Überblick über Elektronenstrahl-Schmelzanlage Technologie
Das Elektronenstrahlschmelzen ist eine additive Fertigungstechnologie, bei der Metallpulver mit Hilfe eines Hochleistungselektronenstrahls in einer Vakuumumgebung Schicht für Schicht miteinander verschmolzen werden. EBM-Anlagen bieten Möglichkeiten, die von anderen 3D-Druckverfahren für Metalle in Bezug auf Baurate, Teiledichte, Eigenspannung und mechanische Eigenschaften nicht erreicht werden.
Zu den wichtigsten Merkmalen der Elektronenstrahlschmelztechnologie gehören:
Tabelle 1: Überblick über die Merkmale des Elektronenstrahlschmelzens
Attribut | Einzelheiten |
---|---|
Wärmequelle | Hochleistungselektronenstrahl |
Umwelt | Hochvakuum |
Rohstoff | Metall-Pulverbett |
Strahlsteuerung | Elektromagnetische Linsen/Ablenkspulen |
Bau-Modus | Schicht für Schicht Metallschmelzen |
Anwendungen | Luft- und Raumfahrt, Medizintechnik, Automobilindustrie, Werkzeugbau |
EBM-Maschinen ermöglichen ein schnelles Schmelzen von leitfähigen Materialien zu vollständig dichten Bauteilen mit Materialeigenschaften, die denen herkömmlicher Herstellungsverfahren gleichwertig oder überlegen sind.
Durch die kontrollierte Vakuumumgebung und die intelligente Energiezufuhr werden Probleme mit Oxidation oder Verunreinigung während der Verarbeitung minimiert. Dies ermöglicht sehr hohe Dichten und eine hervorragende strukturelle Integrität, die sich perfekt für kritische Anwendungen eignet.
Durch die Nutzung einer hohen Strahlleistung für schnelle Abtastraten über jede Schicht hinweg ermöglicht EBM extrem hohe Baugeschwindigkeiten, die mit laserbasierten Systemen nicht zu erreichen sind. Dieser Produktivitätsvorteil ist ein entscheidender Faktor für die Einführung der Technologie.
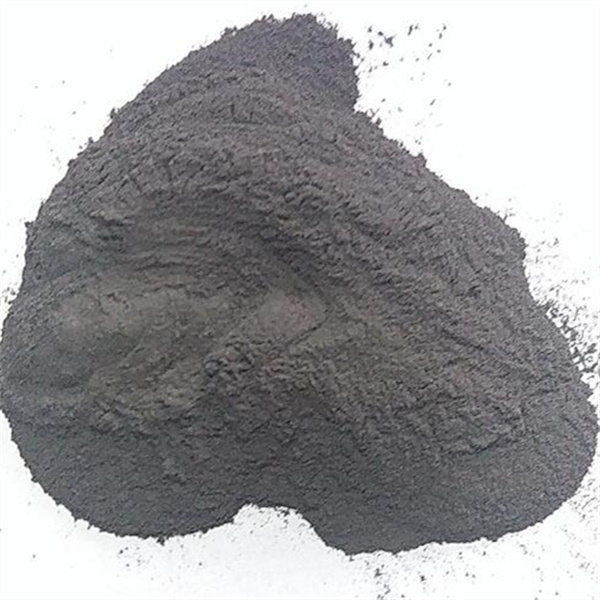
Arten von Elektronenstrahl-Schmelzanlage Systeme
Es gibt mehrere Kategorien von EBM-Anlagen auf dem Markt, die verschiedene Bauraumgrößen, Strahlleistungen und Produktionskapazitäten für unterschiedliche Anwendungen bieten.
Tabelle 2: Typen von Elektronenstrahlschmelzanlagen
Maschinenklasse | Größe bauen | Strahlleistung | Typische Verwendungen |
---|---|---|---|
Kleine Briefumschläge | 150 x 150 x 150 mm | 3-4 kW | Zahnärztliche und medizinische Geräte |
Standard-Plattformen | 200 x 200 x 350 mm | 6-8 kW | Komponenten für die Luft- und Raumfahrt, Werkzeugbau |
Mittelklasse-Plattformen | 400 x 400 x 400 mm | 14-16 kW | Automobilindustrie, größere Flugzeugteile |
Große Briefumschläge | 800 x 800 x 500 mm | 30-60 kW | Strukturelle Halterungen, Turbinenschaufeln |
Größere Geräte ermöglichen größere Komponenten für Branchen wie die Luft- und Raumfahrt und die Automobilindustrie, um die Anzahl der Montageteile zu verringern. Kleinere Maschinen mit geringerer Leistung zielen auf hochwertige Anwendungen in der Medizin- und Dentalbranche ab.
