금속 분무 은 금속 합금을 미세한 분말로 만드는 제조 공정입니다. 가스 또는 물 분무를 사용하여 금속을 녹여 방울로 분해합니다. 이 방울은 맞춤형 크기 범위의 분말 입자로 빠르게 응고됩니다.
금속 분무 분말은 독특한 특성을 가지고 있으며 자동차, 항공우주, 생물의학, 3D 프린팅 등 다양한 산업 분야에서 사용됩니다. 이 문서에서는 금속 분무 장비에 대한 포괄적인 개요를 제공합니다.
금속 원자화 공정 개요
금속 분무는 물리적 공정을 사용하여 입자 크기, 형태 및 미세 구조를 정밀하게 제어하여 미세한 금속 분말을 생산합니다. 다음은 금속 원자화 공정의 주요 측면입니다:
표 1: 금속 원자화 공정 개요
매개변수 | 세부 정보 |
---|---|
방법 | 가스 분무, 물 분무 |
금속 입력 | 철, 니켈, 코발트, 구리, 알루미늄 합금 등 |
녹는 | 유도 용융, 아크 용융, 전자빔 용융 |
원자화 | 고압 가스 또는 물이 용융 금속을 물방울로 분해합니다. |
고형화 | 빠른 냉각 속도로 미세 분말 생성 |
입자 크기 | 10마이크론에서 250마이크론까지 |
파티클 모양 | 구형, 위성, 불규칙한 모양 |
애플리케이션 | 금속 사출 성형, 적층 제조, 용사 분말 |
시작은 와이어 또는 잉곳 형태의 금속 합금을 용융 장치에 공급하는 것입니다. 그런 다음 용융 풀에 고속 가스 또는 물 분사를 가해 금속 방울 스프레이로 분해합니다. 이 방울은 빠르게 냉각되면서 미세한 구형 분말 입자로 응고됩니다.
가스 압력, 용융 유량 및 냉각 속도와 같은 공정 파라미터를 제어하여 분말의 유동성, 밀도, 크기 범위, 형태 및 미세 구조에 맞게 맞춤화할 수 있습니다.
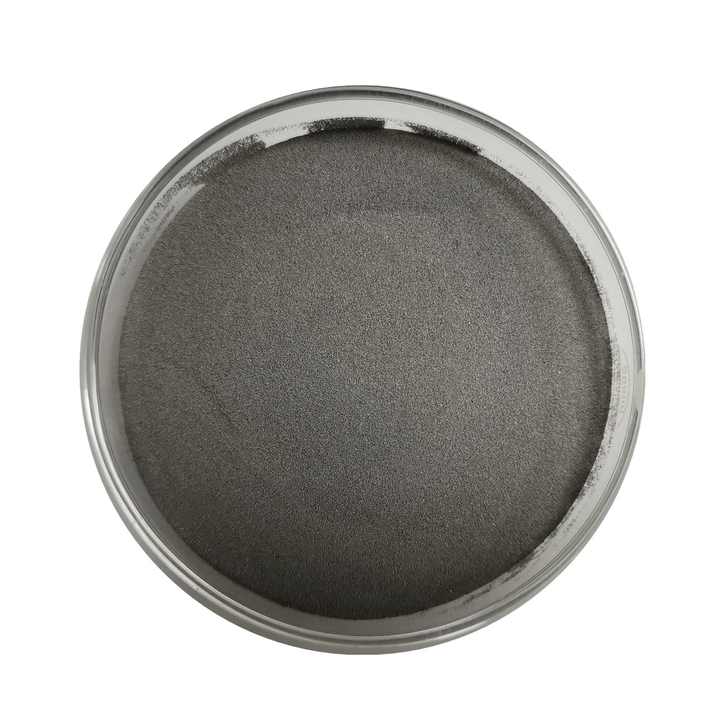
금속 분무 장비의 종류
분무 장비에는 가스 분무와 물 분무의 두 가지 주요 유형이 사용됩니다.
