aluminum powder for 3d printing is increasingly used in additive manufacturing to create lightweight, high-strength parts across industries. This guide provides a comprehensive overview of aluminum powders for 3D printing.
Introduction to Aluminum Powder for AM
Aluminum is a popular material for 3D printing due to:
- Low density – 2.7 g/cc
- High specific strength
- Konduktivitas termal dan listrik yang sangat baik
- Ketahanan korosi yang baik
- Weldability and machinability
- Low material costs
Key properties of aluminum powder:
- Spherical powder morphology
- Distribusi ukuran partikel yang terkendali
- High purity levels over 99.5% Al
- Derived from recycled aluminum in some cases
- Available for binder jetting, DMLS, SLM processes
Aluminum powder enables printing of lightweight components impossible to manufacture by other methods.
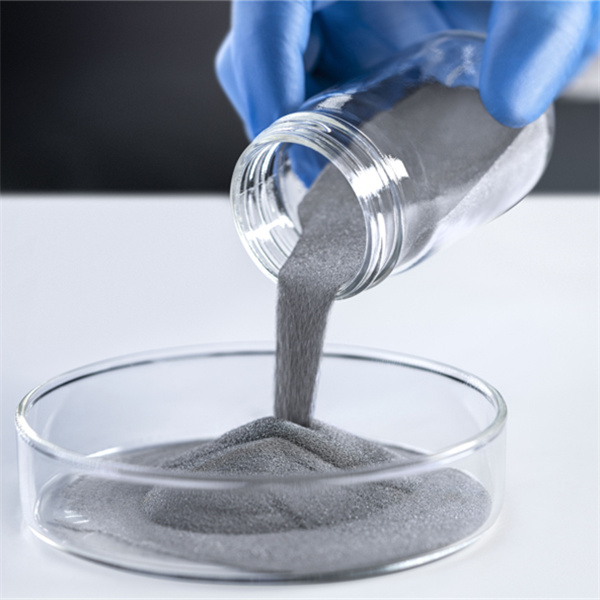
Aluminum Powder Types for Additive Manufacturing
Various aluminum alloy powders are used for AM:
Aluminum Powder Types for 3D Printing
Jenis | Deskripsi | Aplikasi |
---|---|---|
AlSi10Mg | Cast alloy with silicon and magnesium | Kedirgantaraan, otomotif |
AlSi7Mg | Moderate strength alloy with Si, Mg | Industrial machines |
6061 | Medium strength wrought alloy with Mg, Si | Custom brackets, fixtures |
5XXX series | 5% magnesium for strength | Tooling, marine |
Pure aluminum | Unalloyed aluminum >99.7% | Thermal management, electrical |
Specialized alloys are being qualified for additive techniques to match conventional alloy properties.
Komposisi dari aluminum powder for 3d printing
Typical composition of aluminum alloy powders for AM:
Composition of Aluminum Print Powders
Paduan | Al | Mg | Si | Fe | Cu | Mn |
---|---|---|---|---|---|---|
AlSi10Mg | Bal. | 0.2-0.5% | 9-11% | <0.55% | <0,05% | <0.45% |
AlSi7Mg | Bal. | 0.1-0.5% | 6-8% | <1% | <0.1% | <0.1% |
6061 | Bal. | 0.8-1.2% | 0.4-0.8% | <0.7% | 0.15-0.4% | <0.15% |
5056 | Bal. | 4.5-6% | <0.4% | <0.5% | <0.1% | 0.1-0.5% |
Silicon improves castability and fluidity. Magnesium enhances strength. Impurities are minimized for AM suitability.
Key Properties of Aluminum Print Powder
Properties of Aluminum Print Powder
Properti | Nilai |
---|---|
Kepadatan | 2,7 g/cc |
Titik leleh | 475-650°C |
Konduktivitas termal | 120-180 W/mK |
Konduktivitas listrik | 35-38 MS/m |
Kekuatan tarik | 230-520 MPa |
Perpanjangan | 3-8% |
Modulus Young | 68-72 GPa |
Kekerasan | 65-100 HB |
The properties make aluminum suitable for lightweight, thermally and electrically conductive printed parts.
Aluminum Powder Characteristics for AM
Aluminum Powder Characteristics
Parameter | Detail | Signifikansi |
---|---|---|
Bentuk partikel | Bulat | Meningkatkan kemampuan mengalir |
Distribusi ukuran | 10-100 μm | Controls part resolution |
Kepadatan yang tampak | 1.2-1.8 g/cc | Affects final part density |
Laju aliran | 20-30 s/50g | Indicates powder spreadability |
Kandungan oksida | < 3% | Impacts powder flow and sintering |
Kandungan hidrogen | <0,15% | Reduces porosity in parts |
Sphericity and controlled particle size distribution are critical for aluminum AM powders.
Specifications for Aluminum Print Powder
Aluminum Powder Specifications
Parameter | Range/Limit | Standar |
---|---|---|
Ukuran partikel | 10-63 μm | ASTM B214 |
Kepadatan yang tampak | > 0.80 g/cc | ASTM B212 |
Laju aliran aula | < 30 s/50g | ASTM B213 |
Kandungan oksida | < 3% | ASTM B237 |
Mg, Si composition | Alloy limits | ASTM B937 |
Kotoran | Fe, Cu, Mn limits | ASTM B937 |
Key powder characteristics and composition are verified against standardized specifications.
Benefits of Using aluminum powder for 3d printing
Benefits of Aluminum for 3D Printing
- Lightweighting – high strength-to-weight ratio
- Reduced material waste
- Increased design freedom and part consolidation
- Elimination of tooling and machining
- On-demand and just-in-time fabrication
- Konduktivitas termal dan listrik yang tinggi
- Ketahanan korosi yang sangat baik
- Good finishing and post-processing
- Cost-effectiveness for mid-volume production
Aluminum powder additive manufacturing provides significant advantages over conventional techniques for lightweight structural and functional parts.
