개요
가스 분무는 고속 불활성 가스 분사를 사용하여 용융 금속 스트림을 미세한 구형 분말 입자로 분해하는 금속 분말 생산 방법입니다. 가스 분무는 가스 분무 프로세스 는 분말 입자 크기 분포, 형태, 순도, 미세 구조에 대한 탁월한 제어를 달성합니다.
가스 원자화 분말의 주요 특성으로는 구형 입자 모양, 고순도, 10미크론 이하의 미세한 크기, 균일한 조성을 들 수 있습니다. 가스 분무는 금속 사출 성형, 적층 제조, 분말 야금 압착 및 소결과 같은 고급 분말 기반 제조 기술을 용이하게 합니다.
이 가이드는 가스 분무 공정과 파우더에 대한 포괄적인 개요를 제공합니다. 분무 방법, 입자 형성, 공정 파라미터, 장비, 적용 가능한 합금, 분말 특성, 제품 사양, 응용 분야 및 공급업체를 다룹니다. 기술적인 세부 사항을 요약하는 유용한 비교표가 포함되어 있습니다.
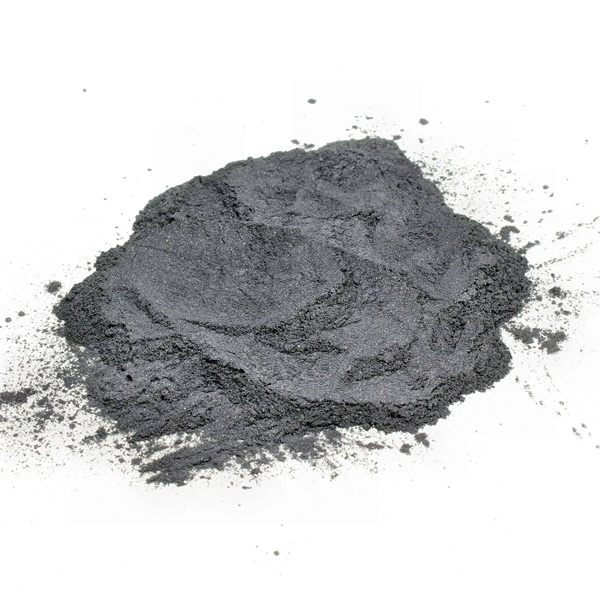
어떻게 가스 분무 프로세스 공장
가스 분무는 다음과 같은 기본 단계를 통해 용융 합금을 분말로 변환합니다:
가스 분무 공정 단계
- 녹는 - 유도 용광로에서 합금을 녹여 액상 온도 이상으로 과열합니다.
- 붓기 - 용융 금속 스트림이 분무 챔버에 부어집니다.
- 원자화 - 고속 불활성 가스 분사가 금속을 미세한 방울로 분해합니다.
- 고형화 - 금속 방울이 챔버를 통과하면서 빠르게 응고되어 분말 입자가 됩니다.
- 컬렉션 - 타워 하단의 사이클론 분리기에 수집된 분말 입자
핵심 현상은 가스 제트의 운동 에너지가 금속의 표면 장력을 극복하고 액체 흐름을 전단하여 방울로 만들 때 발생합니다. 이 방울은 구형 형태의 분말 입자로 얼어붙습니다.
세심한 공정 제어를 통해 분말 입자 크기, 순도 및 미세 구조를 맞춤화할 수 있습니다.
가스 분무 방법
산업에서 사용되는 가스 분무에는 크게 두 가지 방법이 있습니다:
가스 분무 방법
방법 | 설명 | 장점 | 제한 사항 |
---|---|---|---|
밀착형 원자화 | 용융물 주입점에 근접한 노즐 | 컴팩트한 디자인, 가스 사용량 감소 | 노즐로 인한 용융물 오염 가능성 |
자유 낙하 분무 | 주입 지점 아래에 위치한 노즐 | 용융물 오염 감소 | 더 높은 분무 타워 필요 |
밀착 결합 설계는 분무 가스를 재활용하지만 용융물이 산화될 위험이 있습니다. 자유 낙하 방식은 노즐 반응의 위험이 적고 더 깨끗한 분위기를 제공합니다.
추가 변형으로는 다중 가스 노즐, 초음파 분무, 원심 분무, 특수 애플리케이션을 위한 동축 노즐 설계 등이 있습니다.
