초합금 금속 분말 은 기존 금속과는 비교할 수 없는 고강도, 내열 합금 부품의 적층 제조를 가능하게 합니다. 이 가이드는 분말 야금 조달 결정을 내리기 위한 초합금 구성, 분말 사양, 특성 데이터, 가격 인사이트 및 비교를 다룹니다.
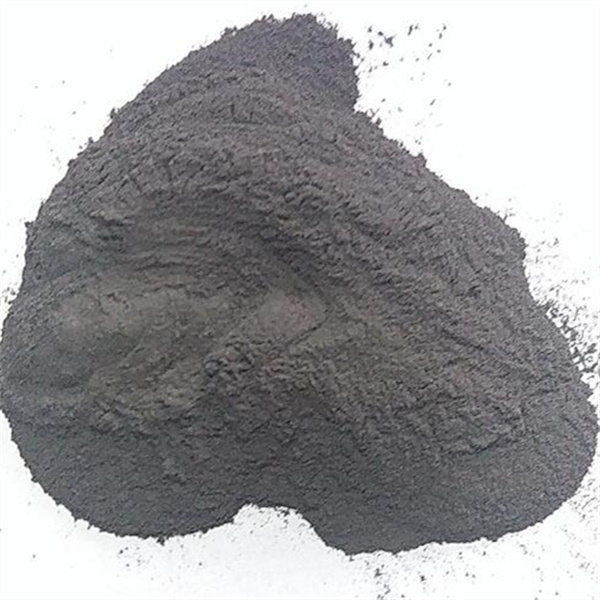
초합금 금속 분말 소개
초합금 분말의 주요 기능:
- 최대 85%의 녹는점까지 견디는 극한의 온도 견딤
- 열악한 환경에서도 강도, 내식성 및 안정성 유지
- 적층 가공을 통한 복잡한 부품 형상 혁신 촉진
공통 분류 그룹:
- 니켈 기반 - 인코넬, 와스팔로이, 르네 합금
- 코발트 기반 - 헤인즈, HS 합금
- 철 기반 - A286, 901, 304 버전
이 가이드는 초합금 분말을 선택할 때 고려해야 할 사항을 제공합니다:
- 합금 조성 및 분말 생산 방법
- 기계적 특성, 테스트 방법 및 데이터 시트
- 입자 크기 분포 사양
- 파우더 형태 특성 및 일관성
- 주문량에 따른 가격 모델
- 산화 및 부식 방지
- 장단점: 파우더와 솔리드 바
- 품질 관리 및 애플리케이션에 대한 FAQ
초합금 분말을 구체적으로 살펴보겠습니다...
초합금 금속 분말 작곡
표 1 은 일반적인 니켈 및 코발트 기반 초합금의 공칭 조성을 보여주며, 분말 제조업체마다 약간의 차이가 있습니다.
합금 | 주요 합금 원소 |
---|---|
인코넬 718 | Ni, Fe, Nb, Mo, Al |
인코넬 625 | Ni, Cr, Mo, Nb |
Rene 41 | Ni, Co, Cr, Mo, Ti, Al |
말벌 | Ni, Co, Cr, Mo, Ti, Al |
헤인즈 282 | Co, Cr, W, Mo, Ti, Al |
붕소, 탄소, 지르코늄 및 실리콘을 소량 첨가하면 입자 구조를 조정하고 경계를 강화하며 침전물 형성을 통해 고온 거동을 개선할 수 있습니다.
기계적 특성 및 테스트 방법
표 2 은 일반적인 초합금 분말이 충족하는 일반적인 최소 기계적 특성을 보여주며, 실제 값은 제작 형상, 후처리 및 열처리에 따라 달라질 수 있습니다.
합금 | 수율 강도 | 인장 강도 | 테스트 방법 |
---|---|---|---|
인코넬 718 | 1035 MPa | 1275 MPa | ASTM E8 |
Rene 41 | 760 MPa | 1035 MPa | ASTM E8 |
헤인즈 282 | 830 MPa | 1035 MPa | ASTM E8 |
테스트 보고서를 주의 깊게 검토하여 조달한 파우더 로트가 인증 요구 사항과 애플리케이션 요구 사항을 충족하는지 확인합니다.
초합금 금속 분말 입자 크기 사양
표 3 은 일반적으로 초합금 분말을 분류하는 데 사용되는 입자 크기 분포 범주를 보여줍니다:
크기 범위 | 일반 메시 |
---|---|
서브미크론 | -100 +325 메시 |
괜찮아요 | -140 +325 메시 |
엑스트라 파인 | -200 +325 메시 |
기타 주요 파티클 특성:
- 구형 형태
- 인공위성이 없는 매끄러운 표면
- 제어된 크기 분포
- 홀 깔때기의 유량 >30대
인쇄의 경우 25-45미크론 평균 크기가 해상도와 유동성의 균형을 잘 맞출 수 있습니다. 특정 기계의 성능과 필요한 최소 피처 크기에 따라 조정합니다.
