개요 MIM 제조
금속 사출 성형(MIM)은 작고 복잡한 금속 부품을 대량으로 생산하는 데 사용되는 분말 야금 제조 공정입니다.
MIM의 주요 단계는 다음과 같습니다:
- 미세 금속 분말과 바인더를 혼합하여 공급원료 만들기
- 플라스틱 사출 성형을 사용하여 금형에 원료 주입하기
- 금속 가루만 남기고 바인더를 제거하기 위한 디 바인딩
- 소결을 통해 분말을 고체 금속 성분으로 밀도화합니다.
MIM은 플라스틱 사출 성형의 설계 유연성과 가공 금속의 강도 및 성능을 결합한 공정입니다. 소형 부품의 복잡한 대량 생산을 위한 비용 효율적인 공정입니다.
MIM 제조의 작동 방식
MIM 제조 프로세스에는 다음이 포함됩니다:
- 미세 금속 분말을 폴리머 바인더와 혼합 및 펠릿화하여 공급 원료 제조
- 원료를 가열하여 원하는 모양으로 사출 성형하기
- 용매 또는 열 디바인딩을 통해 바인더를 화학적으로 제거합니다.
- 디바운드 금속 부품을 용광로에서 소결하여 완전 밀도 부품을 생산합니다.
- 가공, 드릴링, 도금과 같은 2차 마감 작업(옵션)
MIM을 사용하면 복잡한 형상, 엄격한 공차, 우수한 기계적 특성을 가진 부품을 경제적으로 생산할 수 있습니다.
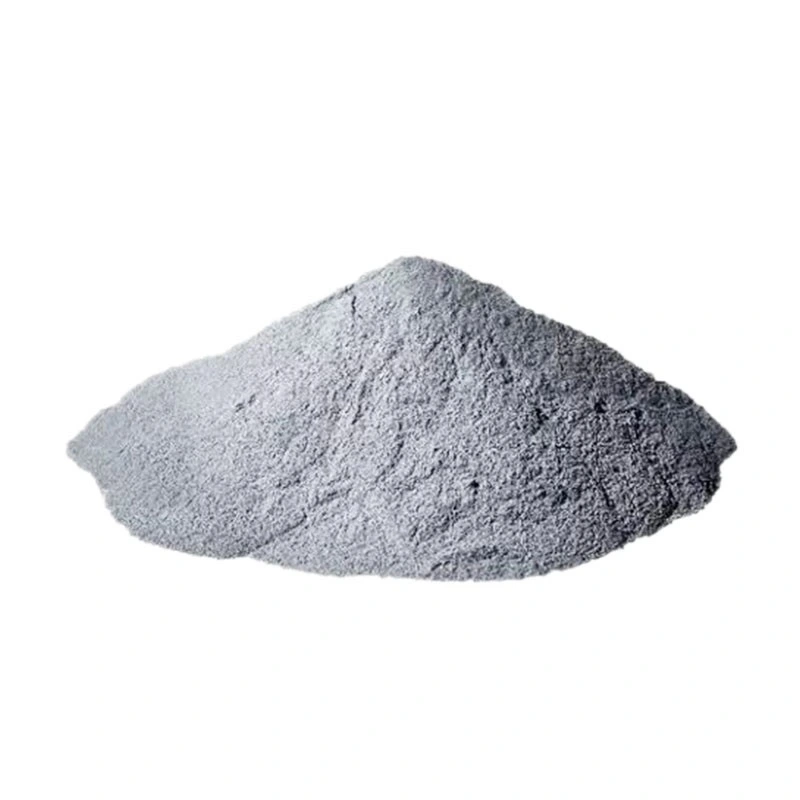
MIM에 사용되는 금속의 종류
MIM 기술로 다양한 금속을 가공할 수 있습니다:
- 스테인리스강 - 316L, 17-4PH, 410, 420
- 공구강 - H13, P20, A2, D2
- 자성 합금 - 소프트 및 하드 페라이트
- 구리 합금 - 황동, 청동
- 저합금강 - 4100, 4600
- 초합금 - 인코넬 625, 718
- 텅스텐 중합금
- 티타늄 합금 - Ti6Al4V, Ti6Al4V ELI
MIM은 일반적으로 고밀도로 소결할 수 있는 모든 재료에 적합합니다. 녹는점이 1000°C 미만인 금속이 선호됩니다.
