개요 전자빔 용융기
전자빔 용융(EBM)은 진공 조건에서 고출력 전자빔을 사용하여 금속 분말을 층별로 완전히 밀집된 부품으로 융착하는 데 사용되는 적층 제조 기술입니다. EBM 장비는 다른 금속 3D 프린팅 방식으로는 달성할 수 없는 탁월한 제작 속도와 기계적 특성을 제공합니다.
EBM 기술의 주요 속성은 다음과 같습니다:
표 1: 전자빔 용융 기술 개요
속성 | 설명 |
---|---|
열원 | 고강도 전자빔 |
환경 | 고진공 |
공급원료 | 금속 파우더 베드 |
빔 제어 | 전자기 렌즈 및 코일 |
빌드 모드 | 층별 금속 분말 융합 |
애플리케이션 | 항공우주, 의료, 자동차, 툴링 |
정밀한 빔 포커싱과 빠른 스캐닝을 활용하여 티타늄, 니켈 합금, 공구강, 내화 금속과 같은 전도성 소재를 가공 제품보다 우수한 특성을 지닌 완전 고밀도 부품으로 융합하는 EBM은 티타늄, 니켈 합금, 공구강, 내화 금속과 같은 전도성 소재를 가공 제품보다 우수한 특성으로 융합합니다.
제어된 진공 환경은 오염을 방지하고 지능형 에너지 전달과 높은 예열 온도는 뒤틀림이나 균열을 유발하는 잔류 응력을 최소화합니다.
이러한 핵심 원칙을 이해하면 EBM이 가장 까다로운 산업 애플리케이션에 맞춤화된 탁월한 기계적 성능을 제공하는 이유를 알 수 있습니다.
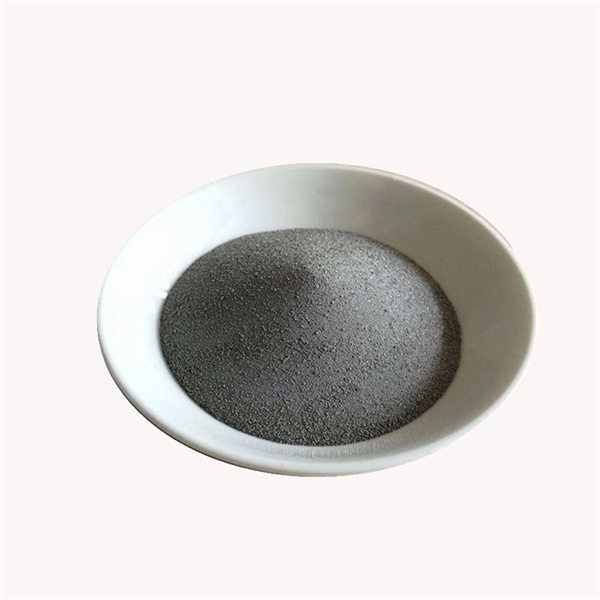
전자빔 용융 시스템의 유형
시장에는 다양한 산업 요구 사항을 충족하는 빌드 볼륨, 빔 출력 수준 및 생산 용량을 제공하는 여러 범주의 EBM 시스템이 있습니다.
표 2: 전자빔 용융 시스템의 유형
머신 클래스 | 빌드 크기 | 빔 파워 | 일반적인 애플리케이션 |
---|---|---|---|
소규모 플랫폼 | 150mm 큐브 | 3-4 kW | 치과용 대처, 의료 기기 |
표준 플랫폼 | 200 x 200 x 350mm | 6~8kW | 항공우주 부품, 툴링 |
미드레인지 플랫폼 | 400 x 400 x 400mm | 14-16 kW | 자동차 부품, 대형 항공우주 부품 |
대형 플랫폼 | 800 x 800 x 500mm | 30-60 kW | 구조용 브래킷, 터빈 블레이드 |
더 큰 기계는 항공우주나 자동차 같은 산업에서 더 큰 부품을 사용하여 어셈블리를 최적화할 수 있습니다. 더 작고 저전력 시스템은 치과 및 더 넓은 의료 분야의 고부가가치 부품을 대상으로 합니다.
현재 대부분의 EBM 제공업체는 시간이 지남에 따라 증가하는 생산 수요에 맞춰 용량, 구축 규모, 빔 파워를 확장할 수 있는 모듈형 아키텍처를 제공합니다.
