개요
High temperature iron powders are specialized metallic powders made from iron-based alloys designed to operate at elevated temperatures exceeding 850°C without rapidly losing strength. Conventional iron and steel powders oxidize and deteriorate faster beyond this threshold.
By carefully tailoring powder chemistry and processing treatments, high temperature strength and environmental resistance is enhanced. Key application areas demanding such extreme thermal structural materials include automotive, aerospace, power generation equipment and chemical processing industries.
종류 High Temperature Iron Powders
Various alloying additions can improve high heat properties:
합금 유형 | Main Alloying Elements | Max Use Temperature |
---|---|---|
Austenitic stainless steels | Ni, Cr, Mn | 950°C – 1050°C |
High nickel iron alloys | Ni, Co, Mo | 1000°C – 1200°C |
Oxide dispersion strengthened | Y2O3 additions | 1050°C – 1150°C |
Iron-aluminides | Al, Cr, Ti, Si | 750°C – 950°C |
Production Methods for High Temperature Powders
- Gas atomization with controlled rapid cooling
- 물 분무
- Plasma spheroidization to round irregular powders
- Carbonyl iron process for stainless steel powders
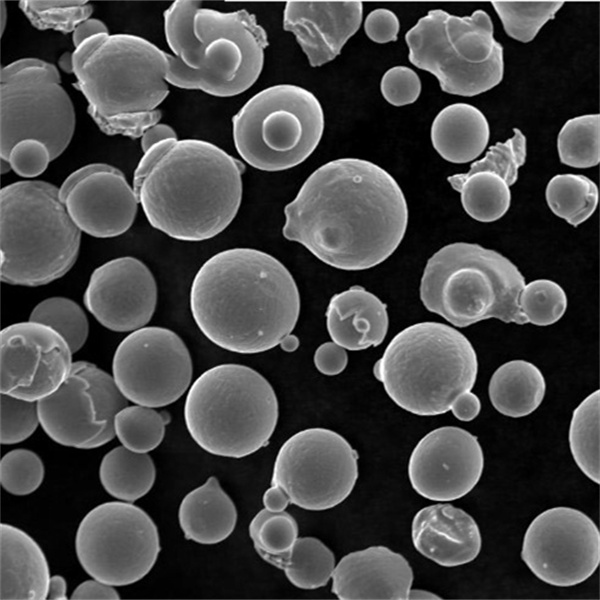
Alloy Types and Compositions
There are four primary categories of specialty iron alloy powders designed for prolonged use at temperatures exceeding 850°C:
Austenitic Stainless Steel Powders
Alloys like 316L, 304L, and 301L stainless steels contain nickel to maintain an austenitic FCC crystal structure up to 1100°C and chromium for oxidation resistance through protective chromia (Cr2O3) surface films at high temperatures.
합금 원소 | 역할 | Weight % Range |
---|---|---|
니켈(Ni) | 오스테나이트 안정제 | 8 – 12% |
크롬(Cr) | 내산화성 | 16 – 18% |
망간(Mn) | Strength and grain refinement | 최대 2% |
질소(N) | 강하게 하는 것 | 0.1 – 0.25% |
혜택: Excellent “hot strength”, ease of compaction and sintering, lower cost than superalloys.
제한 사항: Prone to creep above 1000°C, not suitable for load bearing dynamic applications.
High Nickel Iron Alloys
Nickel-iron alloys containing 25 – 60 wt% nickel offer the optimum combination of high temperature strength, toughness and corrosion resistance. Nickel additions dramatically slow down diffusion rates and reduce detrimental microstructural changes up to 1150°C.
Other key alloying elements are:
합금 원소 | 역할 | Weight % Range |
---|---|---|
니켈(Ni) | 견고한 솔루션 강화 | 25 – 60% |
크롬(Cr) | 내산화성 | 10 – 25% |
코발트 (Co) | Enhances high temperature mechanical properties | 10 – 25% |
몰리브덴(Mo) | 크리프 저항 | 2 – 6% |
혜택: Unmatched mechanical performance at 1100°C+, slower degradation kinetics. Thermally stable microstructure.