Die meisten EBM-Systemhersteller bieten modulare Maschinenarchitekturen an, um die Kapazität, die Strahlleistung und das Bauvolumen zu skalieren, wenn die Kundenakzeptanz und die Anwendungsanforderungen im Laufe der Zeit steigen.
Grundlagen der Elektronenstrahlschmelztechnik
Zu den wichtigsten Teilsystemen und Bearbeitungsschritten der additiven Fertigung mit Elektronenstrahl gehören:
Tabelle 3: Überblick über die Grundlagen des Elektronenstrahlschmelzens
Bühne | Funktion | Wichtige Komponenten |
---|---|---|
1. Handhabung des Pulvers | Neue Materialschichten zuführen | Pulverbehälter und Schwader |
2. Erzeugung von Strahlen | Elektronenstrahl erzeugen/beschleunigen | Wolframglühkathode, Anodenspannung |
3. Strahlfokussierung | Elektromagnetischer Konvergenzstrahl | Magnetische Spulenlinsen |
4. Ablenkung | Ortung des direkt fokussierten Strahls | Ablenkungsspulen |
5. Vakuum-System | Sicherstellung einer schadstofffreien Umgebung | Diffusionspumpen, Ventile, Sensoren |
6. Kontrollsystem | Koordinierung und Überwachung aller Funktionen | Computer, Software, Sensoren |
Eine EBM-Maschine erfordert den integrierten Betrieb dieser Teilsysteme, um Teile effizient Schicht für Schicht aus Metallpulver herzustellen:
- Hochgeschwindigkeits-Strahlablenkung steuert die geschmolzenen Bereiche präzise über jede Pulverbettschicht
- Vakuum entfernt gasförmige Verunreinigungen und verhindert die Oxidation/Nitridierung des Materials
- Pulverschwader verteilen frisches Material effizient und gewährleisten die Dichte
- Sensoren mit geschlossenem Regelkreis sorgen für eine Rückmeldung zur Gewährleistung der Maßgenauigkeit
- Robuste Computersteuerung koordiniert jeden Aspekt des Bauprozesses
Die einzigartige Kombination aus reinem Metallpulver und einer hochintensiven Energiequelle in einer Vakuumkammer ermöglicht ein sehr schnelles Schmelzen und Erstarren für außergewöhnliche metallurgische Eigenschaften.
Das Verständnis dieser grundlegenden Prinzipien hilft den Käufern bei der Auswahl von Geräten, die für ihre Ziele optimiert sind, sei es die Maximierung der Produktivität, der Teilequalität, der Betriebskosten oder der Anwendungsanforderungen.
Spezifikationen von Elektronenstrahlschmelzmaschinen
Es gibt zahlreiche leistungsbestimmende Spezifikationen, die Käufer bei der Auswahl von EBM-Geräten berücksichtigen müssen, die ihren Produktionsanforderungen und Betriebsbedingungen am besten entsprechen.
Tabelle 4: Wichtige Spezifikationen für Elektronenstrahlschmelzanlagen
Parameter | Typischer Bereich | Bedeutung |
---|---|---|
Strahlleistung | 3-60 kW | Bauraten, maximale Teilegröße |
Strahlgeschwindigkeit | Bis zu 8 m/s | Schichtzeiten, Produktivität |
Punktgröße | 50-200 μm | Auflösung, feine Merkmalsdefinition |
Aktuell | 1-50 mA | Materialverträglichkeit, Strahloptimierung |
Beschleunigungsspannung | 30-150 kV | Eindringtiefe, ungeschmolzenes Pulver |
Vakuumniveau | 5 x 10-5 mbar | Reinheit, materielle Integrität |
Schichtdicke des Pulvers | 50-200 μm | Vertikale Auflösung, Dichte |
Die Kenntnis von Spezifikationen wie Strahlleistung, Scangeschwindigkeit, Spotgröße und Mindestschichtdicke ermöglicht die Auswahl einer geeigneten Maschine für die beabsichtigte Anwendung und den angestrebten Durchsatz.
Andere wichtige Faktoren, die die Auswahl des Systems beeinflussen, sind unter anderem:
- Steuerungssoftware: Funktionen für die effiziente Einrichtung der Konstruktion, Optimierungswerkzeuge für die Parameterentwicklung, Überwachungs-/Analysefunktionen und Kompatibilität mit nachgelagerten digitalen CAD/CAM-Workflows.
