Teknologi EBM adalah teknologi manufaktur aditif canggih dengan kemampuan yang unik. Panduan ini memberikan gambaran umum yang komprehensif mengenai teknologi EBM, termasuk cara kerja, manfaat, aplikasi, pemasok sistem, dan perbandingannya dengan proses pencetakan 3D lainnya.
Pengantar Peleburan Berkas Elektron (EBM)
Peleburan berkas elektron adalah teknik manufaktur aditif yang menggunakan berkas elektron untuk secara selektif melelehkan dan memadukan partikel serbuk logam dengan cara lapis demi lapis. Fitur utama:
- Menggunakan berkas elektron sebagai sumber energi untuk melelehkan serbuk logam
- Membuat komponen dengan melelehkan lapisan bubuk secara selektif
- Bahan yang umum digunakan adalah titanium, paduan nikel, baja perkakas, aluminium
- Menghasilkan bagian yang sepenuhnya padat dengan sifat yang sangat baik
- Mendukung geometri kompleks yang tidak mungkin dilakukan dengan pengecoran/pemesinan
- Memberikan kebebasan desain, kustomisasi, mengurangi waktu tunggu
EBM memberikan sifat mekanik yang sangat baik, kemurnian material, permukaan akhir, dan akurasi dimensi pada suku cadang penggunaan akhir di seluruh industri kedirgantaraan, medis, otomotif, dan industri lainnya.
Panduan ini memberikan gambaran umum yang mendetail mengenai proses EBM, teknologi, keuntungan, aplikasi, pemasok sistem, dan perbandingan dengan metode AM lainnya.
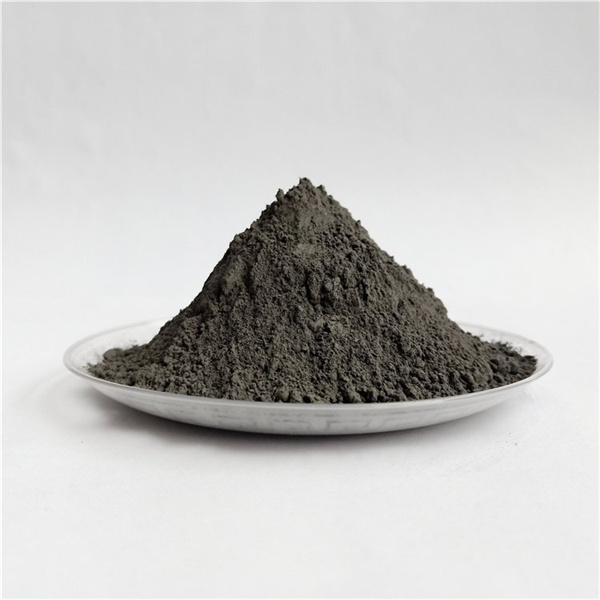
Bagaimana Teknologi EBM Bekerja
Peleburan berkas elektron memproduksi komponen melalui langkah-langkah utama berikut ini:
Langkah-langkah Proses EBM
- Model 3D yang dirancang dalam perangkat lunak CAD dikonversi ke file .STL
- File diiris menjadi beberapa lapisan dan urutan pembuatan dibuat
- Serbuk logam disebarkan secara merata di atas pelat bangunan
- Berkas elektron secara selektif memindai dan melelehkan bubuk untuk memadukan lapisan
- Pelat bangunan diturunkan dan lapisan bubuk baru disebarkan
- Proses diulang sampai seluruh bagian dibangun lapis demi lapis
- Serbuk yang tidak menyatu mendukung bagian selama pembuatan
- Bagian yang sudah selesai dikeluarkan dari mesin untuk diproses lebih lanjut
- Sinar elektron berenergi tinggi menghasilkan peleburan dan pengelasan yang cepat dan tepat
- Proses berlangsung pada suhu tinggi di bawah vakum untuk kemurnian
- Serbuk yang tidak terpakai diambil dan digunakan kembali sehingga meminimalkan limbah
Jenis-jenis Sistem EBM
Ada dua jenis utama sistem EBM yang tersedia saat ini:
Jenis Sistem EBM
Jenis | Deskripsi |
---|---|
Sistem satu balok | Berkas elektron tunggal |
Sistem multi-balok | Beberapa balok paralel |
- Sistem satu balok menggunakan satu berkas elektron berdaya tinggi yang biasanya 50-60kW. Laju pembuatan lebih lambat karena persyaratan pemindaian.
- Sistem multi-balok memanfaatkan beberapa balok secara bersamaan untuk kecepatan yang lebih tinggi. Mengurangi waktu pemindaian secara signifikan.