표 2: 가스 분무와 물 분무의 비교
매개변수 | 가스 분무 | 물 분무 |
---|---|---|
분무 매체 | 질소, 아르곤 | 물 |
압력 범위 | 5 - 50 바 | 2000 - 4000 bar |
입자 크기 | 10 - 150 미크론 | 60 - 250 미크론 |
파티클 모양 | 더 구체적 | 더 불규칙한 |
생산성 | Lower | 더 높음 |
합금 | 대부분의 합금 | 제한된 합금 |
비용 | 더 높은 장비 비용 | 장비 비용 절감 |
가스 분무
질소 또는 아르곤과 같은 불활성 가스를 5~50bar의 압력에서 사용하여 녹는점이 최대 3000°C인 합금을 분무할 수 있는 초음속 제트를 생성합니다. 가스 유속이 낮을수록 구형 분말이 더 많이 생성됩니다. 가스 분무로 10~150미크론의 더 미세한 입자 크기를 얻을 수 있습니다.
티타늄, 알루미늄, 마그네슘, 금속 복합재와 같은 반응성 합금을 포함한 대부분의 합금에 적합한 다목적 공정입니다. 하지만 물 분무에 비해 생산성이 낮습니다.
물 분무
물 분무에서는 융점이 낮은 금속을 분무할 수 있는 고속 물 분사를 형성하기 위해 2000~4000bar의 압력을 사용합니다. 이 공정은 시간당 최대 수천 파운드의 분말을 생산하는 고처리량 공정입니다.
분말은 모양이 더 불규칙하고 산소 흡착률이 높습니다. 입자 크기는 60-250 미크론이 더 일반적입니다. 이 공정은 반응성 합금에는 적합하지 않습니다.
금속 분무 시스템 설계
완전한 금속 분무 시스템은 재료 취급, 용융, 분무 및 분말 처리를 위한 여러 하위 시스템으로 구성됩니다.
표 3: 금속 분무 장비의 하위 시스템
하위 시스템 | 역할 | 사용 장비 |
---|---|---|
자재 취급 | 공급 원료 보관 및 공급 | 호퍼, 컨베이어, 피더 |
녹는 | 금속 합금을 균일한 액체로 용융 | 유도 용광로, 아크 용해로, 전자빔 용해 |
원자화 | 녹은 용융물을 미세한 물방울로 분해 | 분무 챔버, 가스/물 노즐 |
분말 처리 | 분리, 냉각, 수거 및 보관 | 사이클론, 스크린, 컨베이어, 쓰레기통 |
금속 분무 시스템을 설계할 때 중요한 요소는 다음과 같습니다:
- 온도, 가스/수압, 유량과 같은 프로세스 파라미터 제어
- 분무 전 용융 난류 최소화
- 노즐 설계 및 가스/물 분사의 균일한 분배
- 원하는 분말 미세 구조를 위한 냉각 속도 제어
- 분무 매체로부터 효율적인 분말 분리
- 미세 분말 함유 및 위험 최소화
- 실험실 테스트 및 샘플링 지점을 통한 품질 관리
금속 분무 장비 사양
기술 사양은 실험실 규모부터 대규모 생산 모델에 이르기까지 다양한 용량 시스템에 따라 다릅니다.
표 4: 금속 분무 장비의 일반적인 사양
매개변수 | 일반적인 범위 |
---|---|
용량 | 1kg/h ~ 5000kg/h |
용융 유닛 파워 | 10kW ~ 1MW |
온도 | 500°C ~ 2000°C |
압력 | 5 바 ~ 4000 바 |
노즐 크기 | 0.5mm ~ 5mm |
노즐 재질 | 텅스텐 카바이드, 실리콘 카바이드 |
파우더 크기 | 10μm ~ 250μm |
인클로저 | 스테인리스 스틸, 합금강 |
높이 | 2m ~ 10m |
발자국 | 2m x 2m ~ 10m x 4m |
제어 시스템 | PLC, SCADA |
실험실 모델에서 산업 생산 시스템에 이르기까지 용량, 압력 등급, 온도 범위 및 설치 공간이 증가합니다. 중요한 프로세스 매개변수를 모니터링하고 조절하려면 고정밀 제어가 필요합니다.
