Aufgrund seines außergewöhnlichen Verhältnisses von Festigkeit zu Gewicht, Korrosionsbeständigkeit und Biokompatibilität ist Titan ein hoch geschätztes Material für die additive Fertigung in der Luft- und Raumfahrt, der Medizintechnik, der Automobilindustrie und in industriellen Anwendungen. In diesem Überblick werden die verschiedenen Titan-Am-Pulver, ihre entsprechenden Eigenschaften, Nachbearbeitungsprozesse, weltweit führende Anbieter und beispielhafte Anwendungsfälle nach Branchen untersucht.
Überblick über Titan-Am-Pulver
Die wichtigsten Eigenschaften machen Titan zu einem idealen Werkstoff für das Pulverbettschmelzen und das AM-Verfahren mit gerichteter Energieabscheidung:
- Hohe Festigkeit - übertrifft oft geglühtes Titan und kann mit Ti-6Al-4V mithalten
- Geringe Dichte - hohes Verhältnis von Festigkeit zu Gewicht, geringeres Gewicht der gedruckten Teile
- Korrosionsbeständigkeit - Schutzschild aus Oberflächenoxid
- Biokompatibilität - geeignet für medizinische Geräte und Implantate
- Fähigkeit zur Legierung - maßgeschneiderte Eigenschaften wie Festigkeit und Härte
- Kosteneffizienz - geringerer Materialabfall gegenüber der Bearbeitung von Blöcken
- Buy-to-fly-Verhältnisse von mehr als 90%+ - optimierte Designs sparen Gewicht und Material
In Verbindung mit der Designfreiheit, die AM ermöglicht, erschließt Titan neue Anwendungsmöglichkeiten.
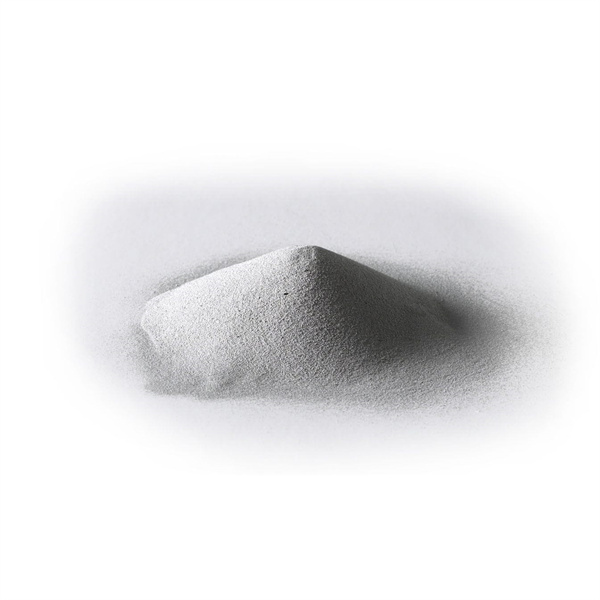
Optionen für Titanlegierungspulver für AM
Zu den beliebten Titanlegierungen, die heute eingesetzt werden, gehören handelsübliche Reinheitsgrade, Alpha- und Alpha-Beta-Legierungen sowie neuartige proprietäre Grade wie Titan 6242.
Übliche Titanlegierungszusammensetzungen
Legierung | Al% | V% | Fe% | O% | Andere |
---|---|---|---|---|---|
CP Ti Klasse 1 | – | – | ≤ 0.20 | ≤ 0.18 | – |
CP Ti Klasse 2 | – | – | ≤ 0.30 | ≤ 0.25 | – |
Ti-6Al-4V | 5.5-6.5 | 3.5-4.5 | ≤ 0.25 | ≤ 0.13 | – |
Ti 6242 | 5.8-6.8 | – | ≤ 0.30 | ≤ 0.20 | Mo, Zr |
Sauerstoff-, Stickstoff- und Kohlenstoffspuren sind streng limitiert, um optimale AM-Verarbeitung und mechanische Eigenschaften zu gewährleisten.
Spezifikationen für Titan-Am-Pulver
Hochreines, kugelförmiges Titanpulver mit kontrollierter Partikelgrößenverteilung ist die Voraussetzung für fehlerfreie, dichte AM-Komponenten.
Titanpulver Partikelgrößenverteilung
Messung | Spezifikation |
---|---|
Größenbereich | 15 - 45 μm |
Mittlere Partikelgröße | 25-35 μm |
Partikelform | Überwiegend kugelförmig |
Die Sphärizität fördert die Verteilbarkeit des Pulvers. Die kontrollierte Verteilung verhindert Entmischungsprobleme bei der Anwendung und Wiederverwendbarkeit.
Nachbearbeitungsverfahren für AM-Teile aus Titan
Zu den üblichen Nachbehandlungsoptionen für additiv gefertigte Titanbauteile gehören:
Nachbearbeitungsmethoden
Stressabbau
Durch die Alterung bei niedrigen Temperaturen werden Eigenspannungen aus dem Herstellungsprozess eliminiert, wodurch ein möglicher Verzug und Rissbildung verhindert werden.
Oberflächenveredelung
Verbessert die Oberflächengüte für Präzisionsmaße, bricht scharfe Kanten oder verbessert das ästhetische Erscheinungsbild.
Heiß-Isostatisches Pressen
Verdichtet jede innere Porosität durch gleichzeitige Anwendung erhöhter Temperatur und isostatischen Drucks. Erforderlich für dynamische Endanwendungen.
Wärmebehandlung
Verändert die Mikrostruktur von Ti-6Al-4V und anderen Titanlegierungen, um mechanische Eigenschaften wie Duktilität und Ermüdungsfestigkeit zu verbessern.
