Cetakan injeksi logam (MIM) adalah proses manufaktur yang digunakan untuk memproduksi komponen logam yang kecil dan kompleks dengan toleransi yang ketat. MIM menggabungkan keserbagunaan cetakan injeksi plastik dengan kekuatan dan integritas logam mesin. Artikel ini memberikan gambaran umum terperinci tentang teknologi MIM, aplikasi, peralatan, proses, pertimbangan desain, dan banyak lagi.
Tinjauan umum tentang cetakan injeksi logam
Cetakan injeksi logam adalah proses metalurgi serbuk yang memungkinkan produksi volume tinggi untuk komponen logam kecil dan presisi dengan menggunakan teknik cetakan injeksi.
Bagaimana MIM Bekerja
Proses MIM melibatkan pencampuran serbuk logam halus dengan bahan pengikat untuk membuat bahan baku yang dapat disuntikkan ke dalam cetakan. Bagian yang dicetak, yang dikenal sebagai bagian hijau, kemudian disinter untuk menghilangkan bahan pengikat dan mengkonsolidasikan serbuk logam ke dalam struktur yang kokoh. Langkah-langkah dasarnya adalah:
- Pencampuran - Serbuk logam halus dicampur dengan pengikat untuk menciptakan bahan baku yang homogen
- Cetakan Injeksi - Bahan baku dilebur dan disuntikkan ke dalam cetakan untuk membentuk bagian berwarna hijau
- Debinding - Pengikat dihilangkan melalui pengikatan pelarut, termal, atau katalitik
- Sintering - Bagian yang terlepas disinter untuk memadatkan dan memperkuat struktur logam
- Operasi Sekunder - Langkah-langkah penyelesaian tambahan seperti pemesinan, pengeboran, penyadapan, dll.
Keuntungan dari MIM
MIM menawarkan beberapa keuntungan dibandingkan dengan teknik manufaktur lainnya:
- Produksi volume tinggi dengan biaya rendah per bagian
- Geometri kompleks dengan toleransi yang ketat
- Berbagai bahan seperti baja tahan karat, titanium, tungsten, kobalt kromium, dll.
- Kehilangan barang bekas dan limbah material yang minimal
- Fabrikasi dengan bentuk jaring yang mengurangi pemesinan
- Ukuran komponen kecil dari 0,005 lbs hingga 0,5 lbs
- Konsolidasi suku cadang dengan menggabungkan rakitan
- Permukaan halus dan hasil akhir yang bagus
Keterbatasan MIM
Beberapa keterbatasan cetakan injeksi logam meliputi:
- Biaya startup dan perkakas yang tinggi
- Kisaran ukuran terbatas untuk suku cadang
- Peralatan khusus yang dibutuhkan
- Proses multi-langkah dengan produksi yang lebih lambat
- Batasan dimensi berdasarkan karakteristik bubuk
- Pembatasan geometri bagian berdasarkan aliran serbuk
Aplikasi MIM
MIM banyak digunakan untuk membuat komponen kecil dan kompleks dengan toleransi yang ketat di seluruh industri seperti:
- Medis - implan ortopedi, implan gigi, instrumen bedah
- Otomotif - komponen mesin, katup, roda gigi
- Dirgantara - bilah turbin, impeler, nozel
- Elektronik - konektor, roda gigi mikro, pelindung
- Senjata api - pemicu, palu, pengaman
- Jam tangan - kotak arloji, gelang, mahkota
- Industri - kenop, pengencang, alat pemotong
MIM bersaing dengan proses lain seperti pengecoran investasi, permesinan, dan stamping untuk produksi komponen logam.
