알루미늄은 낮은 밀도, 우수한 기계적 특성, 기계 가공성, 내식성 및 전도성 덕분에 적층 제조에 널리 사용되는 금속 분말입니다. 알루미늄 파우더 특성을 최적화하면 항공우주, 자동차 및 산업 분야에서 강하고 가벼운 알루미늄 부품을 안정적으로 인쇄할 수 있습니다.
이 가이드는 파우더 베드 융합 또는 바인더 제트 3D 프린팅을 위한 알루미늄 분말 소싱에 대한 특성, 사양, 분무 생산, 품질 보증 고려 사항, 응용 분야 및 조언을 다룹니다.
3D 프린터 알루미늄 분말 작곡
AM에 사용되는 일반적인 알루미늄 등급은 다음과 같습니다:
합금 | 설명 | 일반적인 구성 |
---|---|---|
AlSi10Mg | 실리콘과 마그네슘이 첨가된 주조 합금으로 강도와 내식성 향상 | 나머지 Al, 9-11% Si, 0.25-0.45% Mg, 0.8% 최대 Fe, 0.2% 최대 Cu |
AlSi7Mg | 실리콘 함량이 약간 낮은 AlSi10Mg와 매우 유사합니다. | 나머지 Al, 6-8% Si, 0.25-0.45% Mg, 0.8% 최대 Fe, 0.2% 최대 Cu |
6061 | 마그네슘과 실리콘이 함유된 매우 일반적인 열처리 가능 단조 합금 | 나머지 Al, 0.8-1.2% Mg, 0.4-0.8% Si, 0.7% 최대 Fe, 0.15-0.4% Cu, 0.04-0.35% Cr |
기계적 특성, 내식성, 용접성 요구 사항 및 합금 비용에 맞게 구성을 조정합니다.
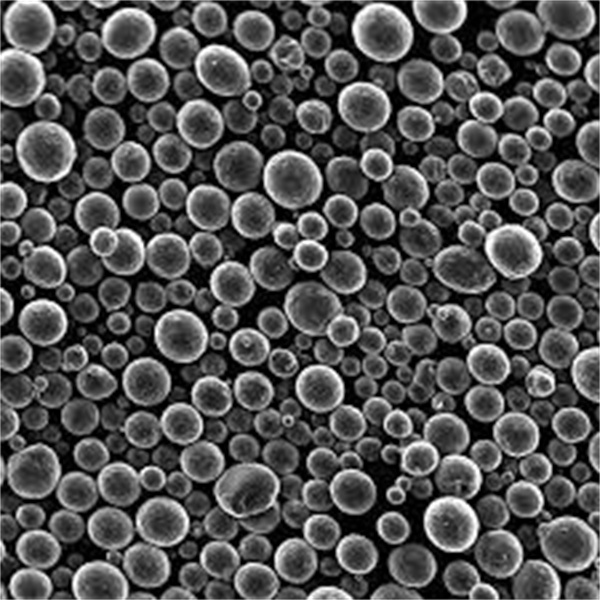
사양 개요
매개변수 | 세부 정보 | 테스트 방법 |
---|---|---|
순도 | >98% 알루미늄 선호 | ICP 분석 |
파티클 모양 | 구형 > 90% 필요 | 현미경 |
크기 분포 | D50: 25-45μm 일반 | 레이저 회절 |
겉보기 밀도 | 1.2-1.8g/cc | 홀 유량계 |
유동성 | 50g 시료에 대한 홀 흐름 25-50초 | 홀 유량계 |
산화물 및 수산화물 | <3% 무게 기준 | TGA, XRD, 불활성 가스 융합 |
수분 함량 | <중량 기준 0.2% 미만 | TGA 분석 |
고밀도의 견고한 부품으로 결함을 최소화하는 데 필요한 높은 파우더 품질과 일관성을 갖춘 AM 공정.