전자빔 용융 공정의 기초
EBM 적층 제조와 관련된 핵심 하위 시스템과 처리 단계는 다음과 같습니다:
표 3: 전자빔 용융 기본 사항 개요
스테이지 | 기능 | 주요 구성 요소 |
---|---|---|
1. 분말 취급 | 신선한 재료의 레이어 배포 | 파우더 호퍼 및 갈퀴 |
2. 빔 생성 | 전자빔 생성 및 가속 | 텅스텐 필라멘트 음극, 양극 전압 |
3. 빔 포커싱 | 전자석 수렴 빔 | 마그네틱 코일 렌즈 |
4. 빔 편향 | 직접 집중된 빔 위치 | 편향 코일 |
5. 진공 시스템 | 오염 물질 없는 환경 보장 | 펌프, 밸브, 센서 |
6. 제어 시스템 | 모든 기능 조정 및 모니터링 | 컴퓨터, 소프트웨어, 센서 |
이러한 하위 시스템의 통합 운영을 통해 EBM은 금속 분말 공급 원료로 부품을 레이어별로 효율적으로 제작할 수 있습니다:
- 빠른 빔 편향 및 스캐닝으로 탁월한 속도로 재료를 정밀하게 융합합니다.
- 진공 환경으로 오염을 방지하는 가스 제거
- 자동 분말 분배로 고밀도 보장
- 피드백 센서는 치수 정확도를 제공합니다.
- 강력한 제어 기능으로 전체 빌드 프로세스 순서 지정
진공 생산 환경에서 순수 금속 분말 소모품과 고강도 빔 열원의 조합을 통해 이전에는 불가능했던 재료 성능을 구현할 수 있습니다.
이러한 기본 원칙을 이해하면 구매자가 제조 생산성, 품질 및 애플리케이션 요구 사항을 충족하는 최적의 EBM 시스템을 선택하는 데 도움이 됩니다.
주요 사양 전자빔 용융기
금속 적층 제조용 EBM 장비를 구매할 때 구매자가 생산 목표와 시설 제약 조건에 따라 평가해야 하는 수많은 성능 중심 사양이 있습니다.
표 4: 주요 전자빔 용융기 사양
매개변수 | 일반적인 범위 | 중요성 |
---|---|---|
빔 파워 | 3-60 kW | 빌드 속도, 최대 부품 크기 |
빔 속도 | 최대 8m/s | 생산성, 레이어 시간 |
스팟 사이즈 | 50-200 μm | 해상도, 세밀한 기능 정의 |
빔 전류 | 1-50 mA | 머티리얼 호환성, 튜닝 최적화 |
가속전압 | 30-150kV | 용융 풀 깊이, 남은 분말 |
진공 | 5 x 10-5 mbar | 순도, 물질적 무결성 |
파우더 층 두께 | 50-200 μm | 수직 해상도, 최종 밀도 |
빔 출력, 스캔 속도, 최소 피처 크기, 파우더 층 두께와 같은 요소는 생산성 목표와 애플리케이션 요구 사항에 따라 적합한 장비를 선택해야 합니다.
기타 주요 고려 사항은 다음과 같습니다:
- 제어 소프트웨어 - 적응형 빌드 설정 도구, 자동화, 데이터 분석/모니터링 기능
- 재료 팔레트 - 적용 범위를 나타내는 사전 인증된 자료의 수
- 보조 장비 - 보조 분말 처리 도구, 후처리, 열처리 오븐
- 서비스 - 유지보수 계약, 애플리케이션 최적화 지원, 운영자 교육, 기계 운송
현재와 미래의 기대치를 기준으로 사양을 평가하면 EBM 용량에 현명하게 투자할 수 있습니다.
전자빔 용융 채택의 경제성
평균 100만~250만 달러에 달하는 장비 도입 비용 외에도 제조 조직은 EBM을 사내에 도입할 때 발생하는 전체 생산 경제성을 모델링해야 합니다.
표 5: EBM 처리 경제성 요약
비용 요소 | 범위 |
---|---|
머신 플랫폼 | $800,000 ~ $2,500,000 |
시설 인프라 | $100,000 ~ $500,000 |
설치 서비스 | $50,000 ~ $250,000 |
보조 분말 취급 도구 | $50,000 ~ $150,000 |
연간 자료 사용량 | $100,000 ~ $800,000 |
소모품/교체 부품 | $20,000 ~ $100,000 |
인건비(운영자, 엔지니어) | 시스템당 1~3명의 기술자 |
에너지 소비량 | $15,000 ~ $50,000 |
유지 관리 계약 | $50,000 ~ $150,000 |
산업용 플랫폼의 경우 장비 구입 비용이 100만~200만 달러에 이르는 것 외에도 운영 비용과 수익성에 영향을 미치는 다른 변수가 있습니다:
- 자료 사용량 - 금속 분말은 부품당 비용에 최대 30%를 기여합니다.