가스 분무 노즐 설계
다양한 노즐 디자인으로 분무에 필요한 고속 가스 분사를 생성합니다:
가스 분무 노즐 유형
노즐 | 설명 | 가스 흐름 패턴 | 물방울 크기 |
---|---|---|---|
드 라발 | 수렴-발산 노즐 | 초음속 | 크고 넓은 분포 |
원뿔형 | 간단한 원뿔형 오리피스 | Sonic | Medium |
슬릿 | 길쭉한 슬릿 오리피스 | Sonic | Small |
여러 | 마이크로 노즐 어레이 | 음파/초음속 | 매우 작고 좁은 분포 |
드 라발 노즐은 기체 가속을 초음속으로 사용하지만 복잡한 형상을 가지고 있습니다. 단순화된 모양의 소닉 노즐은 더 많은 유연성을 제공합니다.
여러 개의 마이크로 노즐 또는 슬릿 구성을 사용하여 더 작은 액적과 엄격하게 제어된 크기 분포를 달성할 수 있습니다.
분말 형성 및 응고
용융 금속이 물방울로 전단되고 이후 응고되는 과정은 뚜렷한 메커니즘을 따릅니다:
파우더 형성 단계
- 헤어짐 - 레일리 제트 불안정성으로 인한 섭동 및 물방울 형성의 원인
- 왜곡 - 공기 저항력으로 인해 물방울이 인대로 길어지는 경우
- 파열 - 인대가 최종 크기에 가까운 물방울로 분해됩니다.
- 고형화 - 가스 접촉 및 방사선을 통한 빠른 냉각으로 고체 입자 형성
- 감속 - 입자가 분무 챔버를 통해 아래로 이동함에 따른 속도 손실
표면 장력, 난류, 공기 저항의 복합적인 효과에 따라 최종 입자 크기와 형태가 결정됩니다. 1,000,000°C/s 이상의 최대 입자 냉각 속도는 준안정 단계를 냉각시킵니다.
프로세스 매개변수
주요 가스 분무 프로세스 파라미터는 다음과 같습니다:
가스 분무 프로세스 매개변수
매개변수 | 일반적인 범위 | 파우더에 미치는 영향 |
---|---|---|
가스 압력 | 2-10 MPa | 압력을 높이면 입자 크기가 줄어듭니다. |
가스 속도 | 300-1200 m/s | 속도가 빠를수록 더 미세한 입자 생성 |
가스 유량 | 0.5-4 m3/min | 더 높은 처리량과 더 미세한 크기를 위한 흐름 증가 |
과열 녹이기 | 150-400°C | 더 높은 과열로 위성 감소 및 분말 흐름 개선 |
용융 주입 속도 | 10-150kg/분 | 낮은 주입 속도로 입자 크기 분포 개선 |
용융 스트림 직경 | 3~8mm | 스트림이 클수록 처리량 증가 |
이격 거리 | 0.3-1 m | 거리가 멀어질수록 위성 콘텐츠 감소 |
이러한 매개변수의 균형을 조정하면 파우더 입자 크기, 모양, 생산 속도 및 기타 특성을 제어할 수 있습니다.
가스 분무용 합금 시스템
가스 분무는 다음을 포함한 거의 모든 합금을 분말 형태로 가공할 수 있습니다:
가스 분무에 적합한 합금
- 티타늄 합금
- 니켈 초합금
- 코발트 초합금
- 스테인리스 스틸
- 공구강
- 저합금강
- 철 및 니켈 베이스 합금
- 귀금속
- 인터메탈릭
가스 분무는 분무 가스의 분해점보다 낮은 용융 온도가 필요합니다. 일반적인 가스에는 아르곤, 질소, 헬륨이 포함됩니다.
텅스텐과 같이 녹는점이 매우 높은 내화 합금은 분무하기가 어려울 수 있으며 특수 가공이 필요한 경우가 많습니다.
대부분의 합금은 미세하게 분산된 방울로 분무하기 위한 충분한 유동성을 유지하기 위해 용융 온도를 훨씬 상회하는 과열이 필요합니다.