제한 사항: Very high alloy prices, porosity control difficulties, requiring HIP densification.
Oxide Dispersion Strengthened Iron Alloys
In oxide dispersion strengthened alloys, very fine (50-100 nm) inert yttrium oxide particles are embedded within the material matrix. These nano-scale oxides hinder dislocation motion thereby maintaining strength above 1000°C.
합금 원소 | 역할 | Weight % Range |
---|---|---|
Yttrium oxide (Y2O3) | Nano-oxide particles providing thermal stability | 0.25% – 1% |
크롬(Cr) | Environmental resistance | Up to 20% |
알루미늄(Al) | Enhances oxide dispersion | Up to 4% |
혜택: Exceptional microstructural stability and creep strength at 1100°C+ operating conditions.
제한 사항: Very high cost, processing difficulties – traditionally made through mechanical alloying and consolidation.
Iron Aluminide (FeAl) Alloys
Iron aluminide alloys having 10- 40% aluminum content offer excellent oxidation and sulfidation resistance up to 900°C through the formation of a durable alumina (Al2O3) protective top layer. Chromium aids surface protection.
합금 원소 | 역할 | Weight % Range |
---|---|---|
알루미늄(Al) | 내산화성 | 10 – 40% |
크롬(Cr) | Enhances environmental resistance | 5 – 10% |
Carbon, Zr (C, Zr) | Carbide strengtheners | Up to 0.5% |
혜택: Great environmental stability, lower densities than steels, ease of fabrication relative to superalloys.
제한 사항: Strength loss above 750°C, poor creep resistance, applied stresses increase pest phenomena.
생산 방법
Special techniques are utilized to produce tailored high temperature iron alloy powders with suitable characteristics:
가스 분무
- Controlled rapid cooling of the molten metal stream enables retention of alloying elements in solution rather than formation of precipitates
혈장 스페로이드화
- Irregular powders from water atomization processes are re-melted using a plasma torch and re-solidified into spherical powders ideal for AM methods
Multiple Cycles Sinter-Crush
- Powders are repeatedly compacted at high temperatures, crushed and sieved to refine powder distribution ideal for MIM processability
기계적 합금
- Ball milling elemental metal powders creates nano-dispersed particle and cluster distributions in ODS alloys
Carbonyl Refining
- Produces extremely high purity metal powders when lower cost production methods yield contamination
Comparison of Production Methods
방법 | 순도 수준 | 산소 함량 | Morphology Options | Throughput (tons/year) |
---|---|---|---|---|
가스 분무 | 보통 | <1000 ppm | 대부분 구형 | High >20,000 |
물 분무 | 낮음 | 2000-4000 ppm | 불규칙 | Very high >50,000 |
혈장 스페로이드화 | Medium | 500-2000 ppm | 구형 | Low <5,000 |
기계적 합금 | 높음 | <1500 ppm | Variable particle shapes | Low hundreds |
카보닐 공정 | Extremely High | <200 ppm | Spherical/nodular | High >25,000 |
특성화 방법
Several analytical methods are vital for qualifying high temperature powder alloys:
화학 성분
- Spectrographic and wet chemistry techniques identify elemental constituents and quantities – necessary for alloy design verification
- Carbon, sulfur, oxygen, nitrogen contents show process-induced contamination that impacts material performance
입자 크기 및 형태
- Laser diffraction particle size analyzers determine full granulometry from 10 nm to 3 mm sizes
- SEM imaging visualizes shape, surface features, satellite particles, porosity useful for build process suitability assessments and defect analysis
Crystallography
- XRD shows phases present, precipitation states, quantitative analysis of crystalline properties
- Assesses effects of thermal exposure on phase fractions by microstructural evolution
Powder Properties Testing
- Hall flowmetry, apparent density and compressibility quantify powder behavior for ease of handling and consolidation
응용 프로그램 및 용도
The unique high strength, creep resistance and slow degradation kinetics of designed high temperature iron alloys powders make them critical for harsh prolonged thermal loading situations like:
Jet Engine and Land Based Turbine Components
- Stainless steels or high nickel alloy discs, shafts, casings, gears, valves facing 900 – 1200°C
Nuclear and Solar Power Plant Parts
- High nickel steel bolts, heat shields, headers, tubing, collector panels resisting temperatures exceeding 1000°C + corrosion
Automotive and Aerospace Components
- Stainless steel turbocharger wheels boosting performance in internal combustion engines
Petrochemical Refining and Cracking Equipment
- Stainless steel heat exchangers, recuperators, furnace trays resisting warping and failure up to 1100°C
In addition, iron aluminides present excellent candidates for replacing stainless steels and superalloys by offering unique environmental resistance benefits over conventional alloys in biological, chemical processing or electrical systems facing aggressive oxidation, carburization and chloride induced corrosion attack mechanisms.
