Gambaran umum tentang Teknologi MIM
Metal injection molding (MIM), juga dikenal sebagai powder injection molding (PIM), adalah proses manufaktur tingkat lanjut yang digunakan untuk memproduksi komponen logam yang kecil dan kompleks dalam volume yang tinggi.
MIM memadukan fleksibilitas desain dan presisi cetakan injeksi plastik dengan kekuatan dan performa komponen logam mesin. Hal ini memungkinkan produksi komponen rumit yang hemat biaya dengan sifat mekanik yang baik dari paduan logam canggih.
Proses MIM dimulai dengan bahan baku yang terbuat dari serbuk logam halus yang dicampur dengan bahan pengikat. Bahan baku ini kemudian diinjeksikan ke dalam cetakan menggunakan peralatan cetakan injeksi plastik. Bahan pengikat menyatukan serbuk logam dan memberikan kemampuan mengalir untuk pencetakan.
Setelah pencetakan, pengikat dikeluarkan dari bagian hijau yang dicetak melalui proses debinding. Bagian yang dilepaskan, yang disebut bagian cokelat, kemudian disinter pada suhu tinggi yang menyatukan partikel-partikel logam menjadi bagian logam padat dengan sifat material yang mendekati sifat material bagian tempa.
MIM cocok untuk membuat komponen kecil dan kompleks menggunakan berbagai logam seperti baja tahan karat, baja paduan rendah, baja perkakas, paduan magnetik, superalloy, paduan titanium, dan paduan berat tungsten. Ini menggabungkan keserbagunaan cetakan injeksi plastik dengan fleksibilitas material metalurgi serbuk.
Manfaat utama dari teknologi MIM antara lain:
- Kemampuan produksi volume tinggi untuk komponen logam yang rumit dan terperinci
- Manufaktur dengan bentuk hampir bersih mengurangi limbah dan meminimalkan pemesinan
- Sifat mekanik yang baik mendekati material tempa
- Berbagai pilihan logam termasuk baja tahan karat, baja perkakas, paduan super
- Memungkinkan konsolidasi suku cadang menjadi komponen tunggal
- Biaya unit yang rendah karena volume yang tinggi
- Konsistensi dan pengulangan dari proses otomatis
Teknologi MIM sangat ideal untuk komponen kecil dan kompleks seperti perangkat medis, komponen senjata api, komponen jam tangan, dan komponen otomotif yang membutuhkan presisi, kekuatan, ekonomi, dan skala produksi massal.
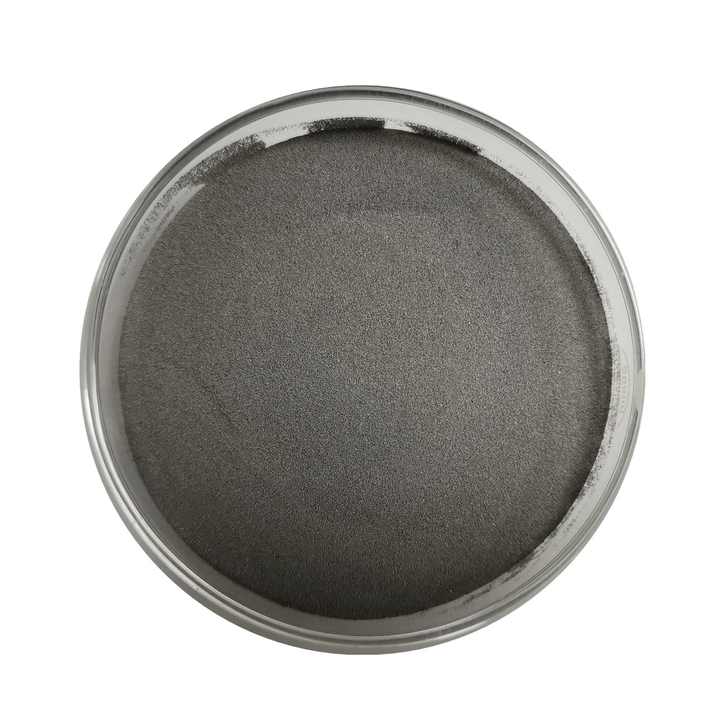
Aplikasi dan Penggunaan Teknologi MIM
Teknologi MIM digunakan di berbagai industri untuk memproduksi komponen logam presisi tinggi berukuran kecil secara efisien dalam volume besar. Berikut ini adalah beberapa area aplikasi utama dan penggunaan teknologi MIM:
Industri | Aplikasi dan Penggunaan |
---|---|
Kedokteran dan Kedokteran Gigi | Instrumen bedah, implan gigi, implan ortopedi, komponen kateter, kanula jarum, gagang pisau bedah, forsep, klem, pengencang bedah, instrumen bedah yang dapat digunakan kembali |
