Überblick über Elektronenstrahlschmelzen
Elektronenstrahlschmelzen (EBM) ist ein additives Fertigungsverfahren, das eine Elektronenstrahl-Energiequelle verwendet, um metallisches Pulvermaterial Schicht für Schicht selektiv zu schmelzen und zu verschmelzen, um Komponenten aufzubauen.
Zu den wichtigsten Details zum Elektronenstrahlschmelzen gehören:
- Verwendet eine Elektronenstrahlkanone unter Vakuum, um das Pulver zu schmelzen.
- Der Aufbau erfolgt bei hohen Temperaturen, was eine gute Zwischenschichthaftung ermöglicht.
- Wird hauptsächlich für Ti-, Ni-, Co-Legierungen und andere Hochleistungsmaterialien verwendet.
- Bietet Teile mit nahezu voller Dichte und Eigenschaften, die herkömmlichen Mitteln entsprechen oder diese übertreffen.
- Unterstützt komplexe Geometrien, die mit herkömmlicher Fertigung nicht realisierbar sind.
- Wird häufig in der Luft- und Raumfahrt-, Medizin- und Automobilindustrie verwendet.
- Wird auch als Elektronenstrahl-Additive Fertigung (EBAM) oder Elektronenstrahl-Freiformfertigung (EBF3) bezeichnet.
Elektronenstrahlschmelzgeräte
Typ | Beschreibung |
---|---|
Elektronenstrahlkanone | Erzeugt und fokussiert einen Hochenergiestrahl, um das Material zu schmelzen. Schlüsselkomponente. |
Pulverbett | Enthält Pulverschichten, die mit Messern oder Walzen geharkt werden. Auf einer beweglichen Plattform aufgebaut. |
Vakuumkammer | Während des Buildvorgangs steht das gesamte System unter Vakuum. Entscheidend für die Strahlfokussierung. |
Kontrollsystem | Software unterteilt und steuert Build-Parameter. Bietet prozessbegleitende Überwachung und Kontrolle. |
Handhabungssystem | Zum Be-/Entladen von Teilen und zum Recycling nicht verbrauchten Pulvers. |
Abschirmung | Aufgrund der Erzeugung von Röntgenstrahlen ist eine Bleiabschirmung rund um die Kammer erforderlich. |
Verwendete Materialien in Elektronenstrahlschmelzen
Material | Wichtige Eigenschaften | Typische Anwendungen |
---|---|---|
Titan-Legierungen | Hohes Festigkeits-Gewichts-Verhältnis, Biokompatibilität | Luft- und Raumfahrt, medizinische Implantate |
Nickel-Legierungen | Korrosionsbeständigkeit, hohe Festigkeit | Turbinen, Raketenkomponenten |
Kobalt-Chrom-Legierungen | Härte, Verschleiß-/Korrosionsbeständigkeit | Medizinische Implantate, Werkzeugbau |
Rostfreier Stahl | Gute Haltbarkeit, einfachere Verarbeitung | Industrieller Werkzeugbau, Formen |
Aluminium-Legierungen | Geringes Gewicht | Luft- und Raumfahrt, Automobilindustrie |
Edelmetalle | Sehr chemisch inert | Schmuck, Medizin |
EBM kann Hochleistungslegierungen aufgrund der Leistungsintensität nur schwer mit laserbasierten Verfahren verarbeiten.
EBM-Prozessspezifikationen
Parameter | Typischer Bereich |
---|---|
Strahlleistung | 1-3 kW |
Strahlspannung | 30-150 kV |
Größe bauen | 200 x 200 x 350 mm max |
Höhe der Schicht | 50-200 μm |
Bauen Sie Geschwindigkeit auf | 5-100 cm3/h |
Balkengröße | 0,1-1 mm Durchmesser |
Vakuumniveau | 5 x 10-4 mbar |
Strahlfokus | 0,1–0,5 mm Punktgröße |
EBM-Systeme ermöglichen die Anpassung von Parametern wie Strahlleistung, Geschwindigkeit, Fokus usw. zur Abstimmung auf bestimmte Materialien.
