격 범위 |
---|---|---|
샌드빅 | 합금강, 스테인레스강 | $50-200/kg |
목수 첨가제 | 공구강, 초합금 | $70-250/kg |
회가나스 | 스테인리스 스틸 | $45-180/kg |
프렉스에어 | 티타늄, 초합금 | $100-350/kg |
LPW 기술 | 알루미늄 합금, 복합재 | $60-220/kg |
가격은 합금 구성, 품질, 로트 크기 및 구매 수량에 따라 다릅니다. 소량의 R&D 수량은 대량 생산 수량보다 비용이 더 많이 듭니다.
취급 및 보관
안전한 취급 및 보관에 대한 지침 구형 분말:
- 산화 및 오염을 방지하기 위해 밀봉된 용기를 서늘하고 건조하며 불활성인 대기에 보관하십시오.
- 분말 덩어리를 피하기 위해 습기에 대한 노출을 제한하십시오.
- 반응을 방지하기 위해 알루미늄 대신 연강이나 플라스틱 용기를 사용하십시오.
- 정전기 축적을 방지하기 위해 용기가 올바르게 접지되었는지 확인하십시오.
- 용기 및 분말은 운반 및 운반 중 입자 손상을 방지하기 위해 조심스럽게 다루십시오.
- 보관 및 취급 구역 근처에 스파크, 화염, 발화원을 피하십시오.
- 적절한 환기 및 집진 장비를 설치하십시오.
- 미세 분말 취급에 적합한 PPE(장갑, 호흡기, 보안경)를 사용하십시오.
적절한 절차는 통합 및 최종 부품 특성에 부정적인 영향을 미칠 수 있는 분말 특성 변화를 방지합니다.
장비 보수
주요 분말 처리 시스템에 대한 유지 관리 팁:
체:
- 찢어지거나 틈이 생기지 않도록 손상된 메쉬 스크린을 교체하십시오.
- 입자 손상으로 이어질 수 있는 막힘을 방지하기 위해 정기적으로 체를 청소하십시오.
- 진동 진폭 및 시간 설정을 확인하여 가공 경화를 방지하십시오.
호퍼 및 피더:
- 출구 포트에 축적물이 있는지 검사하고 흐름을 막는 재료를 제거하십시오.
- 안정적인 흐름을 보장하기 위해 피더 설정이 분말 특성과 일치하는지 확인하십시오.
- 호퍼 라이닝의 마모 여부를 점검하고 성능이 저하된 경우 교체하십시오.
혼합 용기:
- 분리 없이 균일한 혼합을 위해 마모된 배플과 강화 장치를 교체하십시오.
- 칼날 상태 점검 및 손상된 품목 수리/교체
- 작동 중 분말 누출을 방지하기 위해 개스킷 및 씰을 확인하십시오.
압형:
- 치수 정확도를 모니터링하고 필요에 따라 수리/교체
- 쉽게 릴리스할 수 있도록 일정에 따라 프레스 및 다이에 윤활유를 바르십시오.
- 용광로의 가열 요소 및 온도 제어 확인
선택 구형 분말 공급업체
공급업체 선택의 주요 요소:
- 기술 전문성 재료, 제조 공정, 부품 설계 등을 통해 고객을 지원합니다.
- 다양한 파우더 옵션 다양한 재료, 크기, 형태 및 코팅 포함
- 엄격한 품질 보증 화학 분석, 현미경 검사, 공정 제어 등을 다룹니다.
- 생산 능력 적시에 요구를 충족시키기 위해
- 제공되는 서비스 샘플링, 프로토타이핑, 테스트, 분석 등과 같은
- 업계 평판 고품질의 분말을 지속적으로 공급하기 위해
- 인증 ISO 9001, AS9100, ISO 13485 등과 같은
- 경쟁력 있는 가격 부가 가치 서비스 및 고객 지원과 결합
- 배송 및 물류 역량 최소한의 리드타임으로 적시 배송을 위해
올바른 파트너는 요구 사항에 맞는 구형 분말과 성공을 위한 기술 전문 지식을 모두 제공합니다.