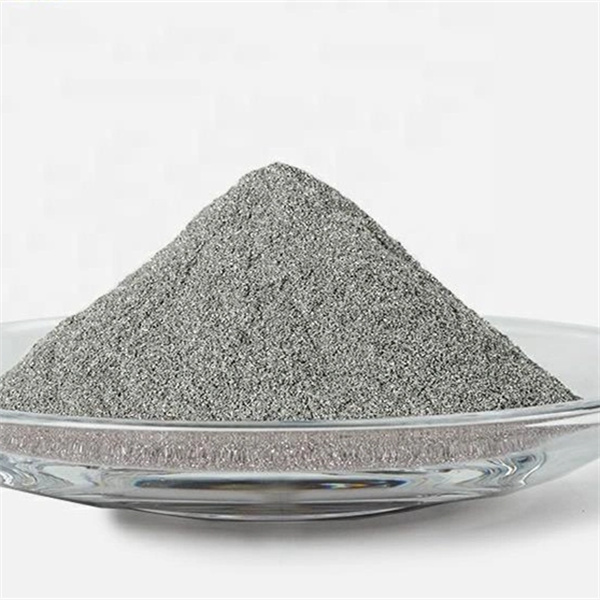
Panduan Peralatan Cetakan Injeksi Logam
Peralatan khusus diperlukan untuk setiap tahap proses MIM. Berikut ini adalah jenis peralatan MIM yang utama:
Peralatan | Fungsi |
---|---|
Pengumpan bubuk | Mengukur serbuk halus secara akurat |
Pencampur | Mencampur bubuk dan pengikat secara homogen |
Granulator | Membentuk bahan baku menjadi butiran untuk dicetak |
Mesin cetak injeksi | Membentuk bahan baku menjadi bentuk yang dibutuhkan |
Tungku debinding | Lepaskan pengikat dari bagian yang dicetak |
Tungku sintering | Memadatkan dan memperkuat struktur logam |
Mesin gerinda | Lepaskan gerbang, pelari, dan permukaan yang halus |
Pusat permesinan | Bor, putar, giling fitur menjadi bagian yang disinter |
Otomatisasi, sistem penanganan, dan kontrol canggih digunakan untuk mengintegrasikan proses dan memaksimalkan produktivitas. Peralatan harus dipilih dengan cermat berdasarkan faktor-faktor seperti material, ukuran komponen, volume produksi, dan persyaratan kualitas.
Proses pencetakan injeksi logam Langkah demi Langkah
Pemrosesan MIM melibatkan beberapa langkah untuk mengubah serbuk logam halus menjadi komponen penggunaan akhir yang sepenuhnya padat.
Langkah 1 - Pencampuran
- Serbuk logam dan pengikat dicampur secara menyeluruh di dalam mixer untuk menghasilkan bahan baku yang homogen
- Ukuran partikel bubuk, bentuk, distribusi berdampak pada kemampuan cetakan dan sintering
- Pengikat memberikan aliran dan daya rekat selama pencetakan injeksi
- Lilin, termoplastik seperti PP, PE, PVC, dan polimer yang digunakan sebagai pengikat
- Pencampuran dilakukan dengan menggunakan sigma blade, Z-blade, mixer planetary ganda
Langkah 2 - Granulasi
- Campuran bahan baku digranulasi menjadi pelet kecil untuk cetakan injeksi
- Meningkatkan aliran material dan mencegah pemisahan di dalam laras
- Granulator menggunakan pisau berputar untuk memotong bahan baku menjadi butiran yang seragam
- Bentuk dan ukuran butiran mempengaruhi kepadatan kemasan dan kemampuan cetakan
Langkah 3 - Cetakan Injeksi
- Butiran bahan baku dicetak ke dalam bentuk dan ukuran bagian yang diperlukan
- Menggunakan mesin cetak injeksi yang dimodifikasi dengan suhu dan tekanan yang terkendali
- Penting untuk mengoptimalkan parameter pencetakan untuk meminimalkan cacat
- Bagian yang dibentuk seperti cetakan yang disebut bagian hijau memiliki bentuk tetapi tidak memiliki kekuatan
Langkah 4 - Mengurai ikatan
- Pengikat diekstraksi dari bagian hijau melalui pelarut, termal atau katalitik
- Pengikatan pelarut menggunakan aksi kapiler untuk melarutkan pengikat
- Pengikatan termal menguraikan pengikat di dalam tungku
- Pengikatan katalitik mempercepat penghilangan pengikat dengan katalis
- Debinding menciptakan bagian berwarna cokelat dengan struktur berpori dari partikel logam
Langkah 5 - Sintering
- Bagian berwarna cokelat disinter dalam tungku atmosfer yang terkendali
- Ikatan antara partikel logam terbentuk melalui difusi dan transportasi massa
- Kepadatan hampir penuh hingga 96-99% dicapai selama sintering
- Suasana, suhu, waktu yang dioptimalkan untuk menghindari cacat
- Penyusutan sintering diperhitungkan selama pencetakan
Langkah 6 - Operasi Sekunder
- Langkah-langkah pengerjaan logam tambahan seperti anil, pemesinan, pengeboran, pelapisan
- Anil mengurangi tekanan internal dari sintering
- Pemesinan CNC menghilangkan serpihan, menghaluskan permukaan, menambah fitur
- Pelapisan dan pengecatan diterapkan untuk peningkatan atau perlindungan korosi
Proses MIM memungkinkan komponen logam yang kompleks dan presisi tinggi dengan menggabungkan keunggulan cetakan injeksi plastik dan metalurgi serbuk.
