금속 분무는 다양한 용도의 미세 금속 분말을 생산하는 데 사용되는 공정입니다. 금속을 녹인 다음 가스 또는 원심력을 사용하여 미세한 방울로 분해합니다. 이 방울은 빠르게 응고되어 분말 입자가 됩니다. 금속 분무 시스템 는 이 프로세스를 산업적 규모로 효율적으로 수행하는 데 사용되는 장비입니다.
금속 분무 시스템 개요
금속 분무 시스템은 금속 용융 장치, 분무 메커니즘, 분말 수집 시스템으로 구성됩니다. 주요 구성 요소는 다음과 같습니다:
금속 용융 장치
- 녹는 도가니
- 유도 코일 또는 전극
- 온도 센서
- 불활성 가스 밀봉
분무 메커니즘
- 가스 분무용 노즐
- 원심 분무용 회전 디스크 또는 컵
파우더 수집 시스템
- 사이클론 분리기
- 백 하우스 필터
- 스크러버 및 콘덴서
금속 전하를 먼저 유도 가열 또는 전기 저항 가열을 사용하여 도가니에서 녹입니다. 그런 다음 용융된 금속을 분무 섹션으로 안내합니다.
가스 분무에서는 고압 가스 제트가 금속 스트림에 부딪혀 미세한 물방울로 분해됩니다. 원심 분무에서는 용융 금속을 회전하는 디스크/컵에 부어 원심력에 의해 방사형으로 방울로 분사합니다.
물방울은 높은 표면적 대 부피 비율로 인해 냉각 챔버를 통과하면서 빠르게 응고됩니다. 불활성 가스가 산화를 방지합니다. 응고된 분말 입자는 분리기, 필터 및 콘덴서에 수집됩니다.
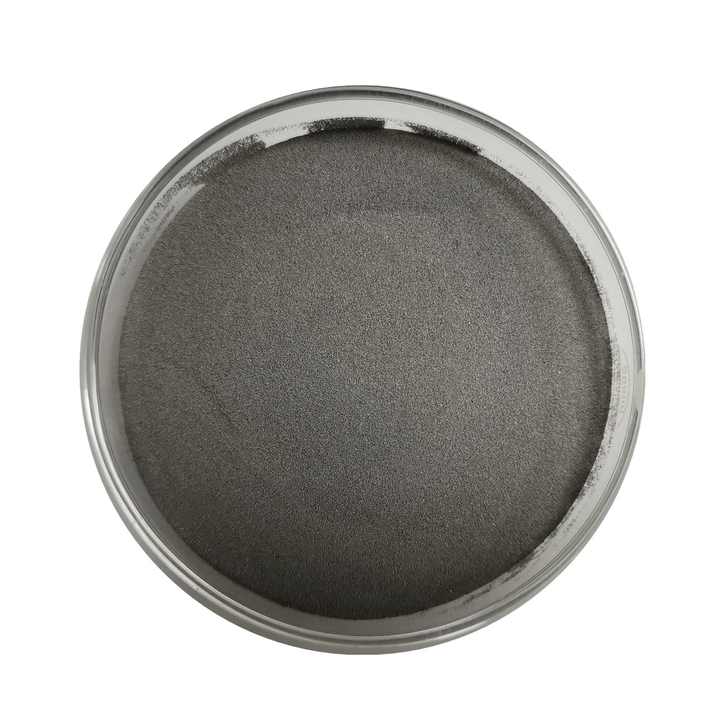
금속 분무 시스템의 유형
분무 메커니즘에는 크게 두 가지 유형이 사용됩니다:
가스 분무
- 고압 불활성 가스 분사 사용
- 10미크론까지 미세한 분말을 만들 수 있습니다.
- 분무 가스로 사용되는 질소, 아르곤
원심 분무
- 회전 컵 또는 디스크 사용
- 20미크론 이상의 거친 분말을 만듭니다.
- 가스 취급이 필요 없는 심플한 디자인
진공 분무
- 불활성 가스 대신 진공 상태에서 수행됩니다.