가스 분무 분말의 특성
가스 분무 분말의 일반적인 특성:
가스 분무 분말 특성
특성 | 설명 | 중요성 |
---|---|---|
파티클 모폴로지 | 고도로 구형 | 뛰어난 유동성, 포장 밀도 |
입자 크기 분포 | 10-150μm 범위에서 조정 가능 | 프레스 밀도 및 소결 거동 제어 |
입자 크기 범위 | 촘촘한 분포 달성 가능 | 균일한 컴포넌트 속성 제공 |
화학적 순도 | 일반적으로 >99.5%(계획 합금 제외) | 노즐 반응으로 인한 오염 방지 |
산소 함량 | <1000 ppm | 고성능 합금에 필수 |
겉보기 밀도 | 최대 60%의 이론상 | 언론성 및 취급 표시 |
내부 다공성 | 매우 낮은 | 미세 구조의 균질성에 적합 |
표면 형태 | 일부 위성과 원활하게 연동 | 프로세스 안정성을 나타냅니다. |
구형이며 크기 분포를 조절할 수 있어 2차 분말 응집 공정에서 쉽게 사용할 수 있습니다. 산소와 화학 물질에 대한 엄격한 제어로 고성능 합금이 가능합니다.
가스 분무 분말 사양
국제 표준 사양을 정의하는 데 도움이 됩니다:
- 입자 크기 분포
- 겉보기 밀도 범위
- 홀 유량
- 허용 가능한 산소 및 질소 수준
- 허용되는 미세 구조 및 다공성
- 화학 성분 제한
- 샘플링 절차
이를 통해 품질 관리와 재현 가능한 파우더 동작을 지원합니다.
가스 분무 분말 사양
표준 | 재료 | 매개변수 | 테스트 방법 |
---|---|---|---|
ASTM B964 | 티타늄 합금 | 입자 크기, 화학, 미세 구조 | X-선 회절, 현미경 |
AMS 4992 | 항공우주 티타늄 합금 | 입자 크기, 산소 함량 | 체 분석, 불활성 가스 융합 |
ASTM B823 | 공구강 분말 | 겉보기 밀도, 유량 | 홀 유량계, 스콧 체적계 |
SAE AMS 5050 | 니켈 합금 | 입자 크기, 형태 | 레이저 회절, SEM |
MPIF 04 | 다양한 표준 합금 | 겉보기 밀도, 유량 | 홀 유량계, 탭 밀도 |
사양은 항공우주, 자동차, 의료 및 기타 품질 중심 산업의 중요한 애플리케이션 요구 사항에 맞게 조정되었습니다.
가스 분무 분말의 응용 분야
가스 분무 분말을 통해 고성능 부품을 제조할 수 있습니다:
- 금속 사출 성형(MIM)
- 적층 제조(AM)
- 열간 등방성 프레스(HIP)
- 분말 단조
- 열 및 냉수 스프레이
- 분말 야금 압착 및 소결
가공 재료 대비 이점:
- 미세한 특징이 있는 복잡한 지오메트리
- 우수한 기계적 성질
- 거의 완전한 밀도 통합
- 새로운 맞춤형 합금
- 다양한 소재 옵션
가스 분무는 산업 전반에 걸쳐 높은 품질 표준을 갖춘 복잡한 부품의 자동 공정에 최적화된 구형의 유동 분말을 생산하는 데 탁월합니다.
가스 분무 분말의 글로벌 공급업체
가스 분무 분말의 저명한 글로벌 공급업체는 다음과 같습니다:
가스 분무 분말 제조업체
회사 | 재료 | 기능 |
---|---|---|
ATI 파우더 메탈 | 티타늄, 니켈, 공구강 합금 | 광범위한 합금 범위, 대용량 |
프렉스에어 표면 기술 | 티타늄, 니켈, 코발트 합금 | 다양한 합금 선택, 통행료 처리 |
샌드빅 오스프리 | 스테인리스강, 저합금강 | 철 소재 전문가 |
회가나스 | 공구강, 스테인리스강 | 맞춤형 합금, 적층 제조 분말 |
목수 첨가제 | 티타늄, 니켈, 코발트 합금 | 맞춤형 합금, 특수 입자 크기 |
소규모 지역 공급업체도 가스 분무 분말을 제공하며, 틈새 합금이나 응용 분야에 서비스를 제공하는 경우가 많습니다.
또한 많은 공급업체가 체질, 혼합, 코팅 및 기타 분말 후처리 작업을 수행합니다.