금속 분무 장비 설계 표준
장비 제조업체는 안전하고 안정적인 작동을 보장하기 위해 중요 구성 요소에 대한 설계 코드와 표준을 따릅니다.
표 5: 금속 분무 장비에 대한 관련 표준
구성 요소 | 적용 표준 |
---|---|
압력 용기 | ASME SEC VIII Div 1, EN 13445, PD 5500 |
배관 | ASME B31.3, ANSI B16.5 |
분말 처리 | NFPA 654, EN 14460 |
노즐 | ASME MFC-7M |
컨트롤 | IEC 61131, NFPA 79 |
구조적 | AISC 360, EN 1993 |
재료 구성 | ASTM, DIN, BS, UN, EN |
압력 장비, 가연성 먼지, 제어 장치, 재료 및 구조 제작과 관련된 표준을 준수해야 합니다. 공급업체는 품질 시스템과 ASME U 또는 CE 마크와 같은 코드 스탬프를 보유해야 합니다.
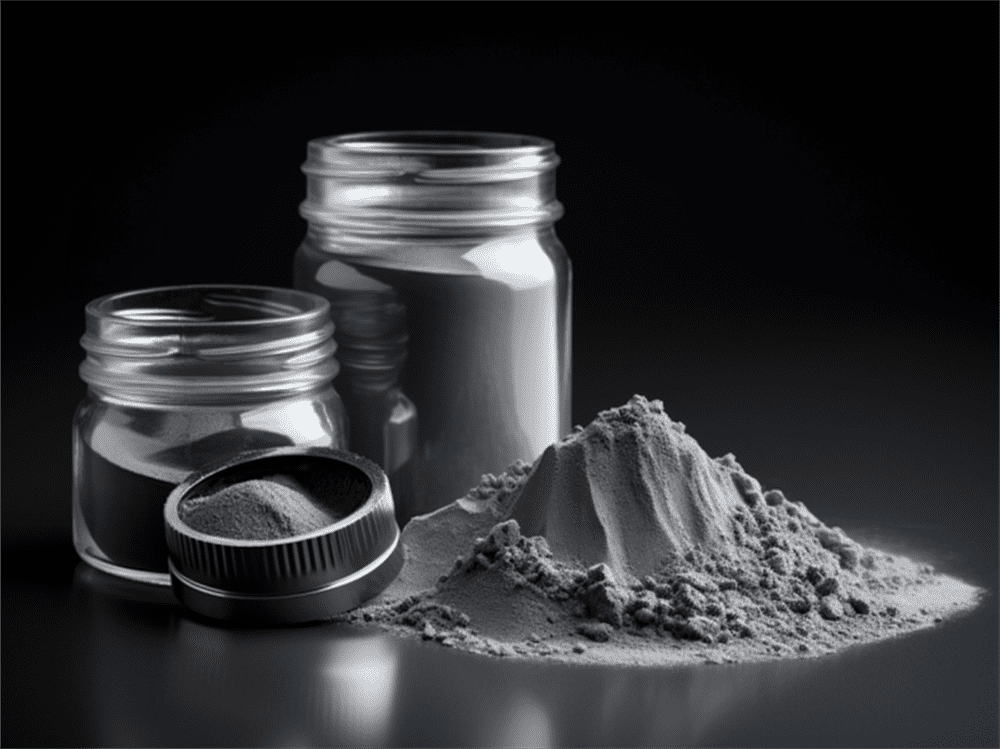
금속 분무 분말의 응용 분야
금속 분무 분말의 고유한 특성으로 인해 몇 가지 주요 응용 분야에 적합합니다:
표 6: 금속 분무 분말의 주요 응용 분야
애플리케이션 | 사용된 합금 | 혜택 |
---|---|---|
금속 사출 성형 | 스테인리스 스틸, 공구강, 구리 | 고정밀, 복잡한 부품 |
적층 제조 | 티타늄, 알루미늄, 니켈 합금 | 맞춤형 합금, 낭비 최소화 |
용사 코팅 | 몰리브덴, 구리, 철 합금 | 마모 및 부식 방지 |
분말 야금 | 철, 텅스텐 중합금 | 다공성 부품, 자석 |
항공우주 | 니켈 초합금 | 고강도 엔진 부품 |
바이오메디컬 | 티타늄, 코발트 크롬 | 관절 대체 임플란트 |
미세 구조와 입자 형태는 부품 제작 시 압축성, 유동성, 치밀화 및 소결 반응에 영향을 미칩니다. 구형 형태의 가스 분무 분말이 최고의 성능을 제공합니다.