- Daya sinar tunggal berkisar antara 3-6kW. Daya total dalam sistem multi-balok lebih dari 10MW.
- Sistem multi-balok generasi terbaru secara dramatis meningkatkan tingkat pembangunan.
- Kontrol sinar, pemindaian, dan pemfokusan adalah subsistem yang sangat penting untuk peleburan yang presisi.
Bahan untuk EBM
EBM kompatibel dengan berbagai logam dan paduan, termasuk:
Bahan EBM
Bahan | Properti Utama | Aplikasi |
---|---|---|
Paduan Titanium | Kekuatan tinggi, bobot rendah | Kedirgantaraan, medis |
Nikel Superalloys | Tahan panas/korosi | Bilah turbin |
Baja perkakas | Kekerasan, ketahanan aus | Perkakas, cetakan |
Baja tahan karat | Ketahanan korosi | Perangkat keras kelautan |
Krom kobalt | Biokompatibilitas | Implan medis |
Paduan aluminium | Ringan | Otomotif, struktur |
Paduan tembaga | Konduktivitas listrik | Elektronik |
- Paduan titanium seperti Ti-6Al-4V adalah yang paling umum untuk komponen kedirgantaraan yang penting.
- Superalloy nikel unggul di lingkungan bersuhu tinggi seperti mesin turbin.
- Baja perkakas memberikan kekerasan yang diperlukan untuk cetakan dan perkakas yang tahan lama.
- Paduan biokompatibel digunakan untuk implan dan perangkat medis.
- EBM mendukung logam reaktif seperti titanium dan aluminium lebih baik daripada proses berbasis laser.
Manfaat dan Keuntungan EBM
Manfaat utama yang membuat EBM menarik untuk aplikasi produksi antara lain:
Manfaat EBM
- Bagian yang sepenuhnya padat dan bebas dari kekosongan
- Sifat mekanik yang sangat baik
- Akurasi geometris dan dimensi yang tinggi
- Permukaan akhir yang bagus dan detail yang halus
- Persyaratan pasca-pemrosesan yang rendah
- Suku cadang dengan kemurnian tinggi dengan sedikit kontaminasi
- Lebih sedikit limbah material karena pemulihan bubuk
- Geometri bagian dalam yang kompleks didukung
- Menggabungkan beberapa bagian menjadi satu desain
Vs. Manufaktur Tradisional
- Memungkinkan desain yang lebih ringan dan lebih kuat yang tidak mungkin dilakukan dengan pengecoran atau pemesinan
- Mengkonsolidasikan rakitan menjadi bagian cetak tunggal
- Memungkinkan bentuk yang tidak dapat dibentuk atau ditempa
- Mengurangi waktu tunggu dari berbulan-bulan menjadi berminggu-minggu
- Menurunkan biaya untuk produksi batch kecil
Aplikasi EBM
Keunggulan EBM membuatnya cocok untuk:
Aplikasi EBM
Industri | Penggunaan |
---|---|
Dirgantara | Bilah turbin, rangka struktural, roket |
Medis | Implan ortopedi, alat bedah |
Otomotif | Prototipe yang lebih ringan, suku cadang khusus |
Perkakas | Cetakan injeksi, cetakan pembentuk, jig dan perlengkapan |
Energi | Penukar panas, katup, pompa |
Elektronik | Pelindung, kontak, sistem pendingin |
- Dirgantara secara ekstensif menggunakan EBM untuk komponen paduan titanium dan nikel yang lebih ringan dan kuat.
- Sektor medis memanfaatkan kebebasan geometris dan biokompatibilitas EBM untuk implan.
- Para peneliti otomotif menggunakannya untuk menghasilkan desain topologi yang dioptimalkan dan ringan.
- Saluran pendingin yang sesuai dapat dibangun ke dalam perkakas untuk pencetakan injeksi.
- Industri minyak dan gas menggunakannya untuk komponen bersuhu dan bertekanan tinggi.
- Elektronik mendapatkan keuntungan dari detail halus dan paduan konduktif EBM.
Pemasok Sistem EBM
Produsen utama yang menyediakan sistem EBM meliputi:
Pemasok Mesin EBM
Perusahaan | Merek Mesin |
---|---|
Arcam EBM | Arcam A2X, Q20plus, Spectra H, Q10plus |
Aditif GE | Arcam EBM Spectra L, Arcam EBM Spectra H |
Freemelt | Freemelt ONE, Freemelt TWO |
Aditif Wayland | Calder |
- Arcam EBM, yang kini menjadi bagian dari GE Additive, adalah pemimpin pasar dalam sistem EBM.
- Perusahaan lain seperti Freemelt dan Wayland Additive menawarkan sistem EBM multi-balok generasi terbaru.