- 분말에 의한 가스 흡수 감소
초음파 분무
- 초음파 진동을 사용하여 물방울을 만듭니다.
- 연구 규모의 프로덕션용
정전기 분무
- 전기장을 사용하여 금속 스트림을 분해합니다.
- 실험 기술
금속 분무 시스템 설계
일반적인 가스 분무 시스템의 주요 구성 요소는 다음과 같습니다:
표 1: 가스 분무 시스템 설계
구성 요소 | 세부 정보 |
---|---|
용융 단위 | 유도 용해 도가니, 용량 50-2000kg |
노즐 어셈블리 | 여러 개의 밀착 결합 노즐, 직경 2~5mm |
용융 과열 | 과열 용융물에 질소/아르곤 주입 |
분무 챔버 | 수냉식, 높이 3~5m |
가스 공급 | 질소/아르곤, 50-100bar 압력 |
사이클론 분리기 | 분말 수집을 위한 여러 개의 사이클론을 직렬로 연결 |
최종 필터 | 백하우스, 카트리지 필터 |
원하는 미세 분말 입자 크기 분포를 얻으려면 노즐 디자인과 개수가 중요합니다. 분무 챔버의 높이에 따라 수거 전에 액적이 굳을 수 있는 시간이 주어집니다.
질소나 아르곤과 같은 고급 산업용 가스는 압축 가스 실린더 또는 현장 발전기에서 공급됩니다. 가스의 압력과 유량에 따라 액적 크기가 결정됩니다.
금속 분무 시스템 사양
산업용 가스 분무 시스템의 일반적인 사양은 다음과 같습니다:
표 2: 금속 분무 시스템 사양
매개변수 | 사양 |
---|---|
생산 능력 | 10kg/h ~ 5000kg/h |
입자 크기 | 10 - 150 미크론 |
금속 유형 | 니켈, 철, 코발트, 구리 합금 |
녹는 온도 | 최대 1600°C |
가스 압력 | 10 - 100 bar |
냉각 속도 | 104 - 106 K/s |
분말 순도 | 99.5% |
노즐 디자인 | 환형 슬릿, 개별 제트 |
분무 가스 | 질소, 아르곤 |
용량은 도가니 크기에 따라 다르며 실험실/파일럿 규모 10kg/h부터 대규모 5000kg/h 시스템까지 다양합니다. 주로 니켈, 철, 코발트 합금이 원자화되지만 알루미늄, 구리 합금과 같은 다른 금속도 처리됩니다.
높은 가스 압력과 빠른 냉각 속도로 10-150미크론 크기의 미세한 분말 입자를 보장합니다. 순도 99.5%의 분말을 얻을 수 있습니다.
금속 분무기 시스템 애플리케이션
분무로 생산된 금속 분말의 주요 응용 분야는 다음과 같습니다:
표 3: 금속 분말 응용 분야
산업 | 애플리케이션 |
---|---|
항공우주 | 터빈 블레이드, 디스크 |
자동차 | 소결 부품, 필터 |
전자 제품 | 칩 저항기, 도체 |
적층 제조 | 3D 프린팅 파우더 |
화학 | 촉매, 안료 |
바이오메디컬 | 임플란트, 보철 |
항공우주 산업에서는 니켈과 티타늄 합금 분말을 사용하여 분말 야금을 통해 복잡한 모양의 터빈 블레이드와 디스크를 생산합니다. 자동차 산업에서는 기어와 같은 소결 부품에 원자화된 철 및 강철 분말을 사용합니다.
미세한 구리 및 은 분말은 마이크로전자 애플리케이션에서 도체 및 저항기 역할을 합니다. 금속 분말은 3D 프린팅과 같은 적층 제조 방법의 공급 원료입니다.
특수 합금 분말은 화학 촉매 및 안료로 사용됩니다. 다공성 스테인리스강 분말은 생의학 분야의 정형외과용 뼈 임플란트에 사용됩니다.