MIM 제조 공정 파라미터
MIM의 중요한 프로세스 매개변수에는 다음이 포함됩니다:
피드스톡 개발:
- 분말 형태, 크기 분포
- 바인더 구성
- 파우더 로딩 - 일반적으로 60-65 vol%
- 혼합 프로세스 - 온도, 시간, 분위기
몰딩:
- 금형 재료 - P20 공구강 선호
- 사출 온도, 압력, 속도
- 게이트 디자인
- 냉각 시스템 설계
디바인딩:
- 용매, 열 또는 촉매 디바인딩
- 디바인딩 온도, 시간, 대기
소결:
- 온도 프로파일 - 디바인딩, 소결 단계
- 가열 속도, 소결 시간, 분위기
- 소결 온도 및 압력
MIM 설계 및 부품 고려 사항
MIM 프로세스를 사용하면 자유롭게 설계할 수 있지만 몇 가지 지침을 따라야 합니다:
- 벽 두께: 0.3~4mm 범위 가능
- 표면 마감: 소결 상태: Ra 1.5μm 내외
- 치수 허용 오차: ±0.5%가 표준이지만 ±0.1% 달성 가능
- 갇힌 가루 방지: 완전히 밀폐된 내부 공간 없음
- 구배 각도: > 1° 구배 각도 선호
- 소결 수축: 약 20%의 체적 수축
- 결함 감소: 넉넉한 코너 반경으로 균열 최소화
고급 시뮬레이션 툴을 사용하면 설계 중에 MIM 프로세스를 가상으로 최적화하여 시행착오를 줄일 수 있습니다.
장점 MIM 제조
MIM 활용의 주요 이점은 다음과 같습니다:
- 복잡한 형상과 엄격한 허용 오차
- 우수한 기계적 성질
- 다양한 소재 옵션
- 저렴한 비용으로 대량 생산
- 낭비 최소화 - 그물 모양에 가까운 공정
- 가공 및 마감 작업 감소
- 구성 요소 통합 및 부품 통합
- 소등 작업에 적합한 자동화 프로세스
- 기계 가공보다 환경 친화적
- 프로토타입에서 전체 생산까지 확장 가능
이러한 장점 덕분에 MIM은 산업 전반에 걸쳐 정밀 금속 부품을 대량으로 비용 효율적으로 제조하는 데 적합합니다.
MIM의 한계와 과제
MIM과 관련된 몇 가지 제한 사항:
- 제한된 크기 - 일반적으로 부품당 완제품 질량 45g 미만
- 고밀도로 소결할 수 있는 금속으로 제한됩니다.
- 원료 배합에 필요한 광범위한 전문성
- 금형 및 프로세스 개발을 위한 초기 비용
- 균열이 생기기 쉬운 직선 부분과 날카로운 모서리
- 다른 프로세스에 비해 더 긴 리드 타임
- 최종 속성을 얻기 위해 종종 필요한 포스트 프로세싱
- 스레드와 같은 일부 기능의 디자인 자유도 부족
- 소결 금속의 2차 가공은 까다로울 수 있습니다.
애플리케이션에 맞는 적절한 공급 원료와 공정 설계를 통해 이러한 문제를 극복하고 MIM 기술의 잠재력을 최대한 활용할 수 있습니다.
MIM 제조 부품의 응용 분야
MIM은 다음 분야에서 광범위하게 사용되고 있습니다:
자동차: 잠금 하드웨어, 센서, 연료 시스템 및 엔진 부품
항공우주: 임펠러, 노즐, 밸브, 패스너
의료: 치과 임플란트, 메스 손잡이, 정형외과 기구
총기류: 방아쇠, 매거진, 슬라이드, 망치
시계: 케이스, 팔찌 링크, 걸쇠 및 버클
전기: 신뢰성을 위한 커넥터 및 리드프레임
일반적인 부품 크기는 0.1그램에서 110그램까지 다양하며 커넥터, 패스너, 수술용 기구, 교정기 등 상업적 생산량이 가장 많은 제품군에서 사용됩니다.