초합금 금속 분말 가격 책정
표 4 는 일반적인 시장 조건에서 대략적인 초합금 분말 가격 추정치를 제공합니다:
주문 수량 | 가격 견적 |
---|---|
10kg | $450+/kg |
100kg | $275+/kg |
500kg | $225+/kg |
1000+ kg | 서브키 할인 |
- 특수 합금은 프리미엄 기본 가격을 적용합니다.
- 500-1000kg 이상의 대량 주문 시 대량 구매 레버리지를 통해 정가 대비 50% 이상의 할인이 가능합니다.
- 원자재 투입 가격 변동에 연동된 실제 시장 가격
산화 및 부식 방지
초합금은 극한의 환경에 노출되어도 뛰어난 안정성을 유지합니다:
표 5
합금 | 일반적인 서비스 온도. | 내식성 |
---|---|---|
인코넬 718 | 700°C | 우수 |
Rene 41 | 760°C | 우수 |
헤인즈 282 | 1095°C | 우수 |
니켈, 크롬 및 알루미늄으로 세심하게 설계된 조성물은 매우 높은 비율의 융점까지 공격으로부터 표면을 보호하는 끈질긴 부동태화 산화물 장벽을 형성합니다.
몰리브덴과 같은 원소는 구멍과 틈새 부식에 대한 내성을 더욱 강화합니다.
장단점: 파우더와 솔리드 바
표 6
장점 | 단점 | |
---|---|---|
초합금 금속 분말 | 복잡한 모양 | 더 높은 비용 |
우수한 속성 | 후처리 | |
무게 감소 | 파라미터 최적화 | |
초합금 솔리드 바 | 비용 절감 | 모양 제한 |
가용성 | 훨씬 더 무겁습니다. | |
가공성 | 재료 낭비 |
일반적으로 초합금 분말은 고급 특성이 중요한 소량 복합 부품의 경우 프리미엄을 정당화합니다. 표준 밀 형태는 대량 생산 사용 사례에서 단순한 형상을 위한 경제성을 제공합니다.
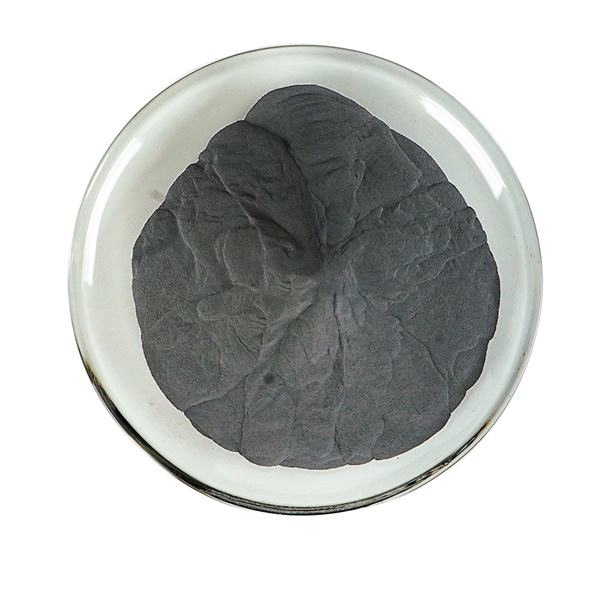
자주 묻는 질문
표 7 - 자주 묻는 질문:
자주 묻는 질문 | 답변 |
---|---|
테스트 보고서를 검토해야 하나요? | 예, 모든 인증서를 면밀히 검토하여 분말 품질을 보장합니다. |
어떤 크기의 파우더 입자로 시작해야 하나요? | 25-45U는 강력한 시작점을 제공합니다. |
일관성에 영향을 미치는 요인은 무엇인가요? | 원료 분말 생산 방식이 변동성에 미치는 영향 |
처음에 파우더를 얼마나 구매해야 하나요? | 소규모로 시작하여 인쇄 프로세스 제어 검증 |
표 8 - 애플리케이션별 조언:
자주 묻는 질문 | 답변 |
---|---|
핫 섹션 터빈 블레이드에는 어떤 포스트 프로세싱을 사용해야 하나요? | 모공 제거 및 피로 성능 향상을 위한 핫 등방성 프레싱 |
고온 항복 강도를 극대화하는 합금은 무엇인가요? | Rene 41 또는 Haynes 282 합금을 고려하십시오. |
부품 이방성 효과를 최소화하려면 어떻게 해야 하나요? | 고온 열처리를 활용하여 스트레스 완화하기 |
극저온 부품에 파우더와 캐스트 중 어떤 것이 더 낫나요? | 파우더는 주조와 달리 복잡한 컨포멀 채널을 가능하게 합니다. |