금속 분무 시스템의 장점
분말 생산에 금속 분무기를 사용하면 얻을 수 있는 몇 가지 이점이 있습니다:
표 4: 금속 분무의 장점
혜택 | 세부 정보 |
---|---|
더 미세한 분말 | 마이크로미터에서 나노미터 크기 |
좁은 크기 분포 | 입자 크기에 대한 정밀한 제어 |
고순도 | 밀링으로 인한 오염 방지 |
비용 절감 | 기계식 연삭보다 저렴 |
구도 제어 | 용융물에서 합금 가능 |
구형 입자 | 우수한 유동성 |
다용도 | 다양한 합금 원자화 |
가스 및 원심 분무는 기계식 분쇄에 비해 10마이크론까지 더 미세한 금속 분말을 생산할 수 있습니다. 입자 크기 분포가 더 좁아져 더 나은 제어가 가능합니다.
분쇄 매체를 사용하지 않기 때문에 분말 순도가 더 높습니다. 기계식 제분보다 자본 및 운영 비용이 낮습니다.
도가니에 합금 원소를 추가할 수 있어 분말 구성에 유연성을 부여할 수 있습니다. 구형 분말 입자는 금형 충진에 중요한 우수한 유동성을 제공합니다.
니티놀부터 인코넬까지 거의 모든 합금을 공정 파라미터를 적절히 제어하여 분무할 수 있습니다.
금속 분무의 한계
금속 분무 시스템의 몇 가지 단점은 다음과 같습니다:
표 5: 금속 분무의 제한 사항
단점 | 세부 정보 |
---|---|
높은 융점 | 저융점 금속으로 제한 |
반응성 금속 | 티타늄, 알루미늄과 같은 반응성 금속을 분무하기 어려운 경우 |
가스 픽업 | 흡수된 가스는 분말 품질에 영향을 미칩니다. |
위성 입자 | 더 큰 불규칙한 입자가 형성됨 |
높은 자본 비용 | 대규모 시스템에 필요한 대규모 투자 |
텅스텐, 몰리브덴과 같이 녹는점이 1800°C 이상으로 매우 높은 금속은 도가니의 한계로 인해 분무하기가 어렵습니다. 티타늄, 알루미늄과 같은 반응성 금속은 진공 또는 불활성 대기가 필요합니다.
분무 과정에서 흡수된 가스는 분말 특성에 영향을 미칩니다. 분무 과정에서 구형 입자와 함께 일부 불규칙한 모양의 위성 입자도 형성됩니다.
대규모 금속 분무 시스템에는 1조 4천 2백만 달러 이상의 대규모 자본 투자가 필요합니다. 운영 비용도 상대적으로 높습니다.
금속 분무 시스템 공급업체
금속 분무 장비의 선도적인 글로벌 공급업체는 다음과 같습니다:
표 6: 금속 분무 시스템 공급업체
회사 | 위치 | 규모 |
---|---|---|
피닉스 사이언티픽 | 록우드, 미국 | 연구실에서 산업으로 |
금속 분말 제조 | 맨체스터, 영국 | 연구실에서 산업으로 |
화학물질에 문의하기 | 독일 힐덴, 독일 | 연구실에서 산업으로 |
ZenniZ | 모스크바, 러시아 | 산업 |
ALD 진공 | 독일 하나우, 독일 | 산업 |
이 회사들은 실험실/파일럿 규모 5kg/h부터 대규모 2000kg/h 용량에 이르는 가스, 원심, 진공 분무 시스템을 제공합니다. 용융, 분무 및 분말 처리 장치를 갖춘 턴키 시스템이 제공됩니다.
분무 시스템의 가격은 용량과 기능에 따라 실험실 단위의 경우 $100,000에서 산업 플랜트의 경우 $ 200만 원 이상입니다. 위치, 세금, 운송 등도 가격에 영향을 미칩니다.