- 노동 - 수동 및 자동화된 후처리 요구사항에 따른 인력 요구 사항
- 시설 - 설치 서비스, 안전 및 유틸리티 비용 합산
- 유지 관리 - 예방적 유지 관리는 생산 처리량과 품질에 필수적입니다.
- 최적화 - 생산성 대 결함률 및 수동 개입의 균형 맞추기
EBM 용량을 확보하기 전에 이러한 요소를 분석하면 현실적인 비즈니스 계획을 수립할 수 있습니다. 정확한 비용 모델링과 생산 시나리오 분석을 통해 리스크와 수익성 전망에 대한 가시성을 높일 수 있습니다.
EBM용 인기 자료
엄격하게 제어되는 진공 환경과 높은 빔 강도가 결합된 EBM은 기존 방식으로는 제조하기 어려운 반응성, 내화성 및 맞춤형 합금을 가공하는 데 독보적으로 용이합니다.
**표 6: EBM 이점을 활용하는 일반적인 합금 시스템 **
머티리얼 클래스 | 합금 예시 | 애플리케이션 |
---|---|---|
티타늄 합금 | Ti-6Al-4V, Ti-6Al-4V ELI | 항공우주 기체 및 엔진 |
니켈 초합금 | 인코넬 718, 인코넬 625 | 터빈 블레이드, 로켓 노즐 |
공구강 | 마징 300, H13 | 사출 금형, 툴링 플레이트 |
코발트 크롬 합금 | CoCrMo, CoCrW | 의료 및 치과 임플란트 |
내화성 금속 | 탄탈륨, 텅스텐 | 고온 용광로 요소, 차폐 |
EBM에 가장 많이 사용되는 합금 시스템은 여전히 구조 부품용 티타늄 합금, 극한 환경을 위한 니켈 초합금, 의료용 코발트 크롬 배합입니다.
그러나 EBM은 알루미늄이나 니오븀과 같이 다른 방법으로는 가공하기 어려운 반응성 금속을 활용한 혁신도 가능하게 합니다. 유연한 분말 혼합 옵션과 결합하여 연구소는 특정 물성 요구 사항에 맞는 새로운 합금 구성을 설계하는 데 EBM의 이점을 활용합니다.
전자빔 용융의 이점
다른 파우더 베드 융합 기술과 비교할 수 없는 매우 빠른 제작 속도 외에도 EBM은 추가적인 기술적, 경제적 이점을 제공하므로 중요한 상업 및 방위 애플리케이션에 이상적인 공정입니다.
**표 7: 전자빔 용융의 주요 이점 **
혜택 | 설명 |
---|---|
높은 입금률 | 레이저 기반 시스템보다 최대 10배 빠른 빌드 속도 |
탁월한 소재 특성 | 주조 또는 가공된 대체품보다 향상된 성능 |
높은 생산 밀도 | 진공 환경에서 높은 빔 에너지 덕분에 100%에 근접합니다. |
매우 낮은 잔류 스트레스 | 70-90% 왜곡 감소로 가공 공차 필요량 감소 |
탁월한 반복성 | 자동화 빌딩의 엄격한 허용 오차 및 기계 장치 |
자유로운 디자인 | 내부 채널, 생체 공학 구조, 무게 감소 |
부품 통합 | 단일 구성 요소로 결합된 어셈블리 |
EBM이 가치를 제공하는 구체적인 사례는 다음과 같습니다:
생산성
- 더 큰 빌드 볼륨을 활용하여 5배 빠른 고관절 임플란트 어셈블리 제조로 더 많은 유닛을 동시에 생산합니다.
- EBM 최적화 노력을 통해 항공우주 랜딩기어 부품 인벤토리를 30개에서 2개로 통합
성능
- 주조보다 코발트 크롬 치과용 코핑에서 더 나은 내피로성 제공
- 기존 니켈 초합금 주조의 다공성 결함이 전혀 없는 깨끗한 인코넬 718 미세 구조 구현
품질
- 높은 예열로 Ti-6Al-4V 의료용 부품의 내부 응력 제로 보장, 폐기율 감소
- 진공 공정 환경을 활용하여 반응성 Ta 및 Nb 합금의 오염 결함 방지
다른 금속 적층 제조 기술이나 기존 기술로는 불가능한 빠른 제작 속도와 탁월한 재료 특성 덕분에 EBM은 최고 수준의 기계적 성능을 요구하는 생산 애플리케이션에 가장 적합한 솔루션입니다.