금속 분무 장비 제조업체
소규모, 중규모 및 대규모 용량의 금속 분무 장비를 제조하는 글로벌 선두 제조업체는 다음과 같습니다:
표 7: 주요 금속 분무 장비 제조업체
회사 | 위치 | 용량 |
---|---|---|
PSI | 독일 | 실험실, 파일럿, 프로덕션 규모 |
EIG | 미국 | 소용량에서 대용량까지 |
ALD 진공 기술 | 독일 | 소규모 실험실 단위 |
TLS 테크닉 GmbH | 독일 | 중간 용량 |
샌드빅 재료 기술 | 스웨덴 | 대규모 생산 시스템 |
평판이 좋은 제조업체는 다양한 합금 그룹과 분말 요구 사항에 맞는 맞춤형 시스템을 설계하는 데 수십 년의 경험을 보유하고 있습니다. 또한 체, 밀, 금속 조직 검사기와 같은 보조 장비도 제공합니다.
표 8: 표준 금속 분무 장비 모델의 가격 범위
용량 | 가격 범위 |
---|---|
실험실 저울(1-5kg/시간) | $100,000 ~ $250,000 |
파일럿 스케일(10~50kg/h) | $500,000 ~ $150만 |
생산 규모(200kg/시간 이상) | $ 200만 ~ $ 500만 |
여러 분무 스트림, 더 큰 용융/가열 장치, 고급 제어 및 분말 처리 시스템을 갖춘 더 큰 생산 능력은 더 많은 비용이 듭니다. 위치 및 현장별 요구 사항도 가격에 영향을 미칩니다.
금속 분무 장비 공급업체를 선택하는 방법
금속 분무 장비 공급업체를 선택할 때 고려해야 할 중요한 요소입니다:
표 9: 금속 분무 장비 공급업체 선정 기준
매개변수 | 세부 정보 |
---|---|
경험 | 사업 연도, 제공된 설치 수 |
기능 | 직원 전문성, 기술 포트폴리오, R&D 시설 |
유연성 | 제품 요구 사항을 충족하는 사용자 지정 |
표준 준수 | ISO, 업계 표준과 같은 인증 |
판매 후 서비스 | 설치 지원, 교육, 유지보수 계약 |
비용 | 가격 모델, 총 소유 비용 |
배달 | 리드 타임, 배송, 사이트 준비 상태 |
위치 | 지원을 위한 지리적 근접성 |
다양한 금속, 스케일 및 파우더 사양에 대해 입증된 전문성을 갖춘 업체를 찾아보세요. 귀사의 요구에 맞는 유연한 솔루션을 제공하는지 확인하세요. 구매 전에 유지보수 비용, 예비 부품 가용성, 보증을 검토하세요.
금속 분무 시스템 설치
금속 분무 장비는 신중한 현장 계획과 설치가 필요합니다. 다음은 몇 가지 주요 지침입니다:
표 10: 금속 분무 장비 설치 체크리스트
활동 | 세부 정보 |
---|---|
사이트 계획 | 적절한 공간, 유틸리티, 2차 격리를 보장합니다. |
토목 공사 | 콘크리트 기초, 벽, 배수 공사 |
어셈블리 | 도면에 따라 하위 시스템 조립하기 |
유틸리티 | 전기, 공정 용수, 불활성 가스 라인 |
환기 | 연기 추출, HEPA 여과 |
커미셔닝 | 건식 및 습식 테스트, 시험용 파우더 실행 |
안전 | 안전 인터록, 알람 통합 |
문서 | 운영 매뉴얼, P&ID 도면, 검사 보고서 |
운영자 교육 | 강의실 및 실습 교육 |
적절한 유틸리티, 안전 시스템, 격리 구조 및 운영자 교육은 원활한 시동과 안전한 운영을 보장하는 데 도움이 됩니다. 공급업체는 설치 및 시운전 중에 기술 지원을 제공합니다.