금속 분무 시스템 설치
금속 분무 시스템을 설치하는 주요 단계는 다음과 같습니다:
표 7: 금속 분무기 설치
스테이지 | 작업 |
---|---|
사이트 준비 | 콘크리트 바닥 수평 맞추기, 유틸리티 설치 |
어셈블리 | 도가니, 노즐 섹션과 같은 하위 유닛을 조립합니다. |
연결 | 가스 라인, 냉각수, 덕트 연결 |
커미셔닝 | 비어 있는 상태에서 테스트 실행, 누수 점검, 저용량으로 시험 실행 |
안전 점검 | 비상 정지, 화재 진압, 경보 설치 |
직원 교육 | 시스템 운영 및 유지 관리에 대한 직원 교육 |
장비가 무겁기 때문에 현장에 평평하고 진동이 없는 콘크리트 바닥이 있어야 합니다. 냉각수, 불활성 가스, 배기 덕트와 같은 유틸리티를 연결해야 합니다.
그런 다음 시스템을 조립, 정렬하고 누출 테스트를 거친 후 실제 고온 시운전 전에 처음에 비어 있는 상태로 가동합니다. 비상 종료, 화재 또는 용융물 누출에 대비한 안전 시스템이 작동해야 합니다.
원활한 운영을 위해서는 공급업체의 운영 인력에 대한 철저한 교육이 필수적입니다.
금속 분무기 작동 및 유지 관리
금속 분무 시스템 운영의 주요 측면은 다음과 같습니다:
표 8: 금속 분무기 작동
활동 | 세부 정보 |
---|---|
원자재 취급 | 적절한 장갑, 금속 충전용 용기 사용 |
도가니 청소 | 분쇄, 산 세척을 통해 잔류물, 슬래그 제거 |
도가니 안감 | 안감 검사, 필요에 따라 재코팅/교체하기 |
프로세스 매개변수 | 적절한 온도, 압력, 유량 유지 |
노즐 상태 | 노즐의 마모, 막힘 여부 검사 |
분말 처리 | 적절한 용기, 전송 절차 확인 |
장비 검사 | 씰, 커넥터, 안전 시스템 점검 |
유지 관리 | 예방적 유지보수, 수리 예약 |
생금속 조각을 취급할 때는 오염을 방지하기 위해 적절한 보호 장비를 사용해야 합니다. 용해 도가니는 정기적인 청소와 라이닝 내화 유지보수가 필요합니다.
온도, 압력, 가스 유량과 같은 공정 파라미터를 주의 깊게 모니터링하는 것이 중요합니다. 특히 가스 분무용 노즐은 주기적으로 점검하고 교체해야 합니다.
생산된 미세 분말은 노출 위험을 방지하기 위해 세심한 취급이 필요합니다. 정기적인 점검을 통해 누출과 손상을 발견하고 모든 안전 시스템이 작동하는지 확인해야 합니다. 고장을 방지하기 위해 예방적 유지보수를 예약해야 합니다.
금속 분말 분무기 공급업체 선택
금속 분무 시스템 공급업체 선정의 핵심 요소:
표 9: 금속 분무기 공급업체 선택하기
기준 | 고려 사항 |
---|---|
기술 전문성 | 경험, 전문 인력 |
장비 범위 | 실험실, 파일럿, 산업 규모 시스템 |
실적 | 관련 사례 연구, 고객 목록 |
사용자 지정 | 특정 요구 사항에 대한 유연성 |
판매 후 서비스 | 설치 지원, 유지보수 계약 |
가격 | 예산에 맞는 견적 |
신뢰성 | 품질과 검증된 성능 구축 |
안전 | 모든 산업 안전 규범 충족 |
인증 | ISO 또는 기타 품질 인증 |
용사 또는 분말 야금 산업에 대한 전문성을 갖춘 회사를 찾아보세요. 실험실 프로토타입부터 대규모 생산에 이르기까지 모든 종류의 분무기를 제공할 수 있어야 합니다.
특정 애플리케이션과 관련된 고객 레퍼런스 및 사례 연구를 요청하세요. 용량 요구 사항과 파우더 특성에 맞는 맞춤형 솔루션을 찾아보세요.
설치 감독, 운영자 교육, 유지보수 계약 등과 같은 애프터서비스 지원을 평가합니다. 가격도 고려하되 성능, 안전, 신뢰성을 우선적으로 고려하세요.
