개요
원자화된 금속 용융 금속을 미세한 물방울로 변환하여 분말 입자로 응고시키는 공정인 분무화를 통해 생산되는 금속 분말을 말합니다. 원자화를 통해 입자 크기, 모양 및 화학 성분이 정밀한 금속 분말을 생산할 수 있습니다.
분무 금속 분말은 제조, 3D 프린팅, 금속 사출 성형, 브레이징, 용접, 열 분무 등 다양한 분야에서 사용됩니다. 이 문서에서는 분무 금속 장비의 유형, 특성, 응용 분야, 사양, 공급업체, 설치, 운영, 유지보수 등에 대한 자세한 가이드를 제공합니다.
원자화된 금속 장비의 유형
장비 | 설명 |
---|---|
가스 분무기 | 고속 불활성 가스(N2, Ar)를 사용하여 용융 금속 스트림을 미세한 물방울로 분해합니다. |
물 분무기 | 고압 워터 제트를 사용하여 용융 금속을 분말로 원자화합니다. |
회전 전극 분무기 | 회전하는 금속 와이어 또는 디스크의 원심력을 사용하여 용융 금속을 물방울로 분해합니다. |
초음파 분무기 | 초음파 진동을 사용하여 모세관 파를 생성하고 용융 금속 흐름을 분해합니다. |
원심 분무기 | 회전 디스크에 부은 용융 금속은 원심력에 의해 바깥쪽으로 튕겨져 나가는 물방울로 부서집니다. |
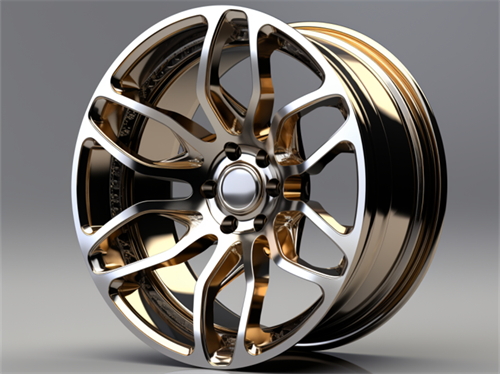
원자화된 금속 분말의 특성
특성 | 설명 |
---|---|
입자 크기 | 미크론에서 밀리미터까지, 분무 공정 파라미터로 제어 가능 |
파티클 모양 | 구형, 불규칙형 또는 위성형(방법 및 조건에 따라 다름) |
크기 분포 | 특정 분무 기술을 사용하여 매우 좁게 만들 수 있습니다. |
순도 | 정제된 용융 금속 공급 원료를 사용하여 고순도 가능 |
밀도 | 금속의 이론적 밀도에 근접 가능 |
유동성 | 입자 크기, 모양 및 분포에 영향을 받으며 취급 시 중요함 |
소결 활동 | 표면적이 넓은 미세 분말은 압축 중에 빠르게 소결되어 단단한 금속으로 변합니다. |
원자화된 금속 분말의 응용 분야
애플리케이션 | 세부 정보 |
---|---|
금속 분말 베드 융합 | 레이저/전자빔 파우더 베드 3D 프린팅에 사용되는 원자화된 미세 분말 |
바인더 분사 | 바인더 제트 3D 프린팅용 스테인리스 스틸, 공구강, 알루미늄 분말 |
금속 사출 성형 | 스테인리스 스틸, 티타늄, 알루미늄 분말을 바인더와 혼합하여 성형한 제품입니다. |
용사 코팅 | 마모/부식 방지를 위해 표면에 분사되는 Fe, Ni, Co, Cu 및 합금 분말 |
브레이징 페이스트 | 금속 접합용 페이스트 제형의 Ag, Cu, Ni 합금 분말 |