Senjata Api dan Pertahanan | Pemicu, palu, pengaman, ejektor, magasin, selongsong bekas, proyektil, komponen hulu ledak |
Otomotif | Komponen sistem bahan bakar, roda gigi pompa oli, impeler, katup, suku cadang turbocharger, suku cadang elektronik, komponen kemudi/transmisi |
Dirgantara | Bilah turbin, impeler, gigi roda gigi, bushing, komponen pompa, suku cadang mesin |
Produk Konsumen | Komponen jam tangan, temuan perhiasan, alat makan, gunting, pisau cukur, perkakas tangan, komponen ritsleting |
Perangkat Keras Industri | Kenop, alat kelengkapan, pengencang, soket, konektor, alat penyiram, nozel |
Elektronik | Konektor, sakelar, mikromotor, roda gigi mikro, masker penyaringan, induktor, rotor magnet |
** Keunggulan MIM untuk Aplikasi Tertentu***.
- Presisi: Ideal untuk komponen miniatur seperti perangkat medis atau komponen jam tangan dengan geometri yang rumit.
- Kekuatan: Cocok untuk komponen yang membutuhkan kekuatan tinggi seperti turbocharger otomotif dan pemicu senjata api.
- Ketahanan aus: Suku cadang MIM yang terbuat dari paduan baja perkakas memiliki ketahanan aus yang sangat baik untuk masa pakai yang lama.
- Ketahanan Korosi: Komponen MIM baja tahan karat tahan terhadap korosi untuk alat bedah, implan, dll. yang dapat digunakan kembali.
- Kekerasan Tinggi: MIM dapat menghasilkan komponen dengan kekerasan lebih dari 40 HRC seperti peralatan makan, perkakas, cetakan, dll.
- Properti Listrik: MIM digunakan untuk membuat komponen magnetik lunak seperti induktor, rotor motor, dll.
- Hemat Biaya: Volume yang tinggi mengurangi biaya suku cadang secara substansial dibandingkan dengan pemesinan.
Panduan Peralatan dan Perkakas MIM
Peralatan utama yang digunakan dalam proses MIM meliputi mesin cetak injeksi, debinding dan tungku sintering. Berikut ini adalah ikhtisarnya:
Peralatan | Tujuan | Pertimbangan |
---|---|---|
Mesin Cetak Injeksi | Untuk menyuntikkan bahan baku MIM ke dalam rongga cetakan di bawah panas dan tekanan | Gaya penjepitan cetakan, laju injeksi dan kapasitas tekanan, presisi dan pengulangan, fitur kontrol dan otomatisasi. |
Oven Penghilang Pengikat | Untuk menghilangkan pengikat secara termal atau kimiawi dari bagian yang dicetak | Kisaran suhu, kontrol atmosfer, kapasitas pemuatan, keseragaman pengikatan. |
Tungku Sintering | Untuk memadatkan bagian coklat yang terlepas dengan memanaskan hingga mendekati titik leleh | Kisaran suhu, kontrol atmosfer, keseragaman pemanasan, kapasitas batch, lebih disukai yang sepenuhnya otomatis. |
Cetakan dan perkakas | Membentuk rongga untuk membentuk bahan baku MIM menjadi geometri yang dibutuhkan | Tahan terhadap tekanan dan suhu cetakan, mesin presisi, permukaan akhir yang baik, memungkinkan pemanasan/pendinginan yang cepat. |