Pertimbangan Desain untuk Suku Cadang MIM
MIM memungkinkan kebebasan geometris yang tidak mungkin dilakukan dengan pemesinan, tetapi memerlukan pertimbangan desain tertentu:
- Ketebalan dinding - Kisaran tipikal 0,3 - 4,0 mm dengan beberapa serbuk yang mendukung dinding hingga 6mm
- Permukaan akhir - Hasil akhir yang lebih halus daripada pengecoran tetapi tidak sehalus pemesinan; Nilai Ra 1 - 4 μm adalah tipikal untuk MIM
- Toleransi dimensi - ± 0,1% hingga ± 0,5% berdasarkan geometri bagian dengan beberapa presisi tingkat mikron
- Kepadatan - Kepadatan penuh hingga 99% dapat dicapai dengan sintering yang dioptimalkan
- Geometri - Menghindari serbuk yang terperangkap dan membiarkan pengikat keluar sangat penting
- Sudut konsep - Dinding meruncing dengan sudut draft 1-3° untuk memudahkan pengeluaran komponen
- Jari-jari dan fillet - Transisi bertahap lebih disukai daripada sudut tajam
- Lubang dan gigi berlubang - Diameter minimum 0,25 - 0,5 mm untuk lubang tembus
- Benang - Dapat dicetak tetapi sering kali dikerjakan setelah sintering untuk akurasi yang lebih baik
- Detail permukaan - Batasi detail halus untuk mengurangi keausan cetakan; proses pasca-pencetakan dapat meningkatkan
Desain MIM harus fokus pada geometri yang memaksimalkan kinerja daripada kemudahan fabrikasi. Proses ini memungkinkan konsolidasi rakitan multi-bagian menjadi satu bagian dengan penghematan biaya dan berat yang signifikan.
Bahan yang Digunakan dalam Cetakan Injeksi Logam
MIM dapat memproduksi komponen dari berbagai macam logam, paduan, dan keramik di berbagai industri.
Bahan | Aplikasi | Properti |
---|---|---|
Baja tahan karat | Medis, senjata api, kelautan | Ketahanan korosi, kekuatan |
Baja paduan rendah | Otomotif, industri | Respons magnetik, kemampuan mesin |
Paduan magnetik lunak | Sensor, aktuator | Permeabilitas tinggi |
Paduan logam keras | Alat pemotong | Ketahanan aus, kekerasan |
Paduan tembaga | Elektronik, termal | Konduktivitas listrik |
Paduan aluminium | Listrik, termal | Ringan, konduktivitas |
Paduan Titanium | Kedirgantaraan, otomotif | Kekuatan, biokompatibilitas |
Paduan tungsten | Pelindung radiasi | Kepadatan tinggi |
Sermet | Elektronik, optik | Ketahanan oksidasi |
Faktor-faktor seperti fungsi komponen, biaya, langkah pasca-pemrosesan, dan kompatibilitas paduan menentukan pilihan material MIM yang ideal.
Pemasok dan Produsen Peralatan MIM
Banyak perusahaan yang menawarkan bahan, layanan, produksi, dan peralatan MIM secara global. Berikut ini adalah beberapa pemasok MIM utama di seluruh rantai nilai:
Perusahaan | Produk/Layanan |
---|---|
BASF | Bahan baku, pengikat |
Sandvik Osprey | Bubuk logam |
Höganäs | Bubuk logam |
Bubuk CNPC | Bubuk logam |
Indo-Mim | Produk dan layanan MIM |
MPP | Produk dan layanan MIM |
Grup ARC | Produk dan layanan MIM |
Logam Tekan Atlas | Produksi suku cadang MIM |
Epson Atmix | Peralatan MIM |
Milacron | Mesin cetak injeksi |
Elnik | Tungku sintering |
TCN | Tungku pengikatan dan sintering |
Ada juga banyak pemain regional yang lebih kecil yang terlibat di seluruh rantai pasokan MIM. Pengguna akhir yang ingin mengadopsi MIM dapat bermitra dengan pemasok material dan produsen kontrak tergantung pada kemampuan yang dibutuhkan.