Applications of 3D Printed Aluminum Components
Industry Applications of 3D Printed Aluminum
Industri | Komponen |
---|---|
Dirgantara | Airframe brackets, heat exchangers, turbine blades |
Otomotif | Chassis, powertrain parts, custom interiors |
Industri | Robotics, tooling, fixtures, mounts |
Konsumen | Electronics housings, drone bodies |
Arsitektur | Decorative panels, wall cladding |
Medis | Implan ortopedi, prostetik |
Additive manufacturing enables previously impossible aluminum geometries, consolidation, and customization across diverse sectors.
How to Choose Aluminum Printer Powder Suppliers
Choosing an Aluminum Powder Supplier
- Experience producing AM powders
- Capability to customize alloys and particle size
- Consistent quality and reproducibility
- Competitive and transparent pricing
- Keahlian teknis dan dukungan pelanggan
- Batch analysis and certification data
- Inventory and shorter lead times
- Capability to meet demand fluctuations
- Responsible and sustainable sourcing
A reliable aluminum powder partner delivers customized and qualified powders tailored to application requirements.
Aluminum Print Powder Manufacturers
Aluminum Powder Suppliers for AM
Perusahaan | Lokasi |
---|---|
Sandvik | Jerman |
AP&C | Kanada |
Praxair | AMERIKA SERIKAT |
Aditif Tukang Kayu | AMERIKA SERIKAT |
Serbuk & Pelapis Canggih | AMERIKA SERIKAT |
Teknologi LPW | INGGRIS |
These leading suppliers provide controlled particle sizes, spherical morphology, custom alloys, and extensive qualification data to ensure optimal prints.
Cost Analysis of Aluminum Print Powder
Aluminum Powder Cost
Kelas | Biaya per kg |
---|---|
Pure aluminum | $50-$100 |
AlSi10Mg | $55-$120 |
6061 alloy | $60-$150 |
5XXX series | $65-$140 |
Prices depend on alloy composition, impurity levels, particle characteristics, and purchase volume. Significant cost savings versus titanium alloys.
Comparison of Aluminum with Other Print Materials
Comparison of Aluminum Powder with Alternatives
Parameter | Aluminium | Titanium | Baja tahan karat |
---|---|---|---|
Kepadatan (g/cc) | 2.7 | 4.5 | 8.0 |
Kekuatan Tarik (MPa) | 230-520 | 900-1200 | 500-1000 |
Konduktivitas termal (W/mK) | 120-180 | 7-16 | 15-30 |
Electrical conductivity (MS/m) | 35-38 | 2.4 | 1.5 |
Biaya per kg | $50-$150 | $200-$500 | $20-$50 |
Kemampuan cetak | Adil | Sulit | Luar biasa |
Aluminum provides the best combination of strength, weight, conductivity and cost. Stainless steel is easier to print but heavier. Titanium is challenging.
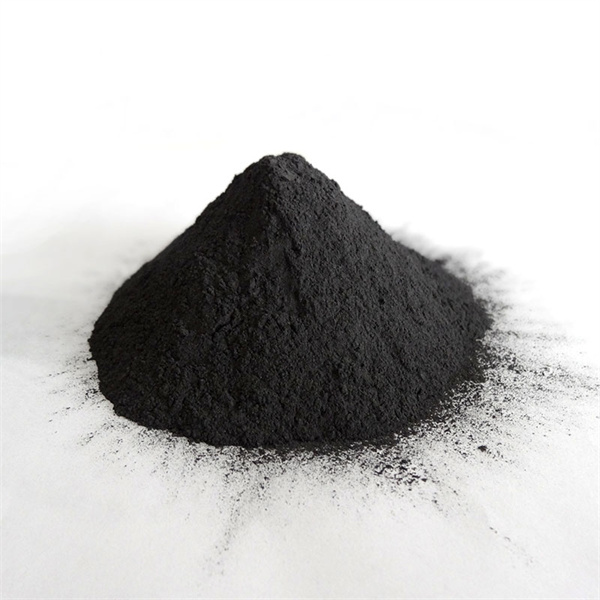
Pertanyaan yang Sering Diajukan
Q: What is the typical particle size for aluminum AM powder?
A: Particle sizes from 10-45 microns are common, with a tight distribution around 20-35 microns for optimal flow and high resolution.
Q: What aluminum grades are compatible with 3D printing?
A: AlSi10Mg, AlSi7Mg, and 6xxx series alloys like 6061 have been qualified. 5XXX grades are also gaining popularity for higher strength.
Q: Which AM process is best suited for aluminum?
A: DMLS, SLM, and binder jetting allow aluminum printing. Binder jetting provides faster build speeds but DMLS and SLM offer better mechanical properties.
Q: Does aluminum powder require special handling precautions?
A: Finely divided aluminum can be flammable or explosive in air. Inert gas glove boxes are recommended for storage and handling.
Q: Are heat treatments required for 3D printed aluminum?
A: Yes, solution treatment, aging, annealing, or stress relieving may be performed to achieve desired material properties and microstructures.
Q: What surface finishes can be achieved with aluminum AM parts?
A: As-printed finishes around 15 microns Ra can be further smoothed to under 1 micron Ra using media blasting, grinding, sanding, and polishing.
Q: Can aluminum printed parts match bulk alloy properties?
A: With optimized parameters and post-processing, additive parts can achieve mechanical properties on par with or better than traditionally processed aluminum alloys.
Q: What design principles apply for aluminum AM?
A: Print orientation, minimal supports, generous internal radii, and accounting for thermal stresses improves results. Wall thicknesses over 1 mm are preferred.