MIM 제조 비용 분석
MIM 제조 비용에는 다음이 포함됩니다:
- 피드스톡 개발 - 제형, 혼합, 특성화
- 금형 제작 - 고정밀 금형 가공
- MIM 머신 - 대규모 설비 투자
- 운영 - 인건비, 유틸리티, 소모품
- 보조 작업 - 디바인딩, 소결, 마감
- 자료 활용 - 금속 분말은 총 비용의 약 60%를 차지합니다.
- 소모품 툴링 - 여러 개의 몰드 캐비티로 대량 생산 가능
- 생산량 - 총 볼륨에 걸쳐 상각되는 설치 비용
- 구매 대 비행 비율 - 다른 PM 프로세스에 비해 2~4배에 불과
- 디자인 최적화 - 최소한의 가공으로 간단한 형상
대량 생산의 경우, MIM은 뛰어난 재료 활용도와 그물 모양에 가까운 기능으로 높은 제조 속도와 매우 유리한 비용을 제공합니다.
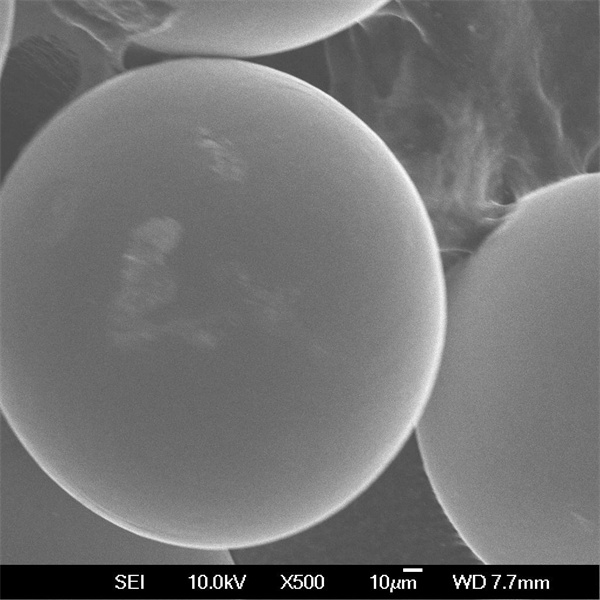
선택 MIM 제조 파트너
MIM 공급업체를 선택할 때 고려해야 할 주요 요소:
- MIM에 대한 전문성과 다년간의 경험 입증
- 소재 포트폴리오 - 다양한 스테인리스 스틸, 공구강, 초합금 옵션
- 품질 인증 - ISO 9001, ISO 13485가 바람직합니다.
- 2차 가공 기능 - 가공, 열처리, 표면 처리
- 엄격한 프로세스 및 제품 품질 관리 절차
- 원료 배합 및 공정 개발을 위한 R&D 역량
- 금형 흐름 시뮬레이션 및 기타 설계 분석 전문성
- 고객 프로젝트를 지원하는 프로그램 관리 기술
- 생산 요구에 따라 확장 가능한 용량 확장성
- 다년 계약을 통한 경쟁력 있는 가격 책정
- 긴밀한 협업과 IP 보호를 가능하게 하는 위치
MIM에 중점을 두고 틈새 시장을 공략하는 기존 MIM 생산업체를 선택하면 일반 CNC 금속 가공업체와 달리 최상의 결과를 얻을 수 있습니다.
MIM과 CNC 가공의 장단점
MIM의 장점:
- 뛰어난 치수 정확도 및 반복성
- 가공을 통해 얻을 수 없는 복잡한 형상
- 재료 낭비를 최소화한 그물 모양에 가까운 형태
- 매우 많은 생산량으로 효율적으로 확장 가능
- 자동화된 프로세스로 연중무휴 24시간 운영 가능
- 설정 후 리드 타임 단축
- 대량 생산 시 부품 비용 대폭 절감
- 가공된 금속과 일치하거나 그 이상의 속성
MIM의 단점:
- 공급 원료 및 금형에 대한 높은 초기 설정 비용
- 제한된 크기 기능
- 일부 기능의 디자인 자유도 제한
- 비효율적인 초기 생산량 감소
- 원료 배합에 필요한 광범위한 전문성
- 2차 마무리 작업이 여전히 필요할 수 있습니다.
