Electron beam melting (EBM) is an additive manufacturing process that uses an electron beam to selectively melt metal powder layer-by-layer to build up fully dense parts. This guide provides an in-depth overview of the EBM process including how it works, materials, applications, advantages, design considerations, equipment, post processing, quality control, comparisons, costs, and FAQs.
Introduction to Electron Beam Melting (EBM)
Electron beam melting is a type of powder bed fusion additive manufacturing where an electron beam selectively fuses regions of a powder bed to construct parts layerwise.
Manfaat utama dari EBM meliputi:
- Fully dense metal parts
- Sifat mekanik yang sangat baik
- Good surface finish and resolution
- High build rates and low costs per part
- Struktur pendukung minimal yang dibutuhkan
- Repeatable and consistent results
EBM enables direct production of complex, high-performance metal components across aerospace, medical, automotive, and industrial applications.
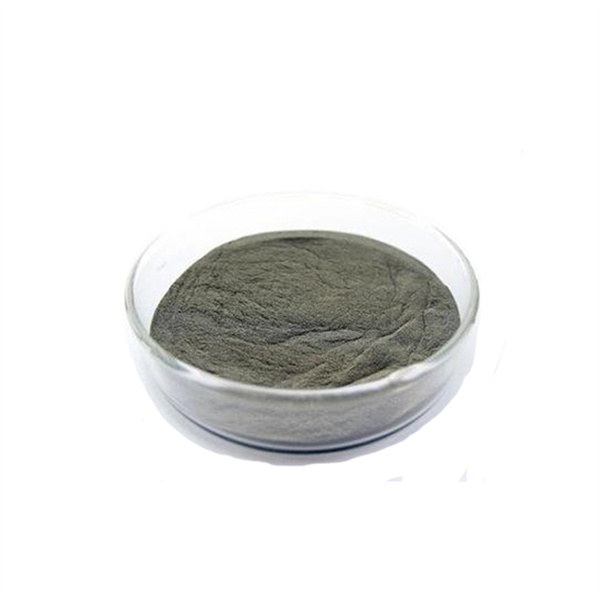
How the EBM Process Works
The EBM process involves the following key steps:
Proses peleburan balok elektron
- CAD model sliced into layers
- Bedak menyebar menjadi lapisan tipis
- Electron beam scans and melts powder
- Layer fused onto prior layers
- Repeated layerwise until part built
- Bagian penyangga bubuk yang tidak menyatu
- Removal from machine and post processing
By selectively melting the powder layers, complex geometries can be fabricated directly from digital data.
Materials for EBM
EBM can process a range of conductive materials including:
- Titanium alloys like Ti6Al4V
- Paduan krom kobalt
- Nickel-based superalloys
- Tool steels like H13
- Paduan aluminium
- Pure copper
- Logam mulia seperti emas, perak
Both standard and custom alloys optimized for AM can be printed with EBM technology. The powder bed nature allows alloys not easily processed by other methods.
EBM Applications
EBM is well suited to components that benefit from:
- Complex geometries only possible with AM
- Short lead production times
- Rasio kekuatan-terhadap-berat yang tinggi
- Good fatigue and fracture resistance
- Sifat mekanik yang sangat baik
- Biocompatibility and corrosion resistance
- High temperature performance
- Part consolidation – reduce assembly steps
Industry applications include:
- Aerospace: structural brackets, turbocharger wheels, engine parts
- Medical: orthopedic implants, surgical instruments
- Automotive: lightweighted lattice structures
- Industrial: heat exchangers, fluid handling parts
EBM supports innovative designs across sectors thanks to broad alloy options and excellent mechanical properties.
Advantages of Electron Beam Melting Additive Manufacturing
Key benefits of the EBM process include:
- Fully dense metal parts – Reach 99.9%+ density matching and exceeding cast properties.
- Sifat mekanik – Excellent strength, fatigue life, hardness, and fracture resistance.
- High build rates – More than 100 cm3/hour possible by scanning multiple regions simultaneously.
- Low operating costs – Electricity is the primary operating cost. Consume less energy than laser-based processes.
- Minimal supports – Parts self-support during the build, requiring little support removal post processing.
- Powder recyclability – Unused powder can be reused, reducing material costs substantially.
- Mengurangi limbah – Very high powder reuse rates and near net-shape production results in less waste than machining processes.
- Konsolidasi bagian – Combine assemblies into single printed parts to reduce manufacturing and assembly steps.
