분말 분무 용융 금속에서 미세한 분말을 생산하는 데 사용되는 기계적 공정입니다. 용융 금속 스트림을 미세한 물방울로 분해하여 분말 입자로 응고시킵니다. 분무는 입자 크기 분포가 제어된 구형 금속 분말을 생산합니다. 이 개요에서는 분말 분무 장비의 주요 측면을 살펴봅니다.
분말 분무 장비 유형
산업용 분말 생산에 사용되는 분무 장비에는 몇 가지 주요 유형이 있습니다:
장비 | 설명 |
---|---|
가스 분무 | 고압 불활성 가스 제트에 의해 분무되는 용융 금속 스트림 |
물 분무 | 고압 워터 제트에 의해 분해된 용융 금속 흐름 |
원심 분무 | 용융 금속이 회전 디스크의 가장자리에 쏟아지거나 떨어져 나감 |
초음파 분무 | 용융 스트림에 고주파 진동 적용 |
플라즈마 분무 | 플라즈마 아크가 금속을 녹여 미세한 물방울로 분무합니다. |
가스 분무와 물 분무는 가장 일반적인 산업 방식입니다. 원심분무, 초음파 및 플라즈마 분무는 보다 전문적인 용도로 사용됩니다. 선택은 분무되는 재료, 필요한 분말 사양, 생산 속도 및 비용과 같은 요인에 따라 달라집니다.
분무 프로세스 특성
다양한 방법을 사용하는 분말 분무 공정의 주요 특징:
특성 | 일반적인 범위 |
---|---|
가스 압력 | 2-8 MPa |
수압 | 10-150 MPa |
가스 유량 | 0.5-3 m3/min/mm2 |
디스크 직경 | 100-1000 mm |
디스크 속도 | 10000-50000 rpm |
빈도 | 20-60kHz |
플라즈마 파워 | 30-80kW |
가스 및 수압이 높을수록 더 미세한 분말 입자가 생성됩니다. 더 빠른 디스크 속도와 더 높은 주파수는 또한 더 미세한 분말을 생성합니다. 이 범위는 강철, 알루미늄, 구리 합금과 같은 일반적인 금속에 대한 산업 관행을 반영합니다.
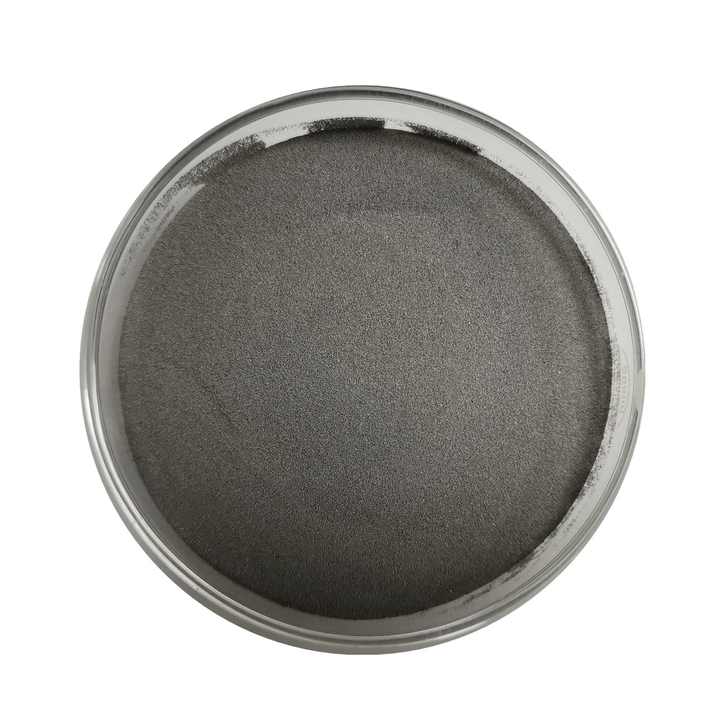
분말 입자 크기 제어
입자 크기 분포는 원자화된 분말의 중요한 품질 지표입니다. 분말 입자 크기를 제어하는 주요 요인은 다음과 같습니다:
- 유체 압력 분무 - 높은 압력으로 더 미세한 입자 생성
- 분무 유체 유량 - 유량이 높을수록 입자가 더 미세해집니다.
- 용융 금속 유량 - 금속 유량이 낮을수록 더 미세한 분말 생성
- 분무 노즐 설계 - 노즐 형상이 액적 크기에 영향을 미침
- 디스크/노즐 상대 속도 - 빠른 상대 운동으로 더 작은 물방울을 만듭니다.
