MIM(금속 분말)은 플라스틱 사출 성형의 설계 유연성과 가공된 금속 부품의 강도 및 특성을 결합한 효율적인 제조 공정입니다. MIM의 핵심 재료는 이 공정을 위해 특별히 맞춤화된 금속 분말입니다. 이 가이드는 구성, 생산, 특성, 응용 분야 등을 포함하여 MIM 금속 분말에 대한 포괄적인 개요를 제공합니다.
개요 MIM 금속 분말
MIM 금속 분말은 금속 사출 성형 공정의 공급 원료로 사용되는 미세 금속 분말을 말합니다. 미세 금속 분말과 바인더의 혼합물로 금형에 주입되어 복잡한 그물 모양의 녹색 부품을 형성합니다.
MIM 파우더의 주요 기능은 다음과 같습니다:
- 10~20미크론 크기의 초미세 구형 분말
- 바인더 부피 기준 55-65%의 파우더 로딩
- 금형 충진을 위한 뛰어난 유동성
- 일관된 입자 크기 분포
- MIM에 최적화된 합금 구성
- 강철, 스테인리스강, 티타늄 합금, 텅스텐 중합금 등 다양한 소재 옵션이 제공됩니다.
- 복잡하고 공차가 엄격한 금속 부품의 비용 효율적인 생산
2020년 전 세계 MIM 파우더 시장 규모는 1조 4,500억 달러가 넘었습니다. 이 산업은 다양한 분야의 수요에 힘입어 8% 이상의 연평균 성장률(CAGR)로 꾸준히 성장할 것으로 예상됩니다.
MIM 금속 분말의 종류
MIM 공급 원료에는 다양한 금속 분말 구성이 사용됩니다. 가장 일반적인 유형은 다음과 같습니다:
재질 | 주요 속성 | 애플리케이션 |
---|---|---|
스테인리스 스틸 | 내식성, 강도 | 의료, 자동차, 소비자 제품 |
공구강 | 높은 경도, 내마모성 | 절삭 공구, 금형, 기어 |
저합금강 | 자기 특성, 가공성 | 전자기계 부품 |
티타늄 합금 | 높은 중량 대비 강도 비율 | 항공우주, 군사, 바이오메디컬 |
텅스텐 중합금 | 밀도, 진동 감쇠 | 자동차, 스포츠 장비 |
초합금 | 고온 강도 | 터빈 및 로켓 부품 |
적절한 분말 금속 합금을 선택하면 특정 용도에 맞는 특성으로 부품을 제작할 수 있습니다.
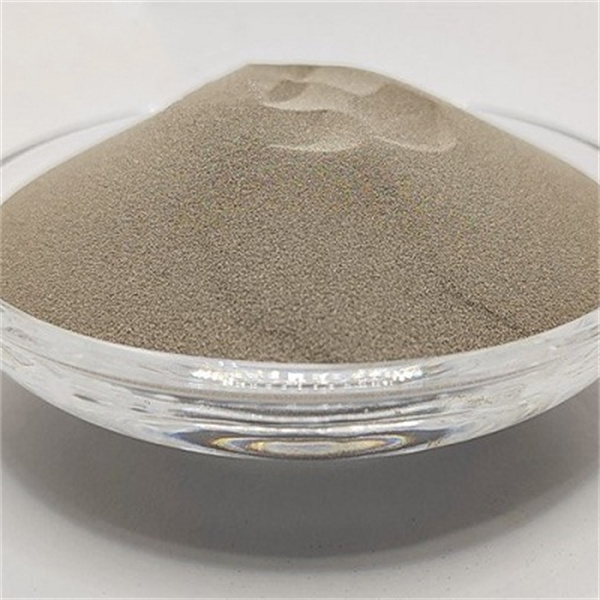
MIM 금속 분말 생산
MIM 공급 원료용 미세 금속 분말을 생산하기 위해 상업적으로 여러 가지 방법이 사용됩니다:
가스 분무 - 고속 불활성 가스 제트는 용융 금속의 얇은 흐름을 미세한 물방울로 분해하여 MIM에 이상적인 구형 분말로 응고시킵니다. 강철, 초합금 및 비철 합금에 일반적으로 사용됩니다.
물 분무 - 가스 분무와 유사하지만 냉각 속도가 낮아 일부 용도에 적합한 불규칙한 분말 모양을 생성합니다. 철, 구리와 같은 일반적인 합금에 사용되는 저비용 공정입니다.