- Palette der Materialien: Die Anzahl der qualifizierten Werkstoffe, die vom OEM zur Verfügung stehen, bestimmt die Bandbreite der Anwendungen, für die das Gerät geeignet ist. Zu den bevorzugten Metallen gehören Titan, Nickelsuperlegierungen, Werkzeugstähle, Edelstahl, Kobalt-Chrom und Aluminium.
- Zusatzgeräte: Anforderungen an zusätzliche Pulverhandhabungsgeräte, Nachbearbeitungsstationen, Siebgeräte, externe Wärmebehandlung, HIP-Öfen und Pulverrecycling-Systeme.
- Dienstleistungen: Wert von Wartungsverträgen, Unterstützung bei der Anwendungsoptimierung, Bedienerschulungen und Rückstellungen für die Verlagerung von Geräten.
Eine sorgfältige Bewertung der Maschinenspezifikationen anhand der aktuellen und zukünftigen Produktionsanforderungen erleichtert angemessene Investitionsentscheidungen in EBM-Kapazitäten.
Überblick über die Wirtschaftlichkeit des Elektronenstrahlschmelzens
Abgesehen von den reinen Anschaffungskosten für die Ausrüstung benötigen Fertigungsunternehmen realistische Prognosen über die gesamte Wirtschaftlichkeit der Produktion, die mit der Einführung der EBM-Technologie verbunden ist.
Tabelle 5: Zusammenfassung der Wirtschaftlichkeit der EBM-Verarbeitung
Kostenelement | Typischer Bereich |
---|---|
Maschinelle Erfassung | $800.000 bis $2.500.000 |
Einrichtung | $50.000 bis $250.000 |
Infrastruktur der Einrichtung | $100.000 bis $500.000 |
Pulver-Hilfsgeräte | $50.000 bis $150.000 |
Jährliche Materialien | $100.000 bis $800.000 |
Verbrauchsmaterialien | $20.000 bis $100.000 |
Betriebliche Arbeit | 1 bis 3 Bediener pro System |
Energieverbrauch | $15.000 bis $50.000 |
Wartungsverträge | $50.000 bis $150.000 |
Bei Maschinenpreisen von etwa $800.000 für Einsteigersysteme bis zu $2.500.000 für große Industrielösungen stellt die Ausrüstung nur einen Teil der gesamten Investitionsgleichung dar.
Andere Schlüsselvariablen, die sich auf die Betriebsrentabilität und die Berechnung der Kapitalrendite auswirken, sind u. a:
- Verwendung der Materialien: Das Pulver kann bis zu 30% der Gesamtkosten eines Teils ausmachen, wobei die Strategien für den Einkauf und die Wiederverwendung optimiert werden.
- Arbeit: Manuelles oder automatisiertes Pulver-/Teilehandling wirkt sich auf den Personalbedarf aus. Optimieren Sie die Fertigung, um die unbeaufsichtigten Laufzeiten zu maximieren.
- Einrichtung: Die Kosten für Installation, Energie, Umweltkontrolle und Zusatzgeräte summieren sich. Berücksichtigen Sie auch die Kosten für Sicherheit, Versorgungsleistungen und die Einhaltung von Vorschriften.
- Wartung: Vorbeugende Instandhaltung ist entscheidend für die Betriebszeit, die Produktionsqualität und die Langlebigkeit der Geräte. Wägen Sie zwischen OEM- und Inhouse-Service-Optionen ab.
Die Analyse dieser Kostenfaktoren vor dem Erwerb von EBM-Kapazitäten erleichtert eine realistische Geschäftsplanung. Die Modellierung von Szenarien für die Teileproduktion auf der Grundlage tatsächlicher Leistungsdaten verbessert die Transparenz der finanziellen Risiken und Rentabilitätsaussichten.
Beliebte Materialien für das Elektronenstrahlschmelzen
Aufgrund der hohen Strahlintensität und der Vakuumumgebung eignet sich EBM für die Verarbeitung reaktiver und refraktärer Legierungen, die mit anderen additiven Verfahren oder Gießprozessen nur schwer zu schmelzen sind.
Tabelle 6: Gängige Materialien für das Elektronenstrahlschmelzen
Material Klasse | Beispiele für Legierungen | Anwendungen |
---|---|---|
Titan-Legierungen | Ti-6Al-4V, Ti-6Al-4V ELI | Strukturen für die Luft- und Raumfahrt |
Nickel-Superlegierungen | Inconel 718, Inconel 625 | Turbinenschaufeln, Abgassysteme |
Werkzeugstähle | H13, Maraging 300 | Spritzgussformen, Werkzeugbau |
Kobalt-Chrom | CoCrMo | Medizinische/zahnmedizinische Implantate |
Rostfreie Stähle | 17-4PH, 316L | Korrosionsbeständigkeit erforderlich |
Exotische und kundenspezifische Legierungen | Cu, Al, Ta, W, Mo | Elektronik, Forschung |
Die beliebtesten Werkstoffe für EBM sind nach wie vor Titanlegierungen für leichte Luft- und Raumfahrtkomponenten, Nickelsuperlegierungen für extreme Temperaturbeständigkeit und medizinisches Kobaltchrom für biokompatible Implantate.