- 재료 특성 - 점도, 표면 장력이 조각화에 영향을 미침
이러한 파라미터를 신중하게 제어하면 목표 입자 크기 분포를 가진 분말을 생산할 수 있습니다. 예를 들어, D50이 10~100미크론인 가스 분무 강철 분말을 예로 들 수 있습니다.
원자화된 금속 분말의 응용 분야
분무 분말은 다양한 산업과 애플리케이션에서 사용됩니다:
산업 | 애플리케이션 |
---|---|
분말 야금 | 프레스 및 소결 부품, MIM 공급 원료 |
금속 적층 제조 | 바인더 제트 인쇄, DED 공급 원료 |
용사 코팅 | 와이어 아크, 플라즈마, 화염 스프레이 코팅 |
용접 | 플럭스 코어 아크 용접 필러 |
브레이징 | 브레이즈 페이스트 및 프리폼 |
전자 제품 | 전도성 페이스트 및 잉크 |
자동차 | 마찰 재료, 분말 단조 |
구형 분무 분말은 다양한 분말 가공 방법에 필요한 뛰어난 유동성과 혼합성을 제공합니다. 분말 크기 분포를 엄격하게 제어하여 성능을 최적화합니다.
분말 분무 시스템 설계
분무 시스템 설계의 핵심 요소는 다음과 같습니다:
- 금속 배송 - 툰디쉬, 붓는 통, 인덕션 가이드 또는 회전 전극
- 분무기 - 노즐 디자인, 노즐 개수, 노즐 배치
- 분무 매체 - 가스 제어 매니폴드, 워터 펌프 및 배관
- 파우더 수집 - 사이클론 분리기, 백 하우스 필터, 스크러버
- 시스템 제어 - 압력, 온도, 유량 센서 및 제어 루프
추가적으로 고려해야 할 사항은 격리, 안전 인터록, 분말 취급 및 보관입니다. 대부분의 금속 합금을 생산하도록 시스템을 맞춤 설계할 수 있습니다.
분무 장비 사양
산업용 가스 및 물 분무 시스템의 일반적인 사양입니다:
매개변수 | 일반적인 범위 |
---|---|
생산 능력 | 10-5000kg/h |
가스 압력 분무 | 2-8 MPa |
가스 흐름 분무 | 0.5-3 Nm3/mm2 |
수압 | 10-150 MPa |
노즐 크기 | 2-8mm ID |
노즐 유형 | 직선 보어, 수렴-발산 |
사이클론 효율성 | >95%(10μm 기준) |
백하우스 효율성 | 1μm에서 >99.9% |
용량, 압력 및 노즐 세부 사항은 합금, 원하는 입자 크기 및 생산 속도에 따라 달라집니다. 시스템은 특정 용도에 맞게 맞춤 설계됩니다.
설치 및 운영
분말 분무 장비 설치 및 운영 시 중요 고려사항:
- 동적 장비를 위한 적절한 기초 및 지지대
- 구조물로의 전달을 최소화하는 진동 차단 장치
- 가스, 수도, 전기 시스템에 대한 강력한 연동 기능
- 프로세스 변수에 대한 모니터링 및 제어 계측 장비
- 작업 구역의 오버 스프레이 및 먼지 차단
- 흄 및 먼지 추출 장비 작동
- 용융 금속 취급 및 스프레이에 대한 안전 프로토콜
- 가스/수도 시스템 교정 및 유지보수
- 축적을 방지하기 위한 종료 및 정리 절차
스타트업은 신중하게 개발된 절차를 따라야 합니다. 시스템을 안전하게 운영하고 유지하려면 직원 교육이 중요합니다.
유지 관리 요구 사항
최적의 가동 시간과 파우더 품질을 위해서는 정기적인 유지 관리가 필요합니다:
- 분무 노즐 점검 - 마모되거나 손상된 노즐 교체
- 원심 분무기의 스핀 플레이트 점검 - 표면을 다시 닦거나 교체하세요.
- 분말 수집 사이클론 및 백 하우스 필터 청소
- 압력, 유량 및 온도 센서의 보정 확인
- 비상정지 밸브 및 인터록 작동 확인
- 분무 가스 순도 모니터링 - 습기로 인해 산화가 발생할 수 있음
- 금속이 쌓이지 않도록 피드 라인과 턴디쉬를 청소하세요.
- 스핀 드라이브 모터 및 베어링 윤활 및 점검
운영 시간 및 중요도에 따라 유지보수 일정과 절차를 수립하세요.
