Gambaran umum tentang Manufaktur MIM
Metal injection molding (MIM) adalah proses manufaktur metalurgi serbuk yang digunakan untuk memproduksi komponen logam yang kecil dan kompleks dengan volume tinggi.
Langkah-langkah utama dalam MIM meliputi:
- Mencampur bubuk logam halus dengan pengikat untuk membuat bahan baku
- Menyuntikkan bahan baku ke dalam cetakan menggunakan cetakan injeksi plastik
- Debinding untuk menghilangkan pengikat yang hanya menyisakan serbuk logam
- Sintering untuk memadatkan serbuk menjadi komponen logam padat
MIM menggabungkan fleksibilitas desain cetakan injeksi plastik dengan kekuatan dan performa logam mesin. Ini adalah proses yang hemat biaya untuk produksi komponen kecil yang kompleks dan bervolume tinggi.
Cara Kerja Manufaktur MIM
Proses pembuatan MIM melibatkan:
- Memformulasikan bahan baku dengan mencampur dan membuat pelet serbuk logam halus dengan pengikat polimer
- Memanaskan bahan baku dan mencetaknya menjadi bentuk yang diinginkan
- Menghilangkan pengikat secara kimiawi melalui pengikatan pelarut atau termal
- Menyinter komponen logam yang terlepas di dalam tungku untuk menghasilkan bagian yang sepenuhnya padat
- Operasi penyelesaian sekunder opsional seperti pemesinan, pengeboran, pelapisan
MIM memungkinkan produksi komponen yang ekonomis dengan geometri yang rumit, toleransi yang ketat dan sifat mekanik yang sangat baik.
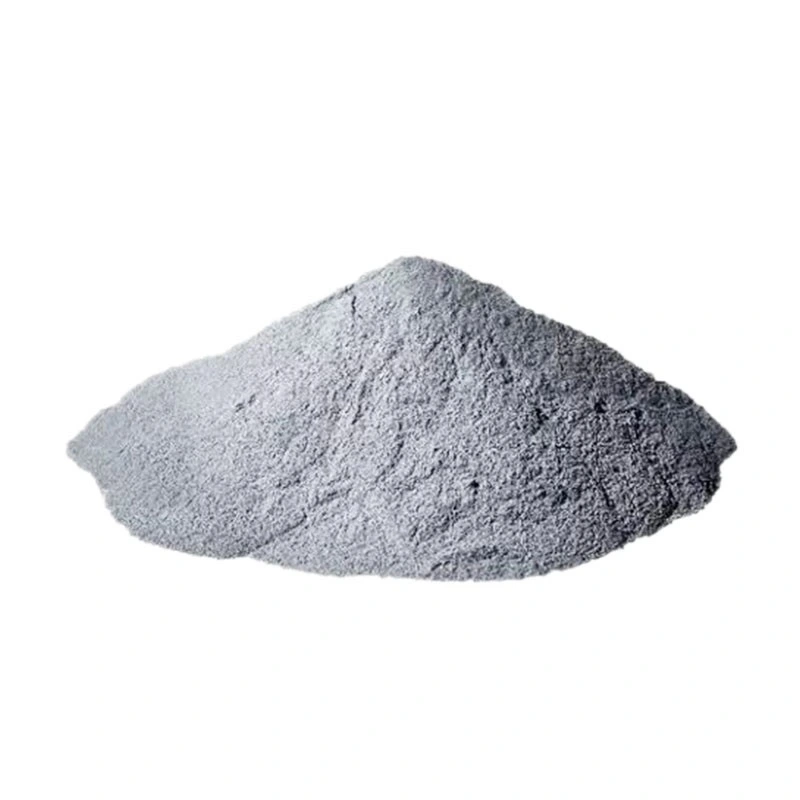
Jenis Logam yang Digunakan dalam MIM
Berbagai macam logam dapat diproses dengan teknologi MIM:
- Baja tahan karat - 316L, 17-4PH, 410, 420
- Baja perkakas - H13, P20, A2, D2
- Paduan magnetik - Ferit lunak dan keras
- Paduan tembaga - Kuningan, perunggu
- Baja paduan rendah - 4100, 4600
- Superalloy - Inconel 625, 718
- Paduan berat tungsten
- Paduan titanium - Ti6Al4V, Ti6Al4V ELI
MIM umumnya cocok untuk bahan apa pun yang dapat disinter hingga kepadatan tinggi. Logam dengan titik leleh di bawah 1000°C lebih disukai.