Peralatan Bahan Baku | Untuk mencampur bubuk logam dan pengikat menjadi bahan baku MIM yang homogen | Mixer, pengontrol suhu, pelet. |
Pemrosesan Sekunder | Langkah-langkah tambahan seperti pemesinan, penyambungan, perawatan permukaan | Sesuai kebutuhan bagian seperti pemesinan CNC, pengelasan, EDM, pelapisan. |
Kontrol Kualitas | Untuk menguji bahan baku, properti komponen yang disinter | Morfologi serbuk, densitas, laju alir, analisa viskositas, peralatan pengujian mekanis. |
Peralatan Keselamatan | Untuk menangani serbuk halus dengan aman | Sarung tangan, respirator, sistem pengumpulan debu. |
Standar Desain dan Kinerja
- ISO 21227 - Serbuk untuk cetakan injeksi logam
- ASTM F2885 - Proses Pencetakan Injeksi Logam
- MPIF 35 - Standar untuk bahan baku MIM
- ASTM E2781 - Desain Spesimen Uji Tarik MIM
- ISO 2740 - Bagian Cetakan Injeksi Logam Sinter
Perincian Biaya
Distribusi biaya yang umum dalam produksi MIM adalah:
- Bahan Baku (Bubuk + Pengikat): 50-60%
- Manufaktur (Pencetakan + Pengikatan + Sintering): 25-35%
- Pemrosesan Sekunder: 5-10%
- Kontrol Kualitas: 2-5%
- Rekayasa (R&D, Desain): 2-5%
Pemasok dan Harga
Berikut ini adalah beberapa pemasok global terkemuka untuk peralatan MIM dan kisaran harganya:
Pemasok | Kategori Produk | Kisaran Harga |
---|---|---|
ARBURG | Mesin cetak injeksi | $100,000 – $500,000 |
MIM Indo-AS | Bahan baku & layanan MIM | $5 - $50 per Kg |
Elnik | Tungku pengikatan dan sintering | $50,000 – $1,000,000 |
FineMIM | Produksi MIM dari ujung ke ujung | $0.5 - $5 per bagian |
Parmatech | Atomisasi bubuk logam | $250,000 – $1,000,000 |
Meridian Technologies | Desain perkakas dan cetakan | $5,000 – $100,000 |
Pemasangan, Pengoperasian dan Pemeliharaan
MIM adalah proses otomatis, tetapi memerlukan pemasangan, pengoperasian dan pemeliharaan yang cermat untuk performa yang optimal:
Aktivitas | Detail |
---|---|
Instalasi | Penyelarasan presisi mesin cetak injeksi dan cetakan. Kalibrasi pengontrol suhu. Uji coba dengan batch percobaan. |
Operasi | Memastikan kontrol kualitas bahan baku sesuai standar. Mencapai parameter proses seperti tekanan injeksi, suhu, dan kecepatan. |
Pemeliharaan | Jadwalkan pemeliharaan preventif untuk barel, sekrup, cetakan mesin cetak. Pertahankan atmosfer tungku yang tidak mengikat. Mengkalibrasi instrumen. |
Pembersihan | Ikuti SOP untuk pembersihan barel mesin setelah dijalankan. Pastikan tidak ada penumpukan serbuk di dalam tungku atau saluran. Pembersihan cetakan dengan media yang dirancang. |
Keamanan | Kenakan alat pelindung diri saat menangani serbuk halus. Pembuangan bahan pengikat kimia dengan benar. Biarkan tungku mendingin sebelum perawatan. |
Pelatihan | Melatih operator alat berat dan tungku tentang prosedur. Mengadakan sesi penyegaran tentang keselamatan dan pemeliharaan. |