플라즈마 원자화 - 티타늄, 니오븀, 탄탈륨과 같은 반응성 합금에서 더 미세한 구형 분말을 생성하는 데 사용되는 초고온 플라즈마 아크입니다.
기계적 마모 - 볼 밀링은 금속 분말 혼합물의 입자 크기를 MIM 범위로 줄이는 데 사용됩니다. 효율적인 건식 공정.
카보닐 공정 - 철과 니켈 카르보닐을 분해하여 1~5미크론 입자 크기의 고순도 구형 분말을 생산합니다.
파우더 제조 방법은 유동성, 탭 밀도 및 불순물과 같은 최종 파우더 특성을 제어합니다.
속성 MIM 금속 분말
MIM 공급 원료 분말의 주요 특성은 다음과 같습니다:
입자 크기 - 1~20미크론 사이, 일반적으로 10미크론 정도가 최적의 충전량입니다. 이 범위에서 수율이 높습니다.
파티클 모양 - 주로 구형 형태이므로 복잡한 금형에 원활하게 유입됩니다. 약간의 불규칙성이 허용됩니다.
입자 크기 분포 - 좁은 분포는 균일한 소결을 향상시킵니다. 일반적으로 10 +/- 5 미크론 범위 내의 입자는 80-90%입니다.
탭 밀도 - 최종 부품 밀도를 나타냅니다. 높은 기계적 특성을 위해서는 3g/cc 이상의 높은 탭 밀도가 필요합니다.
유량 - 초/50g 단위로 측정. 틈새 없이 매끄러운 금형 충진에 필수적입니다. 40초/50g 이하가 바람직합니다.
겉보기 밀도 - 공급 원료에서 일반적으로 최종 소결 밀도는 분말 로딩 분율을 나타내는 40-50%입니다.
피크노메트릭 밀도 - 고체 합금 입자의 실제 밀도입니다. 최종 부품 밀도와 일치하면 순도를 나타냅니다.
특정 표면적 - 값이 높을수록 MIM에 바람직한 입자 크기 분포가 더 미세함을 나타냅니다. 범위는 0.1 ~ 1m2/g입니다.
MIM 금속 분말용 합금 옵션
다음을 포함하여 다양한 합금을 MIM 분말 공급 원료로 사용할 수 있습니다:
합금 | 구성 | 속성 | 애플리케이션 |
---|---|---|---|
스테인리스 스틸 316L | Cr, Ni, Mo | 뛰어난 내식성 | 의료, 식품 접촉 |
스테인리스 스틸 17-4PH | Cr, Ni, Cu | 높은 강도, 경도 | 항공우주 부품 |
공구강 H13 | Cr, Mo, V | 고온 경도, 열 피로 저항 | 사출 성형 |
마레이징 스틸 | Ni, Co, Mo, Ti | 초고강도 | 항공우주, 툴링 |
합금강 | Cr, Mo, C | 열처리 가능, 자성 | 구조 부품 |
니켈 합금 718 | Ni, Fe, Nb, Mo | 고온 강도 | 항공우주 |
티타늄 Ti-6Al-4V | Ti, Al, V | 경량, 생체 적합성 | 의료용 임플란트 |
텅스텐 중합금 | W, Ni, Fe | 고밀도, 방사선 차폐 | 군사, 모터스포츠 |
다양한 합금을 사용할 수 있는 MIM은 필요한 재료 특성과 성능을 유연하게 달성할 수 있습니다.
MIM 금속 분말의 응용 분야
MIM 기술과 원료 분말을 사용하는 주요 응용 분야는 다음과 같습니다:
의료 및 치과 임플란트
MIM은 조인트, 고정 나사, 기구와 같은 작고 복잡한 스테인리스 스틸 및 티타늄 임플란트 부품의 대량 생산에 이상적입니다. 생체 적합성, 내식성, 강도 및 제조 정밀도를 제공합니다.
자동차 부품
MIM이 제작한 터보차저 로터, 인젝터 노즐, 밸브 잠금 캡과 같은 소형 정밀 부품은 최신 엔진과 파워트레인에서 성능 이점을 제공합니다.
소비자 가전
시계 기어, 장식용 피팅, 커넥터 핀 등과 같은 소형 부품은 스테인리스강, 구리 합금 및 공구강으로 MIM을 통해 제조됩니다.
