Überblick über MIM-Fertigung
Metallspritzguss (MIM) ist ein pulvermetallurgisches Herstellungsverfahren, mit dem kleine, komplexe Metallteile in großen Stückzahlen hergestellt werden.
Zu den wichtigsten Schritten im MIM gehören:
- Mischen von feinem Metallpulver mit Bindemittel zur Herstellung eines Ausgangsmaterials
- Einspritzen des Ausgangsmaterials in eine Form mittels Kunststoffspritzguss
- Entbinderung, um den Binder zu entfernen und nur das Metallpulver zurückzulassen
- Sintern, um das Pulver zu einer festen Metallkomponente zu verdichten
MIM kombiniert die Designflexibilität des Kunststoffspritzgusses mit der Festigkeit und Leistung bearbeiteter Metalle. Es handelt sich um ein kostengünstiges Verfahren für die komplexe Großserienfertigung von Kleinteilen.
So funktioniert die MIM-Fertigung
Der MIM-Herstellungsprozess umfasst:
- Formulieren eines Ausgangsmaterials durch Mischen und Pelletieren von feinem Metallpulver mit Polymerbindemitteln
- Erhitzen des Ausgangsmaterials und Spritzgießen in die gewünschte Form
- Chemisches Entfernen des Bindemittels durch Lösungsmittel- oder thermische Entbinderung
- Sintern der entbinderten Metallkomponente in einem Ofen, um ein vollständig dichtes Teil zu erzeugen
- Optionale sekundäre Endbearbeitungsvorgänge wie Bearbeiten, Bohren, Plattieren
MIM ermöglicht die wirtschaftliche Herstellung von Bauteilen mit komplexen Geometrien, engen Toleranzen und hervorragenden mechanischen Eigenschaften.
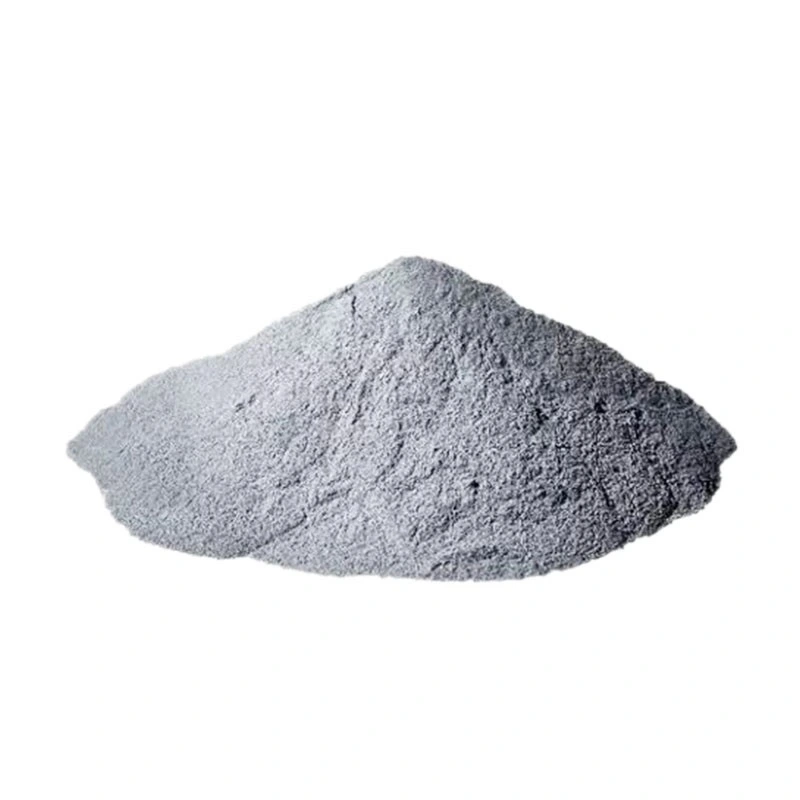
Arten von Metallen, die in MIM verwendet werden
Mit der MIM-Technologie können verschiedenste Metalle bearbeitet werden:
- Edelstähle – 316L, 17-4PH, 410, 420
- Werkzeugstähle – H13, P20, A2, D2
- Magnetische Legierungen – Weich- und Hartferrite
- Kupferlegierungen – Messing, Bronze
- Niedriglegierte Stähle – 4100, 4600
- Superlegierungen – Inconel 625, 718
- Schwere Wolframlegierungen
- Titanlegierungen – Ti6Al4V, Ti6Al4V ELI
MIM eignet sich im Allgemeinen für jedes Material, das auf eine hohe Dichte gesintert werden kann. Bevorzugt werden Metalle mit Schmelzpunkten unter 1000 °C.