Optimalisasi | Menyesuaikan parameter proses hingga kualitas komponen stabil dalam spesifikasi. Menyimpan catatan proses yang terperinci. |
Aktivitas dan Frekuensi Pemeliharaan Umum
Aktivitas | Frekuensi |
---|---|
Pembersihan nosel mesin cetak injeksi | Setelah setiap batch |
Pemolesan cetakan | Mingguan |
Pembersihan barel mesin | Bulanan |
Pemeriksaan atmosfer oven penghilang pengikat | Bulanan |
Kalibrasi termokopel tungku sintering | 6 bulan |
Studi aliran cetakan | Setiap tahun |
Bagaimana Memilih Pemasok MIM
Memilih pemasok MIM yang kompeten sangat penting untuk mendapatkan suku cadang berkualitas baik tepat waktu dengan biaya yang wajar. Berikut adalah faktor-faktor penting yang perlu dipertimbangkan:
Faktor | Kriteria |
---|---|
Kemampuan Teknis | Peralatan canggih, pengalaman bertahun-tahun, keahlian teknis |
Opsi Bahan | Berbagai bahan seperti baja tahan karat, baja perkakas, paduan tungsten |
Pemrosesan Sekunder | Fasilitas pemesinan, penyambungan, dan pelapisan in-house |
Sistem Kualitas | Sertifikasi ISO 9001, kontrol kualitas dan prosedur inspeksi |
Kapasitas Produksi | Kemampuan produksi volume tinggi untuk stabilitas |
Waktu Pimpin | Waktu penyelesaian yang cepat dari desain hingga pengiriman |
Lokasi | Kedekatan geografis untuk efisiensi logistik |
Biaya | Model penetapan harga - harga per bagian lebih disukai |
Layanan Pelanggan | Responsif terhadap pertanyaan, dukungan teknis, manajemen proyek |
Pertanyaan untuk Ditanyakan kepada Calon Pemasok MIM
- Bahan dan ukuran komponen apa yang Anda miliki?
- Apakah Anda menawarkan pemrosesan sekunder seperti pemesinan atau pelapisan?
- Sertifikasi kualitas dan prosedur inspeksi apa yang diikuti?
- Bagaimana cara penanganan bahan sensitif seperti paduan titanium atau tungsten karbida dilakukan?
- Berapa volume produksi yang dapat Anda hasilkan dengan andal setiap bulannya?
- Bagaimana cara meminimalkan sisa dan memaksimalkan hasil panen?
- Apakah variabilitas bagian per bagian dalam dimensi dan properti?
- Bagaimana pengoptimalan desain dilakukan untuk proses MIM?
- Laporan kualitas dan bagan kendali apa yang akan disediakan?
Membandingkan MIM dengan Proses Lainnya
Perbandingan antara MIM dan proses manufaktur logam lainnya:
Proses | Keuntungan | Kekurangan |
---|---|---|
MIM | Geometri yang kompleks, produksi massal, bentuk hampir bersih, pilihan material yang luas | Investasi perkakas di muka, keterbatasan ukuran |
Mesin CNC | Fleksibilitas material, perputaran prototipe yang cepat | Kompleksitas terbatas, volume lebih rendah |
Pengecoran Logam | Biaya suku cadang rendah, volume tinggi | Keterbatasan bentuk, kekuatan yang lebih rendah |
Stamping Logam | Kecepatan tinggi, volume tinggi, biaya rendah | Hanya cocok untuk geometri 2D |