개요 전자빔 용융기 공급업체
다양한 기존 산업 제조업체와 전문화된 신규 업체가 항공우주, 의료, 자동차 및 산업 분야에서 연구부터 대량 생산까지 확장 가능한 전자빔 용융 솔루션을 제공합니다.
표 8: 주요 전자 빔 용융 시스템 제조업체
공급업체 | 세부 정보 | 타겟 세그먼트 |
---|---|---|
GE 애디티브 | 선구적인 EBM 기술 | 항공우주, 의료, 자동차 |
스키아키 | 가장 큰 봉투 크기 | 항공 우주 구조물 |
웨이랜드 첨가제 | 저예산 금속 3D 프린팅 플랫폼 | 소규모 기계 공장 |
절 | 연구 등급 EBM 시스템 | 대학 |
나노 차원 | 멀티 머티리얼 기능 | 전자, 방위 |
현재 GE Additive의 일원이 된 업계 리더 Arcam EBM은 특허 솔루션 덕분에 일찍이 리더십을 확립했으며, 의료용 임플란트 및 항공 우주 분야에서 독보적인 위치를 차지하고 있습니다.
한편 웨이랜드와 같은 신규 업체는 경제적인 시작 플랫폼으로 중소 제조업체를 공략하여 채택을 확대하는 것을 목표로 합니다.
생산자, 연구자, 최종 사용자 그룹 간의 재료, 부품 검증 및 기계 최적화에 대한 협업은 궁극적으로 더 중요한 애플리케이션 전반으로 EBM 보급을 확대할 것입니다.
전자빔 용융 채택의 향후 전망
뛰어난 생산 속도와 다른 금속 첨가제나 기존 공정으로는 불가능한 뛰어난 기계적 특성으로 인해 향후 5~7년 동안 항공우주, 의료 기기, 자동차 및 산업 전반에 걸쳐 EBM 도입이 크게 확대될 것으로 보입니다.
3D 프린팅을 활용하여 공급망을 재편하는 조직에서 프로토타입 제작을 넘어 본격적인 생산에 이르기까지 EBM의 이점에 대한 인식이 확대됨에 따라 장비 투자가 증가할 것으로 예상됩니다.
이제 상용화된 더 큰 빌드 엔벨로프 덕분에 어셈블리를 더 적은 수의 구성 요소로 통합할 수 있어 재고 물류와 리드 타임을 더욱 최적화할 수 있습니다.
그러나 시스템 비용의 감소와 자재 가용성의 증가는 소규모 제조업체의 EBM 기술 접근성을 지속적으로 개선해야 합니다. 보조 파우더 처리 도구와 후처리 워크플로우를 간소화하면 도입도 간소화될 것입니다.
전반적으로 EBM은 대체 금속 첨가제 또는 기존 제조 공정에 비해 탁월한 증착 속도와 탁월한 재료 특성 덕분에 점점 더 광범위한 생산 애플리케이션에 적용될 수 있는 강력한 모멘텀을 유지하고 있습니다.
자주 묻는 질문
질문: EBM을 지원하려면 어떤 시설 인프라가 필요하나요?
A: 장비 자체의 경우 500평방피트 이상의 공간이 필요하며, 파우더 처리 스테이션과 후처리를 위한 공간이 더 필요합니다. 12,000파운드 이상의 장비 하중을 견딜 수 있는 콘크리트 바닥 보강이 일반적입니다.
질문: EBM 머신당 몇 명의 운영자가 필요하나요?
A: 자동화 수준과 생산량에 따라 한 명의 기술자가 여러 대의 EBM 장치를 지원할 수 있습니다. 추가 직원이 파우더 작업, 후처리 작업, 유지보수 및 엔지니어링을 처리합니다.
Q: EBM 기술로 처리할 수 없는 재료에는 어떤 것이 있나요?
A: 비전도성 폴리머는 전자빔으로 가공할 수 없습니다. 그러나 EBM은 다른 방식으로 제조 가능한 거의 모든 전도성 금속 합금 시스템을 수용합니다.
질문: EBM 기술과 관련된 안전 위험은 무엇인가요?
A: 고전력 전자빔 전압은 적절한 인클로저와 제어가 필요한 아크 플래시 위험을 초래합니다. 또한 반응성 금속 분말에 노출되면 화재 및 흡입 위험에 대한 프로토콜이 필요하므로 보호 장비와 교육이 필요합니다.
Q: EBM에 2차 열처리가 필요한가요?
A: 특정 합금은 열처리를 통해 미세 구조를 더욱 개선하고 기계적 특성을 맞춤화할 수 있습니다. 그러나 EBM 공정에 내재된 빠른 응고 사이클과 높은 예열 온도는 일반적으로 이러한 후처리 단계를 제거합니다.