가스 분무의 장점과 한계
가스 원자화 - 장단점
장점 | 제한 사항 |
---|---|
구형 분말 형태 | 더 높은 초기 자본 비용 |
제어된 입자 크기 분포 | 고순도 불활성 가스 필요 |
다양한 합금 시스템에 적용 가능 | 분무가 까다로운 내화 합금 |
깨끗한 분말 화학 및 미세 구조 | 노즐 침식 발생 가능 |
신속한 분말 담금질로 준안정상 보존 | 액체보다 훨씬 높은 용융 과열이 필요합니다. |
연속 분말 생산 프로세스 | 분말 모양으로 인한 그린 강도 제한 |
가스 분무 분말의 구형과 미세한 크기는 뚜렷한 이점을 제공하지만 단순한 기계적 분쇄 공정에 비해 운영 비용이 더 많이 듭니다.
가스 분무 분말 선택
가스 분무 분말을 선택할 때 고려해야 할 주요 사항:
- 원하는 화학 및 합금 구성
- 목표 입자 크기 분포
- 적합한 겉보기 및 탭 밀도 범위
- 애플리케이션에 따른 산소 및 질소 제한 사항
- 자동화된 분말 처리를 위한 흐름 특성
- 대표성 확보를 위한 샘플링 절차
- 공급업체 기술 전문성 및 고객 서비스
- 총 비용 고려 사항
프로토타입 빌드를 테스트하면 새로운 합금과 가스 분무 분말을 애플리케이션에 맞게 검증하는 데 도움이 됩니다. 파우더 생산업체와 긴밀히 협력하면 최적화가 가능합니다.
자주 묻는 질문
가스 분무가 생성할 수 있는 가장 작은 입자 크기는 얼마입니까?
특수 노즐은 1~5미크론까지 한 자릿수 미크론 분말을 생산할 수 있습니다. 그러나 초미세 분말은 겉보기 밀도가 매우 낮고 입자 간 반데르발스 힘이 강하기 때문에 세심한 취급이 필요합니다.
가스 분무 시 분말 위성의 원인은 무엇인가요?
새틀라이트는 방울이 너무 크거나 충돌하여 완전히 응고되기 전에 부분적으로 다시 결합할 때 형성됩니다. 더 높은 과열, 더 낮은 주입 속도, 더 긴 분리 거리는 모두 새틀라이트 감소에 도움이 됩니다.
가스 분무에 고순도 불활성 가스가 필요한 이유는 무엇인가요?
고속 가스 분사는 시간이 지남에 따라 노즐에서 금속을 침식하고 파우더를 오염시킬 수 있습니다. 질소 및 산소와 같은 반응성 가스도 파우더 순도와 합금 성능에 부정적인 영향을 미칩니다.
가스 분무는 물 분무와 어떻게 다른가요?
물 분무는 일반적으로 50~150미크론의 더 큰 크기에서 더 불규칙한 분말을 생산합니다. 가스 분무는 프레스 및 소결 응용 분야에 선호되는 구형 형태를 가진 10마이크론 이하의 미세한 크기를 가능하게 합니다.
원심분무란 무엇인가요?
원심 분무에서는 용융 금속을 회전하는 디스크에 부어 분말로 응고되는 미세한 용융 금속 방울을 떨어뜨립니다. 이 방법은 가스 분무보다 생산 속도가 빠르지만 분말 크기와 모양 제어가 어렵습니다.
가스 분무 중에 합금을 빠르게 전환할 수 있나요?
예, 특수 장비를 사용하면 용융 스트림을 빠르게 변경하여 복합 및 합금 분말을 생산할 수 있습니다. 그러나 챔버 퍼징을 통해 합금 간의 교차 오염을 최소화해야 합니다.
결론
가스 분무 공정은 입자 크기 분포, 순도 및 미세 구조 특성이 엄격하게 제어된 구형의 유동성 금속 분말을 생산하여 중요 응용 분야의 고급 분말 통합 공정에 최적화되어 있습니다. 공정 파라미터와 특수 노즐 설계를 신중하게 조작하여 최종 분말 특성을 광범위하게 제어할 수 있습니다. 지속적인 개발을 통해 가스 분무는 엔지니어가 창의적이고 새로운 방식으로 고성능 부품을 제조할 수 있는 능력을 향상시킵니다.