Pencetakan 3D | Kebebasan desain, pembuatan prototipe yang cepat | Kekuatan lebih rendah, biaya lebih tinggi, ukuran dan bahan terbatas |
Manfaat MIM dibandingkan Pemesinan
- Pemanfaatan material yang lebih tinggi dengan bentuk yang hampir bersih
- Tidak ada pemesinan yang mahal untuk bentuk yang rumit
- Sifat mekanik yang unggul
- Biaya perkakas yang lebih rendah dibandingkan dengan cetakan pemesinan
- Proses otomatis memungkinkan produksi massal
- Hasil akhir permukaan yang lebih baik dimungkinkan
Keunggulan MIM dibandingkan Pengecoran Logam
- Akurasi dimensi dan hasil akhir permukaan yang lebih baik
- Lebih sedikit cacat seperti porositas dibandingkan dengan komponen cor
- Sifat isotropik tidak seperti pengecoran terarah
- Rendah atau tanpa flash atau bukaan tidak seperti coran
- Tidak ada reaksi yang berhubungan dengan peleburan atau perubahan komposisi
- Core dan undercut dimungkinkan tidak seperti casting
- Pilihan material yang luas di luar paduan yang dapat dicor
- Konsistensi sifat dengan metalurgi serbuk
Keterbatasan Mesin MIM versus Mesin CNC
- Ukuran dibatasi oleh kapasitas mesin cetak injeksi
- Lebih banyak waktu dan biaya di muka untuk perkakas
- Toleransi ketat +/- 0,5% vs +/- 0,1% untuk pemesinan CNC
- Batasan geometri vs pemesinan yang tidak dibatasi
- Kekerasan maksimum yang lebih rendah dapat dicapai dibandingkan dengan pemesinan
- Pemesinan sekunder sering kali masih diperlukan untuk mencapai toleransi
Kapan Tidak Menggunakan MIM
- Suku cadang yang sangat besar di luar kapasitas peralatan MIM
- Suku cadang yang membutuhkan toleransi sangat ketat di bawah 0,5%
- Aplikasi yang membutuhkan kekerasan permukaan di atas 50 HRC
- Produk dengan persyaratan volume yang sangat rendah
- Komponen dengan rasio aspek ekstrem yang tidak cocok untuk pencetakan
- Ketika tidak ada waktu untuk pengoptimalan desain untuk proses MIM
- Aplikasi yang sensitif terhadap biaya dengan opsi manufaktur yang lebih murah
Pertimbangan Desain dan Pemodelan MIM
Desain komponen dan bahan baku yang tepat sangat penting bagi MIM untuk mencapai sifat dan kinerja yang dibutuhkan. Berikut adalah pertimbangan desain utama:
Tahap Desain Bagian
- Mengoptimalkan ketebalan dinding untuk pengisian cetakan yang seragam selama injeksi
- Termasuk jari-jari internal dan fillet yang besar untuk memudahkan pengisian
- Hindari perubahan besar pada penampang melintang di sepanjang jalur aliran
- Rancang gerbang dan pelari cetakan yang tepat untuk pola aliran yang sesuai
- Tambahkan rusuk dan buhul penguat untuk menghindari kendur atau bengkok
- Memperhitungkan penyusutan bagian selama sintering dalam dimensi awal
- Mengembangkan cetakan prototipe untuk validasi desain sebelum produksi penuh
Pengembangan Bahan Baku