Lieferanten von EBM-Systemen
Anbieter | Wichtige Details | Einstiegspreisspanne |
---|---|---|
Lieferant 1 | Pionier der EBM-Technologie. Größte installierte Basis. | $1,2-$1,5 Millionen |
Lieferant 2 | Systeme für kleinere Teile. Schnellere Scangeschwindigkeiten. | $0,8-$1,2 Millionen |
Lieferant 3 | Forschungssysteme. Öffnen Sie die Parametersteuerung. | $0,5-$0,8 Millionen |
Die Systemkosten variieren je nach Bauvolumen, Strahlleistung, mitgeliefertem Zubehör und Softwarefunktionen.
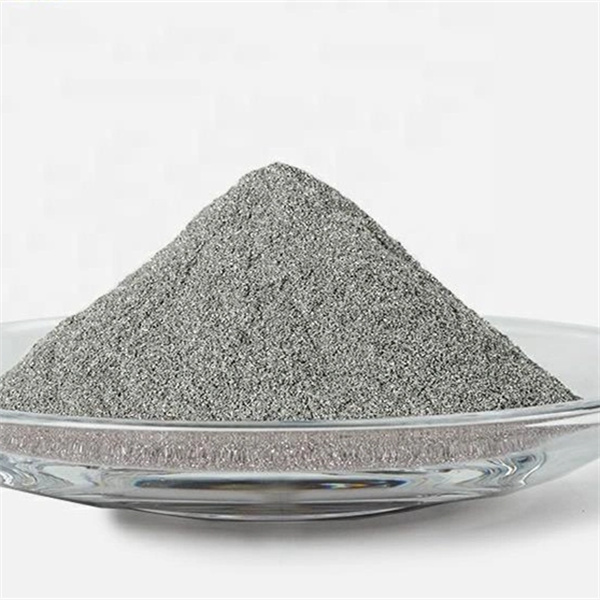
So wählen Sie einen EBM-Systemlieferanten aus
Bei der Auswahl eines EBM-Systemlieferanten sind folgende Schlüsselfaktoren zu berücksichtigen:
- Technisches Fachwissen – Der Lieferant sollte über fundierte Kenntnisse der Elektronenstrahlphysik, Metallurgie und Prozesserfahrung verfügen.
- Bewiesene Technologie – Suchen Sie nach etablierten Lieferanten mit einer Erfolgsbilanz erfolgreicher Systeminstallationen.
- Anwendungserfahrung – Der Lieferant sollte die Anwendungsanforderungen des Kunden verstehen und entsprechende Systemspezifikationen empfehlen.
- Systemzuverlässigkeit – Wählen Sie Lieferanten, die für die Entwicklung robuster EBM-Systeme mit angemessenen Betriebszeiten und Wartungsintervallen bekannt sind.
- Steuerungssoftware – Der Lieferant sollte benutzerfreundliche Software zum Programmieren, Überwachen und Optimieren von Builds anbieten.
- Technische Unterstützung – Suchen Sie nach reaktionsschnellen Supporttechnikern, die Probleme beheben und zur Verbesserung der Prozessergebnisse beitragen.
- Ausbildung – Der Lieferant sollte umfassende Schulungen zum Betrieb, zur Wartung und zur Sicherheit der Ausrüstung anbieten.
- Zukünftige Roadmap – Wählen Sie einen Lieferanten, der in laufende EBM-Innovationen für Ihren langfristigen Bedarf investiert.
So optimieren Sie die EBM-Prozess
Um qualitativ hochwertige EBM-Druckteile zu erhalten, befolgen Sie diese Best Practices zur Prozessoptimierung:
- Beginnen Sie mit einem hochreinen, kugelförmigen Pulver-Ausgangsmaterial, das speziell auf EBM zugeschnitten ist. Handhabung, Lagerung und Wiederverwendung des Pulvers sind ebenfalls von entscheidender Bedeutung.
- Nehmen Sie sich Zeit, das Profil und den Fokus des Elektronenstrahls zu kalibrieren. Durch Strahlformung kann die Dichte weiter verbessert werden.
- Wählen Sie den optimalen Strahlstrom und die optimale Scangeschwindigkeit für ein stabiles, homogenes Schmelzen.
- Passen Sie den Strahlfokus während des Aufbaus dynamisch an, um Geometrieänderungen zu berücksichtigen.
- Stellen Sie die Temperatur des Heißbetts auf über 700 °C ein, um Restspannungen zu reduzieren und Risse zu vermeiden.
- Passen Sie die Parameter separat für Konturen und Schraffurbereiche an, um die Oberflächenbeschaffenheit und Auflösung zu verbessern.
