Ikhtisar
Inconel 718 adalah superalloy nikel-kromium berkekuatan tinggi yang banyak digunakan untuk aplikasi suhu ekstrem seperti komponen turbin gas, mesin roket, dan reaktor nuklir. Kombinasi sifat mekanik yang sangat baik, ketahanan terhadap korosi, dan kemampuan kerja menjadikan Inconel 718 sebagai bahan serbaguna di berbagai industri seperti kedirgantaraan, minyak dan gas, pembangkit listrik, dan otomotif.
Dalam beberapa tahun terakhir, manufaktur aditif (AM) Inconel 718 telah muncul sebagai metode produksi transformatif untuk membuat komponen logam yang kompleks dan berkinerja tinggi. Juga dikenal sebagai pencetakan 3D, AM membangun komponen lapis demi lapis langsung dari model 3D tanpa kendala pemesinan atau pengecoran tradisional.
Panduan ini memberikan gambaran mendalam tentang Pencetakan 3D Inconel 718termasuk sifat paduan, jenis proses AM yang populer, parameter, mikrostruktur, perilaku mekanis, pasca-pemrosesan, aplikasi, dan pemasok. Hal ini bertujuan untuk membantu para insinyur, perancang, dan manajer program teknis dalam mengimplementasikan pencetakan 3D Inconel 718 dan memenuhi syarat suku cadang yang dicetak untuk penggunaan produksi.
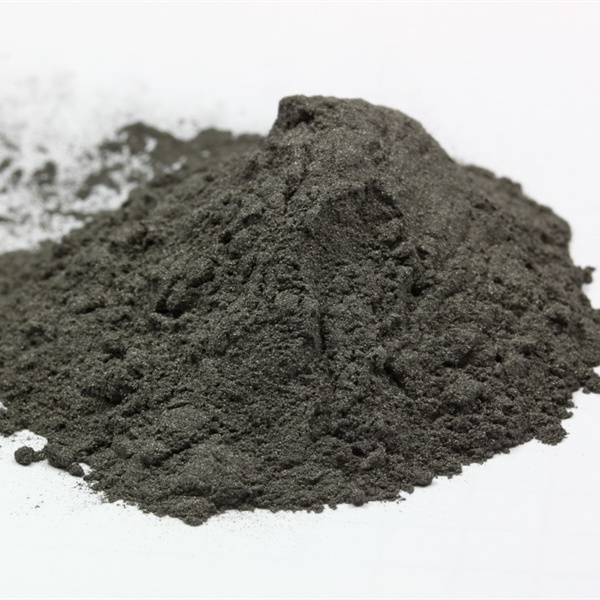
Ikhtisar Paduan Inconel 718
Inconel 718 adalah paduan nikel-kromium yang dikeraskan dengan presipitasi yang mengandung elemen paduan penting seperti niobium, molibdenum, aluminium, dan titanium.
Komposisi Inconel 718
Elemen | Berat % | Tujuan |
---|---|---|
Nikel | 50-55% | Ketahanan korosi, keuletan |
Kromium | 17-21% | Ketahanan oksidasi |
Besi | Keseimbangan | Efektivitas biaya |
Niobium | 4.75-5.5% | Penguatan curah hujan |
Molibdenum | 2.8-3.3% | Penguatan solusi yang solid |
Nikel dan kromium memberikan ketahanan terhadap korosi dan stabilitas suhu tinggi. Elemen pengerasan seperti niobium dan molibdenum memberikan kekuatan yang unggul melalui presipitasi dan mekanisme penguatan larutan padat.
Properti Inconel 718
- Kekuatan luar biasa hingga 700°C
- Ketangguhan benturan tinggi dan ketahanan lelah
- Ketahanan oksidasi dan korosi yang baik
- Kekuatan pecah creep yang tinggi
- Mudah dibentuk dan dilas dengan teknik standar
- Kepadatan 8,19 g/cm3
Kombinasi properti ini membuat Inconel 718 cocok untuk lingkungan yang ekstrem di luar kemampuan baja dan paduan aluminium.