MIM-Herstellungsprozessparameter
Zu den kritischen Prozessparametern im MIM gehören:
Rohstoffentwicklung:
- Pulvermorphologie, Größenverteilung
- Bindemittelzusammensetzung
- Pulverbeladung – typischerweise 60-65 vol%
- Mischprozess – Temperatur, Zeit, Atmosphäre
Formen:
- Formmaterial – P20-Werkzeugstahl bevorzugt
- Einspritztemperatur, Druck, Geschwindigkeit
- Tordesign
- Kühlsystemdesign
Entbinden:
- Lösungsmittel-, thermische oder katalytische Entbinderung
- Entbinderungstemperatur, Zeit, Atmosphäre
Sintern:
- Temperaturprofil – Entbinderungs- und Sinterschritte
- Aufheizrate, Sinterzeit, Atmosphäre
- Sintertemperatur und -druck
Überlegungen zum MIM-Design und zu Teilen
Der MIM-Prozess ermöglicht Gestaltungsfreiheit, es müssen jedoch einige Richtlinien befolgt werden:
- Wandstärke: Bereich 0,3 – 4 mm möglich
- Oberflächenbeschaffenheit: Im gesinterten Zustand beträgt der Ra 1,5 μm
- Maßtoleranzen: ±0,5% ist Standard, aber ±0,1% erreichbar
- Vermeidung von Pulvereinschlüssen: Keine vollständig geschlossenen Hohlräume im Inneren
- Formschrägen: > 1° Formschräge bevorzugt
- Sinterschrumpfung: Volumenschrumpfung ca. 20%
- Fehler reduzieren: Großzügige Eckenradien minimieren Risse
Fortschrittliche Simulationstools ermöglichen eine virtuelle Optimierung des MIM-Prozesses während des Entwurfs, um Versuch und Irrtum zu reduzieren.
Vorteile von MIM-Fertigung
Zu den wichtigsten Vorteilen der Verwendung von MIM gehören:
- Komplexe Geometrien und enge Toleranzen
- Hervorragende mechanische Eigenschaften
- Große Auswahl an Materialoptionen
- Hohe Produktionsmengen zu geringen Kosten
- Minimiert Abfall – endkonturnaher Prozess
- Reduzierte Bearbeitung und Endbearbeitung
- Komponentenintegration und Teilekonsolidierung
- Automatisierter Prozess, geeignet für den Lights-Out-Betrieb
- Umweltfreundlicher als Zerspanung
- Skalierbar vom Prototypen bis zur vollständigen Produktion
Aufgrund dieser Vorteile eignet sich MIM branchenübergreifend für die kostengünstige Herstellung von Präzisionsmetallkomponenten in großen Stückzahlen.
Einschränkungen und Herausforderungen von MIM
Einige mit MIM verbundene Einschränkungen:
- Begrenzte Größe – typischerweise <45 g Fertigmasse pro Teil
- Beschränkt auf Metalle, die zu hoher Dichte sintern können
- Umfangreiches Fachwissen bei der Rohstoffformulierung erforderlich
- Vorabkosten für die Formen- und Prozessentwicklung
- Gerade Abschnitte und scharfe Ecken neigen zu Rissen
- Längere Vorlaufzeit im Vergleich zu anderen Prozessen
- Um die endgültigen Eigenschaften zu erzielen, ist häufig eine Nachbearbeitung erforderlich
- Mangelnde Gestaltungsfreiheit bei einigen Funktionen wie Threads
- Die Sekundärbearbeitung kann bei gesinterten Metallen eine Herausforderung darstellen
Mit geeigneten, auf die Anwendung zugeschnittenen Rohstoffen und Prozessdesigns können diese Herausforderungen gemeistert werden, um das volle Potenzial der MIM-Technologie auszuschöpfen.
Anwendungen von MIM-gefertigten Teilen
MIM findet in den folgenden Sektoren weit verbreitete Anwendung:
Automobilindustrie: Hardware, Sensoren, Kraftstoffsystem und Motorkomponenten sperren
Luft- und Raumfahrt: Laufräder, Düsen, Ventile, Befestigungselemente
Medizinische: Zahnimplantate, Skalpellgriffe, orthopädische Instrumente
Feuerarme: Abzüge, Magazine, Schlitten, Hämmer
Uhren: Gehäuse, Armbandglieder, Verschlüsse und Schnallen
Elektrisch: Steckverbinder und Leadframes für Zuverlässigkeit
Typische Teilegrößen reichen von 0,1 Gramm bis 110 Gramm, wobei die größten kommerziellen Produktionsmengen bei Verbindungsstücken, Verbindungselementen, chirurgischen Instrumenten und kieferorthopädischen Zahnspangen entstehen.