사양 및 등급
High temperature powder alloys must meet minimum specifications for chemistry, cleanliness, particle characteristics and properties:
Alloy Grade Compositions
합금 유형 | Applicable Specifications | Grade Examples |
---|---|---|
Austenitic Stainless Steels | AMS 5759, ASTM B898 | Custom 316L, 301L, 310L |
High Nickel Iron Alloys | AMS 5383, ASTM B162 | IN625, HastelloyTM X , Nimonic® 80A |
Oxide Dispersion Strengthened | ASTM B937, B934 | MA956, PM2000 |
Iron Aluminides | ASTM C1072 | Custom FeAl grades |
Critical Parameters and Thresholds
매개변수 | Thresholds | Test Methods |
---|---|---|
산소 함량 | <4000 ppm | 불활성 가스 융합 |
질소 함량 | <1500 ppm | 불활성 가스 융합 |
평균 입자 크기 | Application specific, customized | 레이저 회절 |
겉보기 밀도 | >2.5g/cm3 초과 | Hall flowmeter funnels |
탭 밀도 | >3.5 g/cm3 | Scott volumeter tests |
유량 | >23 s/50 g | Hall flowmeter tests |
Purchasers work with reputable powder producers to define application-specific characterization needs and property goals reflecting service conditions and production process requirements.
비용 분석
Prices for specialty high temperature iron alloy powders meant for service >850°C depend heavily on:
1. Base Material
- Stainless steels offer lowest costs while superalloys are most expensive
2. Alloying Additions
- Nickel, cobalt and specialized elements like rhenium drastically increase material expense
3. Production Method
- Water atomization and carbonyl processes enable higher volumes and lower pricing
4. Additional Processing
- Additional powder property enhancements increase cost
5. Order Quantities
- Larger batch sizes can decrease unit pricing
합금 등급 | 가격 견적 | Cost Factors |
---|---|---|
316L 스테인리스 스틸 | $15 – $30 per kg | Low alloy costs, high production rate processes |
Custom High Nickel Alloys | $50 - $250 kg당 | High value elements, lower volume production |
Oxide Dispersion Strengthened | $250 - $1000 kg당 | Low batch sizes, specialized mechanical alloying process |
Iron Aluminides | $30 – $100 per kg | Lower aluminum and chromium content versus superalloys |
Contact reputable suppliers like Sandvik Osprey, Hoganas, Carpenter Technologies to request specific price quotations.