For metals production across aerospace, medical, automotive and industrial applications, EBM delivers high performance additive manufacturing results not easily matched by other methods.
Pertimbangan Desain EBM
To fully utilize EBM benefits, designs should follow AM design principles:
- Use organic, bionic shapes not possible by machining
- Minimize supports by designing appropriate geometry
- Optimize wall thicknesses for balance of speed and strength
- Account for minimum feature size capabilities
- Orient parts to maximize resolution and mechanical properties
- Consolidate subassemblies into single parts when possible
- Consider the effects of layerwise fabrication
- Desain saluran internal untuk menghilangkan bubuk yang tidak meleleh
Work with experienced AM engineering specialists to design high-performance parts tailored to EBM capabilities.
Equipment for the EBM Process
EBM systems consist of:
- Electron beam column – Powerful electron beam
- Powder cassettes – Deliver fresh powder
- Powder hoppers – Feed powder layerwise
- Build tank – Contains the build platform and growing parts
- Vacuum pump – Maintains high vacuum during builds
- Kontrol – Software to prepare and monitor builds
Industrial EBM systems allow both prototyping and volume production. Manufacturers include Arcam EBM and GE Additive.
Key EBM Machine Specifications:
- Build envelope size – diameter up to 500 mm, height up to 380 mm
- Beam power – Up to 3.7 kW
- Beam focus – Down to 0.1 mm spot size
- Build speed – Over 700 cm3/hour possible
- Vacuum – High 10-4 mbar vacuum required
- Precise layer control – 0.05 mm thickness
Options like multiple powder hoppers or beam guns enable higher throughput. The build chamber is maintained under high vacuum during printing using integrated vacuum pumps.
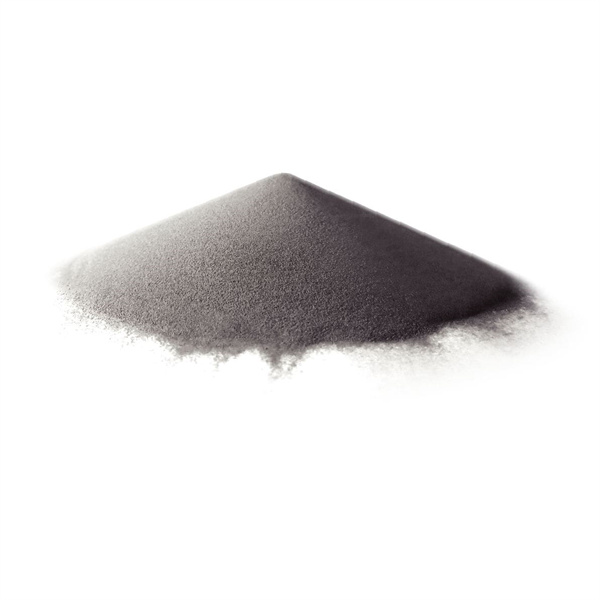
EBM Post Processing
After printing, parts undergo post-processing:
- Penghapusan bubuk – Excess powder is recovered and sieved for reuse
- Penghapusan dukungan – Minimal manual support removal needed
- Perlakuan panas – Stress relief and altering microstructure as needed
- Finishing permukaan – Machining, blasting, grinding or polishing if required
Since support structures are minimal and high density is achieved directly from the EBM machine, post-processing is relatively straightforward compared to some other AM methods.
Kontrol Kualitas untuk EBM
Consistent high quality results require procedures like:
- Validation builds to dial in parameters and verify properties
- Monitoring of powder characteristics and reuse
- Testing of mechanical properties for qualification
- CT scanning or X-ray inspection of complex internal geometries
- Dimensional accuracy checks
- Measurement of surface roughness
- Documentation of build parameters and batch traceability
- Periodic calibration and maintenance of EBM equipment
Work with experienced suppliers with rigorous quality systems tailored for regulated sectors requiring part qualification.
How EBM Compares to Other Additive Methods
EBM vs SLM:
- EBM uses electrons while SLM uses a laser
- EBM has higher build rates while SLM offers finer resolution
- EBM does not require inert gas while SLM normally uses nitrogen
- Both produce near fully dense metal parts in a powder bed
EBM vs Binder Jetting:
- EBM melts powder while binder jetting glues particles together
- EBM creates >99% dense parts while binder jetting produces a “green” part needing sintering
- EBM metals retain excellent properties while binder jetting has lower performance
EBM vs DED:
- EBM utilizes powder bed vs blown powder for DED
- EBM has higher accuracy and surface finish while DED is faster
- EBM has minimal supports while DED needs more supports
For low to medium volumes of end-use metal parts, EBM competes favorably against other powder-based AM processes on cost.