마찰 재료 | Cu, Fe 파우더는 브레이크 라이닝과 클러치 표면의 마찰과 마모를 개선합니다. |
용접 | 용접 특성 향상을 위해 아크 용접 시 첨가되는 원자화된 Ti, Al 분말 |
분말 야금 | 원자화된 Fe, 강철, 구리 분말을 그물 모양의 구성 요소로 프레스 및 소결합니다. |
자기학 | 자석 및 인덕터에 압착된 절연 철, 페라이트 분말 |
금속 촉매 | 화학 산업에 사용되는 광범위한 합금 분말 촉매 |
원자화 금속 장비의 사양
매개변수 | 일반적인 범위 |
---|---|
생산 능력 | 10-100kg/시간 |
가스 소비량 | 10-100 Nm3/시간 아르곤 또는 질소 |
냉각수 사용량 | 100-1000 L/min |
전력 소비 | 50-500 kW |
바닥 공간 | 100-500 평방 피트 |
제어 시스템 | PLC, SCADA, 데이터 모니터링 |
안전 시스템 | 가스 감지기, 화재 진압, 안전 PPE |
용융 금속 취급 | 세탁기, 물통, 주입 시스템 |
파우더 수집 | 사이클론, 백 필터, 스크류 컨베이어 |
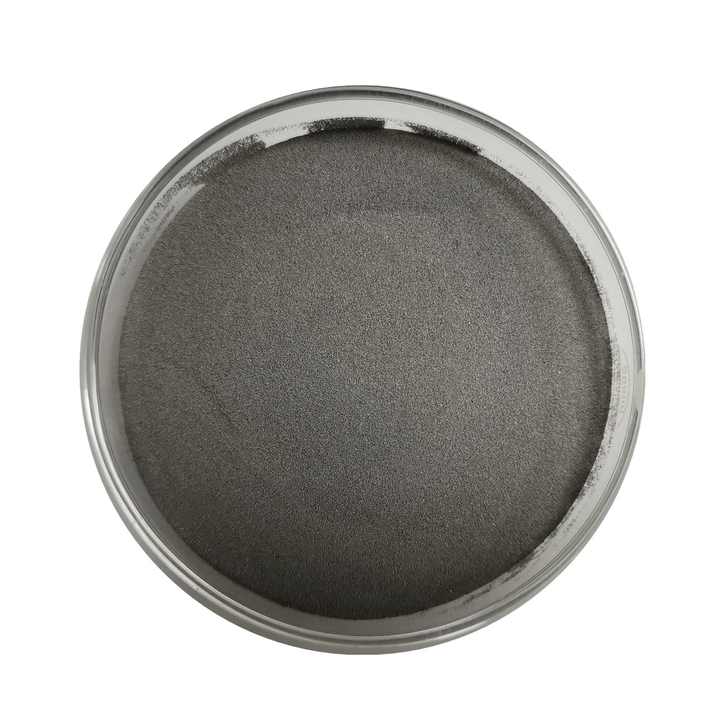
공급업체 및 가격
공급업체 | 장비 | 가격 범위 |
---|---|---|
가스바레 | 가스 분무기 | $50만 - $200만 |
Idra | 물 분무기 | $1 - 500만 |
케세니치 | 회전 전극 | $25만 - $100만 |
Sodick | 초음파 노즐 | $100,000 – $500,000 |
AcuPowder | 원심 휠 | $50,000 – $250,000 |
원자화된 금속 장비 가격은 용량, 자동화 기능, 보조 시스템, 브랜드 평판 및 기타 요인에 따라 크게 달라집니다. 산업 규모의 생산 장치에는 최소 $25만~$100만 달러의 예산이 필요합니다.
설치 및 시설
- 원자화된 금속 장비는 통풍이 잘되고 온도와 습도가 제어되는 생산 공간에 설치해야 합니다.
- 장비 설치 및 유지보수를 위한 충분한 오버헤드 크레인, 호이스트 및 리깅 장비를 제공합니다.
- 전원 공급 장치, 유틸리티 및 압축 공기 연결이 제대로 되어 있는지 확인합니다.
- 장비 조립, 정렬, 테스트 및 커미셔닝을 위한 자격을 갖춘 인력을 확보하세요.
- 안전한 설치를 위해 적절한 기초, 앵커 볼트, 장비 플랫폼을 설계하세요.
- 집진 덕트, 사이클론 및 분무형 금속 분말을 수집하기 위한 백하우스를 포함합니다.
- 가스 모니터링 센서, 화재 진압 시스템과 같은 안전 기능을 설치하세요.
- 자재 취급, 워크플로 및 유지보수 액세스를 위한 충분한 여유 공간을 확보하세요.