Inconel 718 pencetakan 3D Proses
Beberapa proses manufaktur aditif telah menunjukkan keberhasilan dengan Inconel 718 dan melihat peningkatan adopsi untuk aplikasi produksi:
Proses AM Populer untuk Inconel 718
Proses | Deskripsi | Kepadatan | Struktur mikro | Sifat Mekanis |
---|---|---|---|---|
Laser Powder Bed Fusion (L-PBF) | Laser melelehkan lapisan bubuk | 99.5%+ | Butir kolumnar, beberapa porositas | Kekuatan tarik dalam rentang tempa |
Fusi Bedengan Serbuk Berkas Elektron (E-PBF) | Sinar elektron melelehkan bubuk | 99.5%+ | Butir kolumnar, beberapa porositas | Kekuatan tarik dalam rentang tempa |
Deposisi Energi Terarah (DED) | Sumber panas terfokus melelehkan bubuk atau umpan kawat | 99% | Butir epitaxial, beberapa porositas | Variabel berdasarkan parameter proses |
Pengaliran Pengikat | Pengikat cair secara selektif bergabung dengan partikel bubuk | 60%+ | Berpori, membutuhkan infiltrasi | Rendah saat dicetak, meningkat dengan infiltrasi |
L-PBF dan E-PBF dapat mencapai kepadatan lebih dari 99,5% dengan sifat yang mendekati Inconel 718 tempa. Pengaliran DED dan pengikat membutuhkan pasca-pemrosesan untuk mencapai kepadatan penuh.
Setiap proses memerlukan optimalisasi parameter cetak untuk mencapai struktur mikro dan properti yang diinginkan.
Parameter Pencetakan 3D Inconel 718
Parameter pencetakan secara signifikan memengaruhi struktur mikro yang dihasilkan, cacat, dan kinerja mekanis komponen Inconel 718 yang dicetak.
Parameter Cetak Kunci Inconel 718
Parameter | Kisaran Khas | Dampak |
---|---|---|
Ketebalan lapisan | 20-100 μm | Kepadatan, permukaan akhir |
Daya laser/sinar | 100-500 W | Ukuran kolam leleh, laju pemanasan |
Kecepatan pemindaian | 100-1000 mm/s | Laju pendinginan, pemadatan |
Jarak penetasan | 50-200 μm | Ikatan antar palka |
Fokus sinar | 30-100 μm | Lebar dan kedalaman kolam leleh |
Ukuran bubuk | 10-45 μm | Aliran bubuk, permukaan akhir |
Lapisan yang lebih tipis dan palka yang lebih sempit meningkatkan kepadatan dan ikatan, tetapi mengurangi kecepatan pembuatan. Pemindaian yang lebih cepat menghasilkan butiran yang lebih halus tetapi dapat menyebabkan keretakan panas. Ukuran serbuk yang kecil meningkatkan hasil akhir permukaan.
Optimalisasi parameter yang cermat menyesuaikan kekuatan struktur butiran, keuletan, kualitas permukaan, dan produktivitas pencetakan.
Struktur Mikro Pencetakan 3D Inconel 718
Inconel 718 menunjukkan struktur mikro yang beragam apabila dicetak menggunakan proses AM:
Fitur Mikrostruktur dalam Inconel 718 yang Dicetak
- Butir-butir kolumnar sejajar dengan arah bangunan
- Butir epitaxial yang cocok dengan orientasi pelat dasar
- Lebar butiran tipikal 100-400 μm
- Pemisahan solidifikasi antara inti dendrit dan daerah interdendritik
- Kurangnya tekstur dibandingkan dengan produk tempa
- Pengendapan fase penguatan seperti γ" dan γ'
- Porositas dan retakan mikro akibat fusi yang tidak sempurna
Morfologi butiran mengikuti aliran panas dan pola pemadatan selama pencetakan. Pemisahan menyebabkan variasi kimiawi yang dapat menyebabkan keretakan. Pemrosesan yang cermat diperlukan untuk mencapai struktur mikro yang seragam dan terkontrol.