Kostenanalyse der MIM-Herstellung
Zu den MIM-Herstellungskosten gehören:
- Rohstoffentwicklung – Formulierung, Mischung, Charakterisierung
- Formenbau – Hochpräzise Formenbearbeitung
- MIM-Maschine – Große Kapitalinvestitionen in Ausrüstung
- Operation – Arbeitskräfte, Betriebskosten, Verbrauchsmaterialien
- Sekundäroperationen – Entbindern, Sintern, Endbearbeiten
- Materialverwertung – Metallpulver macht etwa 60% der Gesamtkosten aus
- Verbrauchsmaterialien – Mehrere Formhohlräume, um ein hohes Volumen zu ermöglichen
- Produktionsvolumen – Einrichtungskosten werden über das Gesamtvolumen amortisiert
- Buy-to-fly-Verhältnis – Nur 2-4x im Vergleich zu anderen PM-Prozessen
- Designoptimierung – Einfache Geometrien mit minimaler Bearbeitung
Bei großen Produktionsmengen bietet MIM sehr günstige Kosten bei hohen Fertigungsraten mit ausgezeichneter Materialausnutzung und nahezu endkonturnahen Fähigkeiten.
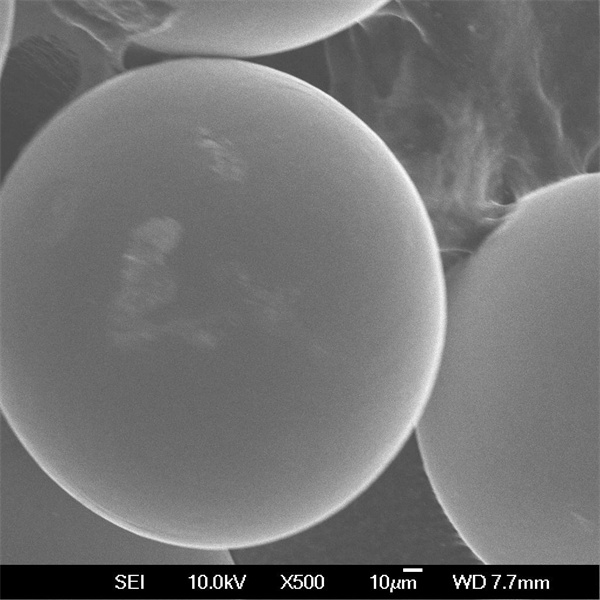
Auswählen eines MIM-Fertigung Partner
Schlüsselfaktoren bei der Auswahl eines MIM-Lieferanten:
- Nachgewiesene Fachkompetenz und langjährige Erfahrung mit MIM
- Materialportfolio – Auswahl an Optionen aus Edelstahl, Werkzeugstahl und Superlegierungen
- Qualitätszertifizierungen – vorzugsweise ISO 9001, ISO 13485
- Sekundärbearbeitungsmöglichkeiten – Bearbeitung, Wärmebehandlung, Oberflächenveredelung
- Strenge Prozess- und Produktqualitätskontrollverfahren
- F&E-Kapazitäten für die Rohstoffformulierung und Prozessentwicklung
- Formflusssimulation und andere Fachkenntnisse in der Designanalyse
- Programmmanagementfähigkeiten zur Unterstützung von Kundenprojekten
- Skalierbare Kapazität, die mit den Produktionsanforderungen wachsen kann
- Wettbewerbsfähige Preise mit mehrjährigen Verträgen
- Standort ermöglicht enge Zusammenarbeit und Schutz des geistigen Eigentums
Die Auswahl eines etablierten MIM-Herstellers mit Nischenfokus auf MIM liefert im Gegensatz zu einer allgemeinen CNC-Metallbearbeitungswerkstatt die besten Ergebnisse.