운영 및 유지 관리
활동 | 세부 정보 | 빈도 |
---|---|---|
장비 검사 | 유체 레벨, 누수, 비정상적인 소음/진동, 안전 장치 점검 | 매일 |
매개변수 모니터링 | 온도, 압력, 유량, 전력과 같은 프로세스 데이터 기록 | 연속 |
소모품 보충 | 냉각수, 불활성 가스 실린더, 윤활유 리필 | 필요에 따라 |
하우스키핑 | 유출물 청소, 빈 집진기 청소, 일반 청소 | 매일 |
구성 요소 교체 | 마모된 노즐, 베어링, 씰, 필터 교체 | 일정별 |
캘리브레이션 | 센서, 측정 장치, 제어 시스템 교정 | 분기별 |
주요 유지 관리 | 주요 부품 점검, 필요한 경우 수리/교체 | 매년 |
제조업체 지침에 따른 적절한 작동 및 예방적 유지보수는 장비 수명과 성능을 극대화하는 데 있어 핵심입니다. 모든 유지보수 작업에 대한 상세한 로그를 유지하세요.
원자화된 금속 장비 공급업체 선택
고려 사항 | 세부 정보 |
---|---|
기술 전문성 | 분무 기술 및 금속 분말 생산에 대한 오랜 경험 |
사용자 지정 | 특정 생산 요구 사항에 맞게 장비를 맞춤화할 수 있는 기능 |
신뢰성 | 고장률이 낮은 견고하고 신뢰할 수 있는 장비에 대한 입증된 실적 |
자동화 | 고급 제어 시스템, 최적화된 분말 특성을 위한 데이터 모니터링 |
애프터 서비스 | 설치 지원, 운영자 교육, 유지보수를 위한 서비스 계약 |
참조 | 장비 품질 및 공급업체 평판에 대한 기존 고객의 긍정적인 피드백 |
가치 | 품질, 성능 및 공정한 가격의 적절한 균형 |
로컬 존재감 | 대면 회의 및 빠른 응답을 위한 물리적 근접성 |
원자화된 금속 장비에 투자하기 전에 위의 매개변수에 대해 공급업체를 철저히 평가하세요. 품질, 신뢰성, 최저 비용 대비 서비스 등의 요소를 고려하여 선택해야 합니다.
원자화된 금속 공정의 장단점
가스 분무
장점
- AM, MIM 등에 이상적인 매우 구형의 부드러운 분말을 생산합니다.
- 좁은 입자 크기 분포 가능
- 우수한 생산성으로 지속적인 운영
- 물 분무에 비해 낮은 자본 비용
단점
- 일반적으로 100미크론 미만의 작은 입자 크기로 제한됩니다.
- 대량의 고가의 불활성 가스가 필요함
- 작업 공간의 먼지 수준이 높을 수 있습니다.
물 분무
장점
- 큰 직경을 포함한 다양한 크기의 분말 생산 가능
- 가스 분무보다 낮은 가스 소비량
- 분무된 기체에 비해 밀도가 높은 분말
단점
- 구형 입자는 줄이고, 인공위성은 늘리세요.
- 물 분무에 필요한 수처리
- 물 접촉으로 인한 산화물 포함 가능성
원심 분무
장점
- 최소한의 유틸리티를 갖춘 간단한 메커니즘
- 자본 비용을 절감하는 컴팩트한 디자인
- 우수한 생산성으로 반 연속적으로 운영됩니다.
단점
- 입자 크기 분포에 대한 제한된 제어
- 불규칙하고 구형이 아닌 입자 모양
- 시간이 지남에 따라 디스크 마모로 인한 오염 위험
원자화된 금속 공정의 한계
- 특히 초미세 금속 분말의 경우 높은 생산 비용
- 기술에 따른 파티클 모양 및 크기 범위 제약 조건
- 요구 사항조건이 통제된 특수 장비
- 순수 분말에 필요한 고순도 공급 원료 금속
- 일부 방법의 일괄 작업은 생산성을 저하시킵니다.
- 입자 크기 제어를 위해 종종 체질과 같은 후처리가 필요합니다.
- 장비 운용에 필요한 고도로 숙련된 인력
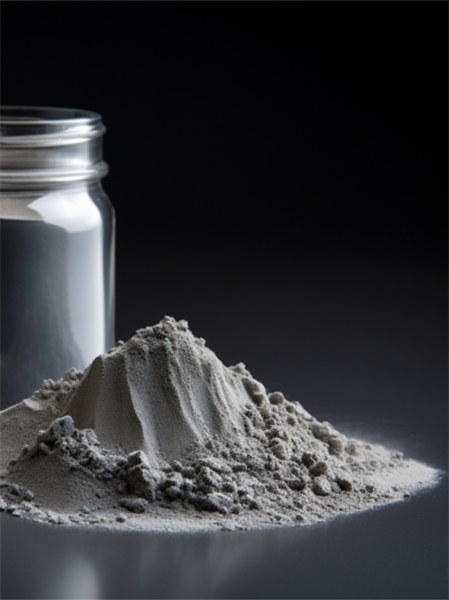
자주 묻는 질문
입자 크기별로 원자화된 금속 분말을 분류하는 데 어떤 방법이 사용되나요?