Analisis Biaya Suku Cadang MIM vs. Alternatif
Berikut ini adalah perbandingan perkiraan biaya untuk memproduksi 1000 suku cadang dengan menggunakan proses manufaktur yang berbeda:
Proses | Biaya Penyiapan | Biaya Mesin | Biaya Perkakas | Biaya Bagian | Total (1000 bagian) |
---|---|---|---|---|---|
Mesin CNC | Rendah | $100,000 | $2,000 | $50 | $52,000 |
Pengecoran Investasi | Tinggi | $500,000 | $40,000 | $20 | $60,000 |
Cetakan Injeksi Logam | Tinggi | $750,000 | $100,000 | $15 | $115,000 |
Stamping | Tinggi | $1,000,000 | $150,000 | $10 | $160,000 |
- Pemesinan CNC memiliki volume rendah, biaya suku cadang tinggi, kompleksitas terbatas
- Pengecoran investasi lebih baik untuk volume hingga 10.000 unit
- MIM memiliki keunggulan untuk volume menengah hingga tinggi dengan geometri yang kompleks
- Stamping memiliki biaya perkakas yang sangat tinggi tetapi harga suku cadang terendah dalam volume tinggi di atas 100 ribu suku cadang
Titik persilangan di mana MIM menjadi lebih ekonomis daripada proses lainnya tergantung pada volume, kompleksitas, dan ukuran.
Memilih Pemasok atau Mitra MIM
Memilih pemasok MIM atau mitra produksi yang kompeten sangat penting untuk produksi suku cadang yang hemat biaya. Berikut ini adalah pertimbangan utama:
- Keahlian teknis - Pengalaman sebelumnya dengan suku cadang, bahan, industri MIM yang serupa
- Sistem kualitas - Sertifikasi ISO 9001, praktik kontrol kualitas
- Kapasitas produksi - Kemampuan untuk memenuhi kebutuhan volume saat ini dan masa depan
- Proses sekunder - Kemampuan pemesinan, stamping, pelapisan, pengecatan
- Optimalisasi bagian - Desain untuk dukungan MIM untuk memaksimalkan manfaat
- Pembuatan prototipe - Layanan pembuatan prototipe cepat untuk memvalidasi desain
- Kemampuan perkakas - Desain dan fabrikasi perkakas internal lebih disukai
- Akses bahan baku - Membangun saluran pasokan untuk bahan baku
- Kemampuan R&D - Penelitian dan pengembangan yang sedang berlangsung dalam bidang material dan teknik manufaktur yang canggih
- Fokus pada pelanggan - Responsif terhadap kebutuhan dan pendekatan kolaborasi
- Struktur biaya - Model penetapan harga dan daya saing untuk volume yang diperkirakan
- Logistik - Kemampuan untuk mengirimkan suku cadang dengan andal sekaligus memenuhi persyaratan waktu tunggu
Memprioritaskan faktor-faktor ini akan membantu mengidentifikasi mitra MIM strategis yang tepat untuk aplikasi tertentu.
Memasang Peralatan MIM
Bagi perusahaan yang memasang kemampuan MIM di rumah, pemasangan peralatan yang tepat sangatlah penting. Berikut ini adalah pertimbangan utama:
- Ruang lantai sekitar 2000 - 5000 kaki persegi diperlukan untuk jalur MIM
- Diperlukan catu daya yang stabil dengan kapasitas 200-600 kVA
- Saluran udara bertekanan yang diberi peringkat untuk tekanan 100 psi
- Ventilasi pembuangan untuk pengumpulan panas, emisi, dan debu
- Utilitas seperti nitrogen, air proses, dan pasokan gas
- Kontrol suhu dan kelembapan sekitar 20 ± 3 ° C, 50 ± 20%
- Mezanin, platform untuk memasang peralatan tambahan
- Sistem penanganan material seperti kerekan, forklift, tempat sampah
- Ruang kontrol, sistem komputer untuk pemantauan
- Pelatihan staf tentang keselamatan proses dan pengoperasian peralatan
- Simulasi proses, uji coba untuk memvalidasi instalasi
- Jadwal kalibrasi dan pemeliharaan preventif
Ruang yang memadai, utilitas, dan kondisi yang terkendali sangat penting untuk kelancaran pengoperasian peralatan MIM. Pengujian dan pelatihan yang menyeluruh mempersiapkan produksi yang sesungguhnya.