분무 장비 공급업체 선택
분무 시스템 공급업체 선정의 핵심 요소:
- 특정 합금의 원자화 경험
- 전체 시스템을 엔지니어링할 수 있는 역량
- 다양한 노즐 디자인 및 분무기 구성 가능
- 용량 및 입자 크기 요구 사항을 충족하는 유연성
- 설치, 교육 및 애프터서비스 지원 제공
- 타겟 시장의 현지 입지 또는 파트너십
- 관련 규정 및 표준 준수
- 유사한 프로젝트에 대한 참조 및 사례 연구
- 가격 및 배송 일정
장비 비용뿐 아니라 기술 전문성을 기준으로 공급업체를 평가하세요. 경험이 풍부한 파트너가 성공을 보장합니다.
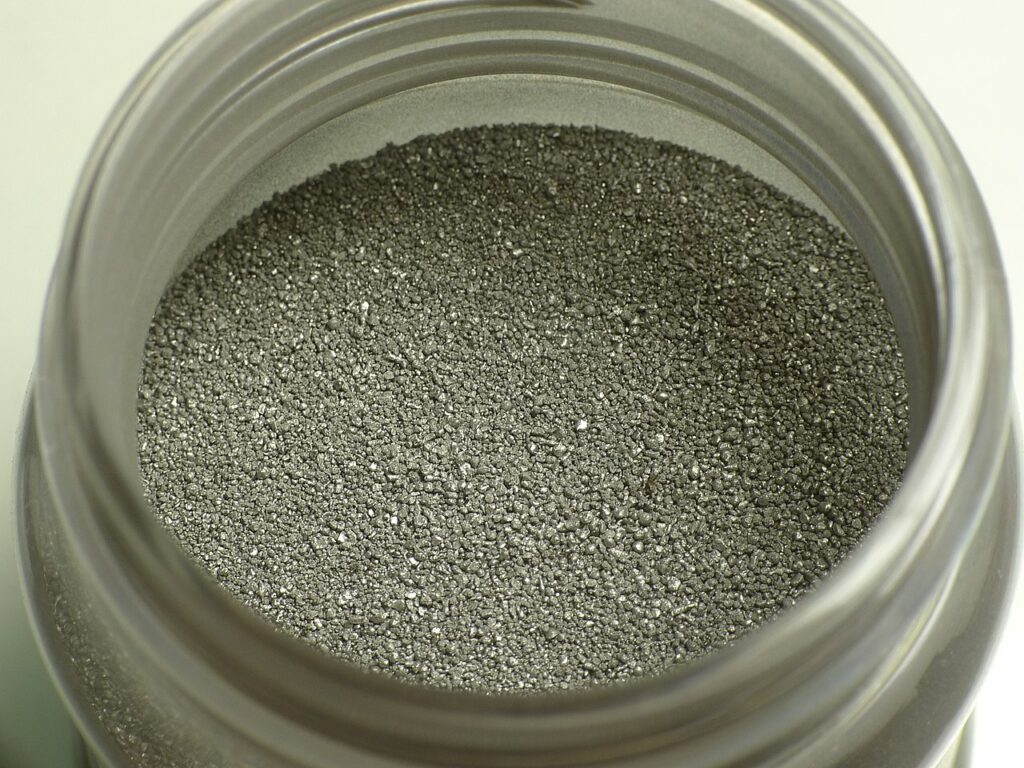
분무 시스템의 비용 분석
분무 장비는 자본 비용이 높지만 경쟁력 있는 가격으로 분말을 생산할 수 있습니다:
시스템 | 자본 비용 범위 | 파우더 가격 범위 |
---|---|---|
가스 분무 | $500,000 – $5,000,000 | $5-50/kg |
물 분무 | $200,000 – $2,000,000 | $2-20/kg |
원심 분무 | $50,000 – $500,000 | $10-100/kg |
초음파 분무 | $100,000 – $1,000,000 | $50-500/kg |
플라즈마 분무 | $200,000 – $2,000,000 | $20-200/kg |
용량, 구성 재료, 제어에 따라 비용이 결정됩니다. 미세 분말은 프리미엄 가격이 책정됩니다. 자본 투자를 정당화하기 위해 많은 생산량이 필요합니다.
분말 분무 방법의 장단점
다양한 분무 기술의 장점과 한계를 비교합니다:
방법 | 장점 | 단점 |
---|---|---|
가스 분무 | 가장 좁은 입자 분포, 불활성 대기 | 높은 자본 비용, 높은 가스 소비량 |
물 분무 | 낮은 장비 비용, 작은 입자 크기 | 산화 가능, 건조 필요 |
원심 분무 | 심플한 디자인, 손쉬운 확장 | 광범위한 입자 분포, 불규칙한 모양 |
초음파 분무 | 수액 필요 없음, 유지보수 비용 절감 | 제한된 합금 및 생산 속도 |
플라즈마 분무 | 순수 금속의 매우 미세한 입자 | 높은 에너지 사용량, 낮은 파우더 출력 |
입자 크기, 대기, 비용, 합금 호환성 등의 우선순위에 따라 방법을 선택합니다. 모든 시나리오에 가장 적합한 단일 옵션은 없습니다.