- Menyesuaikan viskositas bahan baku dengan kompleksitas cetakan pada suhu pencetakan
- Pastikan pemuatan bubuk yang cukup untuk kepadatan sinter yang diperlukan
- Pilih komponen pengikat yang sesuai dan rasio bubuk untuk kemudahan pencampuran
- Mengoptimalkan distribusi ukuran partikel bubuk untuk kepadatan kemasan bubuk
- Sesuaikan formulasi bahan baku untuk menghilangkan pengikat yang bebas cacat
- Memvalidasi properti bahan baku melalui simulasi aliran cetakan
- Menguji beberapa iterasi bahan baku untuk mencapai kemampuan cetakan penuh
Simulasi dan Pemodelan
- Pemodelan aliran cetakan untuk mengoptimalkan lokasi gerbang dan pelari
- FEA struktural untuk memprediksi lengkungan dan mengoptimalkan geometri bagian
- Simulasi CFD untuk penghilangan dan sintering pengikat yang seragam
- Pemodelan termal untuk meminimalkan tegangan sisa
- Pemodelan mekanis untuk memaksimalkan kekuatan dan kinerja
- Perangkat lunak pemodelan proses untuk mempelajari interaksi antar parameter
- Validasi eksperimental prediksi perangkat lunak melalui cetakan prototipe
Output Pemodelan Utama
- Waktu pengisian cetakan, viskositas bahan baku, suhu bagian depan aliran
- Garis las, perangkap udara, dan prediksi cacat cetakan lainnya
- Kandungan pengikat spasial, suhu dan gradien pelarutan
- Laju sintering, gradien densitas, penyusutan, tren lengkungan
- Distribusi tegangan sisa, perkiraan sobekan panas dan retakan
- Kekuatan mekanis, umur kelelahan, analisis toleransi kerusakan
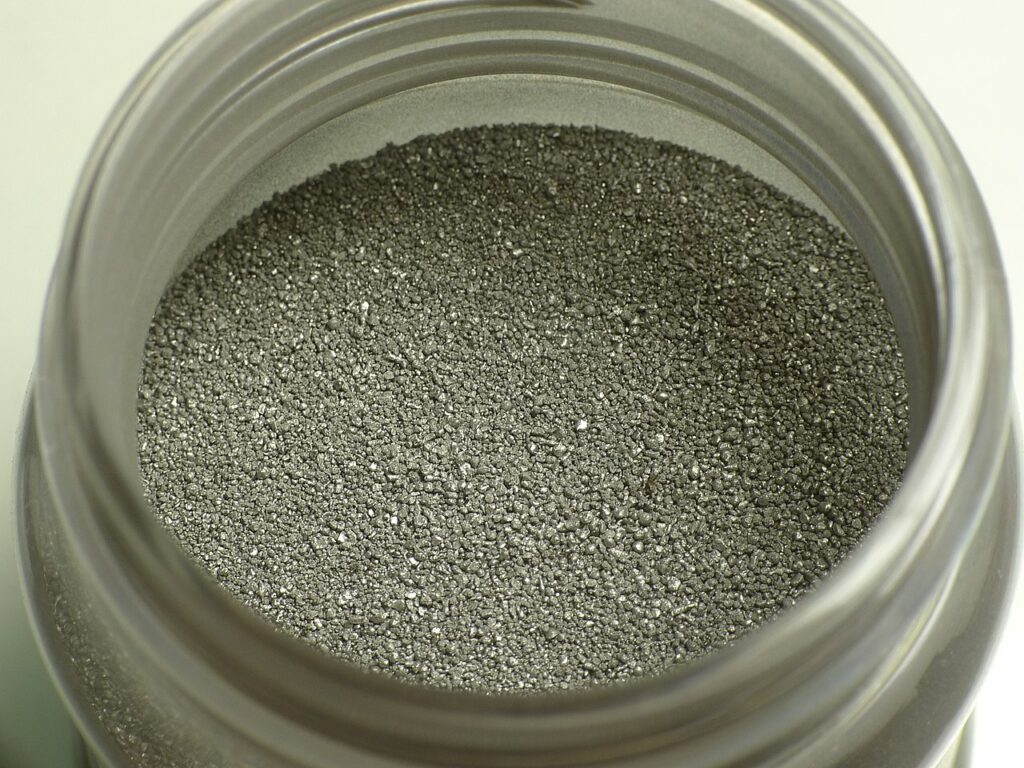
Cacat MIM dan Metode Mitigasi
Cacat dapat muncul pada komponen MIM karena bahan baku, parameter pencetakan, atau kondisi tungku yang tidak dioptimalkan. Berikut ini adalah cacat MIM yang umum terjadi dan metode mitigasinya:
Cacat | Akar Penyebab | Metode Mitigasi |
---|---|---|
Cacat permukaan | Suhu cetakan rendah, gesekan tinggi, komponen pengikat | Optimalkan pemolesan cetakan, gunakan agen pelepas cetakan, turunkan suhu cetakan secara bertahap |
Garis las | Bagian depan aliran bahan baku yang tidak diinginkan | Mengoptimalkan desain gerbang dan runner melalui pemodelan untuk mencegah garis las |
Warpage | Pemanasan yang tidak seragam dalam tungku, tegangan sisa | Optimalisasi struktural, penghilang stres pra-sintering, pengaturan tungku yang dioptimalkan |
Retak | Sintering cepat, kandungan pengikat tinggi, gradien termal yang curam | Laju pemanasan yang lebih rendah, mengoptimalkan sistem pengikat, desain ulang struktur |
Porositas | Pemuatan bubuk yang rendah dalam bahan baku, pencampuran yang buruk | Tingkatkan kandungan bubuk dalam bahan baku, tingkatkan proses pencampuran |
Variasi dimensi | Penyusutan yang tidak konsisten, keausan cetakan, gradien kepadatan | Kontrol proses statistik, pemeliharaan cetakan, mengoptimalkan debinding dan sintering |