- Optimieren Sie die Stützstrukturen, um sie zu minimieren und gleichzeitig für ausreichende Verankerung und Wärmeableitung zu sorgen.
- Berücksichtigen Sie Parameterunterschiede zwischen verschiedenen Materialien – beispielsweise unterscheiden sich die Einstellungen für Titanlegierungen von denen für Nickel-Superlegierungen.
- Wählen Sie einen iterativen, empirischen Ansatz – führen Sie Test-Builds durch und variieren Sie dabei die Parameter, um die optimalen Bereiche zu finden.
So entwerfen Sie Teile für EBM
So entwerfen Sie erfolgreich Komponenten, die für den EBM-Prozess geeignet sind:
- Entwerfen Sie Wände mit einer Dicke von mehr als 0,4 mm, um ein vollständiges Schmelzen zu gewährleisten und Risse zu verhindern.
- Achten Sie bei zur Baurichtung geneigten Flächen auf einen Formschrägenwinkel von 5–15°, um die Pulverentfernung zu erleichtern.
- Minimieren Sie nicht unterstützte Überhänge, um Durchbiegungen und Defekte auf nach unten gerichteten Oberflächen zu reduzieren.
- Integrieren Sie Gitter und konforme Kühlkanäle, die durch die Designfreiheit von EBM ermöglicht werden.
- Konsolidieren Sie Unterbaugruppen zu Einzelteilen, um die Qualität zu verbessern und Verarbeitungsschritte zu reduzieren.
- Positionieren Sie Teile in der Baukammer, um den Supportbedarf zu minimieren und Kollisionen beim Harken zu vermeiden.
- Aufgrund der schichtbasierten Konstruktion ist die mechanische Festigkeit horizontal um 20-50% geringer als vertikal.
- Planen Sie einen zusätzlichen Aufmaß von 0,5–1 mm für die Nachbearbeitung wie Oberflächenbearbeitung oder Schleifen ein.
Arbeiten Sie während der Teilekonstruktionsiterationen eng mit EBM-Maschinenbedienern zusammen, um deren Prozesswissen zu nutzen.
So bearbeiten Sie EBM-Teile nach
Zu den typischen Nachbearbeitungsschritten für EBM-gedruckte Komponenten gehören:
- Entfernung der Stütze – Eventuell vorhandene Stützstrukturen vorsichtig von Hand oder mit Schneidwerkzeugen entfernen.
- Stressabbau – Wärmebehandlung bei 600–800 °C für 1–3 Stunden, um Restspannungen abzubauen.
- Bearbeitung – CNC-Fräsen, Drehen, Bohren zur Verbesserung der Maßgenauigkeit und Oberflächengüte.
- Schleifen – Automatisiertes oder manuelles Schleifen sorgt für präzisere Toleranzen und feinere Oberflächen.
- Polieren – Erzielt eine hervorragende Oberflächengüte ohne anhaftende Pulverpartikel.
- Beschichtungen – Funktionsbeschichtungen für Härte, Verschleißfestigkeit, elektrische Isolierung usw. auftragen.
- Heißisostatisches Pressen (HIP) – Schließt innere Hohlräume und verbessert das Ermüdungsverhalten weiter.
- Beitritt – Integrieren Sie Merkmale wie Gewindebohrungen, Befestigungselemente usw. mit geeigneten Techniken.
Nachbearbeitung von EBM-Teilen durch qualifizierte Bediener mit Erfahrung im Umgang mit der spezifischen Legierungszusammensetzung.
Anleitung zur Installation und Integration EBM Teile
Bei der Vorbereitung von EBM-gedruckten Teilen für die Integration in Endprodukte:
- Reinigen Sie die Oberflächen gründlich, um loses Pulver und Oxidation zu entfernen. Durch die richtige Reinigung wird die Haftung verbessert.
- Tragen Sie bei Bedarf Schutzbeschichtungen auf – Hartanodisieren, Galvanisieren, Lackieren usw. – verbessern den Korrosions- und Verschleißschutz.
- Berücksichtigen Sie beim Verbinden von EBM-Teilen mit anderen Metallkomponenten Unterschiede in der Wärmeausdehnung, um Spannungen zu vermeiden.
- Wählen Sie für das Material geeignete Verbindungstechniken aus – Schweißen, mechanische Befestigung, Kleben usw.
