Bubuk besi paduan mengacu pada serbuk besi dengan elemen paduan untuk meningkatkan sifat. Panduan ini memberikan gambaran komprehensif tentang jenis, komposisi, karakteristik, penggunaan, pemasok, dan perbandingan serbuk besi paduan.
Gambaran Umum Bubuk Besi Paduan
Poin-poin penting tentang bubuk besi paduan:
- Serbuk besi dasar dengan elemen paduan yang ditambahkan
- Memberikan kekuatan, kekerasan, dan ketahanan aus yang lebih tinggi daripada besi biasa
- Paduan yang umum termasuk jenis baja tahan karat, baja perkakas, dan paduan rendah
- Digunakan dalam metalurgi serbuk dan manufaktur aditif
- Properti yang dapat disesuaikan dengan menyesuaikan komposisi
- Tersedia dalam paduan standar dan khusus
Paduan memperluas kemampuan serbuk besi pada aplikasi yang lebih menuntut.
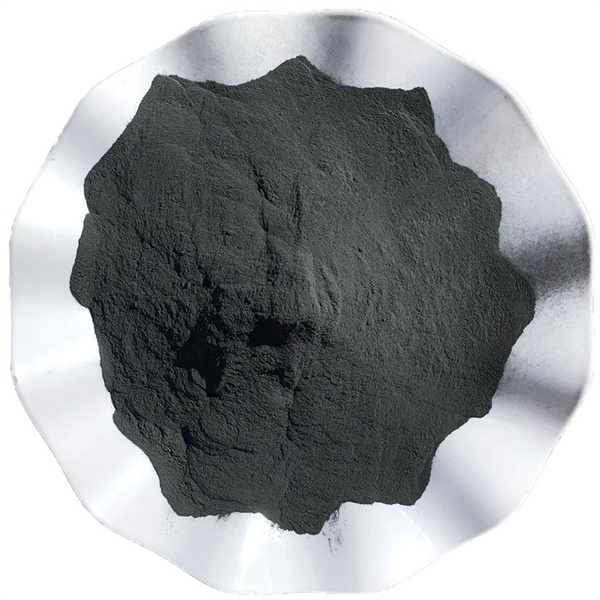
Komposisi Serbuk Paduan
Berbagai elemen paduan ditambahkan ke bubuk besi:
Komposisi Serbuk Paduan Umum
Jenis Paduan | Komposisi khas |
---|---|
Tahan karat | Fe + 10-30% Cr + Ni, Mn, Mo |
Baja perkakas | Fe + Cr, Mo, V, Mn, C |
Paduan rendah | Fe + <10% Cr, Mo, Cu, Ni |
Karbon, tembaga, nikel, kromium, molibdenum, mangan, dan vanadium adalah tambahan yang umum.
Karakteristik dan Properti
Paduan memodifikasi sifat fisik dan mekanik:
- Kekuatan dan kekerasan yang lebih tinggi
- Peningkatan ketahanan aus dan daya tahan
- Sifat suhu tinggi yang ditingkatkan
- Ketahanan korosi yang lebih baik
- Lebih banyak variasi dalam sifat magnetik
- Kepadatan yang lebih berat dibandingkan dengan besi biasa
Paduan yang tepat mengoptimalkan properti untuk aplikasi yang membutuhkan performa yang lebih tinggi.
Aplikasi dari Bubuk Besi Paduan
Penggunaan yang umum dilakukan dengan memanfaatkan sifat serbuk besi paduan:
- Suku cadang otomotif - roda gigi, cincin piston, sinkronisasi
- Pemrosesan bahan - perkakas logam bubuk
- Daya fluida - katup, tutup, segel, pembawa bantalan
- Magnet - komponen rendah/non-magnetik
- Manufaktur aditif - perkakas dan komponen cetak 3D
- Suku cadang aus - bantalan, bushing, pukulan
- Komponen gesekan - rem, kopling, komponen transmisi
Paduan memperluas ruang desain untuk komponen besi bubuk berkinerja tinggi.
Spesifikasi dan nilai
Tersedia berbagai kualitas bubuk besi paduan standar:
- FSM-HP: 4% Ni, bubuk besi 1,5% Cu
- FLN2-4405: 2% Ni, 1% Cu, 0,5% bubuk besi Mo
- Ancorsteel 1000B: 1% Ni, bubuk besi 0,5% Mn
- ATOMET EM-1: Fe + 1.5% Ni + Mo, Cu, C
- Komposisi paduan khusus dimungkinkan
Spesifikasi termasuk ISO, ASTM, ANSI, dan standar internal dari pemasok.
Bubuk Besi Paduan Pemasok
Pemasok global terkemuka untuk bubuk besi paduan meliputi:
- Höganäs - Berbagai macam nilai paduan air dan gas yang dikabutkan
- Rio Tinto Metal Powders - AncorSteel, paduan yang disesuaikan dengan Atomet
- JFE Steel - Baja tahan karat, baja perkakas, kelas paduan rendah
- CNPC Powder - Nilai paduan rendah dan nilai tahan karat
- BASF - Serbuk besi paduan khusus untuk pembuatan aditif
Memilih pemasok yang memenuhi syarat memastikan bubuk paduan yang andal dan konsisten.