분말 분무 기술에 대한 주요 시사점
- 용융 합금에서 미세 금속 분말을 생산하기 위한 다양한 장비 옵션
- 가스 및 물 분무가 가장 일반적이며 특수 기술 사용 가능
- 유체 및 금속 흐름 역학 제어로 최종 입자 크기 결정
- 입자 분포가 최적화된 구형 분말로 고급 응용 분야 지원
- 상당한 자본 투자가 필요하지만 파우더 가격 책정으로 지원 가능
- 성공적인 원자화 프로젝트를 위해서는 경험이 풍부한 공급업체와의 파트너십이 중요합니다.
세심한 공정 개발과 엔지니어링을 통해 애플리케이션 요구 사항에 맞는 특성을 가진 파우더를 생산합니다.
분말 분무 장비 FAQ
Q: 분말로 분무할 수 있는 금속과 합금에는 어떤 것이 있나요?
A: 대부분의 표준 강철, 알루미늄 합금, 구리 합금, 니켈 초합금은 원자화할 수 있습니다. 텅스텐과 탄탈륨과 같은 내화성 금속도 가능합니다. 제한 사항은 융점, 반응성 및 점도와 관련이 있습니다.
Q: 일반적인 가스 분무 압력 및 유량은 얼마인가요?
A: 가스 압력 범위는 공기 또는 질소 및 아르곤과 같은 불활성 가스의 경우 2~8MPa입니다. 유량은 압력 및 입자 크기 목표에 따라 노즐 개방 영역의 0.5~3Nm3/min/mm2에서 다양합니다.
Q: 원자화를 통해 입자를 얼마나 작게 만들 수 있나요?
A: 가스 및 물 분무는 5~10마이크론 이하의 분말을 생성할 수 있습니다. 초음파나 플라즈마와 같은 특수 기술을 사용하면 미크론 이하의 입자를 생성할 수 있습니다. 크기가 작을수록 생산 속도가 훨씬 느립니다.
질문: 입자 크기 분포는 얼마나 일관성이 있나요?
A: 잘 설계된 분무 시스템은 일반적인 입자 크기 분포에서 5-10%의 CV를 달성할 수 있습니다. 더 엄격한 분포도 가능하지만 광범위한 공정 개발 및 제어가 필요합니다.
Q: 원심 분무 공정에서 생산할 수 있는 분말의 양은 얼마입니까?
A: 원심 분무기는 상대적으로 컴팩트하고 비용이 저렴합니다. 생산 용량은 10~100kg/h로 소량의 특수 합금에 적합합니다.
Q: 분무 시스템의 자본 비용은 어떻게 결정되나요?
A: 주요 요소는 처리되는 합금, 입자 크기 및 분포 목표, 생산 속도, 제어 및 구성 재료입니다. 500kg/h 가스 분무 시스템의 비용은 약 $1~2백만입니다.
Q: 분말 분무 시 어떤 안전 예방 조치가 필요하나요?
A: 뜨거운 금속과 분무 분말을 취급할 때는 적절한 개인 보호 장비를 착용하는 것이 중요합니다. 과다 분무 방지, 적절한 환기, 가스 및 먼지 모니터링 장비, 비상 정지 회로가 위험을 완화하는 데 도움이 됩니다.
Q: 분무 장비에는 어떤 유지 관리가 필요하나요?
A: 노즐, 스핀 플레이트, 집진 사이클론은 시간이 지남에 따라 마모되므로 교체해야 합니다. 호스, 밸브, 센서, 펌프는 정기적으로 서비스를 받아야 합니다. 적절한 시작과 종료는 축적을 방지합니다. 직원들에게 프로토콜을 교육하는 것은 매우 중요합니다.
Q: 분무 후 분말 취급 및 보관은 어떻게 관리되나요?
A: 파우더는 노출과 산화를 제한하기 위해 수집기에서 밀폐된 용기로 신속하게 옮겨야 합니다. 수분 관리가 중요합니다. 화재 진압 및 폭발 환기 장치를 갖춘 별도의 실온 보관이 표준입니다.
Q: 분무 시스템 설계에는 어떤 표준이 적용되나요?
A: 보편적인 표준은 없지만, 해당 압력 용기 코드 및 재료 표준에 따라 설계 선택이 결정됩니다. 현지 규정과 요건을 잘 알고 있는 숙련된 공급업체와 상담하세요. 새로운 위험 시스템을 설치할 때는 법률 및 규제 위원회의 자문을 구하세요.