- Nutzen Sie beim Schweißen oder Löten das Wärmemanagement – Vorwärmen und kontrollierte Abkühlraten.
- Validieren Sie die Funktionalität der Baugruppe unter Betriebslasten und Umgebungen mithilfe von Prototyping und Tests.
- Prüfen Sie mithilfe von Techniken wie Röntgen, UT und Eindringprüfung auf Mängel – entscheidend für Anwendungen mit hoher Haftung.
Arbeiten Sie bei der Integration von EBM-Teilen Seite an Seite mit Designern und Ingenieuren, um eine robuste, optimierte Leistung in der Endbaugruppe sicherzustellen.
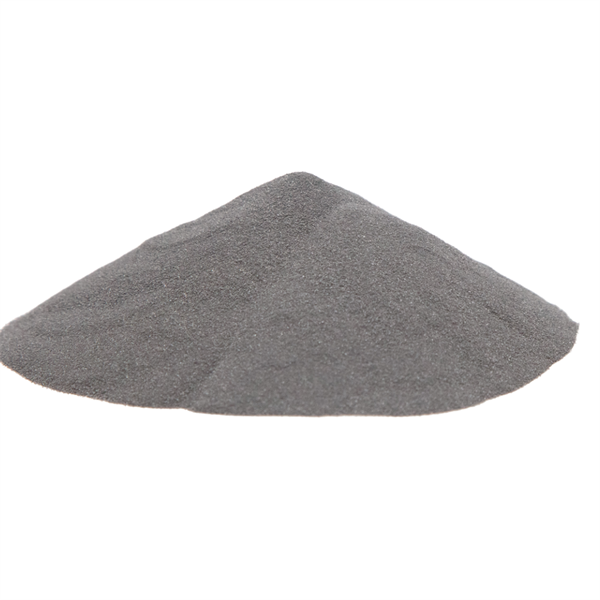
Betrieb und Wartung von EBM-Druckern
Um einen optimalen EBM-Druckerbetrieb aufrechtzuerhalten und Ausfallzeiten zu vermeiden:
- Führen Sie geplante vorbeugende Wartungsarbeiten gemäß den Richtlinien des Lieferanten durch – ersetzen Sie verschlissene Komponenten wie Abschirmungen.
- Überprüfen Sie die xyz-Genauigkeit des Strahls regelmäßig mithilfe von Kalibrierungsmethoden. Bei Bedarf neu ausrichten.
- Überprüfen Sie die wichtigsten Komponenten des Vakuumsystems – überprüfen Sie Dichtungen auf Lecks, überwachen Sie Pumpen und tauschen Sie Filter regelmäßig aus.
- Kalibrieren Sie integrierte Prozessüberwachungssensoren in vorgeschriebenen Abständen.
- Überwachen Sie die Vakuumqualität kontinuierlich – identifizieren und beheben Sie eventuelle Lecks sofort.
- Befolgen Sie die empfohlenen Reinigungsverfahren – halten Sie die Baukammer und das Pulverhandhabungssystem sauber.
- Erlauben Sie nur qualifizierten Technikern, die Hochspannungsstrahlversorgung und die Pistole zu warten.
- Halten Sie Ersatz-/Verschleißteile wie Schutzschilde, Pumpen und Filter auf Lager, um Ausfallzeiten zu minimieren.
Planen Sie Wartungsabschaltungen für Zeiten mit geringem Volumen. Überwachen Sie den Zustand des EBM-Systems proaktiv zwischen Builds.
Vor- und Nachteile von Elektronenstrahlschmelzen
Das Elektronenstrahlschmelzen hat im Vergleich zu herkömmlichen Herstellungsverfahren sowohl Vorteile als auch Einschränkungen:
Vorteile
- Stellt komplexe Geometrien her, die mit anderen Mitteln nicht möglich wären.
- Konsolidiert Unterbaugruppen zu Einzelteilen.
- Reduziert Abfall – verwendet nur benötigtes Material.
- Verkürzt die Entwicklungszeit für neue Designs.
- Eigenschaften entsprechen oder übertreffen herkömmliche Mittel wie Guss.
- Erfordert keine Bindemittel oder zusätzliche Stützen – ergibt reineres Material.
Benachteiligungen
- Höhere Stückkosten bei geringen Produktionsmengen.