- Kapasitas mesin berkisar dari volume pembuatan 150 mm x 150 mm x 150 mm hingga versi yang lebih besar, yaitu 1000 mm.
- Mesin EBM terbaru menyediakan penanganan serbuk otomatis dan daur ulang loop tertutup.
- Parameter yang disesuaikan dan dukungan pelatihan disediakan untuk berbagai aplikasi.
Analisis Biaya untuk EBM
Biaya produksi EBM tergantung pada:
Faktor Biaya EBM
- Harga pembelian mesin - $500.000 hingga lebih dari $2 juta
- Biaya bubuk bahan per kg
- Biaya tenaga kerja untuk desain suku cadang, operasi, pasca-pemrosesan
- Volume produksi
- Membangun kecepatan dan tingkat pemanfaatan
- Konsumsi energi
- Pemeliharaan peralatan dan biaya overhead
Kisaran Khas
- Bagian kecil dalam Ti-6Al-4V: $20 - 150 per bagian
- Komponen kedirgantaraan yang lebih besar: $2000 - 15.000+
- Produksi volume tinggi dengan sistem multi-balok memberikan biaya terendah
Perbandingan Antara EBM dan Proses AM Lainnya
EBM vs AM Logam Lainnya
EBM | Laser PBF | DED | Pengaliran Pengikat | |
---|---|---|---|---|
Bahan | Ti, Ni, Al, baja perkakas | Ti, Al, baja, Ni | Sebagian besar logam | Baja tahan karat |
Kepadatan | 99% yang sepenuhnya padat | 99% yang sepenuhnya padat | 99% padat | 90-95% padat |
Akurasi | Luar biasa, ± 0,2% | Luar biasa, ± 0,1% | Sedang, ± 1% | Sedang, ± 0,5% |
Permukaan akhir | Sangat bagus, Ra 25 μm | Sangat baik, Ra 10 μm | Kasar seperti yang diendapkan | Bagus setelah sintering |
Tingkat Pembangunan | Sedang | Cepat | Sangat cepat | Sedang |
Biaya Peralatan | Tinggi | Tinggi | Sedang | Rendah |
Aplikasi | Kedirgantaraan, medis | Kedirgantaraan, otomotif | Perbaikan, pelapisan, suku cadang besar | Produksi seri |
- Laser PBF menawarkan tingkat pembuatan yang lebih cepat dan resolusi yang lebih baik daripada EBM.
- EBM memberikan sifat material yang sangat baik dengan tekanan internal yang lebih sedikit.
- Pengaliran pengikat berbiaya lebih rendah tetapi membutuhkan sintering untuk mendapatkan kepadatan penuh.
- DED cepat tetapi sesuai dengan aplikasi industri skala besar.
- Pengguna memilih proses berdasarkan bahan, kualitas, kecepatan, dan kebutuhan anggaran.
Tantangan dan Keterbatasan EBM
Beberapa tantangan dengan EBM meliputi:
- Biaya mesin dan material yang tinggi
- Pemasok peralatan dan dukungan layanan yang terbatas
- Pemilihan material yang terbatas dibandingkan dengan AM lainnya
- Kecepatan pembuatan yang lebih rendah daripada PBF laser
- Penanganan dan daur ulang serbuk logam reaktif
- Pasca-pemrosesan untuk meredakan tekanan internal
- Persyaratan lingkungan vakum selama pembangunan
Pengembangan yang sedang berlangsung bertujuan untuk meningkatkan tingkat pembangunan, menurunkan biaya peralatan, memperluas kemampuan material, dan membuat prosesnya lebih terukur untuk manufaktur volume tinggi.
Prospek Masa Depan untuk Teknologi EBM
Tren masa depan dalam EBM:
- Kecepatan pembuatan yang lebih cepat dengan sistem multi-balok yang lebih baru
- Platform rakitan yang lebih besar dengan ukuran lebih dari 500 mm x 500 mm
- Rangkaian material yang diperluas termasuk lebih banyak paduan aluminium dan tembaga
- Penanganan bubuk yang lebih baik dan daur ulang loop tertutup
- Peningkatan perangkat lunak untuk desain dan pengoptimalan proses
- Mengurangi biaya peralatan dan adopsi yang lebih luas untuk manufaktur penggunaan akhir
- Aplikasi dalam komponen satelit, transportasi listrik, perkakas, dan sektor biomedis
Kemajuan dalam sistem EBM akan memperluas adopsi di seluruh industri kedirgantaraan, otomotif, medis, elektronik, dan energi.
Hal-Hal Penting tentang Teknologi EBM
- EBM menggunakan berkas elektron untuk melebur dan memadukan partikel serbuk logam secara selektif lapis demi lapis.