항공우주 및 방위
경량의 고강도 Ti 및 Ni 합금 MIM 부품은 터빈과 기체의 무게를 줄여줍니다. 텅스텐 합금은 우주 및 방위용으로 방사선 차폐 기능을 제공합니다.
총기류
방아쇠, 해머, 안전장치, 이젝터와 같은 작고 복잡한 총기 부품은 스테인리스강과 공구강 합금으로 대량으로 MIM 제작할 수 있습니다.
시계 산업
MIM을 사용하면 복잡한 모양의 스테인리스 스틸 시계 케이스, 팔찌, 버클, 기어 및 스프링과 같은 소형 이동 부품을 경제적으로 생산할 수 있습니다.
MIM은 설계 유연성을 바탕으로 소비자 제품부터 핵심 산업 부품에 이르기까지 다양한 분야에서 응용 분야를 계속 발굴하고 있습니다.
선택 방법 MIM 금속 분말
MIM 원료 분말을 선택할 때 고려해야 할 주요 사항:
- 합금 구성 - 분말 합금을 내식성, 강도, 마모 특성 등과 같은 최종 애플리케이션 요구 사항에 맞출 수 있습니다.
- 입자 크기 및 모양 - 최적의 흐름과 패킹을 위해 10미크론 내외의 좁은 분포의 구형 형태를 선호합니다.
- 분말 순도 - 의료용과 같은 특수 애플리케이션에는 오염을 방지하기 위해 99% 이상의 고순도가 필요합니다.
- 탭 밀도 - 3g/cc 이상의 높은 밀도는 소결 후 금형 충진 및 최종 부품 밀도를 향상시킵니다.
- 파우더 로딩 - 바인더 함량은 30~50 vol%가 일반적입니다. 점도와 몰드 그린 강도에 영향을 줍니다.
- 분말 생산자 - 샌드빅, 바스프, 키메라와 같은 유명 파우더 제조업체는 검증된 프로세스를 갖추고 있습니다.
- 로트 간 일관성 - 일관된 공급 원료 특성으로 장시간 생산에도 안정적인 성형 파라미터를 유지할 수 있습니다.
- 기술 지원 - 개발 시험 중 자세한 애플리케이션 데이터와 파우더 공급업체의 지원을 받을 수 있습니다.
샌드빅 오스프리, 바스프 울트라폼, 키메라 인터내셔널, 엡손 아트믹스 등 선도적인 글로벌 공급업체는 부품 및 공정 개발 과정에서 최종 사용자와 협력하여 최적의 결과를 도출합니다.
분무형 분말과 분쇄형 분말의 비교
매개변수 | 분무 분말 | 기계적으로 분쇄된 분말 |
---|---|---|
파티클 모양 | 구형 | 불규칙하고 각진 |
크기 범위 | 1 - 20 미크론 | 10 - 100미크론 이상 |
크기 분포 | 매우 좁은 | 광범위 |
탭 밀도 | 더 높은 ~3-4g/cc | 낮은 ~2-3g/cc |
유량 | 우수 | 보통 |
순도 | 높음 | Lower |
비용 | 더 높음 | Lower |
사용 가능한 합금 | 대부분의 표준 및 특수 합금 | 제한된 합금 |
애플리케이션 | 대부분의 MIM 구성 요소 | 더 크고 덜 중요한 MIM 부품 |
원자화된 파우더를 사용하면 더 복잡하고 고성능의 MIM 구성 요소를 만들 수 있습니다. 분쇄 분말은 일부 애플리케이션에 비용 절감 옵션을 제공합니다.
MIM 파우더 생산 공장 설치
MIM 파우더 생산 공장 설치의 주요 단계:
- 사이트 선택 - 적절한 공간, 유틸리티 공급, 폐기물 처리, 진입로 및 적재함.
- 건물 및 레이아웃 - 자재 및 인력 흐름, 안전, 생산 구역, 향후 확장을 위한 공장 레이아웃을 설계합니다.
- 유틸리티 연결 - 대용량 전기 공급, 정제수, 압축 공기 라인, 액체 질소.
- 기계 기초 - 분무기, 밀, 용광로를 위한 강력한 철근 콘크리트 기초. 진동 감쇠.