Perlakuan panas melarutkan fasa yang tidak diinginkan dan meningkatkan endapan pengerasan seperti Ni3Nb gamma-double-prime untuk kekuatan yang optimal.
Properti Inconel 718 yang Dicetak
Pemrosesan AM dapat mencapai sifat mekanik yang sebanding dengan Inconel 718 tempa dengan pengoptimalan yang tepat:
Sifat Mekanis Inconel 718
Properti | Sebagai-Cetak | Tempa Pabrik-Anil-Anil |
---|---|---|
Kekuatan Tarik | 1000-1300 MPa | 1000-1200 MPa |
Kekuatan Hasil | 500-1100 MPa | 500-900 MPa |
Perpanjangan | 10-35% | 20-35% |
Kekuatan Kelelahan | 100-600 MPa | 300-500 MPa |
Kekerasan | 25-50 HRC | 25-35 HRC |
Kekuatannya memenuhi atau melampaui tingkat tempa, meskipun sifat perpanjangan dan kelelahan tetap lebih rendah dan lebih bervariasi.
Anisotropi tarik diamati antara orientasi pembuatan vertikal dan horizontal. Properti sangat dipengaruhi oleh parameter proses AM spesifik yang digunakan.
Pasca-Pemrosesan Cetak Inconel 718
Proses pasca-cetak sering kali diperlukan untuk meningkatkan hasil akhir permukaan, akurasi dimensi, dan sifat material:
Metode Pasca-Pemrosesan Umum
- Perlakuan panas - Mengembangkan struktur mikro yang optimal dan pengerasan endapan
- Penekanan isostatik panas - Menutup rongga dan porositas internal
- Pemesinan permukaan - Mengurangi kekasaran permukaan untuk hasil akhir yang kritis
- Shot peening - Menginduksi tegangan tekan untuk meningkatkan umur kelelahan
- Pelapis - Memberikan ketahanan aus atau korosi bila diperlukan
Pengerasan usia standar Inconel 718 umumnya digunakan, meskipun beberapa memodifikasi perlakuan panas untuk struktur mikro AM. Pemesinan, penggilingan atau pemolesan digunakan di mana persyaratan permukaan akhir sangat ketat.
Aplikasi Inconel 718 yang Dicetak
Pencetakan 3D Inconel 718 sangat cocok untuk itu:
- Dirgantara - Komponen turbin, nozel roket, rakitan mesin
- Pembangkit listrik - Bagian bagian panas turbin gas, kelongsong bahan bakar nuklir
- Otomotif - Roda dan rumah turbocharger
- Petrokimia - Alat-alat lubang bawah, katup, pompa
- Ruang - Komponen satelit dan landasan peluncuran
- Obat-obatan - Implan gigi, instrumen bedah
Manfaat dibandingkan metode konvensional:
- Kebebasan mendesain untuk geometri yang kompleks
- Pengurangan bobot melalui kisi-kisi dan pengoptimalan topologi
- Konsolidasi bagian, mengurangi perakitan
- Waktu tunggu yang lebih singkat untuk produksi sesuai permintaan
- Bentuk yang disesuaikan, inventaris yang digerakkan secara digital
Keterbatasan termasuk biaya proses untuk volume produksi yang rendah dan tantangan sertifikasi dalam industri yang diatur.
Pemasok dari Dicetak Inconel 718
Banyak produsen menawarkan layanan pencetakan 3D Inconel 718 di seluruh dunia:
Pilih Penyedia Layanan
Perusahaan | Proses AM | Bahan Tambahan | Kapasitas Produksi |
---|---|---|---|
Aditif GE | DED, Pengaliran Pengikat | Paduan titanium, baja, superalloy | Volume besar |
Mewujudkan | Laser PBF | Titanium, aluminium, baja | Volume sedang |
Sistem 3D | Laser PBF, Pengaliran Pengikat | Titanium, baja tahan karat, CoCr, AlSi10Mg | Pembuatan prototipe hingga volume menengah |
Equispheres | Laser PBF | Titanium, baja, aluminium | Volume kecil |
Aditif Tukang Kayu | Laser PBF, E-PBF | Titanium, baja tahan karat, baja perkakas | Volume sedang |
Baik OEM besar maupun biro layanan AM khusus menawarkan pencetakan Inconel 718. Banyak yang menyediakan operasi finishing sekunder.