Bearbeitung
Ermöglicht hochpräzise Abmessungen und Oberflächengüten für Lager- und Dichtungsoberflächen von endkonturnahen AM-Teilen.
Additive Fertigungstechniken für Titanpulver
Der moderne Metall-3D-Druck nutzt das Mikroschweißen von feinem Titan, um komplexe Bauteile zu konstruieren. Zwei gängige Ansätze sind:
Vergleich von Titan-AM-Prozessoptionen
Methode | Beschreibung | Vorteile | Beschränkungen |
---|---|---|---|
Pulverbett Fusion | Laser oder E-Beam schmelzen Bereiche des Pulverbettes selektiv nach digitalem Modell | Außergewöhnliche geometrische Fähigkeiten und Materialvielfalt für funktionelle Titanbauteile zur Endanwendung | Langsamere Baugeschwindigkeiten als beim DED; Größenbeschränkungen durch das Maschinenbett |
Gezielte Energieabscheidung | Fokussierte Wärmequelle schmilzt Metallpulversprühdüse | Größere Bauteile möglich; kumulative Baufläche. Ideal für Reparaturen und Beschichtungen. | Schlechtere Oberflächengüte; höhere Porosität - erfordert umfangreiche Nachbearbeitung |
Laserbasierte Verfahren werden derzeit am häufigsten für das Drucken hochreiner Titanlegierungen eingesetzt, da sie sich durch Präzision und Materialeigenschaften auszeichnen.
Anwendungen von Titan-Am-Pulver
Dank der Vorteile des Titanmaterials, wie hohe mechanische Leistung pro Gewichtseinheit, kombiniert mit der Freiheit des AM-Designs, gibt es viele Anwendungen:
Branchen, die Titan-AM-Teile einsetzen
Luft- und Raumfahrt - Motorhalterungen, Drohnenteile, Satellitenkomponenten
Medizinisch & Zahnmedizinisch - Implantate, Prothesen, chirurgische Instrumente
Automobilindustrie - Motorsportausrüstung, kundenspezifische Halterungen
Öl und Gas - Tiefseewerkzeuge, Ventile und Pumpen
Stromerzeugung - Leichtbau-Laufräder, Turbinenschaufeln
Neuartige technische Legierungen wie Ti-6242 erweitern die Möglichkeiten von Titan in wachstumsstarken Sektoren noch weiter.
Führende Anbieter von Titandruckpulvern
Zu den wichtigsten Herstellern von sphärischen Titanpulvern für zuverlässige AM-Prozesse gehören:
Titanpulver Hersteller
Unternehmen | Gemeinsame Noten | Preis/Kg |
---|---|---|
AP&C | Ti-6Al-4V, Ti-6242, Güteklasse 2, 23 | $50 – $350 |
Der Linde Konzern | Ti-6Al-4V, Güteklasse 2, 23, 5 | $200 – $600 |
Wolfram-Metall-Pulver | Ti-6Al-4V, Güteklasse 5 | $100 – $500 |
Sandvik | Ti-6Al-4V | $120 – $310 |
Die Preise hängen wesentlich von den Reinheitsstandards, den Parametern der Pulvergröße, der zertifizierten Chemie und den Abnahmemengen ab.
FAQ
Welcher Titanlegierungsgrad eignet sich am besten für medizinische oder zahnmedizinische AM-Teile?
Medizinisches Titan der Güteklasse 5 mit strengen chemischen Kontrollen wird für biologisch inerte Implantatanwendungen empfohlen, die eine optimale Biokompatibilität und eine hohe Ermüdungsleistung erfordern.
Warum ist ein niedriger Sauerstoffgehalt bei Titandruckpulvern so wichtig?
Ein hoher Sauerstoffgehalt führt zu überschüssigen Titanoxiden, die die Schmelzfähigkeit, Duktilität, Ermüdungsfestigkeit und mechanische Leistung beeinträchtigen. Der Sauerstoffgehalt wird auf unter 0,18-0,2% begrenzt.
Welche Titanlegierungen profitieren am meisten von Nachbearbeitungsprozessen?
Zweifache Wärmebehandlungen für Ti-6Al-4V erhöhen die Zugfestigkeit und verbessern gleichzeitig die Duktilität. Titan der Güteklasse 2 erzielt die höchsten Zugfestigkeitssteigerungen durch Entlastungsglühen, gefolgt von einer Alterungsreaktion.
Ist für AM-Teile aus Titan eine Oberflächenbehandlung erforderlich?
Bestimmte Anwendungen erfordern Maßgenauigkeit, tribologische, ästhetische oder inaktivierende Anforderungen, die am besten durch Oberflächenveredelung erfüllt werden - einschließlich CNC-Präzisionsbearbeitung, Schleifen/Polieren, Erodieren, Kugelstrahlen, Eloxieren, Plasma-Elektrolyt-Oxidation usw.
Wie sollten Lieferanten für Aufträge zum Druck von Titanpulver bewertet werden?
Zu den wichtigsten Merkmalen, die von Additivherstellern und Konstrukteuren für die Qualifizierung von Titanpulverlieferanten herangezogen werden und die über einen angemessenen Preis hinausgehen, gehören: kugelförmige Morphologie, strenge Kontrolle der Partikelgrößenverteilung, extrem niedriger Gehalt an gasförmigen Verunreinigungen (insbesondere Sauerstoff und Stickstoff), Rückverfolgbarkeit der Chargen durch ein strenges Qualitätsmanagementsystem, reaktionsschnelles technisches Fachwissen, Verfügbarkeit von Probenahmen und Zertifizierungen, die standardisierte interne Prüfprotokolle belegen.