장점과 한계
장점
- 우수한 분말 흐름 및 패킹 밀도
- 소결밀도 및 미세구조 개선
- 압축 중 내부 응력 감소
- 복잡한 형상을 제조할 수 있습니다.
- 일관된 금속학적 특성
- 소결 부품의 표면 조도가 우수함
제한 사항
- 불규칙한 분말보다 가격이 비쌉니다.
- 고급 제조 기술이 필요합니다
- 매우 미세한 분말에 사용 가능한 제한된 크기
- 입자 크기 분포를 제어하는 것이 어려울 수 있습니다.
- 일부 재료는 구형 분말로 원자화하기가 어렵습니다.
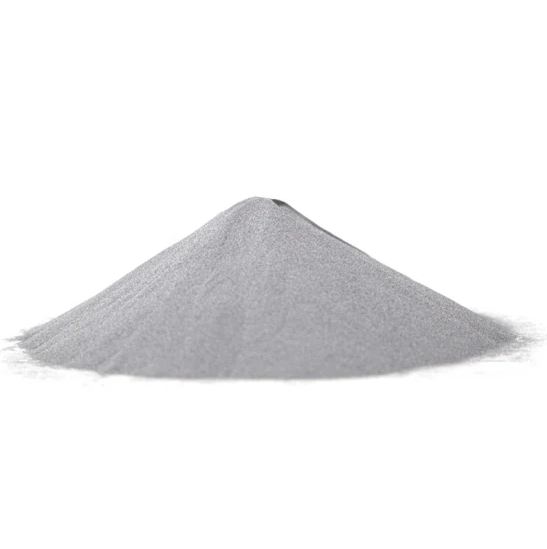
자주 묻는 질문
구형 분말을 사용하면 가장 큰 장점은 무엇입니까?
주요 이점은 취급 용이성을 위한 우수한 유동성, 향상된 압축을 위한 높은 패킹 밀도, 복잡한 형상을 가능하게 하는 낮은 입자 간 마찰 및 일관된 야금학적 특성입니다.
구형 분말로 일반적으로 사용 가능한 재료는 무엇입니까?
일반적인 재료에는 스테인리스강, 공구강, 초합금, 티타늄 합금, 알루미늄 합금, 니켈 기반 합금 및 세라믹 분말이 포함됩니다.
일반적으로 구형 분말을 사용하는 산업은 무엇입니까?
주요 산업에는 항공우주, 의료, 자동차, 방위, 에너지, 전자 및 산업 장비 제조가 포함됩니다.
구형 분말의 일반적인 크기 범위는 무엇입니까?
기존의 가스 원자화 구형 분말의 범위는 약 10-150 마이크론입니다. 특수 기술을 사용하면 서브미크론에서 나노 크기의 구형 분말을 생산할 수 있습니다.
구형 분말은 불규칙 분말에 비해 얼마나 비쌉니까?
구형 형태의 프리미엄은 일반적으로 불규칙한 분말에 비해 20-50%입니다. 그러나 이러한 이점으로 인해 중요한 애플리케이션에 대한 더 높은 비용이 정당화되는 경우가 많습니다.
결론
특징적인 둥근 모양과 매끄러운 표면으로 구형 분말 불규칙한 분말에 비해 더 높은 밀도와 우수한 흐름을 가능하게 합니다. 일관된 입자 특성은 다양한 금속과 세라믹에 탁월한 압축성, 압축성 및 소결성을 부여합니다. 원자화 공정의 지속적인 개발을 통해 이전보다 더 다양한 재료와 크기로 구형 분말을 사용할 수 있게 되었습니다. 구형 분말로 시작하는 이점을 최대한 활용하기 위한 부품 설계 및 공정 최적화를 통해 비용 효율적으로 고성능 부품을 생산할 수 있습니다.