Cost Breakdown of EBM Parts
When analyzing EBM part costs, key factors include:
- Machine costs – Hourly operating lease rate. Runs ~$100-$300/hour.
- Tenaga kerja – Part design, optimization, pre/post processing.
- Bedak – Material choice and reuse rates greatly affect costs.
- Energi – Electricity to run EBM machine and ancillary equipment.
- Kontrol kualitas – Testing degree depends on application.
- Pengolahan pasca – Mostly automated means lower processing costs.
- Volume – Set up is fixed cost amortized at higher volumes.
Leveraging EBM design rules and quality procedures tailored for production applications provides very cost-effective metal parts unachievable by other means.
Innovation Trends in EBM Technology
Advances in EBM technology and applications include:
- Larger build envelopes and faster scan rates enabling higher volume production
- New generation multi-beam systems for increased throughput
- Expanded material options like copper, aluminum, and custom alloys
- Automated powder handling and internal metrology equipment
- Hybrid EBM and CNC machining centers
- Design software integrating EBM capabilities for “design for AM”
- Supply chain optimization with distributed manufacturing models
These innovations will drive increased adoption of EBM across regulated industries appreciating the technology’s quality, consistency, and performance.
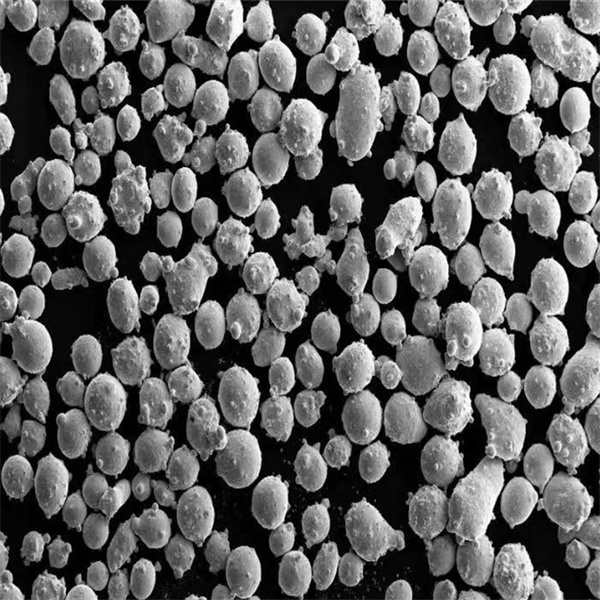
PERTANYAAN YANG SERING DIAJUKAN
T: Bahan apa saja yang dapat Anda proses dengan EBM?
A: Titanium, nickel superalloys, tool steels, cobalt chrome, aluminum, and precious metals are commonly processed. Both standard and custom alloys optimized for AM can be used.
Q: What industries use EBM?
A: Aerospace, medical, automotive, and industrial sectors leverage EBM for high-performance end-use metal parts not easily manufactured conventionally.
Q: What is the typical surface finish?
A: As-printed surface finishes in the 15-25 micron Ra range are typical but can be improved further with post-processing if needed.
T: Seberapa akuratkah EBM dibandingkan dengan pemesinan CNC?
A: Dimensional accuracy within 0.1-0.3% is standard for EBM technology, comparable or exceeding machined accuracy for most features.
Q: What types of internal channels and geometries can be produced?
A: Complex freeform channels and lattices with diameters down to 1-2 mm can be reliably fabricated using EBM technology.
Q: Can you electroplate EBM parts?
A: Yes, EBM parts can be electrically conductive and readily accept platings like chrome, gold, or silver plating if required.
Q: Are the mechanical properties comparable to wrought metals?
A: Yes, EBM parts meet or exceed the tensile strength, fatigue, and fracture resistance of wrought equivalents.
Q: How long does it take to build a part?
A: Build speed is geometry dependent but ranges from 5-20 cm3/hour on modern EBM machines, enabling rapid turnaround.
T: Apakah EBM memerlukan dukungan apa pun?
A: Minimal supports are needed due to the high powder bed temperature. Reduces post-processing time.
Q: Is EBM environmentally friendly?
A: EBM has good sustainability credentials from high powder reuse rates and low waste compared to subtractive processes. Energy use per part is declining with newer generation equipment.