Parameter Proses Manufaktur MIM
Parameter proses penting dalam MIM meliputi:
Pengembangan bahan baku:
- Morfologi bubuk, distribusi ukuran
- Komposisi pengikat
- Pemuatan bubuk - biasanya 60-65 vol%
- Proses pencampuran - suhu, waktu, atmosfer
Cetakan:
- Bahan cetakan - Baja perkakas P20 lebih disukai
- Suhu, tekanan, kecepatan injeksi
- Desain gerbang
- Desain sistem pendingin
Debinding:
- Pelarut, termal, atau pengikatan katalitik
- Suhu, waktu, atmosfer yang mengikat
Sintering:
- Profil suhu - langkah debinding, sintering
- Laju pemanasan, waktu sintering, atmosfer
- Suhu dan tekanan sintering
Desain MIM dan Pertimbangan Bagian
Proses MIM memungkinkan kebebasan desain, tetapi ada beberapa panduan yang harus diikuti:
- Ketebalan dinding: Kisaran 0,3 - 4 mm mungkin
- Permukaan akhir: As-sinter sekitar Ra 1,5 μm
- Toleransi dimensi: ± 0,5% adalah standar tetapi ± 0,1% dapat dicapai
- Menghindari serbuk yang terperangkap: Tidak ada rongga internal yang tertutup sepenuhnya
- Sudut angin: > Lebih disukai sudut angin 1°
- Penyusutan sintering: Penyusutan volumetrik sekitar 20%
- Mengurangi cacat: Jari-jari sudut yang besar meminimalkan keretakan
Alat simulasi canggih memungkinkan pengoptimalan virtual dari proses MIM selama desain untuk mengurangi coba-coba.
Manfaat dari Manufaktur MIM
Keuntungan utama dari penggunaan MIM antara lain:
- Geometri yang kompleks dan toleransi yang ketat
- Sifat mekanik yang sangat baik
- Beragam pilihan material
- Jumlah produksi tinggi dengan biaya rendah
- Meminimalkan limbah - proses bentuk hampir bersih
- Mengurangi pemesinan dan penyelesaian akhir
- Integrasi komponen dan konsolidasi bagian
- Proses otomatis yang cocok untuk operasi mati lampu
- Lebih ramah lingkungan daripada pemesinan
- Dapat diskalakan dari prototipe hingga produksi penuh
Manfaatnya membuat MIM cocok untuk memproduksi komponen logam presisi dengan biaya yang efektif pada volume tinggi di seluruh industri.
Keterbatasan dan Tantangan MIM
Beberapa keterbatasan yang terkait dengan MIM:
- Ukuran terbatas - biasanya <45 g massa jadi per bagian
- Dibatasi pada logam yang mampu menyinter hingga kepadatan tinggi
- Keahlian yang luas diperlukan dalam formulasi bahan baku
- Biaya di muka untuk pengembangan cetakan dan proses
- Bagian lurus dan sudut tajam yang rentan retak
- Waktu tunggu yang lebih lama dibandingkan dengan proses lainnya
- Pemrosesan pasca sering kali diperlukan untuk mendapatkan properti akhir
- Kurangnya kebebasan mendesain pada beberapa fitur, seperti utas
- Pemesinan sekunder dapat menjadi tantangan pada logam yang disinter
Dengan bahan baku yang tepat dan desain proses yang disesuaikan untuk aplikasi tersebut, tantangan-tantangan ini dapat diatasi untuk memanfaatkan potensi penuh teknologi MIM.
Aplikasi Suku Cadang yang Diproduksi MIM
MIM digunakan secara luas di berbagai sektor berikut ini:
Otomotif: Perangkat keras pengunci, sensor, sistem bahan bakar, dan komponen mesin
Dirgantara: Impeler, nozel, katup, pengencang
Medis: Implan gigi, gagang pisau bedah, instrumen ortopedi
Senjata api: Pemicu, majalah, slide, palu
Jam tangan: Casing, tautan gelang, jepitan, dan gesper
Listrik: Konektor dan rangka utama untuk keandalan
Ukuran komponen yang umum berkisar antara 0,1 gram hingga 110 gram dengan volume produksi komersial terbesar pada konektor, pengencang, instrumen bedah, dan kawat gigi ortodontik.