분무 방법
3D 프린터 알루미늄 분말 생산 비아:
- 공기 분무 - 고압의 공기가 용융된 알루미늄을 미세한 구형 방울로 분해하여 산화를 방지합니다. 저에너지 공정으로 바인더 제트 인쇄에 적합한 더 큰 입자를 생성합니다.
- 질소 분무 - 질소 주변은 분무 시 표면 산화를 방지하여 SLM 및 EBM에 선호되는 미세한 분말 크기, 낮은 산소 및 높은 유동 특성을 가능하게 합니다.
- 전극 회전 분무 - 얇은 용융 알루미늄을 질소로 빠르게 회전시키면 크기 분포가 매우 촘촘하고 포장 밀도가 우수한 분말이 만들어집니다.
공정 대기, 냉각 속도 및 가스 역학을 제어하면 우수한 유동 및 전단 응답이 필요한 파우더 베드 애플리케이션에 적합한 알루미늄 입자 크기와 형태를 최적화할 수 있습니다.
기계적 특성
합금 | 밀도(g/cc) | 항복 강도(MPa) | 인장 강도(MPa) | 신장 |
---|---|---|---|---|
AlSi10Mg | 2.68 | 228 | 398 | 7.9% |
AlSi7Mg | 2.74 | 261 | 372 | 8.1% |
6061 | 2.70 | 241 | 303 | 11% |
지정된 강도를 충족하려면 최적화된 인쇄 파라미터와 에이징과 같은 후처리가 필요합니다. 부품 방향도 기계적 성능에 큰 영향을 미칩니다.
금속 3D 프린팅 애플리케이션
AlSi10Mg 알루미늄은 적층 제조를 위해 산업 전반에 걸쳐 폭넓게 사용되고 있습니다:
- 항공우주 및 방위: 경량 기체, 무인 항공기 부품, 컨포멀 열교환기 및 냉각판, 액티브 격자 구조. 복합재 레이업을 위한 신속한 툴링.
- 자동차: 알루미늄은 강철보다 3배 낮은 응집 에너지를 가지고 있어 경량화를 통해 연비를 향상시킬 수 있습니다. 맞춤형 차체 패널, 피팅, 컨트롤 암과 같은 섀시 요소를 통해 성능을 개선할 수 있습니다. 매니폴드 하우징과 같은 열교환기 부품은 기능을 향상시킵니다. 탄소 섬유 복합재용 지그 및 고정 장치.
- 산업용: 중소형 로트 크기를 위한 맞춤형 시리즈 생산. 최적화된 폼 팩터로 전자제품 열 관리를 위한 방열판. 임펠러, 펌프, 밸브 및 하우징과 같은 유체 흐름 구성 요소. 가벼운 내구성을 제공하는 지그, 픽스처, 가이드 및 게이지.
- 건축: 주문형으로 제작되는 특수 맞춤형 부품. 브론즈 인필과 하이브리드 프린팅을 사용한 장식 요소. 시각화를 위한 차원적으로 정확한 스케일 모델.
인증 표준
- ASTM B556 - 합금 6061을 사용하는 분말 야금(PM) 알루미늄 합금 구조 부품의 표준 사양
- ASTM B925 - 자동차, 항공우주 및 방위 응용 분야를 위한 분말 야금 방법을 통한 가공용 프리미엄급 알루미늄 합금 분말에 대한 표준 사양
- ASTM E2926 - 적층 제조 알루미늄 분말 및 공급 원료에 대한 표준 사양
구매 전에 목표 등급 사양 및 AM 처리 요구 사항과 관련된 규정 준수를 보여주는 통계적으로 검증된 배치 인증서를 검토하세요.