Kontaminasi | Penanganan yang buruk, kontrol atmosfer tungku | APD yang tepat, meningkatkan filter udara, mencegah kontaminasi silang dalam batch tungku |
Pengisian tidak lengkap | Suhu cetakan tinggi, viskositas tinggi | Tingkatkan suhu cetakan dan bahan baku, gunakan pengikat dengan viskositas yang lebih rendah |
Data dan Tren Industri MIM
Ukuran Pasar Global MIM
Pasar MIM global bernilai USD 1,5 miliar pada tahun 2022 dan diproyeksikan mencapai USD 3,1 miliar pada tahun 2030, tumbuh pada CAGR 8,7%, didorong oleh permintaan dari sektor perawatan kesehatan, otomotif, dan kedirgantaraan.
Pendorong Pertumbuhan Industri
- Tren keringanan di seluruh sektor otomotif, kedirgantaraan, dan elektronik
- Permintaan untuk komponen logam yang kecil dan kompleks pada perangkat medis
- Lebih layak dengan rentang bahan yang lebih luas yang dapat digunakan untuk MIM
- Otomatisasi menurunkan biaya produksi
- Pertumbuhan dalam pembuatan komponen presisi
- Peningkatan adopsi dalam aplikasi baru seperti pembuatan jam tangan
Proyeksi CAGR berdasarkan Wilayah
- Asia Pasifik: CAGR 9,3%
- Eropa: CAGR 10,2%
- Amerika Utara: CAGR 7,6%
- Seluruh Dunia: CAGR 7,9%
Pangsa Suku Cadang MIM berdasarkan Industri
- Produk konsumen: 22%
- Otomotif: 21%
- Senjata Api: 15%
- Medis: 14%
- Industri: 13%
- Dirgantara: 8%
- Lainnya: 7%
Tren Perkembangan Teknologi MIM
- Sistem pengikat baru untuk mengurangi cacat dan memungkinkan geometri yang kompleks
- Formulasi bahan baku baru untuk pemuatan dan sintering bubuk yang lebih baik
- MIM multi-material yang menggabungkan bubuk berbeda menjadi satu komponen
- Otomatisasi pasca-pemrosesan seperti pemesinan, penggabungan, penguliran, dll.
- Teknik MIM Hibrida + Manufaktur Aditif
- Metode pemanasan baru seperti sintering gelombang mikro untuk pemrosesan yang lebih cepat
- Simulasi terintegrasi yang menggabungkan beberapa langkah fisika dan manufaktur
- Meningkatnya penerapan sistem manajemen mutu
Ringkasan
Hal-hal penting yang dapat diambil:
- MIM memungkinkan produksi volume tinggi untuk komponen logam yang rumit dengan menggabungkan cetakan injeksi dan metalurgi serbuk.
- Cocok untuk komponen kecil, kompleks, dan presisi tinggi dalam industri medis, senjata api, otomotif, kedirgantaraan, dan konsumen.
- Manfaatnya termasuk bentuk yang mendekati jaring, pilihan material yang luas, sifat mekanik yang baik mendekati material tempa.
- Melibatkan pencetakan bahan baku, debinding, dan langkah-langkah sintering menggunakan peralatan khusus.
- Membutuhkan keahlian dalam desain komponen, pengembangan bahan baku, pemodelan proses, pengendalian cacat, dan manajemen kualitas.
- Diproyeksikan tumbuh pada CAGR 8,7% secara global yang didorong oleh permintaan di seluruh industri.