Vor- und Nachteile von MIM vs. CNC-Bearbeitung
Vorteile von MIM:
- Hervorragende Maßgenauigkeit und Wiederholbarkeit
- Komplexe Geometrien, die durch maschinelle Bearbeitung nicht erreichbar sind
- Nahezu Endform mit minimalem Materialabfall
- Lässt sich effizient auf sehr hohe Produktionsmengen skalieren
- Automatisierter Prozess ermöglicht 24/7-Betrieb
- Kürzere Vorlaufzeiten nach der Einrichtung
- Deutlich geringere Teilekosten bei hohen Stückzahlen
- Die Eigenschaften entsprechen oder übertreffen bearbeitete Metalle
Nachteile von MIM:
- Hohe anfängliche Einrichtungskosten für Ausgangsmaterial und Form
- Begrenzte Größenmöglichkeiten
- Eingeschränkte Gestaltungsfreiheit bei einigen Funktionen
- Geringere anfängliche Produktionsmengen sind ineffizient
- Umfangreiches Fachwissen bei der Rohstoffformulierung erforderlich
- Möglicherweise sind noch sekundäre Endbearbeitungsvorgänge erforderlich
- Längere Vorlaufzeiten und geringere Qualität für erste Prototypen
Für kleine komplexe Metallteile, die in sehr großen Stückzahlen hergestellt werden, ist MIM die zeit- und kosteneffizienteste Fertigungsmethode.
Vergleich zwischen MIM und Metall-3D-Druck
Hauptunterschiede zwischen MIM und 3D-Druck:
Parameter | MIM | 3D-Druck |
---|---|---|
Prozess | Bindemittelspritzguss + Sintern | Pulverbettschmelzen oder -binden |
Materialien | Große Auswahl an Legierungen | Begrenzte Materialoptionen |
Teilegröße | < 45 Gramm | Bis zu mehreren kg |
Genauigkeit | Ausgezeichnet, ±0,5% | Mäßig, ±1% |
Oberflächengüte | Sehr gut | Mittel bis schlecht |
Produktionsmaßstab | 10.000 bis Millionen | Prototyping bis mittlere Stückzahlen |
Kosten pro Teil | Sehr niedrig | Mittel bis hoch |
Sekundärbearbeitung | Wird vielleicht benötigt | Normalerweise erforderlich |
Vorlaufzeit | Länger für die Prozessentwicklung | Schnellere Prototypen, aber langsamere Serienproduktion |
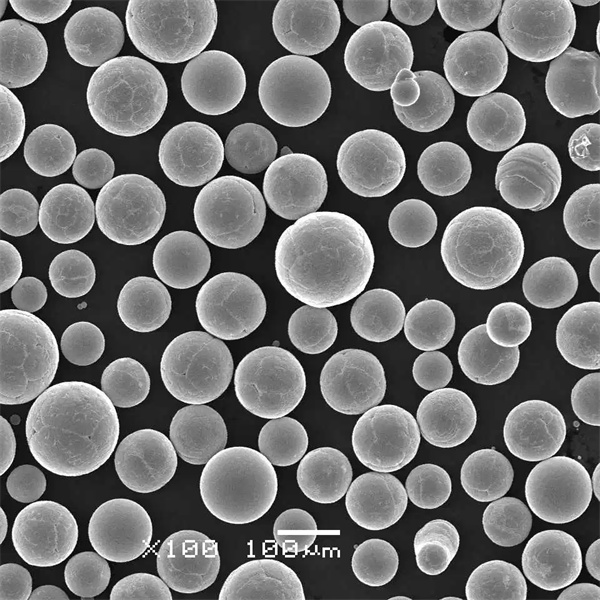
FAQ
Was ist die typische Toleranzfähigkeit für die MIM-Fertigung?
MIM kann zuverlässig Maßtoleranzen von ±0,5% mit fortschrittlichen Prozessen erreichen, die eine Toleranz von ±0,1% für kleine Präzisionskomponenten ermöglichen.
Was sind übliche MIM-Rohstoffzusammensetzungen?
Typische MIM-Rohstoffe bestehen aus 60–651 TP3T Metallpulver, beladen mit 35–401 TP3T Bindemittel, bestehend aus Polymeren wie Polypropylen, Polyethylen und Polystyrol. Wachse verbessern den Pulverfluss.
Kann MIM Teile aus mehreren Materialien herstellen?
Ja, MIM kann Verbund- und abgestufte Strukturen herstellen, indem in jeden Formhohlraum unterschiedliche Ausgangsstoffe eingespritzt werden oder Bindemittel mit unterschiedlichen Schmelzpunkten verwendet werden.
Welche Formteilgröße kann mit MIM erreicht werden?
MIM-Formteile sind typischerweise auf Teile mit einer Masse von weniger als 45 Gramm und Abmessungen von weniger als 50 mm beschränkt. Größere oder schwerere Komponenten lassen sich nur schwer ausreichend füllen und verdichten.
Wie schneidet MIM im Vergleich zum Druckguss für kleine Metallkomponenten ab?
MIM bietet eine höhere Maßgenauigkeit und Materialfestigkeit, Druckguss hat jedoch schnellere Zykluszeiten. MIM eignet sich besser für komplexe Geometrien, während Druckguss für einfachere Formen vorzuziehen ist.