일반적인 결함
주요 알루미늄 금속 AM 결함 및 근본 원인:
결함 | 원인 | 솔루션 |
---|---|---|
다공성 | 수분, 산화물, 금속 기화 | 습도 감소, 산화물 최소화, 에너지 밀도 조정 |
크래킹 | 급속 냉각, 잔류 응력, 불순물 | 빌드 플레이트 예열 최적화, 고온 등방성 프레싱, 고순도 파우더 |
박리 | 리코터 블레이드 힘; 레이어 융합 불량 | 부드러운 파우더 크기 분포, 스프레드 레이어 최적화, 스프레더 설정 유효성 검사 |
볼링 | 높은 표면 장력으로 흐름 억제 | 빠른 녹임을 위한 예열판 |
표면 마감 문제 | 스패터, 녹지 않은 입자가 융합된 경우 | 주어진 파우더에 대한 파라미터 최적화 |
시험 제작을 통해 프린팅 파라미터를 조정하여 양산 전에 완벽한 밀도의 부품을 제작할 수 있습니다.
가격 요소
매개변수 | 영향 |
---|---|
파우더 등급 | 높은 순도/구형도에는 프리미엄이 따릅니다. |
로트 크기 | 500kg 이상에서 규모의 경제 실현 |
인증 수준 | 전체 인증과 배치 테스트 |
분무 방법 | 질소 > 공기, 높은 농도와 낮은 산화물로 인해 질소 > 공기 |
지역 물류 | 가능하면 로컬에서 소싱 |
더 작은 크기의 알루미늄 AM 파우더를 납품할 경우 $50-100/kg 정도의 가격이 책정될 것으로 예상됩니다. 대형 제조업체는 규모의 경제를 제공합니다.
구매 고려 사항
매개변수 | 중요성 |
---|---|
품질 규정 준수 | 높음 |
샘플링 가용성 | 높음 |
기술 전문성 | Medium |
고객 참조 | Medium |
가격 책정 | 낮음 |
공급업체 비교
제조업체 | 크기 범위 | 품질 | 일관성 | 리드 타임 | 가격 책정 |
---|---|---|---|---|---|
[브랜드 1] | 10-45 μm | 완전 인증 | 매우 일관성 있음 | 12~14주 | $$$ |
[브랜드 2] | 15-65 μm | 배치 테스트 | 사소한 변화 | 3-4주 | $ |
[브랜드 3] | 10-63 μm | 독립 MPI | 최소 사양 충족 | 8~10주 | $$ |
가격 프리미엄이 있더라도 부품 애플리케이션의 품질 규정 준수 요구 사항에 부합하는 선도적인 브랜드를 선택하여 결함 및 속성 편차 위험을 방지하세요.

자주 묻는 질문
Q: 알루미늄 레이저 파우더 베드 용융에 가장 적합한 입자 크기는 얼마입니까?
A: 25-45 μm 알루미늄 분말 크기 분획은 파우더 베드 응용 분야에서 확산 및 고밀도 융합에 이상적인 우수한 전단 및 용융 흐름 응답으로 고밀도 패킹을 용이하게 합니다.
Q: 알루미늄 AM 파우더를 올바르게 보관하려면 어떻게 해야 하나요?
A: 직사광선을 피해 서늘하게 보관할 경우 유통기한이 6~12개월로 제한되는 산화를 방지하고 안정화를 위해 습기 흡수 백으로 용기를 밀폐하세요.
Q: 금속 AM용 알루미늄 파우더는 특별한 취급 주의가 필요합니까?
A: 위험하지 않은 것으로 분류되지만 미세한 금속성 미립자는 호흡기 건강 및 먼지 폭발 위험을 수반하므로 안전 프로토콜을 수립해야 하므로 환기가 잘 되는 곳에서 승인된 개인보호구를 착용하고 파우더를 사용해야 합니다.
Q: 적층 제조 알루미늄 부품에는 일반적으로 어떤 후처리가 이루어지나요?
A: 알루미늄 AM 부품은 잔류 응력을 완화하고 기계적 특성과 표면 마감을 개선하기 위해 용액 처리, 노화 침전 경화, 패시베이션 및 전기 연마를 거치는 경우가 많습니다. 보호 코팅은 부식과 내마모성을 개선합니다.