- Menghasilkan komponen yang mendekati bentuk jaring dengan kemurnian, kepadatan, kekuatan, dan akurasi material yang tinggi.
- Paduan titanium, superalloy nikel, baja perkakas, paduan aluminium adalah bahan yang umum digunakan.
- Sektor kedirgantaraan dan medis adalah pengadopsi utama EBM saat ini.
- Memberikan manfaat lebih dari pengecoran, pemesinan, dan metode AM lainnya untuk geometri yang kompleks.
- Sistem multi-balok secara dramatis meningkatkan kecepatan pembuatan dan skala produksi.
- Pengembangan yang sedang berlangsung bertujuan untuk memperluas kemampuan material dan menurunkan biaya.
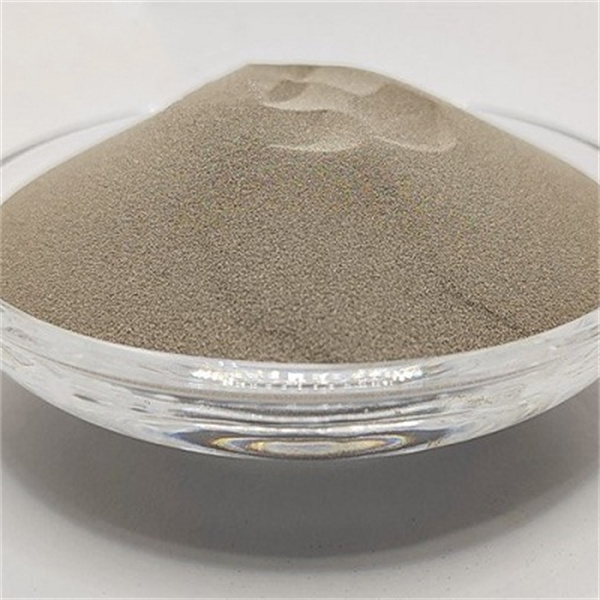
Tanya Jawab Tentang Teknologi EBM
T: Bahan apa saja yang dapat diproses dengan EBM?
J: Bahan EBM yang umum termasuk paduan titanium, superalloy nikel, baja perkakas, baja tahan karat, krom kobalt, paduan aluminium, dan paduan tembaga.
T: Apa saja contoh komponen yang dibuat oleh EBM?
J: EBM digunakan untuk memproduksi komponen kedirgantaraan yang penting seperti bilah turbin, rangka struktural, suku cadang mesin. Ini juga digunakan untuk implan medis, prototipe otomotif, perkakas industri, dan banyak lagi.
T: Seberapa akuratkah EBM?
J: EBM menawarkan akurasi dimensi yang sangat baik dalam deviasi ±0,2% dibandingkan dengan dimensi desain, berkat proses peleburan berkas elektron yang tepat.
T: Apakah EBM lebih cepat daripada metode pencetakan 3D logam seperti DMLS?
J: Secara umum, proses fusi unggun serbuk laser menawarkan kecepatan pembuatan yang lebih cepat daripada EBM saat ini. Tetapi sistem EBM multi-beam yang baru bertujuan untuk menyamai atau melampaui kecepatan PBF laser.
T: Pemrosesan pasca-pemrosesan apa yang diperlukan untuk suku cadang EBM?
J: Pasca-pemrosesan yang umum dilakukan meliputi pelepasan penyangga, perlakuan panas penghilang stres, Hot Isostatic Pressing, dan pemesinan atau penggerindaan jika persyaratan penyelesaian permukaan sangat penting.
T: Apa manfaat EBM multi-beam?
J: Sistem multi-beam menggunakan beberapa berkas elektron paralel untuk melelehkan lapisan. Hal ini memberikan laju pembuatan yang jauh lebih cepat sekaligus mempertahankan sifat material EBM.
T: Apakah EBM menghasilkan komponen berpori atau benar-benar padat?
J: EBM menghasilkan lebih dari 99% komponen padat dan padat sepenuhnya dengan integritas material yang sangat baik dan sifat yang cocok untuk penggunaan akhir fungsional dalam aplikasi yang menuntut.
T: Bagaimana cara mendaur ulang bubuk EBM?
J: Serbuk yang tidak terpakai dapat dikumpulkan, diayak untuk menghilangkan partikel besar, dicampur dengan serbuk baru, dan dimasukkan kembali ke dalam mesin untuk digunakan kembali.
T: Apakah EBM ramah lingkungan?
J: EBM memiliki manfaat keberlanjutan dari tingkat penggunaan ulang serbuk yang tinggi, limbah yang rendah, dan desain yang dioptimalkan ringan yang mengurangi penggunaan material selama siklus hidup komponen.