Pemeliharaan Peralatan MIM
Pemeliharaan yang konsisten meningkatkan waktu kerja dan kinerja peralatan produksi MIM. Aspek-aspek utama:
- Jadwal pemeliharaan preventif yang terdokumentasi untuk setiap mesin
- Pembersihan harian tumpahan material, kebocoran, debu, puing-puing
- Memeriksa tingkat cairan, kebocoran, suara yang tidak biasa, getaran
- Memantau tekanan, suhu, konsumsi daya
- Pengujian sistem pemanas, pendingin, dan kontrol
- Penggantian suku cadang aus seperti layar, sekrup, barel
- Inspeksi untuk kelelahan komponen, kerusakan, keselarasan
- Pembangunan ulang dan perbaikan rutin berdasarkan jam operasional
- Pelacakan log pemeliharaan untuk analisis
- Penyimpanan persediaan suku cadang untuk komponen penting
- Pelatihan tentang pengoperasian dan keselamatan peralatan yang tepat
- Layanan dan dukungan tepat waktu dari vendor peralatan
Staf yang terlatih dan kolaborasi dengan vendor peralatan membantu memaksimalkan produktivitas peralatan MIM sekaligus meminimalkan waktu henti.
Perangkat Lunak Simulasi Cetakan Injeksi Logam
Perangkat lunak simulasi digunakan untuk memodelkan proses MIM secara digital sebelum produksi aktual. Manfaatnya meliputi:
- Prediksi pola pengisian cetakan dan optimalisasi lokasi gerbang
- Mengidentifikasi jalur las dan perangkap udara untuk mencegah cacat
- Mempelajari gradien termal dan pemadatan dalam geometri yang kompleks
- Mensimulasikan efek profil debinding dan sintering pada bentuk akhir
- Memvalidasi desain perkakas sebelum fabrikasi
- Mengurangi biaya uji coba melalui pembuatan prototipe virtual
- Melatih personel melalui representasi visual
Beberapa paket simulasi MIM komersial termasuk:
- MIMSIM - Simulasi terintegrasi untuk pencetakan melalui sintering
- Sigma Soft - Analisis FEM 3D untuk pengisian dan distorsi cetakan
- Netzsch MIMPre - Pemodelan sifat reologi bahan baku MIM
- Simufact Aditif - Simulasi multiphysics dari proses AM
- EOS PSW - Simulasi difokuskan pada sintering dan perlakuan panas
Menggunakan perangkat lunak MIM meningkatkan konsistensi proses, mengoptimalkan kualitas komponen, dan mengurangi biaya pembuatan prototipe fisik. Alur kerja simulasi-ke-produksi yang terintegrasi lebih disukai.
Memecahkan Masalah Cacat MIM yang Umum Terjadi
Beberapa cacat umum pada komponen MIM dan potensi penyebabnya adalah:
Cacat | Penyebab |
---|---|
Bidikan pendek | Tekanan injeksi rendah, pemadatan dini |
Flash | Cetakan yang terlalu banyak, kerusakan cetakan |
Warpage | Pendinginan yang tidak seragam, masalah pengikat |
Retak | Sintering cepat, kandungan pengikat tinggi |
Porositas | Homogenisasi yang buruk, gas yang terperangkap |
Kontaminasi | Kontaminasi silang, atmosfer tungku |
Variasi dimensi | Masalah bahan baku, keausan cetakan, penyusutan |
Cacat permukaan | Porositas gas, penggetasan logam cair |
Inklusi | Bahan baku yang terkontaminasi, nosel tersumbat |
Metodologi analisis cacat yang sistematis harus digunakan untuk mengisolasi parameter proses yang menyebabkan cacat dan melakukan tindakan korektif seperti menyesuaikan formulasi bahan baku, parameter pencetakan, debinding dan profil sintering.