금속 분무 시스템 작동 방법
일관된 품질의 파우더는 표준 절차에 따른 안정적인 작동에 달려 있습니다:
표 11: 금속 분무 장비 운영 지침
활동 | 지침 |
---|---|
시작 | 유틸리티 전원 공급, 퍼징 주기 실행, 노즐 예열 |
녹는 | 공급 원료를 충전하고 충분한 용융 담금 시간을 허용합니다. |
원자화 | 가스/물 밸브를 정격 압력으로 개방 |
모니터링 | 노즐 분사 패턴 관찰, 매개 변수 조정 |
종료 | 분무를 중지하고 용융물이 굳을 때까지 기다렸다가 배출합니다. |
분말 처리 | 뜨거운 분말을 조심스럽게 다루고 공기 유입을 피하십시오. |
유지 관리 | 소모품 검사, 예비 부품 재고 관리 |
안전 | 인터록, 환기가 작동하는지 확인합니다. |
품질 검사 | 크기 분석, 형태학, 화학을 위한 샘플 채취 |
온도, 압력, 물/가스 흐름과 같은 공정 변수에 대한 지속적인 모니터링이 필요합니다. 유지보수 일정과 표준 운영 절차를 엄격하게 준수해야 합니다.
금속 분무 장비의 유지보수 요구 사항
장비의 수명과 성능을 극대화하려면 정기적인 유지 관리가 필수적입니다.
표 12: 금속 분무 장비의 유지보수 체크리스트
하위 시스템 | 유지 관리 활동 | 빈도 |
---|---|---|
용융 단위 | 유도 코일, 전하 재료, 절연 검사 | 월간 |
노즐 | 오리피스 상태 점검, 노즐 교체 | 500주기 |
분무 챔버 | 내화 상태 검사 | 6개월 |
가스 라인 | 누수 확인, 유량 보정 | 3개월 |
물 라인 | 씰, 밸브, 펌프 검사 | 월간 |
컨트롤 | 센서 보정, 인터록 테스트 | 3개월 |
연기 추출 | 필터, 덕트 점검 | 주간 |
분말 처리 | 쓰레기통, 씰, 개스킷 검사 | 주간 |
인덕션 코일, 노즐, 개스킷과 같은 중요한 소모품은 가동 중단을 방지하기 위해 재고 계획을 세워야 합니다. 공급업체와 연간 유지보수 계약을 맺는 것이 좋습니다.
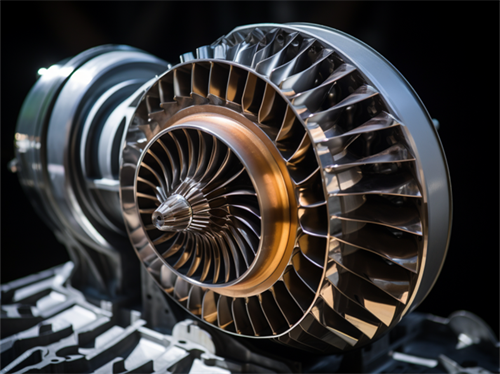
금속 분무의 장점과 한계
표 13: 금속 원자화 공정의 장점과 한계
장점 | 제한 사항 |
---|---|
입자 크기 및 형태에 대한 정밀한 제어 | 더 높은 자본 및 운영 비용 |
맞춤형 합금 및 미세 구조 가능 | 소규모 단위의 제한된 생산성 |
최소한의 용융 과열 필요 | 반응성 합금에는 불활성 가스가 필요합니다. |
가스 분무에 비해 낮은 산화율 | 물 분무가 가능한 불규칙한 분말 모양 |
불활성 가스를 사용하는 반응성 합금에 적합 | 보조 분말 처리 장비 필요 |
분말의 그물 모양에 가까운 부품 | 미세 발열성 분말의 안전 위험으로 인해 주의가 필요합니다. |
이 공정은 높은 비용에도 불구하고 특수 분말의 소량 배치에 가장 적합합니다. 반응성 미세 금속 분말을 취급할 때는 안전 절차가 필수적입니다. 대량 생산 모델은 대량 응용 분야에 더 나은 규모의 경제를 제공합니다.