Die Flexibilität des Pulverbettschmelzens eignet sich jedoch für praktisch jedes Legierungssystem, einschließlich reaktiver Elemente wie Aluminium oder hochschmelzender Metalle, die bei herkömmlichen Verfahren eine Herausforderung für die Schmelze darstellen. Dies erleichtert Innovationen in Bereichen wie Wärmemanagement in der Elektronik, Spektroskopiekomponenten und Hochtemperaturanwendungen über 1000 °C.
Dank der Vakuumbearbeitungsumgebung, die Verunreinigungsprobleme mindert, ist die Materialqualität und -integrität im Vergleich zu konkurrierenden AM- oder Gussverfahren sehr günstig.
Vorteile der Elektronenstrahlschmelztechnologie
Abgesehen von der Ermöglichung sehr hoher Aufbauraten, die von anderen Pulverbetttechnologien nicht erreicht werden, bietet EBM weitere Vorteile, die es zum Verfahren der Wahl für kritische Anwendungen in der Luft- und Raumfahrt, der Medizin und der Industrie machen.
Tabelle 7: Hauptvorteile des Elektronenstrahlschmelzens
Nutzen Sie | Beschreibung |
---|---|
Hohe Dichte | Annäherung an 100% dank hoher Strahlungsenergie und Vakuum |
Außergewöhnliche Materialeigenschaften | Besser als gegossen oder geschmiedet |
Hohe Ablagerungsraten | 10-mal höhere Baugeschwindigkeit als bei laserbasierten Systemen |
Geringe Eigenspannung | 70-90% weniger Verformung oder Rissbildung |
Gestaltungsfreiheit | Erleichterung komplexer Geometrien |
Kaufen:Anpassungen vornehmen | Kombinieren Sie mehrere Teile zu einer komplexen Baugruppe |
Konkrete Beispiele, bei denen EBM einen Mehrwert gegenüber der konventionellen Herstellung bietet, sind:
Produktivität
- Herstellung von Turbinenschaufeln aus Inconel 718 mit der 10-fachen Geschwindigkeit von Präzisionsgussverfahren.
- Herstellung von mehr als 10 Hüftimplantaten gleichzeitig aufgrund größerer Produktionsmengen.
- Einsatz von automatisiertem Pulverhandling und Auftragswarteschlangen für eine 24/7-Produktion ohne Unterbrechung.
Leistung
- Entwicklung von Ti-6Al-4V-Satellitenhalterungen mit hervorragendem Verhältnis zwischen Festigkeit und Gewicht.
- Wir bieten kobaltverchromte Zahnbrücken mit hervorragender Ästhetik und Präzision an.
- Herstellung von H13-Werkzeugen mit konformer Kühlung für eine längere Lebensdauer der Spritzgussform.
Qualität
- Erzielung sauberer Materialmikrostrukturen, die frei von den beim Gießen üblichen Mikroporositätsfehlern sind.
- Keine inneren Spannungen und Verformungen dank hoher Vorwärmtemperaturen.
- Verhinderung von Verunreinigungen in reaktiven Materialien durch Nutzung der Hochvakuumumgebung.
Die einzigartigen Schmelzbedingungen, die durch die Elektronenstrahltechnologie ermöglicht werden, erweisen sich immer wieder als die führende AM-Lösung für hochwertige Anwendungen, die eine außergewöhnliche Materialleistung erfordern.
Beliebt EBM-Ausrüstung Anbieter
Eine Vielzahl etablierter Industrieunternehmen und spezialisierter Start-ups bieten Lösungen für das Elektronenstrahlschmelzen an, die auf die unterschiedlichen Hürden der Kunden in den verschiedenen Marktsegmenten zugeschnitten sind.