원자화된 금속 분말을 분류하는 일반적인 방법은 다음과 같습니다:
- 체 - 메쉬 크기가 감소하는 체 스택이 분말을 크기 분획으로 분리합니다.
- 공기 분류 - 원심 분리기 또는 사이클론 분리기는 더 거친 입자에서 미세한 입자를 분류합니다.
- 용출 - 역류 공기/물 유동화를 통해 중력에 의해 미립자가 흘러넘칠 수 있습니다.
- 침전 - 입자가 크기/밀도에 따라 액체에서 아래쪽으로 가라앉습니다.
분무형 금속 분말을 취급할 때 어떤 안전 예방 조치가 필요하나요?
분무형 분말을 취급할 때의 주요 안전 수칙:
- 피부/눈 접촉 및 흡입을 방지하기 위해 장갑, 눈 보호구, 필터 마스크 등 개인보호장비 사용
- 분말 산화 및 먼지 폭발을 방지하는 불활성 가스 퍼징
- 정전기를 방출하기 위한 분말 취급 장비의 적절한 접지
- 분말 가공 구역에서 모든 점화원을 피하십시오.
- 공기 중 분말 포집을 위한 집진 장비 설치
- 공기 모니터링을 수행하여 가연성 먼지 수준 확인
원자화된 금속 분말은 어떻게 취급 및 운송되나요?
일반적인 분말 처리 단계:
- 사이클론 분리기 또는 백 하우스 필터 아래의 드럼에 수집됩니다.
- 산소 접촉을 방지하기 위해 밀폐된 용기에 넣어 운송합니다.
- 파이프라인을 통해 질소 또는 아르곤을 통한 공압 이송
- 분말 저장 용기로의 진공 흡입 이송
- 소량 배치를 위한 수동 퍼내기/삽질 작업
- 대량 물량을 위한 자동 기계 컨베이어
파우더는 오염을 방지하기 위해 사용 준비가 될 때까지 밀봉된 상태로 보관됩니다.
원자화된 금속 분말을 생산하는 동안 오염을 방지하기 위해 어떤 조치를 취하나요?
- 고순도 원료 및 공급 원료 사용
- 아르곤/질소를 사용하여 불활성 대기 유지
- 밀봉을 통해 산소와 습기 차단
- 파우더와 고철의 접촉 방지
- 파우더와 접촉하는 장비의 잦은 청소
- 솔벤트를 사용하여 오일 및 그리스 잔여물 제거하기
- 불규칙한 입자를 분리하기 위한 체질/분류
- 불순물 소스 식별 및 제거를 위한 분석
분무를 통해 생산되는 스테인리스강 분말의 가장 일반적인 응용 분야는 무엇입니까?
분무형 스테인리스강 분말의 일반적인 응용 분야:
- 적층 제조 - 선택적 레이저 용융, 바인더 분사
- 작고 복잡한 부품의 금속 사출 성형
- 접합용 브레이징 페이스트 및 납땜 필러
- 다공성 필터로 압착하는 분말 야금 기술
- 자체 윤활 베어링 제조
- 섬유용 스테인리스 스틸 섬유 생산
- 전기 화학 가공/방전 가공 전극
- 스테인리스 스틸 분말 도료 및 코팅 제조
가스 분무용 불활성 가스 공급 시스템을 선택하는 방법은 무엇입니까?
불활성 가스 공급에 대한 고려 사항:
- 티타늄과 같은 반응성 금속에는 질소보다 아르곤이 선호됩니다.