- 장비 설치 - 공급업체 지침에 따라 글러브 박스, 분무기, 체, 컨베이어, 호퍼, 제어 장치를 설정하세요.
- 보조 시스템 - 배관, 환기, 공기 여과, 화재 안전, 자재 취급, 폐수 처리.
- 제어 시스템 - 센서, 액추에이터, HMI를 설치합니다. 프로세스 제어 시스템을 통합하고 프로그래밍합니다.
- 커미셔닝 - 본격적인 생산 전에 파우더 품질, 안전성, 환경 규정 준수를 검증하기 위한 테스트 생산 실행.
MIM 파우더 플랜트 설치에는 유틸리티, 제어, 안전 및 규제 요구 사항에 대한 광범위한 계획과 주의가 필요합니다.
MIM 파우더 장비의 운영 및 유지보수
MIM 분말 제조 장비의 안정적인 작동이 필요합니다:
- 예방적 유지 관리 - OEM 권장 사항에 따라 분무기, 용광로, 밀, 컨베이어의 정기 유지보수를 예약합니다.
- 장비 모니터링 - 유량, 압력, 온도, 전력 소비와 같은 프로세스 파라미터를 지속적으로 모니터링합니다.
- 검사 - 누수, 비정상적인 소음 또는 진동, 안전 문제가 있는지 매일 육안으로 검사합니다.
- 서비스 및 수리 - 질소 발생기, 냉각기, 전기 시스템에 대한 연간 서비스 계약을 예약하세요.
- 예비 부품 - 발열체, 모터, 베어링과 같은 일반적인 예비 부품의 재고를 확보하여 가동 중단 시간을 최소화하세요.
- 장비 로그 - 생산 속도, 수리, 고장에 대한 로그를 유지하여 자산 활용도를 최적화하세요.
- 하우스키핑 - 매일 청소하여 장비를 깨끗하고 정돈된 상태로 유지하고 분말 취급 구역에서 발화 위험을 방지합니다.
- 직원 교육 - 운영 효율성과 문제 해결 능력을 향상시키기 위한 실습 장비 교육을 실시하세요.
우수한 유지보수 관행을 통해 MIM 파우더 제조 장비는 수년간 안전하고 신뢰할 수 있는 생산을 제공할 수 있습니다.
MIM 파우더 공급업체를 선택하는 방법
MIM 파우더 공급업체를 선택할 때 고려해야 할 주요 요소:
- 기술 전문성 분말의 경우 - MIM을 위한 분말 특성 및 바인더 배합 최적화를 경험하세요.
- 합금의 범위 - 스테인리스강부터 티타늄, 공구강 등 다양한 합금을 사용할 수 있습니다.
- 품질 시스템 - ISO 9001 인증. 파우더 특성에 대한 내부 품질 관리.
- 일관성 - 분말 특성은 배치마다 일관되게 유지되므로 안정적인 성형 공정이 가능합니다.
- R&D 역량 - 까다로운 애플리케이션을 위한 새로운 맞춤형 합금과 바인더를 개발하기 위한 지속적인 연구.
- 고객 서비스 - 신속한 기술 및 영업 지원 평가판 및 램프업 중 현장 지원.
- 물류 기능 - 여러 지역에 걸쳐 정시에 효율적으로 파우더를 배송할 수 있는 시스템.
선도적인 글로벌 공급업체로는 샌드빅 오스프리, 바스프, 키메라 인터내셔널, 엡손 아트믹스 등이 있으며, 이들은 MIM 파우더 기술에 집중하고 있습니다.
MIM 파우더의 장단점
장점
- 저렴한 비용으로 대량 생산되는 복잡한 그물 모양의 부품
- 가공하기 어려운 금속을 포함한 다양한 합금 사용 가능
- 단조 소재에 가까운 우수한 기계적 특성
- 높은 정확도와 반복성
- 기계 가공에 비해 스크랩 손실 최소화
- 소결 부품에 필요한 마감 처리 제한
- 기계 가공보다 폐기물이 적은 환경 친화적인 공정
단점
- 더 적은 생산량으로 더 높은 부품 비용
- 일반적으로 500g 미만의 소형 부품으로 크기가 제한됩니다.
- MIM 파우더 블렌드로 제공되는 합금으로 제한됩니다.
- 소결 부품은 단조 금속보다 연성이 낮습니다.