결론
금속 분무는 항공우주, 자동차, 적층 제조 및 기타 산업의 첨단 응용 분야를 위해 다양한 합금으로부터 깨끗하고 구형의 미세 금속 분말을 생산하는 효율적인 공정입니다.
가스 및 원심 분무 시스템은 금속 용융, 액적 형성 및 분말 수집 하위 장치로 구성됩니다. 원하는 입자 크기와 분말 특성을 얻으려면 신중한 설계가 필요합니다.
주요 공급업체는 적절한 판매 후 지원과 함께 소규모에서 대규모 산업 용량의 표준 및 맞춤형 분무 시스템을 제공합니다. 올바른 공급업체를 선택하고 모범 운영 사례를 따르면 원활한 작동과 최대 분말 생산을 보장할 수 있습니다.
자주 묻는 질문
Q: 금속 분무 시스템의 일반적인 용량 범위는 어떻게 되나요?
A: 금속 분무 시스템은 실험실/파일럿 규모를 위한 10kg/h부터 대량 산업 생산을 위한 5000kg/h 이상의 용량으로 제공됩니다. 최대 10,000kg/h까지 더 큰 용량도 가능합니다.
Q: 어떤 산업에서 일반적으로 금속 분무기를 사용하나요?
A: 금속 원자화를 사용하는 주요 산업으로는 항공우주, 자동차, 적층 제조, 분말 야금, 전자 및 화학 산업이 있습니다. 미세한 구형 분말은 중요한 부품을 제조하는 데 사용됩니다.
Q: 파우더 입자 크기를 얼마나 미세하게 만들 수 있나요?
A: 가스 분무에서는 노즐, 가스 압력 및 유속을 최적으로 설계하여 10마이크론 이하의 분말 크기를 얻을 수 있습니다. 원심 분무는 일반적으로 20미크론 이상의 거친 분말을 만듭니다.
Q: 어떤 금속을 원자화할 수 있나요?
A: 녹는점이 1800°C 미만인 대부분의 엔지니어링 금속은 분무할 수 있습니다. 일반적인 예로는 니켈, 철, 코발트 및 티타늄 합금이 있습니다. 알루미늄과 마그네슘과 같은 일부 반응성 금속도 통제된 조건에서 분무할 수 있습니다.
Q: 가스 분무에는 어떤 가스가 사용되나요?
A: 질소와 아르곤은 불활성과 가용성 때문에 가장 널리 사용됩니다. 경우에 따라 산소나 공기도 사용되지만 분말을 오염시킬 수 있습니다.
Q: 분무 시스템의 운영 비용은 어떻게 되나요?
A: 고압 가스를 지속적으로 공급해야 하므로 기계식 밀링보다 운영 비용이 높습니다. 또한 유도 가열을 위한 전기 에너지와 도가니/노즐 유지보수 비용도 추가됩니다.
Q: 어떤 안전 측면에 주의가 필요한가요?
A: 고온 금속 용융물, 압력 하의 불활성 가스, 미세 가연성 분말은 화재, 폭발 방지를 위해 신중한 취급과 안전 시스템이 필요합니다. 적절한 작업자 교육은 필수입니다.
질문: 장비에 어떤 유지 관리가 필요하나요?
A: 노즐 점검 및 교체, 도가니 수리/리라이닝, 누출 점검, 에어 필터 청소는 일반적인 유지보수 작업입니다. 예약된 예방 유지보수는 고장을 최소화합니다.
Q: 금속 합금을 원자화할 수 있나요?
A: 예, 금속 합금은 크롬, 알루미늄, 티타늄과 같은 합금 원소를 용해 도가니에 정확한 비율로 첨가하여 원하는 조성을 얻기 위해 쉽게 원자화할 수 있습니다.
Q: 금속 분무는 소규모로 할 수 있나요?
A: 예, R&D 목적과 같은 소량 분말 생산을 위해 1~5kg 용량의 용융 도가니가 있는 실험실 규모 분무기를 공급업체에서 구입할 수 있습니다. 하지만 kg당 운영 비용이 더 높습니다.