Tabelle 8: Führende Anbieter von Anlagen für das Elektronenstrahlschmelzen
Anbieter | Einzelheiten | Ziel-Segmente |
---|---|---|
Arcam EBM (GE Additiv) | Pionierarbeit mit der ersten EBM-Maschine | Luft- und Raumfahrt, Medizintechnik, Automobilindustrie |
Sciaky | Größte Bauumfänge | Strukturen für die Luft- und Raumfahrt |
JEOL | Plattformen für die Forschung | Universitäten |
Wayland-Zusatzstoff | Haushaltssysteme | Job-Shops |
6K | Kostengünstige Metallpulver | Prozessentwicklung |
Andere Gerätehersteller, die Elektronenstrahlanwendungen außerhalb der traditionellen additiven Fertigung anstreben, sind unter anderem:
- Canon - Lösungen für das Elektronenstrahlschweißen
- PTR Group - Elektronenstrahlöfen und Schweißgeräte
- IBE Services - Kleine Elektronenstrahlschweißgeräte
- Teta - Industrielles EB-Hochleistungsschweißen
Der Branchenführer Arcam EBM (jetzt Teil von GE Additive) hat nach der Einführung der ersten kommerziellen EBM-Maschine im Jahr 2002 eine dominante Patent- und Marktanteilsposition aufgebaut. Das Unternehmen ist nach wie vor der führende Ausrüstungslieferant in den Bereichen Luft- und Raumfahrt, Medizintechnik, Automobil und Industrie.
Die meisten Anbieter nutzen Partnerschaften mit Materialherstellern, Forschungsgruppen und Endbenutzerorganisationen, um die EBM-Prozessfähigkeiten entsprechend den realen Produktionsanforderungen kontinuierlich zu verbessern. Diese gemeinsamen Anstrengungen zur Verbesserung der Technologie werden letztendlich die Akzeptanz in noch mehr kritischen Industrieanwendungen in Zukunft erhöhen.
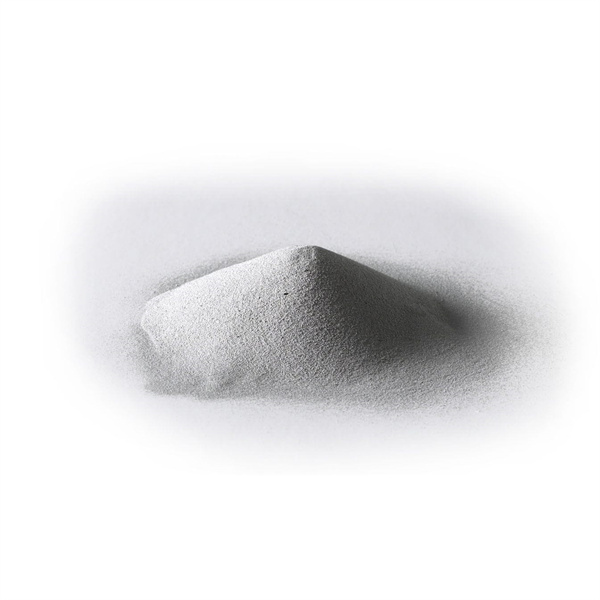
FAQ
F: Wie groß muss eine Einrichtung sein, um EBM-Geräte unterzubringen?
A: Die Mindestaufstellfläche beträgt etwa 100 m² für kleinere Maschinen, aber größere Plattformen, die mehr als 500 m² belegen, sind üblich. Weitere 500+ Quadratmeter sind typisch für zusätzliche Pulverhandhabungs- und Nachbearbeitungsstationen. Die Einrichtungen benötigen mindestens 8 Fuß hohe Decken und eine Verstärkung für schwere Ausrüstungslasten von mehr als 12.000 Pfund.
F: Welche Materialien sind mit der EBM-Verarbeitung nicht kompatibel?
A: Aluminiumlegierungen stellen ohne geeignete inerte Umgebung ein Oxidationsrisiko dar. Refraktärmetalle mit sehr hohen Schmelztemperaturen von über 3600°C wie Wolfram oder Rhenium sind ungeeignet. Ansonsten eignet sich EBM für die meisten Legierungssysteme.
F: Wie viele geschulte Bediener werden pro EBM-Maschine benötigt?
A: Ein Maschinenbediener kann in der Regel mehrere EBM-Maschinen überwachen, je nach Automatisierungsgrad und Produktionsvolumen. Zusätzliches Personal wird für den Pulverbetrieb, die Nachbearbeitung, die Qualität, die Wartung und die technische Unterstützung benötigt.
F: Welche Sicherheitsrisiken sind mit der EBM-Technologie verbunden?
A: Hochspannungselektronenstrahlen stellen eine Gefahr für Lichtbögen dar und erfordern eine angemessene Umhüllung und Sicherheitskontrolle. Das Risiko der Exposition gegenüber reaktiven Metallpulvern erfordert ebenfalls Schutzausrüstung und Handhabungsprotokolle für Brand- und Gesundheitsgefahren. Eine ordnungsgemäße Ausbildung ist entscheidend.