Pro dan Kontra Bubuk Paduan
Keuntungan | Kekurangan |
---|---|
Kekuatan dan ketahanan aus yang lebih tinggi | Lebih mahal dari bubuk besi biasa |
Peningkatan sifat suhu tinggi | Kompresibilitas yang lebih rendah membutuhkan tekanan tekan yang lebih tinggi |
Ketahanan korosi yang lebih baik | Lebih sulit untuk dipadatkan sepenuhnya setelah pemadatan |
Pengoptimalan paduan khusus | Peningkatan pemisahan bubuk selama penanganan |
Mencocokkan properti dengan aplikasi | Keterbatasan pada geometri dan ukuran |
Pemilihan paduan yang tepat menyeimbangkan performa dan kemampuan produksi.
Paduan vs Serbuk Besi Biasa
Parameter | Bubuk Besi Paduan | Bubuk Besi Biasa |
---|---|---|
Biaya | Lebih mahal | Bahan berbiaya lebih rendah |
Properti | Lebih kuat, lebih keras, lebih banyak variasi | Kekuatan dan kekerasan yang lebih rendah |
Kemampuan kerja | Lebih menantang untuk dipadatkan dan disinter | Lebih mudah mencapai densitas penuh |
Aplikasi | Komponen berkinerja tinggi | Suku cadang dengan tegangan rendah untuk keperluan umum |
Kustomisasi | Jangkauan properti yang lebih luas | Penyesuaian properti terbatas |
Pilihan yang tepat tergantung pada biaya, performa dan kebutuhan manufaktur.
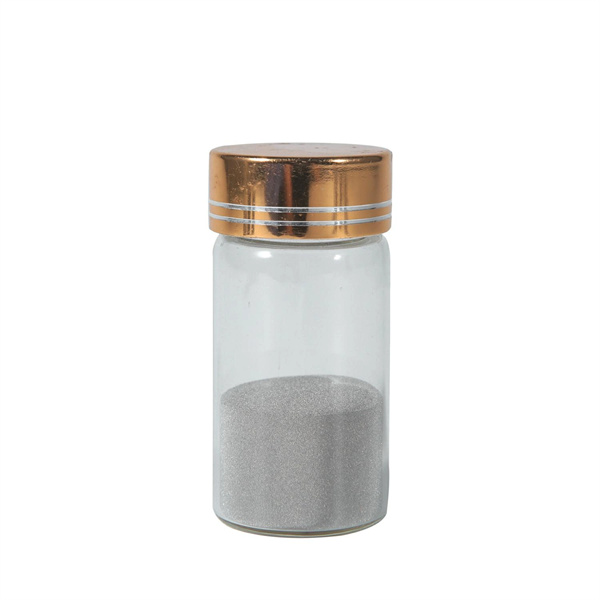
PERTANYAAN YANG SERING DIAJUKAN
Untuk apa bubuk besi paduan digunakan?
Serbuk besi paduan digunakan untuk membuat komponen logam serbuk berkinerja tinggi untuk otomotif, tenaga fluida, magnetik, keausan, dan aplikasi suhu tinggi.
Apa perbedaan antara besi biasa dan serbuk paduan?
Serbuk paduan mengandung unsur-unsur seperti nikel, tembaga, kromium, dan molibdenum yang ditambahkan ke besi untuk mencapai kekuatan yang lebih tinggi, ketahanan aus, dan sifat-sifat lain yang tidak dapat dicapai dengan besi biasa.
Apakah serbuk besi paduan lebih mahal?
Ya, serbuk paduan menimbulkan biaya tambahan untuk elemen paduan. Namun, mereka memungkinkan aplikasi bernilai tambah tinggi yang membenarkan harga yang lebih tinggi.
Komposisi paduan apa yang tersedia?
Paduan yang umum termasuk stainless, baja perkakas, dan campuran paduan rendah. Komposisi paduan khusus juga dapat diproduksi untuk memenuhi persyaratan aplikasi.
Bagaimana elemen paduan mengubah sifat bubuk?
Unsur-unsur seperti nikel, kromium, dan molibdenum meningkatkan kekuatan, ketahanan aus, kekerasan, dan sifat temperatur tinggi. Mangan meningkatkan kemampuan pengerasan. Karbon meningkatkan ketahanan aus saat dipadukan.
Pemilihan paduan yang cermat akan membuka potensi penuh serbuk besi untuk desain komponen yang menantang.
Kesimpulan
Serbuk besi paduan dibuat berdasarkan keunggulan manufaktur serbuk besi dengan menggabungkan elemen-elemen seperti nikel, kromium, molibdenum, tembaga, dan karbon untuk meningkatkan sifat-sifatnya. Hasilnya adalah serbuk besi yang mampu menyamai persyaratan kinerja untuk kekuatan, keausan, suhu tinggi, dan ketahanan korosi yang diperlukan dalam aplikasi otomotif, kedirgantaraan, tenaga fluida, dan industri yang kritis. Seiring dengan kemajuan metalurgi serbuk dan manufaktur aditif logam, serbuk besi paduan akan memainkan peran penting dalam mendorong batas-batas dengan komponen berbasis serbuk yang semakin mumpuni.