- 백업 실린더가 있는 대용량 가스 저장 탱크
- 99.99%+의 순도 수준으로 오염 방지
- 가스 제어용 압력 레귤레이터 및 유량계
- 가스 회수 시스템 사용으로 폐기물 최소화
- 습기 동결 방지를 위한 가열 가스 라인
- 가스 매개변수의 자동 전환 및 모니터링
- 가스 안전을 위한 적절한 경보 및 인터록
원자화된 금속 분말 특성 최적화
원자화된 금속 분말의 특성은 공정 파라미터와 원자화 조건을 제어하여 최적화할 수 있습니다:
입자 크기 분포
방법 | 효과 |
---|---|
용융 금속 유량 증가 | 더 큰 평균 입자 크기 |
더 빠른 분무기 회전 속도 사용 | 미세 분말 비율 증가 |
용융 금속 주입 온도 감소 | 더 촘촘한 입자 크기 분포 |
체질/공기 분리를 통한 분말 분류 | 큰 크기 및 작은 크기의 분수 제거 |
파티클 모양
방법 | 효과 |
---|---|
가스 또는 물 분무 사용 | 더 많은 구형 입자 |
금속 주입 속도 감소 | 더 많은 구형 입자 |
용융 과열 온도 증가 | 새틀라이트 및 불규칙한 모양 감소 |
분무 후 분말 어닐링 | 구형 형태 개선 |
분말 순도
방법 | 효과 |
---|---|
고순도 금속 공급 원료 사용 | 금속 불순물 감소 |
슬래그 제거 단계 추가 | 비금속 이물질을 제거합니다. |
불활성 가스 순도 증가 | 기체 불순물 감소 |
니켈 도금 수거 용기 사용 | 아이언 픽업 감소 |
파우더를 체로 쳐서 새틀라이트 제거 | 분말 순도 증가 |
파우더 밀도
방법 | 효과 |
---|---|
원자화 매개변수 최적화 | 균일한 고밀도 파우더 |
분무 후 어닐 파우더 | 내부 공극과 모공 제거 |
분무 후 분말 압축 | 파우더를 단단하게 굳히고 통합하는 작업 |
열 기계 처리 | 파우더 미세 구조 개선 |
분무 공정과 분말 처리 단계를 최적화하여 분무된 금속 분말의 특성을 응용 분야 요구 사항에 맞게 조정할 수 있습니다.
원자화된 금속 분말 생산의 새로운 트렌드
분무 분말 생산 기술의 주요 최신 트렌드는 다음과 같습니다:
- 적층 제조는 30미크론 이하의 구형 초미세 분말에 대한 수요를 증가시키고 있습니다. 새로운 노즐과 원자화 방법을 통해 이러한 분말을 생산할 수 있습니다.
- 인더스트리 4.0 개념을 사용한 분말 생산 자동화를 통해 원격 모니터링, 제어 및 데이터 기반 제조가 가능합니다.
- 가스, 물, 원심 분무의 장점을 결합한 하이브리드 분무 기술을 통해 입자 제어를 개선합니다.
- 용융 금속의 마이크로파 보조 가열을 통해 분무화 전에 더 빠르고 균일하게 가열합니다.
- 물방울 형성 역학 시뮬레이션 및 모델링을 통해 원자화 물리학에 대한 이해를 높일 수 있습니다.
- 적층 제조 애플리케이션에 특별히 맞춤화된 새로운 합금 개발.
- 체질, 분류 및 보관이 통합된 개선된 분말 처리 시스템.
- 배치 방식이 아닌 연속 분말 생산 공정을 통해 처리량을 높입니다.
- 원자화 프로세스의 자동 최적화를 위해 AI 및 머신러닝 알고리즘을 사용하는 고급 제어 시스템.
- 티타늄 및 알루미늄 합금과 같은 반응성 금속에 최적화된 특수 가스 분무 노즐입니다.
- 열처리를 통해 AM 공정에서 발생하는 고철 분말을 재활용 및 재사용합니다.
- 더 나은 분말 품질 관리를 위한 적외선 이미지와 같은 공정 중 모니터링 기술.
결론
원자화된 금속 분말은 자동차, 항공우주, 의료, 3D 프린팅 및 기타 주요 산업 전반에 걸쳐 중요한 응용 분야를 가능하게 합니다. 고품질 분말에 대한 수요가 증가함에 따라 금속 분무 기술은 공정 강화, 자동화, 합금 개발 및 고급 특성화 기술의 새로운 혁신을 통해 계속 발전하고 있습니다. 분말 생산업체는 최신 기술을 도입하여 민첩하고 비용 효율적이며 지속 가능한 방식으로 분말을 제조할 수 있습니다.