Analisis Biaya Pembuatan MIM
Biaya produksi MIM meliputi:
- Pengembangan bahan baku - Formulasi, pencampuran, karakterisasi
- Fabrikasi cetakan - Pemesinan cetakan presisi tinggi
- Mesin MIM - Investasi peralatan modal besar
- Operasi - Tenaga kerja, utilitas, bahan habis pakai
- Operasi sekunder - Pengikatan, penyinteran, finishing
- Pemanfaatan material - Serbuk logam menyumbang sekitar 60% dari total biaya
- Perkakas habis pakai - Beberapa rongga cetakan untuk memungkinkan volume tinggi
- Volume produksi - Biaya penyiapan diamortisasi atas total volume
- Rasio beli-ke-terbang - Hanya 2-4x dibandingkan dengan proses PM lainnya
- Optimalisasi desain - Geometri sederhana dengan pemesinan minimal
Untuk volume produksi yang besar, MIM memberikan biaya yang sangat menguntungkan dengan tingkat produksi yang tinggi dengan pemanfaatan material yang sangat baik dan kemampuan yang mendekati bentuk bersih.
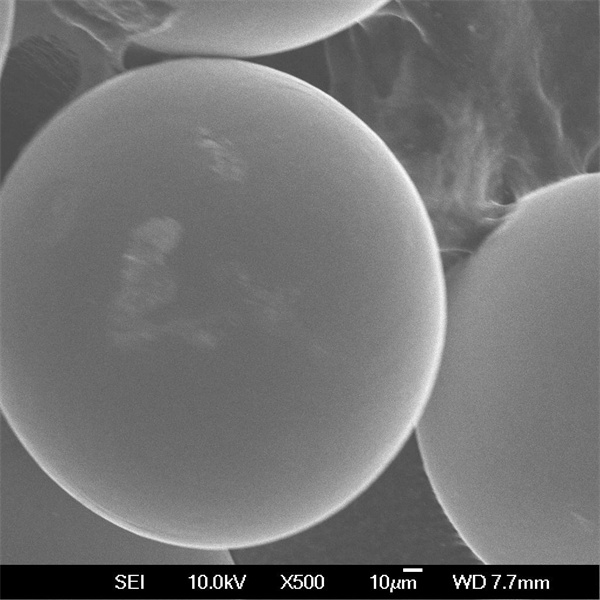
Memilih Manufaktur MIM Mitra
Faktor-faktor utama saat memilih pemasok MIM:
- Keahlian yang ditunjukkan dan pengalaman bertahun-tahun dengan MIM
- Portofolio material - berbagai pilihan baja tahan karat, baja perkakas, dan superalloy
- Sertifikasi kualitas - ISO 9001, ISO 13485 lebih disukai
- Kemampuan pemrosesan sekunder - pemesinan, perlakuan panas, finishing permukaan
- Prosedur kontrol kualitas proses dan produk yang ketat
- Kemampuan R&D untuk formulasi bahan baku dan pengembangan proses
- Simulasi aliran cetakan dan keahlian analisis desain lainnya
- Keahlian manajemen program untuk mendukung proyek-proyek pelanggan
- Kapasitas yang dapat ditingkatkan sesuai dengan kebutuhan produksi
- Harga kompetitif dengan perjanjian multi-tahun
- Lokasi yang memungkinkan kolaborasi erat dan perlindungan hak kekayaan intelektual
Memilih produsen MIM yang sudah mapan dengan fokus khusus pada MIM akan memberikan hasil terbaik dibandingkan dengan toko mesin logam CNC pada umumnya.
Pro dan Kontra Pemesinan MIM vs CNC
Keuntungan dari MIM:
- Akurasi dan pengulangan dimensi yang sangat baik
- Geometri kompleks yang tidak dapat dicapai melalui pemesinan
- Bentuk mendekati jaring dengan limbah material yang minimal
- Skala yang efisien untuk volume produksi yang sangat tinggi
- Proses otomatis memungkinkan pengoperasian 24/7
- Waktu tunggu yang lebih singkat setelah penyiapan
- Biaya suku cadang yang jauh lebih rendah pada volume tinggi
- Sifatnya cocok atau melebihi logam mesin
Kekurangan MIM:
- Biaya penyiapan awal yang tinggi untuk bahan baku dan cetakan
- Kemampuan ukuran terbatas
- Kebebasan desain yang terbatas pada beberapa fitur
- Jumlah produksi awal yang lebih rendah tidak efisien
- Keahlian yang luas diperlukan dalam formulasi bahan baku
- Operasi penyelesaian sekunder mungkin masih diperlukan
- Waktu tunggu yang lebih lama dan kualitas yang lebih rendah untuk prototipe awal
Untuk komponen logam kecil yang kompleks yang diproduksi dalam volume yang sangat tinggi, MIM menjadi metode manufaktur yang paling efisien dari segi waktu dan biaya.