Biaya suku cadang berkisar dari perkiraan $100-500 / lb tergantung pada ukuran pesanan, persyaratan kualitas, dan metode pemrosesan yang digunakan.
Suku Cadang Inconel 718 Cetak yang Memenuhi Syarat
Protokol kualifikasi yang ketat berlaku untuk ruang angkasa dan aplikasi yang diatur lainnya:
- Pengujian mekanis pada berbagai orientasi cetak
- Analisis kimia untuk kesesuaian komposisi
- Evaluasi non-destruktif (NDE) untuk deteksi cacat
- Evaluasi kinerja jangka panjang melalui perlakuan panas, pengepresan isostatik panas, uji coba pemesinan
- Penilaian reproduktifitas proses
- Dokumentasi optimalisasi parameter, struktur mikro, pencegahan cacat
Artefak uji seperti batang tarik, sampel fatik, dan kupon material mengoptimalkan karakterisasi sifat cetak.
Mematuhi spesifikasi industri yang berlaku mendukung sertifikasi dan persetujuan produksi.
PERTANYAAN YANG SERING DIAJUKAN
Berapa ukuran partikel yang direkomendasikan untuk mencetak Inconel 718?
Serbuk 10-45 mikron adalah tipikal, dengan serbuk yang lebih halus ~15 mikron meningkatkan kepadatan dan permukaan akhir tetapi mengorbankan aliran dan pemulihan.
Apa yang menyebabkan porositas saat mencetak Inconel 718?
Peleburan yang tidak mencukupi, kurangnya fusi antar lapisan, dan gas yang terperangkap menyebabkan kekosongan. Mengoptimalkan masukan energi, pola pemindaian, ketebalan lapisan, dan aliran gas akan mengurangi porositas.
Pasca-pemrosesan apa yang meningkatkan masa pakai Inconel 718 yang dicetak?
Shot peening menginduksi tegangan tekan yang menguntungkan yang menghambat inisiasi dan pertumbuhan retak. HIP dan pemesinan juga membantu dengan menutup pori-pori permukaan.
Bagaimana Inconel 718 yang dicetak dibandingkan dengan 718 yang dicetak dan ditempa?
AM mendekati sifat mekanik material cor dan tempa tetapi dengan struktur mikro yang lebih halus dan lebih terpisah. Perlakuan panas dapat mencapai penguatan presipitasi yang sebanding dengan produk tempa.
Apa saja alternatif selain Inconel 718 untuk pencetakan 3D?
Krom kobalt, superalloy nikel seperti 625 dan 686, dan baja tahan karat pengerasan presipitasi menawarkan sifat suhu tinggi yang serupa. Paduan titanium unggul di mana kepadatan yang lebih rendah sangat penting.
Dapatkah Anda mencetak 3D bagian bimetal Inconel 718 dan baja tahan karat?
Ya, deposisi energi terarah mampu bertransisi di antara paduan yang berbeda dengan peralihan serbuk atau kawat yang tepat untuk membangun komponen multi-material.
Kesimpulan
Singkatnya, pencetakan 3D Inconel 718 melepaskan kebebasan desain yang luar biasa dan peningkatan kinerja dengan memanfaatkan superalloy berkekuatan tinggi ini. Mencocokkan persyaratan komponen dengan kemampuan proses dan mengoptimalkan parameter pencetakan adalah kunci untuk mengeksploitasi manfaat dibandingkan metode konvensional. Kemajuan yang sedang berlangsung dalam kualitas, properti, struktur multi-material, dan biaya terus memperluas adopsi Inconel 718 AM di seluruh aplikasi industri yang menuntut.