- Größenbeschränkungen basierend auf der Baukammer.
- Die Materialauswahl ist im Vergleich zu anderen AM-Prozessen begrenzt.
- Um endgültige Teile zu erhalten, ist häufig eine Nachbearbeitung erforderlich.
- Anisotrope Eigenschaften durch schichtbasierten Aufbau.
- Erfordert eine erhebliche Energiezufuhr für den Elektronenstrahl.
Berücksichtigen Sie bei der Abwägung von EBM im Vergleich zu herkömmlichen Methoden Mengen, Größe, Eigenschaften, Vorlaufzeit und Kosten. EBM zeichnet sich durch komplexe, leistungsstarke Metallteile aus, jedoch mit höheren Einrichtungskosten.
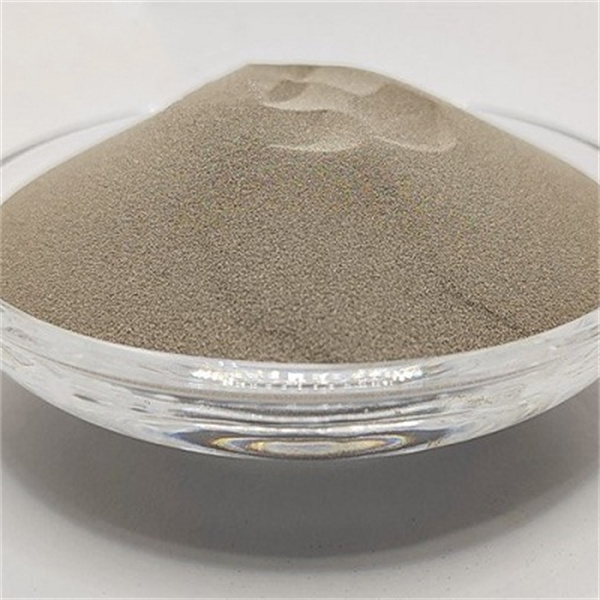
FAQ
F: Welche Materialien können Sie mit EBM bearbeiten?
A: Bisher hauptsächlich Titan-, Nickel-, Kobalt- und Edelstahllegierungen. Die Forschung erweitert die Materialoptionen, darunter Aluminium, Werkzeugstähle, Gold, Tantal und mehr.
F: Was ist der Hauptunterschied zwischen EBM und selektivem Laserschmelzen (SLM)?
A: EBM verwendet eine Elektronenstrahl-Energiequelle, während SLM einen Laser verwendet. Die mit EBM erreichbaren höheren Strahlleistungsdichten ermöglichen die Verarbeitung von höher schmelzenden Metallen.
F: Welche Branchen nutzen EBM-Druck?
A: Die Luft- und Raumfahrtindustrie ist bislang der größte Anwender von Komponenten wie Turbinenschaufeln. Aber auch die Medizin-, Automobil- und Industriebranche nutzen zunehmend EBM.
F: Produziert EBM poröse oder vollständig dichte Teile?
A: EBM kann mit optimalen Parametern eine Dichte von über 99% erreichen. Die Hochtemperaturaufbauten verbessern die Diffusionsbindung zwischen den Schichten.
F: Welche Teilegrößen können Sie mit EBM erstellen?
A: Die maximale Größe ist durch den Bauraum begrenzt und beträgt typischerweise etwa 250 x 250 x 300 mm. Größere Systeme sind in der Entwicklung und zielen auf 500-mm-Würfel ab.
F: Wie genau ist EBM im Vergleich zur CNC-Bearbeitung?
A: EBM kann bei guter Kalibrierung Toleranzen von bis zu 0,1–0,3 mm erreichen. Um engere Toleranzen unter 0,05 mm zu erreichen, ist jedoch eine Bearbeitung erforderlich.
F: Was sind die wichtigsten Vorteile von EBM?
A: Designfreiheit, Teilekonsolidierung, schnelles Prototyping, hochfeste Legierungen, reduzierter Abfall und kurze Vorlaufzeiten im Vergleich zur herkömmlichen Fertigung.
F: Welche Sicherheitsvorkehrungen sind für EBM erforderlich?
A: EBM-Systeme erzeugen Röntgenstrahlung, daher ist eine ausreichende Bleiabschirmung der Baukammer von entscheidender Bedeutung. Nur geschultes Personal darf den Betrieb durchführen.