Perbandingan Antara Pencetakan 3D MIM dan Logam
Perbedaan utama pencetakan MIM vs 3D:
Parameter | MIM | Pencetakan 3D |
---|---|---|
Proses | Cetakan injeksi pengikat + sintering | Fusi atau pengikatan bedengan bubuk |
Bahan | Berbagai macam paduan | Pilihan material yang terbatas |
Ukuran bagian | <45 gram | Hingga beberapa kg |
Akurasi | Luar biasa, ± 0,5% | Sedang, ± 1% |
Permukaan akhir | Sangat bagus | Sedang hingga buruk |
Skala produksi | 10.000 hingga jutaan | Pembuatan prototipe hingga volume sedang |
Biaya per bagian | Sangat rendah | Sedang hingga tinggi |
Penyelesaian sekunder | Mungkin diperlukan | Biasanya diperlukan |
Waktu tunggu | Lebih lama untuk pengembangan proses | Prototipe yang lebih cepat tetapi produksi serial yang lebih lambat |
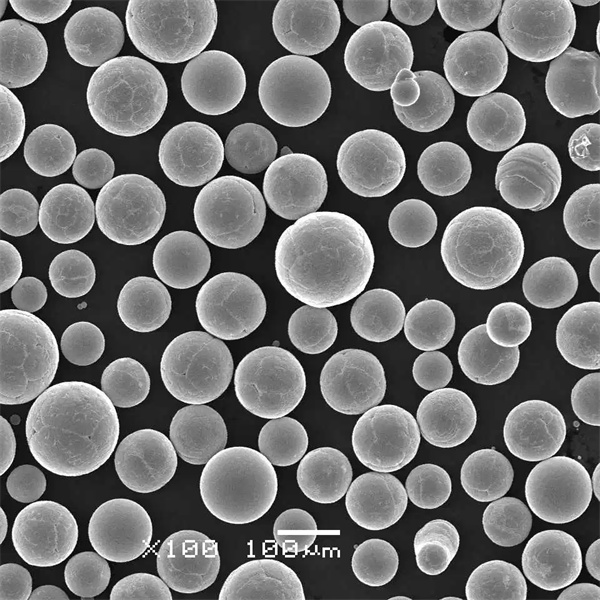
PERTANYAAN YANG SERING DIAJUKAN
Apa kemampuan toleransi tipikal untuk manufaktur MIM?
MIM dapat diandalkan untuk mencapai toleransi dimensi ± 0,5% dengan proses lanjutan yang mampu mencapai toleransi ± 0,1% untuk komponen presisi kecil.
Apa saja komposisi bahan baku MIM yang umum?
Bahan baku MIM yang umum terdiri dari pemuatan serbuk logam 60-65% dengan pengikat 35-40% yang terdiri dari polimer seperti polipropilena, polietilena, dan polistirena. Lilin membantu meningkatkan aliran bubuk.
Dapatkah MIM memproduksi komponen dalam berbagai bahan?
Ya, MIM dapat menghasilkan struktur komposit dan bergradasi dengan mencetak injeksi bahan baku yang berbeda ke dalam setiap rongga cetakan atau menggunakan pengikat dengan titik leleh yang berbeda.
Berapa ukuran bagian cetakan yang dapat dicapai dengan MIM?
Cetakan MIM biasanya terbatas pada komponen yang lebih kecil dari 45 gram dan dimensi kurang dari 50 mm. Komponen yang lebih besar atau lebih berat menjadi sulit untuk diisi dan dipadatkan secara memadai.
Bagaimana MIM dibandingkan dengan die casting untuk komponen logam kecil?
MIM memberikan akurasi dimensi dan kekuatan material yang lebih tinggi, tetapi die casting memiliki waktu siklus yang lebih cepat. MIM lebih cocok untuk geometri yang kompleks sementara die casting lebih disukai untuk bentuk yang lebih sederhana.