자주 묻는 질문
Q: 가스 분무와 물 분무의 차이점은 무엇인가요?
A: 가스 분무는 낮은 압력에서 불활성 가스를 사용하여 더 미세하고 구형의 분말 입자를 생성하는 반면, 물 분무는 초고압에서 물을 사용하여 처리량은 높지만 분말 모양이 불규칙합니다.
Q: 금속 분무로 어떤 입자 크기를 얻을 수 있나요?
A: 방법과 작동 매개변수에 따라 약 10마이크론에서 250마이크론 범위의 입자 크기를 생산할 수 있습니다. 가스 분무는 10~100미크론 범위의 더 미세한 분말을 생산할 수 있습니다.
Q: 분말로 분무할 수 있는 금속에는 어떤 것이 있나요?
A: 강철, 알루미늄, 티타늄, 니켈, 코발트, 구리 합금을 포함한 대부분의 합금 시스템은 분무가 가능합니다. 녹는점이 매우 높은 내화성 금속은 분무하기가 어렵습니다.
Q: 금속 분무 장비 시스템 비용은 얼마인가요?
A: 비용은 용량, 자동화 및 사용자 지정 요구 사항에 따라 실험실 단위의 경우 약 $100,000달러에서 대규모 산업 시스템의 경우 수백만 달러까지 다양합니다.
Q: 금속 분무에는 어떤 안전 예방 조치가 필요하나요?
A: 주요 요구 사항에는 환기가 되는 인클로저, 불활성 가스 퍼징 주기, 안전 인터록, 미세 발열성 금속 분말에 대한 적절한 격리 시스템, 개인 보호 장비 등이 있습니다.
Q: 분무 분말의 입자 크기 분포는 어떻게 결정되나요?
A: 입자 크기는 용융 유량, 분무 가스/수압, 노즐 설계, 용융 온도 및 냉각 속도와 같은 요소의 영향을 받습니다. 이러한 파라미터를 최적화하는 것이 원하는 크기 분포의 핵심입니다.
Q: 금속 분무 분말의 주요 응용 분야는 무엇인가요?
A: 주요 응용 분야는 금속 사출 성형, 3D 프린팅, 용사 코팅, 분말 야금 프레스 및 소결, 항공우주 부품, 생체 의료용 임플란트 등 적층 제조입니다.
Q: 금속 분무 장비의 유지보수는 얼마나 자주 필요하나요?
A: 성능을 극대화하려면 가스 라인, 수도 라인, 노즐, 인덕션 코일, 안전 인터록과 같은 하위 시스템에 대해 몇 개월마다 정기적인 예방 유지보수를 실시하는 것이 좋습니다. 소모품은 사용량에 따라 수백 주기마다 교체해야 할 수도 있습니다.
결론
금속 분무는 합금을 산업 전반의 까다로운 응용 분야에 맞는 고유한 특성을 가진 미세한 구형 또는 불규칙한 분말로 변환합니다. 가스 분무는 대용량 물 분무에 비해 입자 크기와 모양을 더 세밀하게 제어할 수 있습니다.
최적의 성능을 위해서는 재료 취급, 용융, 분무 및 분말 수집을 위한 하위 시스템을 신중하게 설계해야 합니다. 평판이 좋은 공급업체는 소규모 R&D 시스템부터 대규모 산업 용량에 이르기까지 맞춤형 장비를 제공합니다.
금속 분무 장치를 작동할 때 생산, 효율성 및 안전을 극대화하려면 적절한 설치, 안전 기능, 작업자 교육 및 일상적인 유지보수가 필수적입니다. 분무된 금속 분말을 사용하면 기존 야금 방식으로는 생산하기 어려운 고성능 부품을 제조할 수 있습니다.