Pros and Cons of High Temperature Iron Alloys
혜택 및 장점
Tunable Chemistry and Properties
- Allows customization of powder composition and characteristics for given service needs
Economic Production Scalability
- Mature large volume manufacturing methods available
Fabrication Route Flexibility
- Compatible with metal AM, MIM and press and sinter techniques
Favorable Cost Economics
- Avoid precious elements making superalloys considerably more expensive
Challenges and Disadvantages
Property Optimization Complexity
- Improving one characteristic like high conductivity can negatively impact another like strength
Melting Point Limitations
- Maximum capability typically capped at 1150°C for constituent particle stability
Post Processing Requirements
- Nearly full density and superior properties demand hot isostatic pressing and heat treatments
Limited High Stress-Exposure Resilience
- Creep resistance inferior to Ni, Co or ceramic-based alloys
Here is a comparison between high temperature stainless steel powders versus alternatives:
매개변수 | High Temp Stainless Steels | 니켈 초합금 | Ceramic Composites |
---|---|---|---|
융점 | 1400°C | 1350°C | >1800°C |
밀도 | 7.5 – 8 g/cm3 | 8 – 9 g/cm3 | >4g/cm3 |
비용 | $ | $$$$$ | $$$ |
열 전도성 | 더 나은 | Worse | 유사 |
Environmental Resistance | 양호 | 더 나은 | 최고 |
Ease of Fabrication | 우수 | 보통 | Poor |
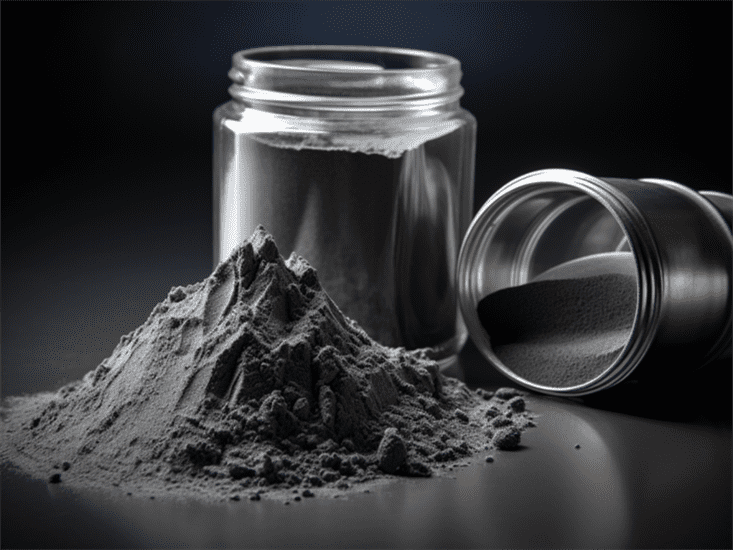
자주 묻는 질문
Q: What is the typical particle size distribution used for high temperature stainless steel powders in metal AM?
A: For powder bed fusion processes like selective laser melting (SLM) and electron beam melting (EBM), the common range is 15 μm – 45 μm size fractions. Finer distributions can improve resolution but impair powder spreading during layer deposition and reduce flow characteristics.
Q: What gas atomization cooling rates preserve optimal alloy powder compositions?
A: For the best combination of chemistry retention and appropriate powder morphology, solidification rates between 1000 – 3000°C per second are widely used for high temperature stainless steel and superalloy powders.
Q: Why are high levels of oxide particles detrimental in high temperature iron alloys?
A: During service, oxides present can coarsen and migrate forming less protective and less stable oxide populations resulting in accelerated attack from oxidizing, sulfidizing, carburizing or chlorinating environments – reducing component life. Careful determination and control of oxygen levels based on maximum exposure temperatures and operating conditions is necessary in alloy development.
Q: What methods can be used to increase powder densities to >95% theoretical?
A: Hot isostatic pressing is commonly applied on high temperature stainless steel or superalloy components after initial AM or MIM fabrication to eliminate residual pores, creating material performance close to that of wrought alloys in the same strengthened heat treated states. Near theoretical densities ensure mechanical robustness.
Q: Why is nitrogen control below 1000 ppm critical in high strength high conductivity copper alloys?
A: Nitrogen pickup deleteriously forms very hard, brittle nitride phases that drastically lower thermal and electrical conductivities reducing functionality in thermal management applications, while also decreasing formability and ductility during manufacture.