- 초기 프로토타입의 경우 리드 타임이 길어지고 품질이 저하됩니다.
대량으로 생산되는 복잡한 소형 금속 부품의 경우 MIM이 가장 시간과 비용 효율적인 제조 방법이 될 수 있습니다.
MIM과 금속 3D 프린팅의 비교
MIM과 3D 프린팅의 주요 차이점:
매개변수 | MIM | 3D 프린팅 |
---|---|---|
프로세스 | 바인더 사출 성형 + 소결 | 파우더 베드 융합 또는 바인딩 |
재료 | 다양한 합금 | 제한된 재료 옵션 |
부품 크기 | < 45g 미만 | 최대 수 kg |
정확도 | 우수, ±0.5% | 보통, ±1% |
표면 마감 | 매우 좋음 | 보통에서 나쁨 |
생산 규모 | 10,000명에서 수백만 명 | 중간 규모의 프로토타입 제작 |
부품당 비용 | 매우 낮은 | 중간에서 높음 |
보조 마무리 | 필요할 수 있습니다. | 일반적으로 필수 |
리드 타임 | 프로세스 개발 기간 연장 | 더 빠른 프로토타입 제작, 더 느린 연속 생산 |
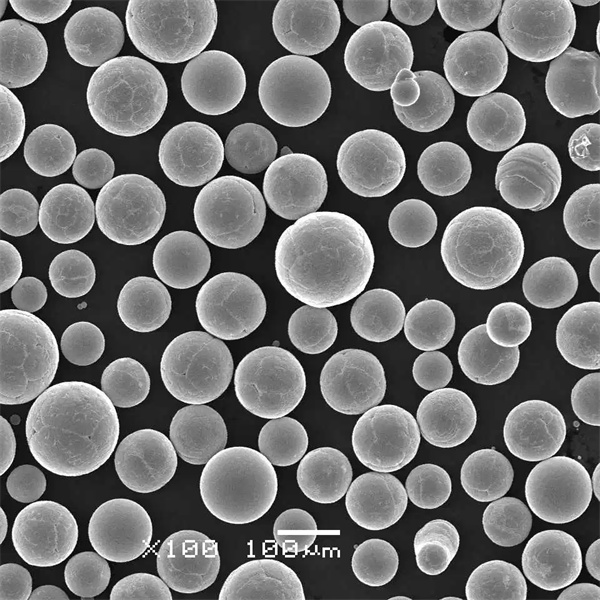
자주 묻는 질문
MIM 제조의 일반적인 허용 오차 범위는 어떻게 되나요?
MIM은 소형 정밀 부품에 대해 ±0.1%의 공차가 가능한 고급 공정을 통해 ±0.5%의 치수 공차를 안정적으로 달성할 수 있습니다.
일반적인 MIM 공급 원료 구성은 무엇인가요?
일반적인 MIM 공급 원료는 폴리프로필렌, 폴리에틸렌, 폴리스티렌과 같은 폴리머로 구성된 35-40% 바인더와 60-65% 금속 분말 로딩으로 구성됩니다. 왁스는 파우더 흐름을 개선하는 데 도움이 됩니다.
MIM으로 여러 재료로 부품을 제조할 수 있나요?
예, MIM은 각 금형 캐비티에 서로 다른 공급 원료를 사출 성형하거나 융점이 다른 바인더를 사용하여 복합 및 등급 구조물을 생산할 수 있습니다.
MIM으로 어떤 성형 부품 크기를 구현할 수 있나요?
MIM 몰딩은 일반적으로 질량이 45g 미만이고 치수가 50mm 미만인 부품으로 제한됩니다. 더 크거나 무거운 부품은 충분히 채우고 밀도를 높이기가 어렵습니다.
MIM은 소형 금속 부품의 다이캐스팅과 어떻게 다릅니까?
MIM은 더 높은 치수 정확도와 재료 강도를 제공하지만 다이캐스팅은 사이클 시간이 더 빠릅니다. MIM은 복잡한 형상에 더 적합하지만 다이캐스팅은 단순한 형태에 더 적합합니다.