- Pengembangan teknologi yang sedang berlangsung untuk pemrosesan yang lebih cepat, lebih banyak bahan, peningkatan otomatisasi, dan peningkatan kualitas komponen.
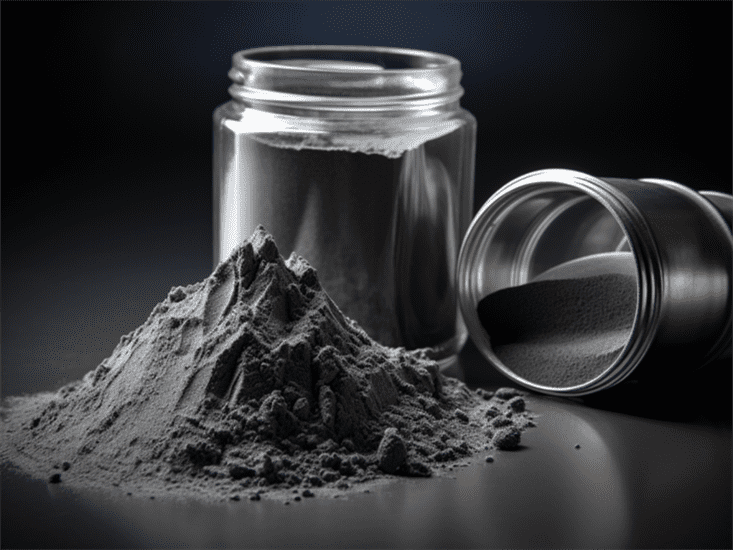
Pertanyaan Umum
T: Apa saja keunggulan utama teknologi MIM?
J: Keuntungan utama MIM adalah:
- Kemampuan untuk menghasilkan geometri kecil dan kompleks yang tidak mungkin dilakukan melalui pemesinan atau pengecoran
- Manufaktur bentuk hampir bersih yang menghasilkan
T: Apa kemampuan toleransi tipikal MIM?
J: MIM pada umumnya dapat mencapai toleransi +/- 0,5% meskipun +/- 0,3% dimungkinkan untuk beberapa geometri dan pemesinan mungkin diperlukan untuk toleransi yang lebih ketat.
T: Berapa ukuran komponen yang dapat diproduksi menggunakan MIM?
J: MIM dapat memproduksi komponen dari 0,1 gram hingga sekitar 250 gram. Komponen yang lebih besar dapat dibuat tetapi sulit karena keterbatasan ukuran mesin cetak.
T: Bagaimana MIM dibandingkan dengan cetakan injeksi plastik?
J: Meskipun keduanya menggunakan peralatan cetakan injeksi, MIM dapat menghasilkan komponen logam sedangkan plastik memiliki kekuatan yang jauh lebih rendah. Tetapi MIM memiliki tingkat produksi yang lebih rendah dan biaya yang lebih tinggi daripada cetakan injeksi plastik.
T: Perlakuan panas apa yang digunakan dalam MIM?
J: Proses sintering dalam MIM melibatkan pemanasan hingga hampir mencapai titik leleh serbuk logam sehingga tidak diperlukan perlakuan panas lebih lanjut. Perlakuan panas tambahan dapat dilakukan sesuai kebutuhan untuk memodifikasi properti.
T: Bahan apa saja yang dapat digunakan dalam MIM?
J: Berbagai macam material dapat dibuat dengan MIM, termasuk baja tahan karat, baja perkakas, superalloy, titanium, paduan berat tungsten, dan paduan magnetik. Pengembangan material baru adalah area penelitian utama dalam MIM.
T: Bagaimana MIM dibandingkan dengan pencetakan 3D logam?
J: MIM dapat menghasilkan volume yang lebih tinggi dengan hasil akhir permukaan dan sifat mekanis yang lebih baik. Tetapi pencetakan 3D menawarkan kebebasan desain yang lebih besar dan waktu yang lebih cepat untuk memasarkan prototipe atau komponen khusus.