Keuntungan dari Teknologi MIM
MIM menawarkan keunggulan yang signifikan dibandingkan pendekatan produksi komponen logam lainnya:
- Kompleksitas - Geometri 3D yang rumit dapat dilakukan, mengkonsolidasikan rakitan
- Konsistensi - Proses yang sangat dapat diulang dengan varians bagian yang rendah
- Efisiensi - Fabrikasi bentuk hampir bersih dengan lebih sedikit limbah bahan baku
- Otomatisasi - Proses yang sangat otomatis mengurangi tenaga kerja
- Fleksibilitas - Berbagai macam bahan seperti logam, keramik, komposit
- Kualitas - Hasil akhir permukaan dan sifat mekanik yang baik
- Produktivitas - Output volume tinggi dengan biaya rendah per bagian
- Miniaturisasi - Komponen mikro dengan detail hingga 10 μm
- Keberlanjutan - Efisiensi energi dibandingkan dengan pemesinan
- Biaya - Total biaya yang lebih rendah untuk volume produksi menengah hingga tinggi
Kemampuan unik MIM mendorong adopsi di berbagai industri seperti otomotif, kedirgantaraan, medis, dan elektronik.
Keterbatasan Cetakan Injeksi Logam
Meskipun memiliki banyak manfaat, MIM memiliki keterbatasan tertentu:
- Investasi perkakas awal yang tinggi
- Kisaran ukuran terbatas biasanya di bawah 65 gram
- Akurasi yang lebih rendah dari mesin CNC
- Risiko porositas yang membutuhkan kontrol proses
- Pilihan bahan yang terbatas berdasarkan karakteristik bubuk
- Bahaya keselamatan dari serbuk halus
- Batasan geometri bagian yang terkait dengan kemampuan cetakan
- Potensi variabilitas lot-ke-lot
- Sifat mekanik yang lebih rendah dari bahan tempa
- Produksi prototipe yang terbatas dalam volume yang lebih rendah
- Persyaratan untuk pemesinan sekunder dalam banyak aplikasi
- Peralatan khusus dan operator terlatih dibutuhkan
Untuk presisi yang sangat tinggi atau komponen logam yang lebih besar yang diproduksi dalam volume rendah, proses lain mungkin lebih cocok daripada MIM.
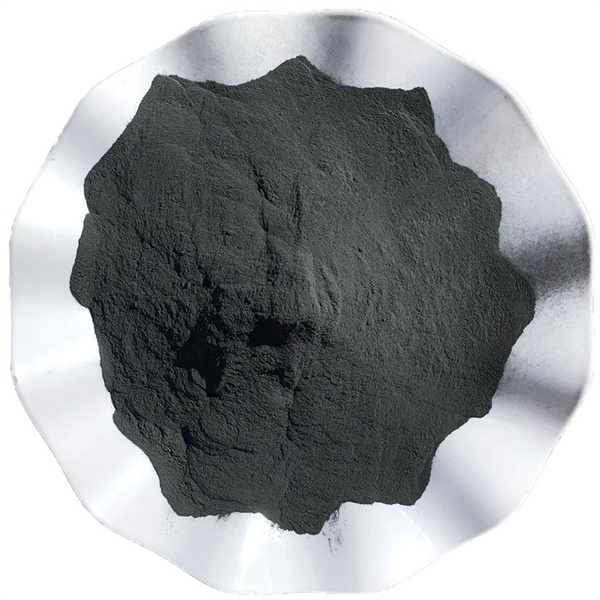
Masa Depan Cetakan Injeksi Logam
MIM diperkirakan akan terus mengalami pertumbuhan yang kuat seiring dengan perkembangan teknologi dan material yang terus membaik:
- Sistem pengikat baru untuk meningkatkan kemampuan cetakan dan kekuatan hijau
- Formulasi bahan baku baru menggunakan nanokomposit
- Komponen berukuran lebih besar yang melebihi batas saat ini
- Peningkatan penggunaan keramik dan paduan tungsten
- Pertumbuhan permintaan yang kuat di sektor medis dan elektronik
- Penggunaan manufaktur aditif untuk membuat perkakas MIM
- Otomatisasi menggunakan robotika dan integrasi Industri 4.0
- Lebih banyak aplikasi di lingkungan yang ekstrem
- Konvergensi dengan pencetakan 3D logam menggunakan deposisi logam terikat
Dengan peningkatan R&D dan adopsi yang lebih mudah, penggunaan MIM akan berkembang pesat di berbagai aplikasi di tahun-tahun mendatang.