- 전문 장비 및 전문 지식 필요
- 추가 디바인딩 및 소결 단계
다른 응용 분야를 위한 MIM 파우더와 금속 파우더 비교
매개변수 | MIM 파우더 | 적층 제조 파우더 | 프레스 및 소결 분말 |
---|---|---|---|
합금 | 광범위한 스테인리스, 공구강, Ti 합금 | 17-4PH, Ti-6Al-4V, CoCr과 같은 제한된 합금 | 저합금 및 스테인리스강 |
파티클 모양 | 주로 구형 | 고도로 구형 | 불규칙 허용 |
크기 범위 | 1-20 미크론 | 15-45 미크론 | 최대 150미크론 |
크기 분포 | 매우 좁은 | 좁은 | 더 넓은 허용 범위 |
순도 | 중간에서 높음 | 높음 | Medium |
비용 | Medium | 높음 | 낮음 |
일반적인 제작 방법 | 가스 또는 물 분무 | 가스 또는 플라즈마 분무 | 물 분무, 기계식 밀링 |
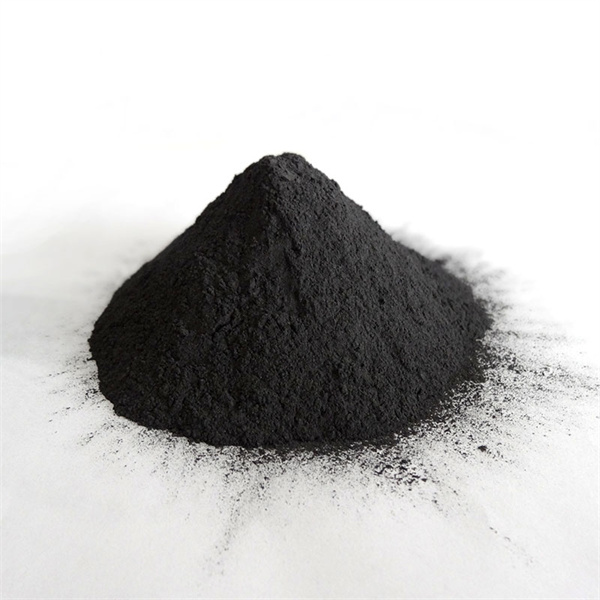
자주 묻는 질문
Q: MIM 파우더의 일반적인 크기 분포는 어떻게 되나요?
A: 최적의 패킹 밀도와 흐름을 위해 약 80-90%의 MIM 파우더 입자는 10 +/- 5마이크론 이내로 떨어집니다.
Q: 바인더의 파우더 로딩에 영향을 미치는 요인은 무엇인가요?
A: 파우더 로딩 %를 제어하는 주요 요소는 입자 크기 분포, 모양, 탭 밀도, 파우더-바인더 상호작용입니다.
Q: MIM 부품의 고온 강도는 단조 합금에 비해 어떤가요?
A: 최적의 소결을 통해 스테인리스강 316L 및 17-4PH와 같은 합금의 MIM 부품은 90% 이상의 가공 강도를 달성합니다.
Q: MIM에서 불완전한 금형 충진 결함의 원인은 무엇인가요?
A: 부적절한 파우더 로딩, 넓은 입자 분포, 낮은 파우더 유동성 및 낮은 주입 속도는 충전 결함을 유발할 수 있습니다.
Q: MIM은 성형 압력 측면에서 플라스틱 사출 성형과 어떻게 비교되나요?
A: MIM 사출 압력 범위는 70-140MPa로, 일반적인 플라스틱 성형 압력인 15-60MPa보다 높습니다.
질문: MIM 파우더를 취급할 때 어떤 안전 예방 조치가 필요하나요?
A: MIM 파우더는 가연성일 수 있습니다. 불활성 가스 글러브 박스를 사용하고, 스파크 발생원, 지상 장비를 피하고, 먼지 추출기를 사용하세요.
결론
MIM은 고성능의 복잡한 금속 부품을 저비용으로 대량으로 제조할 수 있는 그물망에 가까운 형상 기술로 각광받고 있습니다. MIM 분말은 첨단 분말 야금 기술로 이 공정을 위해 특별히 제조된 핵심 원자재입니다. 합금과 파우더가 확대되고 개선됨에 따라 비용과 리드 타임이 개선된 기계 가공 및 주조 부품을 대체하기 위해 산업 전반에서 MIM 채택이 계속 증가할 것입니다.